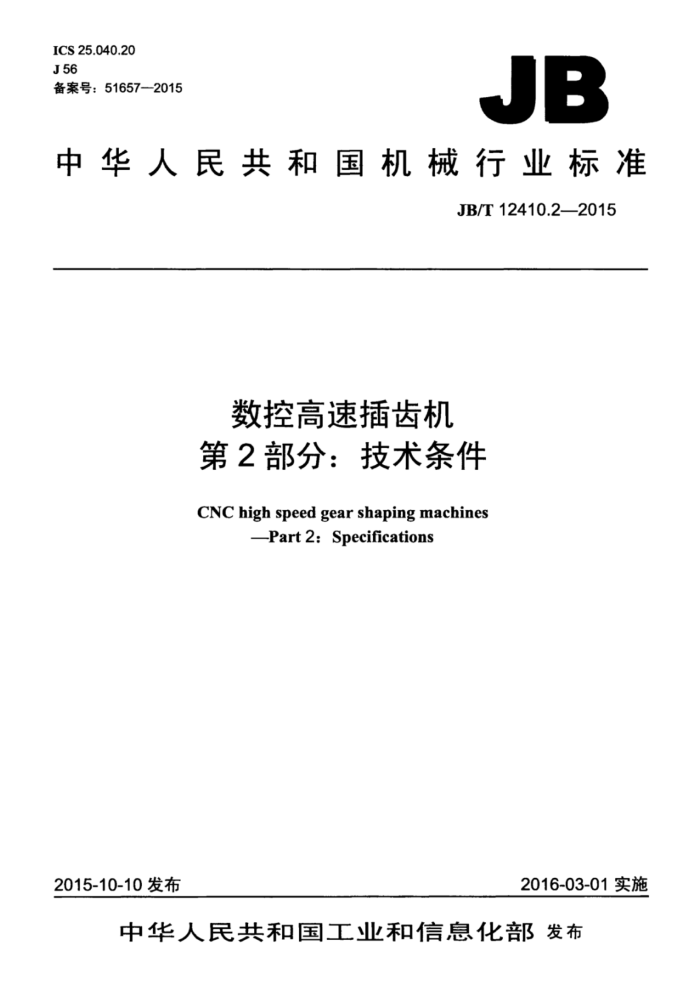
ICS25.040.20 J56 备案号:516572015
JB
中华人民共和国机械行业标准
JB/T12410.2—2015
数控高速插齿机第2部分:技术条件 CNC high speed gear shaping machines
-Part2: Specifications
2015-10-10发布
2016-03-01实施
中华人民共和国工业和信息化发布
JB/T12410.2—2015
目 次
前言 1范围 2规范性引用文件 3技术要求 3.1 一般要求, 3.2 参数 3.3 附件和工具 3.4 布局和外观 3.5 电气系统. 3.6 数控系统 3.7 液压、润滑和冷却系统 3.8 安全卫生 3.9 加工和装配质量. 3.10 机床的空运转试验要求 3.11 机床的负荷试验要求, 3.12 机床的精度检验要求 4检验与验收.
1
T
一
4.1 概述, 4.2 般要求. 4.3 参数检验(抽查) 4.4 附件和工具的检验, 4.5 外观检验. 4.6 电气系统检验.. 4.7 数控系统的检验, 4.8 液压,润滑和冷却系统的检验 4.9 安全卫生检验. 4.10 机床加工及装配质量检验 4.11 机床的空运转试验 4.12 机床的负荷试验 4.13 机床的精度检验 4.14 其他 5包装.
一
表1附件和工具表2错位量及贴合缝隙值. 表3脏物质量限值表4空运转试验条件. 表5轴承温度及温升限值
2
心
4
I
JB/T12410.2—2015
前言
JB/T12410《数控高速插齿机》分为两个部分:
一第1部分:精度检验;一第2部分:技术条件。
本部分为JB/T12410的第2部分。 本部分按照GB/T1.1一2009给出的规则起草。 本部分由中国机械工业联合会提出。 本部分由全国金属切削机床标准化技术委员会(SAC/TC22)归口本部分起草单位:南京二机齿轮机床有限公司、国家机床质量监督检验中心、天津第一机床总厂、
宜昌长机科技有限责任公司、重庆机床(集团)有限责任公司。
本部分主要起草人:蒋小彦、李光华、吕福根、李祥文、柴宝连、钟瑞龄、喻可斌。 本部分为首次发布。
II
JB/T12410.2—2015
数控高速插齿机第2部分:技术条件
1范围
JB/T12410的本部分规定了数控高速插齿机设计、制造、检验与验收的要求。 本部分适用于最大工件直径为125mm320mm、刀具主轴最大往复冲程数大于1500次/min,同
时其平均切削速度大于50m/min的数控高速插齿机(以下简称机床)。
2规范性引用文件
下列文件对于本文件的应用是必不可少的。凡是注日期的引用文件,仅注日期的版本适用于本文件。 凡是不注日期的引用文件,其最新版本(包括所有的修改单)适用于本文件。
GB5226.1一2008机械电气安全机械电气设备第1部分:通用技术条件 GB/T6576--2002机床润滑系统 GB/T9061--2006 金属切削机床通用技术条件 GB15760—2004 金属切削机床安全防护通用技术条件 GB/T16769--2008 金属切削机床噪声声压级测量方法 GB/T23570—2009 金属切削机床焊接件通用技术条件 GB/T23572—2009 金属切削机床液压系统通用技术条件 GB/T25372—2010 金属切削机床精度分级 GB/T25373—2010 金属切削机床装配通用技术条件 GB/T25374---2010 金属切削机床清洁度的测量方法 GB/T25376--2010 金属切削机床机械加工件通用技术条件 GB/T26220-2010 工业自动化系统与集成机床数值控制 数控系统通用技术条件 JB/T8356.1—1996 机床包装技术条件 JB/T8356.2—1996 机床包装箱 JB/T12410.1一2015数控高速插齿机第1部分:精度检验
3技术要求
3.1一般要求 3.1.1按本部分验收机床时,还应对GB5226.1—2008~GB/T9061—2006、GB/T23570—2009GB/T 25373一2010GB/T25376—2010等标准中未经本部分具体化的有关项目进行检验。 3.1.2机床验收时,按GB/T25372--2010规定的V级精度机床的要求检验。 3.2参数
机床的参数应符合设计文件的规定。机床与工夹量具、附件等连接部位的型式和尺寸应符合有关标准的规定。
1
JB/T12410.2—2015
3.3附件和工具 3.3.1机床应随机供应表1所列的附件和工具
表1 附件和工具
名称减晨垫铁专用扳手螺母或螺钉刀垫连接套
用途安装机床用调整机床用安装刀具用安装刀具用安装工件用
数量 1套 1套 1套 1套 1件 1套
拉杆、法兰盘、垫和螺母等(由制造厂根据机床结构确定)
3.3.2扩大机床性能的特殊附件,可根据用户要求按协议供应。 3.4布局和外观 3.4.1机床布局应合理、造型美观、色泽和谐,设计符合人类工效学原则并便于调整及维修。 3.4.2 机床外观表面不应有未规定的凸起、凹陷,粗糙不平和其他损伤。 3.4.3 机床的防护罩表面应平整、匀称,不应翘曲、凹陷。 3.4.4 机床外露零件表面不应有磕碰、锈蚀,螺钉、铆钉、销子端部不应有扭伤、锤伤等缺陷。 3.4.5 电镀件、发黑件色调应一致,防护层不应有褪色、脱落现象。 3.4.6 机床可拆卸的装配结合面的接缝处,在涂漆以后,应切开,切开时不应扯破边缘。 3.4.7 机床涂漆层应平整,光泽应均匀一致,涂漆表面不应有起泡、流挂、起皮及脱落现象。 3.4.8 机床的各种信息标志及标牌应固定在机床相应的明显位置上,且清晰耐久,不歪斜。 3.4.9 机床电气、液压,润滑及冷却等管道的外露部分,应布置紧凑,排列整齐,必要时应用管夹固定,软管不应扭曲、折叠及断裂。 3.4.10装入沉孔的螺钉不应凸出零件表面,其头部与沉孔之间不应有明显的偏心。定位销一般应略凸出零件表面。螺栓尾端应略凸出螺母端面。外露轴端应凸出包容件的端面,凸出值约为倒棱值。内孔表面与壳体凸缘间的壁厚应均匀对称,其凸缘壁厚之差不应大于实际最大壁厚的25%。 3.4.11机床零部件外露结合面的边缘整齐匀称,不应有明显的错位。门、盖与机床的结合面应贴合。 错位量及贴合缝隙值不应大于表2的规定。
表2错位量及贴合缝隙值 ≤500
单位为毫米 >3150 4 2
结合面边缘及门、盖边长尺寸
>1250-3150
>5001250
错位量错位不匀称量贴合缝隙值缝隙不均匀值
2 1 1.5 1.5
3 1.5 2 2
1.5 1 1 1
一
注1:当结合面边缘及门,盖的长、宽尺寸不一致时,可按长边尺寸确定允许值。 注2:错位不匀称量指外露结合面边缘同一边或对应边最大错位量与最小错位量之差值。 注3:缝隙不均匀值指门、盖间对开缝或其相对机床本体间最大缝隙值与最小缝隙值之差值。
2
JB/T12410.2--2015
3.5电气系统
机床的电气系统应符合GB5226.1—2008的规定。 3.6数控系统
机床的数控系统应符合GB/T262202010的规定。 3.7液压、润滑和冷却系统 3.7.1机床的液压系统应符合GB/T23572-2009的规定。 3.7.2机床的润滑系统应符合GB/T6576—2002的规定。 3.7.3机床的冷却系统应保证冷却充分、可靠。 3.7.4机床的液压、润滑、冷却系统及其他部位均不应渗漏。切削液不应混入液压系统和润滑系统。 3.8安全卫生 3.8.1机床上有可能对人体健康或对设备造成损伤的部位,应采取安全措施,机床的安全防护应符合 GB15760—2004~GB5226.1—2008的规定。 3.8.2在机床加工区应设置防护罩,并应具有足够的强度和刚性。防护装置的设置应便于工件的置换以及操作者的观察。 3.8.3外露而易被尘屑磨损的导轨副应安装防护装置。 3.8.4液压系统应能提供稳定的正常工作的压力,当压力超出设定限值时,应发出警告信号或使机床运动停止。 3.8.5按GB/T167692008的规定测量机床的空运转噪声,其噪声声压级不应超过83dB(A)。机床运转时,不应有异常的尖叫声,冲击声。 3.9加工和装配质量 3.9.1机械加工件~焊接件应符合图样。工艺文件及GB/T253762010、GB/T235702009的规定。 机床装配应符合GB/T25373一2010的规定。 3.9.2刀架体、工作台壳体、立柱、立柱滑板,刀架滑座、工作台主轴床身、中床身、工作台分度蜗轮、刀架分度蜗轮等为重要零件,应在粗加工后进行时效处理(如人工时效、振动时效等)。 3.9.3刀具主轴往复运动导轨副为重要导轨副,刀具主轴往复运动导轨副和主轴轴承应采取与高速相适应的耐磨措施(如静压导轨,静压轴承等) 3.9.4刀架分度蜗杆副、工作台分度蜗杆副、让刀凸轮、径向进给凸轮。刀具主轴、刀具套等主要零件应采取与机床寿命相适应的耐磨措施。 3.9.5下列结合面按重要固定结合面的要求检验,其制造及验收应符合GB/T25373一2010和GB/T 25376—2010的规定:
a)驱动箱与立柱的结合面: b)刀架蜗杆体与刀架体(或床身)的结合面: C)工作台蜗杆体与工作台底座或工作台蜗杆体与工作台体的结合面。
3.9.6下列结合面按“特别重要固定结合面”的要求检验,其制造及验收应符合GB/T25373--2010和 GB/T25376--2010的规定:
a)对于工作台做径向进给的机床,床身与中床身(或立柱)的结合面: b)对于立柱做径向进给的机床,立柱与中床身、工作台体与床身的结合面。
3.9.7下列导轨面按滑动导轨的要求检验,其制造及验收应符合GB/T25373一2010和GB/T25376 2010的规定:
3
JB/T12410.2—2015
a)刀架中的固定导轨(螺旋导轨)与滑块的导轨面: b)工作台(或立柱、径向滑板)与床身的导轨面。
3.9.8立柱与中床身相配的导轨面、工作台底座与工作台体相配的导轨面按移置导轨的要求检验,其制造及验收应符合GB/T25373—2010和GB/T25376—2010的规定。 3.9.9带刻度装置的径向进给手轮或手柄,其反向空程量不应超过1/4转 3.9.10机床清洁度按GB/T25374--2010规定的方法进行检验,其中工作台、刀架内部、润滑系统、 液压系统的清洁度按重量法检验,其他部位按目测、手感法检验,不应有脏物。
a)刀架、工作台内部的清洁度按清洗油液中所含脏物质量来确定,其清洁度值不超过表3的规定;
表3脏物质量限值
最大工件直径mm
检测部位
≤125
>125~320 脏物质量mg
>320~400
刀架工作台 b)机床液压、润滑系统的清洁度:在机床开车运行30min后,立即在液压系统(或润滑系统)的
3 200 2400
4.800 4000
7200 4600
回油处取样,一般不应少于200mL,其杂质污物不应超过120mg/L。
3.10机床的空运转试验要求 3.10.1运转检验
整机空运转试验:运行过程中各机构应正常,其运转条件应符合表4的规定。
表4空运转试验条件
运转时间 min ≥10 ≥10 ≥60
平均切削速度
往复冲程次数
冲程长度
圆周进给量
径向进给量
m/min
低中高
大中小
大中小
长中短
在最高冲程数运转时不低于50
3.10.2温升试验 3.10.2.1 主轴轴承达到稳定温度时,在靠近刀具主轴轴承的外壳处测量轴承的温度和温升,其值不应超过表5的规定。
表5轴承温度及温升限值
单位为摄氏度
温度 55 65
轴承型式滑动轴承滚动轴承
温升 25 35
注:机床经过一定时间运转后,当其测量温度值上升幅度不超过5℃/h时,可认为达到了稳定温度。 3.10.2.2液压系统应在额定工作压力下连续运转,待油液达到稳定温度后,测量油液的温度和温升,其温度不应朝超过60℃,温升不应超过30℃。
4