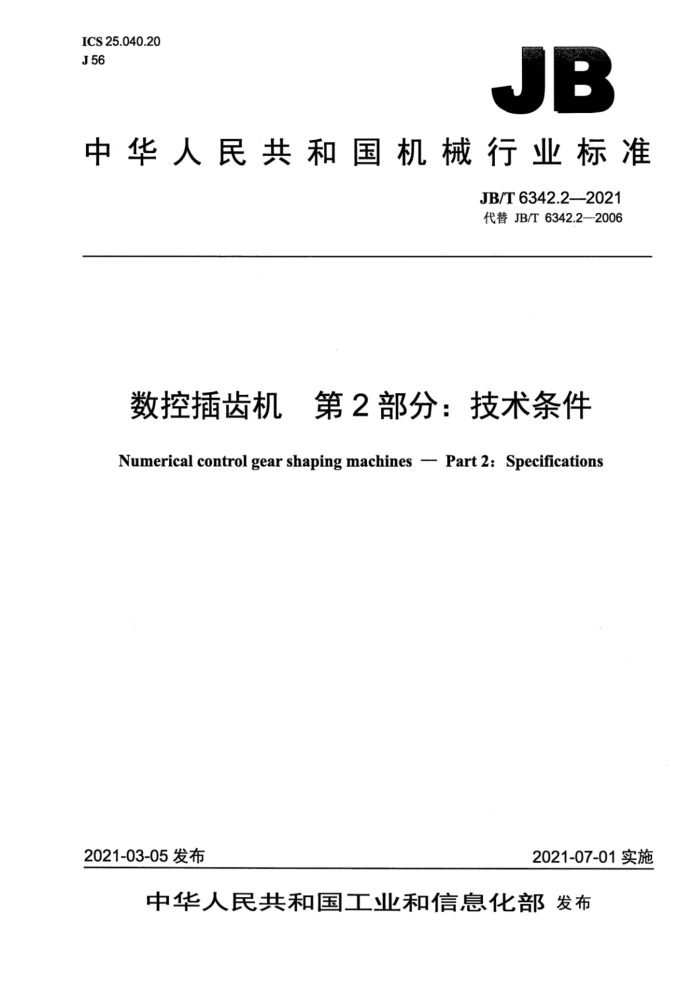
JB
中华人民共和国机械行业标准
JB/T6342.2--2021 代替JB/T6342.2—2006
数控插齿机 第2部分:技术条件
Numerical control gear shaping machines -- Part 2: Specifications
2021-07-01实施
2021-03-05发布
目 次
前言 1范围. 2规范性引用文件 3一般要求.. 4附件和工具 5安全卫生 6加工和装配质量 7空运转试验.
7.1 运转检验 7.2 温升试验 7.3 空运转功率试验(抽查) 7.4 动作试验. 7.5 整机连续空运转试验 8负荷试验 9最小设定单位检验 9.1 概述. 9.2 试验方法 9.3 误差计算 9.4 公差... 9.5 检验工具. 10精度检验 11 包装
图1 最小设定单位检验
表1附件和工具,表2机床重要部件清洁度要求表3空运转时间.. 表4.轴承温度及温升
前言
JB/T6342《数控插齿机》分为两个部分:
第1部分:精度检验;第2部分:技术条件。
本部分为JB/T6342的第2部分。 本部分按照GB/T1.1一2009给出的规则起草。 本部分代替JB/T6342.2—2006《数控插齿机第2部分:技术条件》,与JB/T6342.2一2006相比
主要技术变化如下:
引用了现行版本的相关标准,增加引用了GB/T26220-2010《工业自动化系统与集成机床数值控制数控系统通用技术条件》和JB/T8356一2016《机床包装技术条件》(见第2章);删除了“布局和外观”要求(见2006年版的第5章);增加了“安全卫生”要求(见第5章);修改了“动作试验”的内容(见7.4):修改了“整机连续空运转试验”的内容(见7.5,2006年版的7.6); -增加了“最小设定单位检验”要求(见第9章):一删除了“其他试验”要求(见2006年版的第10章);增加了“包装”要求(见第11章)。
本部分由中国机械工业联合会提出。 本部分由全国金属切削机床标准化技术委员会(SAC/TC22)归口。 本部分起草单位:重庆机床(集团)有限责任公司、天津第一机床总厂、南京二机齿轮机床有限公
司、宜昌长机科技有限责任公司、武汉格威机械有限责任公司。
本部分主要起草人:李毅、曾令万、喻可斌、柴宝连、刘德全、李光华、钟瑞龄、朱旺全。 本部分所代替标准的历次版本发布情况为:
JB/T6342—1992、JB/T6342.2—2006
数控插齿机第2部分:技术条件
1范围
JB/T6342的本部分规定了数控插齿机设计、制造和验收的要求。 本部分适用于最大工件直径为125mm~3150mm的数控插齿机(以下简称机床)。
2规范性引用文件
下列文件对于本文件的应用是必不可少的。凡是注日期的引用文件,仅注日期的版本适用于本文件。凡是不注日期的引用文件,其最新版本(包括所有的修改单》适用于本文件。
GB/T5226.1一2019机械电气安全机械电气设备第1部分:通用技术条件 GB/T6576-2002机床润滑系统 GB/T9061—2006 金属切削机床通用技术条件 GB15760—2004金属切削机床安全防护通用技术条件 GB/T17421.5—2015 机床检验通则第5部分:噪声发射的确定 GB/T23570—2009 金属切削机床焊接件通用技术条件 GB/T23572-2009 金属切削机床液压系统通用技术条件 GB/T25372—2010 金属切削机床精度分级 GB/T25373—2010 金属切削机床装配通用技术条件 GB/T25374—2010 金属切削机床清洁度的测量方法 GB/T25376—2010 金属切削机床机械加工件通用技术条件 GB/T26220-2010 工业自动化系统与集成机床数值控制数控系统通用技术条件 JB/T6342.1—2021 数控插齿机第1部分:精度检验 JB/T8356一2016机床包装技术条件
3一般要求
3.1按本部分验收机床时,还应对GB/T9061—2006、GB/T23570—2009、GB/T25373-2010、GB/T 25376一2010等中未经本部分具体化的有关项目进行检验。 3.2验收机床时,按GB/T25372一2010规定的V级精度机床的要求检验。
4附件和工具
4.1为保证机床的基本性能,应随机供应表1所列附件和工具。
表1附件和工具
名称
用途
数量
表1附件和工具(续)
名称螺母或螺钉刀垫连接套
用途
数量 1套 1件 1件 1套
安装刀具用
拉杆、法兰盘、垫和螺母等由制造商根据机床结构而确定提供的种类和数量,
安装工件用
4.2扩大机床使用性能的特殊附件,可按协议供应。
5安全卫生
5.1机床的安全防护应符合GB15760—2004GB/T5226.1-2019的规定。 5.2在机床加工区应设置防护罩或挡板,且防护罩或挡板的设置应便于操作者观察加工区。 5.3外露而易被尘屑磨损的导轨副应安装防护装置。 5.4液压系统应能提供稳定的正常工作压力,当压力低于设定限值时,应发出警告信号或使机床运动停止。 5.5按GB/T17421.52015的规定测量机床的噪声,机床在空运转条件下噪声声压级不应超过 83dB(A)。机床运转时,不应有异常的尖叫声、冲击声。
6加工和装配质量
6.1刀架蜗轮、工作台蜗轮、工作台、工作台壳体、工作台底座、刀架中的滑块、固定导轨(或螺旋导轨)、床身、立柱、中床身(或径向滑板)、工件主轴及刀架体为重要铸件,应在粗加工后进行热时效或振动时效等时效处理。 6.2床身与工作台底座(或立柱)导轨副、刀架中的固定导轨(或螺旋导轨)与滑块导轨副为重要导轨副,应采取耐磨措施,并符合材质及热处理的规定。 6.3焊接件应符合GB/T23570—2009的规定。 6.4刀架、工作台分度蜗杆副、让刀凸轮、径向进给丝杠副、轴向进给丝杠副、刀具主轴及刀轴套(或齿条体)等为主要零件,应采取耐磨措施,并符合材质及热处理的规定。 6.5下列结合面按GB/T25373—2010和GB/T25376—2010中重要固定结合面”的要求考核:
a)传动箱与立柱的结合面: b)刀架蜗杆体与刀架体(或床身)的结合面; c)工作台蜗杆体与工作台底座或工作台蜗杆体与工作台体的结合面。
6.6下列结合面按GB/T25373—2010和GB/T25376—2010中“特别重要固定结合面”的要求考核:
a)立柱与床身或工作台与床身(或径向滑板与立柱)的结合面; b)中床身与床身的结合面。 注:对于结构偏重的机床,允许仅在紧固后进行塞尺检验。
6.7下列导轨副按GB/T25373—2010和GB/T25376—2010中“滑动导轨”的要求考核:
a)刀架中的固定导轨(或螺旋导轨)与滑块导轨副; b)工作台(或立柱、径向滑板)与床身导轨副。
b)工作台底座与工作台体导轨副。 6.9按GB/T25374一2010的规定检验机床的清洁度,其中刀架和工作台内部、润滑系统、液压系统的清洁度按重量法检验,其他部位按目测、手感法检验,不应有脏物,具体要求如下:
a)刀架和工作台内部的清洁度限值应不超过本部分表2的规定;
表2机床重要部件清洁度要求
最大工件直径mm
部件名称
≤200
>200~320
>320~500 脏物质量mg
>500~1250
>1250
6 000 5 000
刀架工作台 b)液压系统、润滑系统的清洁度:在机床开车运行30min后,立即在液压系统(或润滑系统)的回油处取样,样品一般不少于200mL,其杂质、污物应不超过150mg/L。
4 000 3000
9 000 7000
12 000 10 000
17 000 14 000
6.10机床数控系统的装配应符合GB/T26220一2010的规定。 6.117 机床液压系统的装配应符合GB/T23572-2009的规定。 6.12 机床润滑系统的装配应符合GB/T6576—2002的规定。
7 空运转试验
7.1 运转检验
机床主运动机构和进给机构应进行空运转试验,试验过程中各机构应运转正常,其空运转试验条件应符合表3的规定。
表3空运转时间平均切削速度
运转时间 min ≥10 ≥10 ≥60
往复冲程次数
圆周进给量
冲程长度
径向进给量
m/min
大中小
大中小
低中高
长中短
≥28
7.2 温升试验 7.2.1插齿刀主轴以最高往复冲程次数空运转应不少于1h,使主轴轴承达到稳定温度后,在靠近刀具主轴轴承的外壳处测量轴承的温度和温升,其值应不超过表4的规定。
表4轴承温度及温升
单位为摄氏度
温度 60 70
轴承型式滑动轴承滚动轴承
温升 30 40
注:机床经过一定时间运转后,当其测量温度值上升幅度不超过每小时5℃时,便可认为达到了稳定温度。
7.3空运转功率试验(抽查)
在插齿刀主轴以中等速度进行整机连续空运转时测量机床空运转功率:其值应不超过设计规定。 7.4动作试验
机床动作试验一般包括下述内容: a)刀具主轴在中等速度下进行包括起动、停止及自动变速等的往复运动各10次,动作应灵活、准
确、可靠。 b)刀具主轴及工作台主轴在中等速度下进行包括起动、停止,自动变速及快速旋转等的圆周运动
各10次,动作应灵活、准确、可靠。 c)立柱(或工作台)进行径向进给及径向微量进给运动各10次,动作应灵活、准确、可靠。 d)用数控程序操作机床,在中等速度下分别对各坐标轴进行正,反向起动、停正(或制动)、工作
进给、快速进给及定向试验,各进行10次,动作应灵活、准确、可靠。对于无级变速的主运动和进给运动,还应做系统的低、中、高及快速的变换操作试验,动作应灵活、可靠。
e)按设计要求,对机床的各坐标轴联动、定位、进给坐标超程保护、坐标位置显示、回基准点、
手动数据输入、程序序号指示和检索、程序暂停、程序消除等功能分别进行试验,其功能应可靠,动作应灵活、准确。
7.5整机连续空运转试验
机床以中等速度模拟工作状态做不切削连续空运转试验,其空运转时间应符合GB/T9061一2006的规定,即机床联动轴数<3时,空运转时间不少于36h;机床联动轴数≥3时,空运转时间不少于48h。 各循环间的休止时间不应超过1min。整个运转过程中,各部分工作应正常、灵活、可靠,不应出现故障;机床的液压、润滑、冷却系统和其他部位均不应渗漏;转动部位的油不应甩出;润滑油路应畅通,切削液应充分;切削液不应混入液压和润滑系统。当机床出现故障时,应加以排除后重新进行试验。
8负荷试验
8.1机床采用切削方法进行负荷试验,其切削条件及规范由设计规定,使机床达到规定的功率(设计功率)。试验过程中,机床各机构应运转正常(抽查)。 8.2机床应按有限功率切削试验的方法(达到主电动机额定功率或设计功率的70%)进行抗振性切削试验,试验条件由设计规定。试验过程中,机床各机构应运转正常。 8.3定型生产的机床按设计规定的切削条件和规范进行负荷试验。试验过程中,机床各机构应运转正常。
9最小设定单位检验
9.1概述
按设计要求,对直线轴坐标进行最小设定单位检验。 9.2试验方法
先以快速使直线运动轴线上的运动部件向正向(或负向)移动一定距离后停止,再向同一方向给出
然后从上述的最终位置,继续向同一方向给出数个最小设定单位的指令,使运动部件移动并停止。从此位置再向负向(或正向)给出数个最小设定单位的指令,使运动部件大约返回到上述最终的测量位置,在这些正向和负向的数个最小设定单位指令下运动部件的停止位置均不做测量。然后从上述的最终测量位置开始,仍向负向(或正向)每次给出1个,共给出20个最小设定单位的指令,继续使运动部件连续移动、停止,大约返回到基准位置,测量其在每个指令下的停止位置,如图1所示。
至少在行程的中间及靠近两端的三个位置分别进行测量。每个直线轴均应检验。
实际移动距离
数个最小设定单位指令下,运动部件的停止位置不做测量
d
中
中
de boo
5
dee
政 dddd
5
LO0
测量范围、
o
最小设定单位
Bea
图1最小设定单位检验
9.3误差计算 9.3.1最小设定单位误差Sa
最小设定单位误差按公式(1)进行计算。
Sa=L-m
(1)
式中: L一某个最小设定单位指令的实际位移值,单位为毫米(mm);
个最小设定单位指令的理论位移值,单位为毫米(mm)。
若实际位移的方向与指令的方向相反,其位移量应为负值。 9.3.2最小设定单位相对误差Sb
最小设定单位相对误差按公式(2)进行计算。
-20m
Su: [il
1a
x100%
(2)
20m
式中:
22
连续20个最小设定单位指令的实际位移的总和,单位为毫米(mm)。
1=1
9.4公差