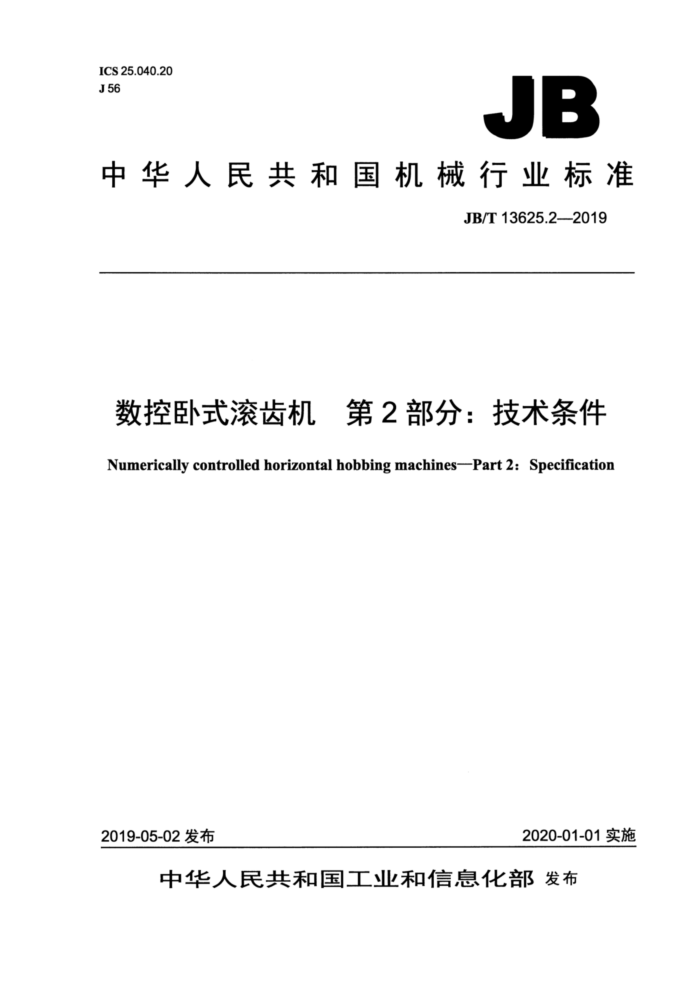
ICS 25.040.20 J56
JB
中华人民共和国机械行业标准
JB/T 13625.2—2019
数控卧式滚齿机 第2部分:技术条件
Numerically controlled horizontal hobbing machines-Part 2: Specification
2019-05-02 发布
2020-01-01实施
中华人民共和国工业和信息化部发布
JB/T 13625.2—2019
目 次
前言. 1 范围, 2规范性引用文件 3一般要求.. 4附件和工具.. 5安全卫生.. 6加工和装配质量空运转试验…… 7.1 温升试验, 7.2 主运动和进给运动的检验(抽查) 7.3动作试验 7.43 空运转功率试验 (抽查) 7.5 连续空运转试验 8负荷试验.. 9最小设定单位试验 9.1 试验方法, 9.2 误差计算方法. 9.3 允差, 9.4 检验工具. 10原点返回试验.. 10.1 试验方法, 10.2 误差计算方法. 10.3 允差.. 10.4 检验工具 11精度检验. 12包装
I
7
图 1 最小设定单位进给试验图2原点返回试验.
表 1 随机供应附件和工具表.清洁度指标.
2
..0...
JB/T 13625.2—2019
前 言
JB/T13625《数控卧式滚齿机》分为两个部分:
第1部分:精度检验; -第2部分:技术条件。
本部分为JB/T13625的第2部分。 本部分按照GB/T1.1一2009给出的规则起草。 本部分由中国机械工业联合会提出。 本部分由全国金属切削机床标准化技术委员会(SAC/TC22)归口。 本部分起草单位:四川普什宁江机床有限公司、重庆机床(集团)有限责任公司、浙江佳雪微特电
机集团有限责任公司。
本部分主要起草人:缪丹、李学伟、张学智、喻可斌、姚志学。 本部分为首次发布。
I
JB/T13625.2—2019
数控卧式滚齿机第2部分:技术条件
1范围
JB/T13625的本部分规定了数控卧式滚齿机的设计、制造、检验和验收的要求。 本部分适用于最大工件直径至500mm、最大模数至6mm的数控卧式滚齿机(以下简称机床)。
2规范性引用文件
下列文件对于本文件的应用是必不可少的。凡是注日期的引用文件,仅注日期的版本适用于本文件。凡是不注日期的引用文件,其最新版本(包括所有的修改单)适用于本文件。
GB5226.1--2008机械电气安全机械电气设备第1部分:通用技术条件 GB/T9061一2006金属切削机床通用技术条件 GB/T9239.1一2006机械振动恒态(刚性)转子平衡品质要求第1部分:规范与平衡允差的
检验
GB 15760—2004 金属切削机床安全防护通用技术条件 GB/T17421.2机床检验通则第2部分:数控轴线的定位精度和重复定位精度的确定 GB/T17421.5一2015机床检验通则第5部分:噪声发射的确定 GB/T23570—2009金属切削机床焊接件通用技术条件 GB/T 23571—2009 金属切削机床随机技术文件的编制 GB/T 25373—2010 金属切削机床装配通用技术条件 GB/T 25374—2010 金属切削机床清洁度的测量方法 GB/T 25376—2010 金属切削机床机械加工件通用技术条件 JB/T8356—2016机床包装技术条件 JB/T 13625.1—2019 数控卧式滚齿机第1部分:精度检验
3一般要求
按本部分验收机床时,还应对GB/T9061一2006、GB/T23570一2009、GB/T25373一2010、GB/T
25376一2010等中未经本部分具体化的有关项目进行经验
4附件和工具
4.1应随机供应表1所列的附件和工具。
表1随机供应附件和工具
名称常用滚刀心轴组件
用途
数量 1套 1套 1套 1套
说明
包括心轴、垫圈、螺母、键等
安装常用尺寸规格滚刀用
专用扳手垫铁地脚螺栓
辅助工具安装机床用安装机床用
1
JB/T13625.2—2019
4.2扩大机床性能的特殊附件,可根据订货协议提供。
5安全卫生
5.1 机床的安全防护应符合GB15760—2004、GB5226.1—2008的规定。 5.2按GB/T17421.5-2015的规定测量整机的噪声,其噪声声压级不应超过83dB(A)。机床运转时,不应有异常的尖叫声、冲击声。
6加工和装配质量
6.1机床的底座、主轴箱、轴向滑座、径向滑座、切向滑板、尾座等重要铸件,应在粗加工后进行热时效或振动时效等时效处理。必要时半精加工后再进行一次时效处理。 6.2各进给运动导轨副应采取耐磨措施(如耐磨铸铁、滚动导轨、表面淬硬处理等)。 6.3主轴箱安装面、尾座安装面、轴/径向滑座、切向滑板导轨面均不应焊补。 6.4下列结合面为“特别重要固定结合面”:
a)主轴箱与底座的结合面; b)尾座与底座的结合面; c)滚刀架体与径向滑座的结合面。
6.5下列导轨为“滑/滚动导轨”副
a)径向滑座径向进给导轨副; b)轴向滑座轴向进给导轨副; c)切向滑板切向移动导轨副; d)尾座轴向移动导轨副。
6.6尾座与底座导轨副为“移置导轨”副。除机床尾座与底座结合处按“移置导轨”的要求检验,其余运动轴按“滑/滚动导轨”的要求检验。 6.7重要部位的紧固螺钉的紧固力矩应符合设计文件的规定。 6.8镶钢或镶铜导轨、拼接导轨的接合处应留有一定的缝隙值。接合处相邻导轨导向面的错位量应符合GB/T25373-2010的规定。 6.9主轴组件装配后应按GB/T9239.1一2006进行动平衡和校正,平衡品质等级应符合设计文件的规定。 6.10按GB/T25374一2010抽查(批量生产时抽查5%,但不少于一台)机床总装后的清洁度。其中主轴箱等内部清洁度按质量法进行检测,其杂质、污物的质量不应超过本部分表2的规定,其他部位用目测、手感法进行检测,不应有明显的脏物。
表2清洁度指标
最大工件直径mm
<80
部位
≥80
脏物质量 mg
主轴箱
1 000
1 200
2
JB/T 13625.2—2019
7空运转试验
7.1温升试验
机床滚刀主轴做低、中、高三档转速运转,运转时应安装随机提供的滚刀杆,每级转速的运转时间不少于2min,最高转速运转时间不应少于1h。当滚刀主轴轴承达到稳定温度时,在靠近滚刀主轴轴承处测量其温度和温升,温度不应超过65℃,温升不应超过35℃。机床滚刀主轴转速不应超过公称值的 110%。 7.2主运动和进给运动的检验(抽查) 7.2.1检验滚刀主轴转速和进给机构进给量的实际偏差,分别不应超过设定值的土10%。 7.2.2对各进给轴线的运动部件,在全行程上分别用低、中、高进给速度和快速进行空运转试验,试验时,机床各运动部件运动应平稳、灵活,无明显爬行和振动,限位装置应可靠。 7.2.3对各线性运动部件在低、中、高进给速度和各坐标轴行程范围内进行不少于10次的试验,其中快速行程应大于1/2全行程。 7.3动作试验 7.3.1按低、中、高进给速度,在各坐标轴行程范围内做工作进给和快速移动速度试验。其中快速行程应大于1/2全行程。正、反向起动、停止连续操作试验10次,动作应灵活、可靠。 7.3.2按设计要求,对机床的各坐标轴联动、定位、直线插补、圆弧插补、进给坐标超程保护、坐标位置显示、回基准点、手动数据输入、程序序号指示和检索、程序暂停、程序消除等功能分别进行试验,其功能应可靠,动作应灵活、准确。 7.3.3有夹紧机构的运动部件在各自全部运动范围内的任意工作位置上(一般选3~5个位置)进行夹紧试验,动作应可靠、灵活。 7.3.4用手摇脉冲发生器移动各坐标上的运动部件,其动作应灵活、准确。 7.4空运转功率试验(抽查)
在滚刀主轴各级转速下,测量机床各级转速的空运转功率,其值应符合设计文件的规定。 7.5连续空运转试验 7.5.1机床按设计文件规定的程序(应包括机床主要加工功能在内的数控程序)模拟工作状态做不切削的连续空运转试验,连续空运转时间为48h。 7.5.2试验时机床运转应正常、平稳、可靠,不应发生故障,否则在故障排除后应重新进行连续空运转试验。 7.5.3连续空运转应包括滚刀主轴低、中、高进给速度,在接近全行程范围内进行,高进给速度的运行时间宜不少于每个循环所用时间的10%。
8负荷试验
8.1机床可以标称的最大模数切削试验代替主传动系统最大功率试验和扭矩试验,试验时,改变切削参数,使工件主轴和滚刀主轴电动机达到最大设计功率(或扭矩)。 8.2最大模数切削试验所用的齿坏直径应不小于机床标称最大规格的65%。 8.3在负荷试验时,机床各部位工作应正常稳定,无异常尖叫,试件齿面均匀,无明显振纹。
3
JB/T13625.2—2019
9最小设定单位试验
9.1试验方法
先以快速使直线坐标上的运动部件向正(或负)向移动一定距离,停止后,向同方向给出数个最小设定单位指令,以此位置作为基准位置,每次给出1个,共给出20个最小设定单位指令,使运动部件向同方向移动,测量各指令的停止位置。从上述的最终位置,继续向同方向给出数个最小设定单位指令,停止后,向负(或正)向给出数个最小设定单位指令,使运动部件约返回到上述的最终测量位置,这些正向和负向的数个最小设定单位指令下运动部件的停止位置不做测量。然后从上述最终测量位置开始,每次给出1个,共给出20个最小设定单位指令,使运动部件继续向负(或正)向移动,测量各指令停止位置,如图1所示。
数个最小设定单 实际移动距离位指令下运动部件的停止位置不做测量
效 双双双双
中
双双双 双双
51
测量范围
B
双双双 &
双双双双双双 d
双
最小设定单位
双
8
图1最小设定单位进给试验
至少在行程的中间及两端3个位置分别进行试验,各直线坐标均应进行试验。按9.2的规定计算误差,以3个位置上的最大误差值作为该项的误差。
具有螺距误差、间隙补偿装置的机床,可在使用这些装置的情况下进行试验。 注:要注意实际转动的方向。
9.2误差计算方法
误差计算方法如下: a)最小设定单位误差Sa按公式(1)计算。
(1)
Sa=|L;-m|max
式中: Sa一最小设定单位误差,单位为毫米(mm); L;一一1个最小设定单位指令的实际位移,单位为毫米(mm);
一1个最小设定单位指令的理论位移,单位为毫米(mm)。
m-
注:实际位移的方向如与给出的方向相反,其位移应为负值。 b)最小设定单位相对误差S按公式(2)计算。
4
JB/T 13625.2—2019
20
ZL; -20m Sp i=1
Imax × 100%
·(2)
20m
式中:
Sp -最小设定单位相对误差;
2L
-20个最小设定单位指令的实际位移之和,单位为毫米(mm)。
台
9.3允差
允差应符合以下要求:
-Sa:根据机床的具体情况由制造厂自行规定; -Sb:不应大于25%。
9.4检验工具
激光干涉仪或其他长度检测装置。
10原点返回试验
10.1试验方法
各直线坐标上的运动部件,从行程上的任意点按相同的移动方向,以快速进行5次返回原点Po试验。测量每次实际位置Pio与原点理论位置Po的偏差Xio(=1,2,,5),如图2所示。
Po Xo
i=1
QP1O
X20 QR 蓝
i=2
X30
i=3
X40
i=4
P40
Xso
i=5
Pso 图2原点返回试验
各直线坐标至少在行程的中间及靠近两端的任意3个位置进行试验,按10.2的规定计算误差,以3
个位置上的最大误差值作为该项的误差。
设有向原点自动返回功能的机床宜进行本项试验。具备螺距误差、间隙补偿装置的机床,可在使用这些装置的情况下进行试验。 10.2误差计算方法
各直线坐标中,原点返回试验时的4倍标准不确定度的最大值,即为原点返回误差Ro,按公式(3)
5