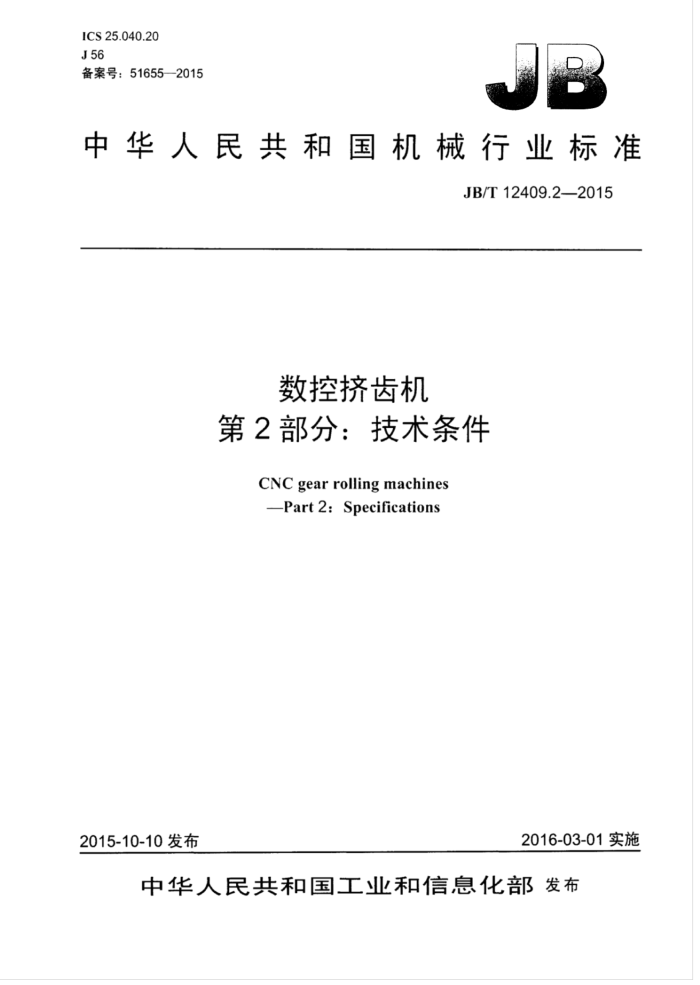
ICS25.040.20 J56 备案号:51655—2015
中华人民共和国机械行业标准
JB/T12409.2—2015
数控挤齿机第2部分:技术条件
CNC gearrollingmachines Part2:Specifications
2016-03-01实施
2015-10-10发布
中华人民共和国工业和信息化部发布
JB/T12409.2—2015
目 次
前
.....II
范间. 2 规范性引用文件技术要求
1
3
3.1 股要求 3.2 参数. 3.3 附件和具. 3.4 布局和外观 3.5 电气系统 3.6 数控系统 3.7 液和润滑系统 3.8 安个生 3.9 加!和装配质量 3.10 机床的牢运转试验婴求 3.11 机床的负荷试验要求 3.12 机床的最小设定单位检验要求 3.13 机床的精度检验要求. 4检验验收 4.1 概述, 4.2 般要求 4.3 参数检验(查) 4.4 附件和下具的检验 4.5 布局和外观检验.. 4.6 电气系统检验 4.7 数控系统的检验. 4.8 液压和润滑系统的检验 4.9 安全1生检验 4.10 机床加工和装配质量检验, 4.11 机床的空运转试验 4.12 机床的负荷试验 4.13 机床的最小设定单位检验. 4.14 机床的精度检验 5包装
.6 HC
表1附件和工具表2错位量及贴合缝隙值表3轴承温度及温升限值
JB/T12409.2—2015
前言
JB/T12409《数控挤齿机》分为两个部分:
第1部分:精度检验:第2部分:技术条件。
本部分为JB/T12409的第2部分。 本部分按照GBT1.1-2009给山的规则起草。 本部分出中国机械「业联合会提出。 本部分用全金属切机标雅化技术委员会(SAC/TC22)。 本部分起草单位:庆机床(集)有限责低公司、重庆神工机械制造有限货任公同、家机床质
监督检验啡心、南京:机轮机床作限公司、天洋第机床总、审长机科技行限贵公司。
本部分要起草人:全毅、李先、喻叮斌、赵耀、邓福安、祥文、蒋小彦、刘德个、钟瑞龄。 本部分为首次发布。
II
JB/T12409.2—2015
数控挤齿机第2部分:技术条件
1范围
JB/T12409的本部分规定了数控挤齿机设计、制造、检验与验收的要求本部分适用」最大加1直径至250mm、最人加厂模数至5mm的挤倒维齿的数控挤齿机(以下简
称机床)。
2规范性引用文件
下列文件对本文件的应是必不可少的。凡是注期的用文件,仪注「期的版本适用」本文件。 凡是不注日期的啡用文件,最新版本(包括所有的修改单)适用本文件。
GB5226.1—2008 机械电(安个机械心设备第1部分:通用技术条件 GB/T6576—2002 机床润滑系统 GB/T9061-2006 金腐切削机床 通技术条件 GB 15760-2004 金底切削机床安全防护通用技术条件 GB/T16769—-2008 金底切削机床 噪级测量方法 GB/T23570—2009 金腐切削机床焊接件通用技术条件 GB/T23571- 2009 金属切削机床随机技术文件的编制 GB/T23572--2009 金属切削机床 液压系统通用技术条件 GB/T25372—2010 金属切削机床精度分级 GB/T25373-2010 金属切刷机床 装配通用技术条件 GB/T25374—2010 金属切削机床清洁度的测量方法 GB/T25376—-2010 金属切削机床机械加T件通用技术条件 GB/T26220—2010 干业自动化系统与集成机床数值控制数控系统通用技术条件 JB/T3997—2011 金属切削机床灰铸铁件技术条件 JB/T8356.1—1996 机床包装技术条件 JB/T8356.21996 机床包装箱 JB/T12409.1—2015 数控挤齿机第1部分:精度检验
3技术要求
3.1一般要求 3.1.1按本部分验收机床时,还以对GB5226.1—2008、GB/T9061—2006、GB/T23570—2009GB/T 25373—2010、GB/T25376一2010中未经本部分具体化的有关项目进行检验。 3.1.2机床验收时,以按GB/T25372一2010规定的V级精度机床的要求检验。
1
JB/T12409.2-2015
3.2参数
机床的参数以符合设计文件的规定。机床与火量具、附件等连接部位的型式和尺小应符合有关标准的规定。 3.3附件和工具 3.3.1机床随机供应表1所列的附种和1具。
表1附件和工具
用 途调整床身安装水安装具挤轮
数量 4件作 2 1
名称减是塔铁 J杆内六角搬于
安装工装
3.3.2扩人机床性能的特殊附件,可根据用广要求按协议供应。 3.4布局和外观 3.4.1机床布局合理、造型美观、色彩利谐,设计符合人类「效学原则并便调整及维修。 3.4.2 机床外观表面,不有未规定的起,降。料糙不平和其他损伤。 3.4.3机床的防扩留及防护装置应表面斗平整、匀称,不翘山、叫陷。 3.4.4机床外露零件表而不有磕碰、锈蚀,螺旬、铆钉、销子端部不以有扭伤、锤伤等缺降。 3.4.5金属手轮轮缘和操纵手柄表面应涂防锈层。电镀件、发黑件色调应-致,防层不应有褪色、 脱落现象。 3.4.6机床涂漆颜色及光泽以均匀一致,涂漆层以平整,涂漆表面不应有起泡及脱落等缺降。机床可拆卸的装配结合面的接缝处,在涂漆以后,切开,切开时不应扯破边缘。 3.4.7机床的各种信息标志及标牌应在机床明显位置平整固定,清晰耐久,不歪斜。 3.4.8机床电气、液压及润滑等的管道的外露部分,布置紧凑、排列整齐,不应产生批山、折叠及断裂等现象。 3.4.9装入沉孔的螺钉不应凸出零件表面,其头部与沉孔之问不应有明显的偏心,定位销般略凸出零件表面。螺栓尾端应略凸出螺端面。外露轴端凸出包容件的端面,凸出值约为倒棱值。内孔表面与壳体凸缘问的壁厚以均匀对称,其凸缘壁厚之差不大实际最大壁厚的20%。 3.4.10机床零部件外露结合面的边缘应整齐匀称,不应有明显的错位,门、盖与机床的结合面应贴合。 错位量及贴合缝隙值不应大表2的规定。
表2错位量及贴合缝隙值 ≤500
单位为毫米
结合面边缘及门、盖边长八寸
>500~1250
>12503150
错位量错位不匀称量贴合缝隙值缝隙不均勾值
1.5 1 1 I
2
3 1.5 2 2
1.5 1.5
注1:当结合面边缘及门、盖边长的长、宽心寸不一致时,可按长边尺寸确定允许值。 注2:错位不匀称量指外露结合面边缘同一边或对成边最人错位量与最小错位量之差值。 注3:缝隙不均匀值指门、盖间对开缝或其相对机床本体间最人缝隙值最小缝隙之差值。
2
JB/T12409.2—2015
3.5电气系统
机床的电气系统符合GB5226.1-2008的规定。 3.6数控系统
机床的数控系统符合GB/T26220-2010的规定。 3.7液压和润滑系统 3.7.1机床的液系统应符合GB/T23572-2009的规定。 3.7.2机床的润滑系统应符合GB/T6576-2002的规定。 3.7.3机床的液压系统、润滑系统及其他部位均不应渗满。 3.8安全卫生 3.8.1机床1有可能对人体健康或对设备造成损伤的部位,应采取安全措施,机床的安个防护应符合 GB15760—2004-GB5226.1--2008的规定。 3.8.2在机床加厂×设置防护留,工起够的强度和刚性。防护装置的设置应便「件的置换以及操的观。 3.8.3外露而易被尘屑磨损的导轨副应安装防护装置。 3.8.4液系统能提供稳定的正带作的用力,力超设定限值时,应发出整售信子或使机床运动停山。 3.8.5按GB/T16769-2008的规定测量机床的运转噪,其噪市市级不超过83dB(A。机床运转时,不应有异带的叫、冲。 3.9加工和装配质量 3.9.1机械加.I件、焊接件符合图样「艺文件及GB/T25376—2010GB/T23570—2009等标准的规定。机床的装配应符合GB/T25373—2010的规定。 3.9.2机床火铸铁件小以符合JB/T3997—2011的规定。 3.9.3机床的床身、立柱、刀轴壳体。减速箱壳体等重要铸件,应在粗加下后进行热时效或振动时效等时效处理。 3.9.4进给丝杠副、工作台、托盘等工要零件以采取耐磨措施,川符合材质及热处理有关标准的规定。 3.9.5床身与立柱的结合面、刀轴壳体与床身的结合面、床身与减速箱壳体的结合面等重要固定结合面,具制造及验收应符合GB/T25376一2010和GB/T25373一2010的规定。 3.9.6机床的清洁度的检测按GB/T25374一2010规定的方法进行,机床液压、润滑系统的清洁度:在机床运行30min后,立即在液压系统(或润滑系统)回汕L处取样,-股不少」200mL,其杂质、污物不超过150mg/L。 3.10机床的空运转试验要求 3.10.1运转检验 3.10.1.1在无负荷状态下,机床刀具轴主运动机构应从最低速度起依次运转,每级速度的运转时问不得少了2min。高速运转不以少1h,使主轴轴承达到稳定温度。 3.10.1.2机床各直线运动部件在全行程上分别做低、中、高进给量(或进给速度)和快速进给的空行程试验,其运动应平稳、灵活,无明显的爬行和振动现象。
3
JB/T12409.2--2015
3.10.2温升试验 3.10.2.1正轴轴承达到稳定温度时,靠近刀上轨轴承的外光处测量轴承的温度和温升,其值不超过表3的规定。
表3轴承温度及温升限值
单位为摄氏度
温川 30 40
L度 60 70
轴示型式滑动示滚动灿承
注:机床终过-定时间运转后,"其测量温度值升幅度不超过5℃/h时,可认为达到广稳定温度 3.10.2.2液系统额定1作力下连续运转,洲液达到稳定温度底,测来汕液的温度和温升, H流度不超过60℃,温升不超过30℃。 3.10.3主运动和进给运动的检验(抽查)
检验刀正转速租进给机构进给量的实际偏差,分别不得超过标牌指催的土5%租士10%。试验时机床各运动部件运动应平稳、可带。 3.10.4动作试验
机床动作试验般包拓下述内容: a)机床刀!输在等转速下连续起动、停各10次,动作应准确,无故障。 b)检验辅助支承轴(套简)[下移动的可需性,1下移动应不少」o次。 c)检验作台旋转的平稳性,川手拨动「作台旋转,『作台转动平稳,无下滞现象。 d)检验用盘转动的灵活度,手动转动时无卡滞现象。 e)用数控程厅操作机床,在等速度下分别对各整标轴进行正、反间起动、停山:(或制动)、工作
进给、快速进给及定间试验,各进行10次,动作以灵活、准确、可靠。对无级变速的正运动和进给运动,还以做系统的低、十、高及快速的变换操作试验,动作以灵活可靠。
f)按设计要求,对机床的各整标轴联动、定位、进给必标超程保护、整标位置显示、问基准点、
手动数据输入、程序序号指示和检索、程序暂停、程序消除等功能分别进行试验,其功能应可靠,动作小以灵活、准确。
3.10.5空运转功率试验(抽查)
在刀具正轴各级转速下运转至功率稳定后,测量机床的空运转功率,其值不超过设计规定。 3.10.6整机连续空运转试验
机床模拟工作状态进行连续空运转试验,循环过程以包括各种程序功能,其连续运转时问为:当联动轴数<3时,其连续运转时问不少」36h,当联动轴数≥3时,其连续运转时问不少」48h。在空运转过程中,各部分工作应正常,运行应平稳。各项功能、性能应可靠,不出现故障。各次循环程序之问的体时问不应超过1min。当出现异常或故障时应查明原因并加以排除,然后重新进行试验。 3.11机床的负荷试验要求 3.11.1机床挤齿试验
机床可用挤齿试验代替正传动系统的最大功率试验和转矩试验。在试验时,改变挤齿参数,使机床主电动机达到设计功率或刀具主轴的最大设计转矩。试验还应符合以下要求: 4
JB/T12409.2-2015
a)机床挤大模数时,机床电动机功率短时应不超过额定功率的30%: b)机床重力挤压时,各部位应「作正常稳定,无异常失叫,试件齿而无明显振纹,各种传动及
变速机构应平稳、可靠,机床各运动应准确,机床电气、液压、润滑系统应正带「作。
3.11.2机床生产率试验(抽查)
在挤标准(模数2mm,欧数33)达到挤以要求时,检查挤以效率。正带挤时间不应超过12s (转、反转》。 3.12机床的最小设定单位检验要求
按设计要求,对向线伦标进行最小设定单位检验。最小设定单位进给误差不以超过6m,最小设定单位的相对误差不应超过士25% 3.13机床的精度检验要求
机床的精度检验符个JB/T12409.1-2015的规定。
4检验验收
4.1概述 4.1.1年台机床应在制造厂纶检验合格原出厂,特殊情况下经用广同意可在机床便用处进行检验。 在机床使用处验收机床川,其验收的项山广与制造广商定。 4.1.2机床检验分为型式试验和检验 4.1.3凡有下列情况之:-时,进行型式试验
a)新产品试制、定型鉴定: b)机床结构:性能较基型有重大改动。
4.1.4机床出厂检验股包括以下内容:
a)外观检验: b)附件和工具检验: c)参数检验(抽查): d)机床的空运转试验(含抽查项》: e)机床的负荷试验(含抽查项): f)机床的最小设定单位检验: g)机床的精度检验。
4.2一般要求
4.2.1机床检验时,必注意防Ⅲ气流、光线和热辐射的干扰,应防山受环境温度变化的影响。机床应在规定的恒温条件下进行检验,检具在使用前应与机床等温。 4.2.2检验与验收前,将机床安置在适当的基础上,按照制造商的使用说明书调平机床,并应符合 JB/T12409.1—2015规定的安装要求。 4.2.3检验过程中,不应调整影响机床精度和性能的机构和零件。用地脚螺栓紧固的机床,在检验过程中不应重新调整安装水平。否则,应复检调整后受到影响的有关项目。 4.2.4检验原则上是在制造完毕的成品上进行,特殊情况下可按制造商的使用说明书拆卸某些零、部件。 4.2.5机床由」结构上限制或不具备规定的测试工其,可采用与本部分有等同效果的替代方法进行
5