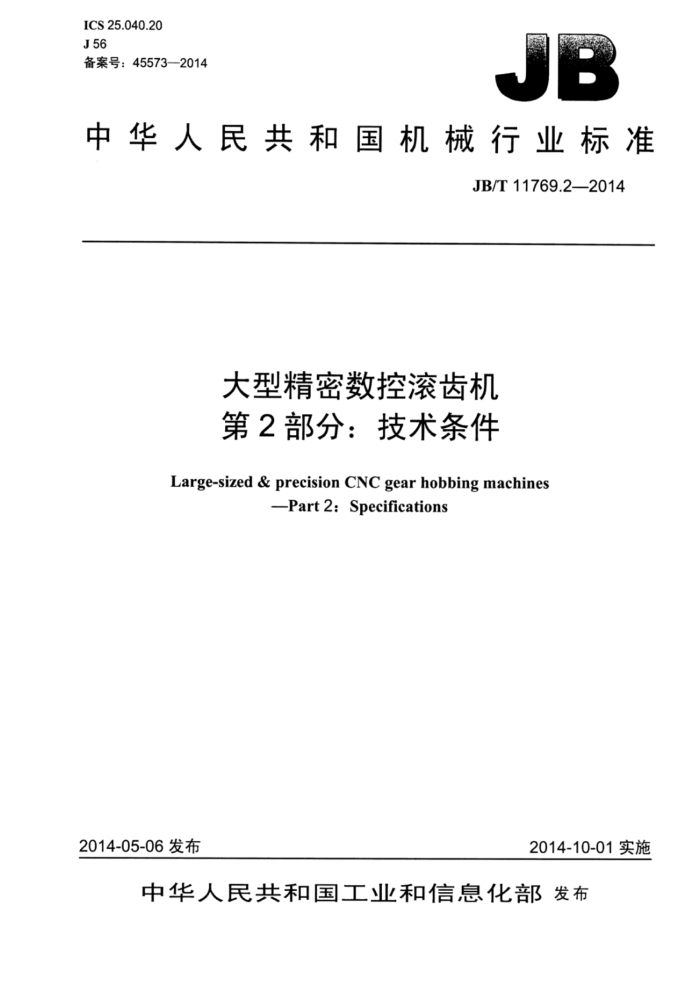
ICS25.040.20 J56 备案号:45573-2014
中华人民共和国机械行业标准
JB/T11769.22014
大型精密数控滚齿机第2部分:技术条件
Large-sized & precision CNC gear hobbing machines
-Part2:Specifications
2014-10-01实施
2014-05-06发布
中华人民共和国工业和信息化部发布
JB/T11769.2—2014
目 次
前言. 1范围 2规范性引用文件 3技术要求.
3.1一般要求, 3.2 参数 3.3 附件和工具. 3.4 布局和外观 3.5 电气系统.... 3.6 数控系统 3.7 液压、润滑和冷却系统. 3.8 安全卫生 3.9 加工和装配质量 3.10 机床的空运转要求. 3.11 机床的负荷要求. 3.12 机床的最小设定单位要求。 3.13 机床的精度要求 3.14 其他要求, 4检验与验收 4.1 般要求. 4.2 参数检验(抽查) 4.3 附件和工具的检验, 4.4 布局和外观检验, 4.5 电气系统检验, 4.6 数控系统的检验. 4.7 液压、冷却和润滑系统的检验 4.8 安全卫生检验 4.9 机床加工及装配质量检验, 4.10 机床的空运转试验 4.11 机床的负荷试验. 4.12 机床的最小设定单位检验 4.13 机床的精度检验 4.14其他检验. 5包装
5 6 一
6
8
5
表1 附件和工具表2错位量及贴合缝隙值表3轴承温度及温升限值
JB/T11769.2—2014
前言
JB/T11769《大型精密数控滚齿机》分为两个部分
第1部分:精度检验:一第2部分:技术条件。
本部分为JB/T11769的第2部分。 本部分按照GB/T1.1—2009给出的规则起草。 本部分由中国机械工业联合会提出。 本部分由全国金属切削机床标准化技术委员会(SAC/TC22)归口。 本部分起草单位:重庆机床(集团)有限责任公司、武汉重型机床集团有限公司、重庆大学、南京
二机齿轮机床有限公司、天津第一机床总厂、青海第二机床制造有限责任公司、齐重数控装备有限公司。
本部分主要起草人:喻可斌、李先广、李毅、伍竞平、王时龙、杨灿辉、李光华、柴宝莲、颜芳、 胡巍。
本部分为首次发布。
II
JB/T11769.2-—2014
大型精密数控滚齿机第2部分:技术条件
1范围
JB/T11769的本部分规定了大型精密数控滚齿机设计、制造、检验与验收的要求。 本部分适用于最大加工直径2000mm~6300mm立式布局的大型精密数控滚齿机(以下简称机
床》。
2规范性引用文件
下列文件对于本文件的应用是必不可少的。凡是注日期的引用文件,仅注日期的版本适用于本文件。凡是不注日期的引用文件,其最新版本(包括所有的修改单)适用于本文件。
GB5226.1一2008机械电气安全机械电气设备第1部分:通用技术条件 GB/T65762002机床润滑系统 GB/T9061一2006金属切削机床通用技术条件 GB/T10089—1988圆柱蜗杆、蜗轮精度 GB15760—2004 金属切削机床安全防护通用技术条件 GB/T16769—2008金属切削机床噪声声压级测量方法 GB/T17421.1-1998 机床检验通则第1部分:在光负荷或精加工条件下机床的几何精度 GB/T23570—2009 金属切削机床焊接件通用技术条件 GB/T235712009 金属切削机床 随机技术文件的编制 GB/T23572—2009 金属切削机床 液压系统通用技术条件 GB/T25372—2010 金属切削机床 精度分级 GB/T25373—2010 金属切削机床 装配通用技术条件 GB/T25374—2010 金属切削机床 清洁度的测量方法 GB/T25376—2010 金属切削机床 机械加工件通用技术条件 GB/T262202010 工业白动化系统与集成机床数值控制数控系统通用技术条件 JB/T3997一2011金属切削机床灰铸铁件技术条件 JB/T8356.11996 5机床包装技术条件 JB/T8356.2—1996 机床包装箱 JB/T11769.1一2014大型精密数控滚齿机第1部分:精度检验
3技术要求
3.1一般要求
3.1.1本部分是对GB/T9061—2006、GB/T23570—2009、GB/T25373—2010、GB/T25376—2010等标准的具体化和补充,机床的设计与制造除应符合本部分的规定外,还应符合上述标准中未经本部分具体化的其他技术要求。
1
JB/T11769.2—2014
3.1.2验收机床时,按GB/T25372一2010规定的IV级精度机床的要求检验。 3.2参数
机床参数符合技术文件的规定。机床与工夹量具、附件等连接部位的型式和尺寸应符合有关标准的规定。 3.3附件和工具 3.3.1机床应随行供应表1所列的附件和工具。
表1附件和工具
数量 1套 1套 1套一套 1套 1套
备注
名称滚刀心轴工件心轴专用扳手工件托座垫铁地脚螺栓
用途
包括装于心轴上的垫圈、平键、套及螺母等包括装于心轴上的垫圈、螺母及接盘等
调整机床及装夹滚刀用调整机床及装夹工件用调整、操作机床用
装夹工件心轴用安装机床用安装机床用
3.3.2扩大机床性能的特殊附件,可根据用户要求按协议供应。 3.4布局和外观 3.4.1 机床应布局合理、造型美观、色彩和谐,符合人类工效学原则并便于调整及维修。 3.4.2# 机床外观表面,不应有图样未规定的凸起、凹陷,粗糙不平和其他损伤。 3.4.3 机床的防护罩及防护装置应表面平整、匀称,不应翘山、凹陷。 3.4.4 机床外露零件表面不应有磕碰、锈蚀,螺钉、铆钉、销子端部不应有扭伤、锤伤等缺陷。 3.4.5金属手轮轮缘和操纵手柄表面应涂层防锈。电镀件、发蓝件、发黑件色调应一致,防护层不应有褪色、脱落现象。 3.4.6机床涂漆颜色及光泽应均勾一致、涂漆层应平整,涂漆表面不应有起泡及脱落等缺陷。机床可拆卸的装配结合面的接缝处,在涂漆以后应切开,切开时不应扯破漆面。 3.4.7机床的各种信息标志及标牌应在机床明显位置平整固定、清晰耐久,不歪斜。 3.4.8机床电气、液压、润滑及冷却等的管道的外露部分,应布置紧凑、排列整齐,不应产生扭曲、 折叠及断裂等现象。 3.4.9装入沉孔的螺钉一般不应突出于零件表面,其头部与沉孔之间不应有明显的偏心,固定销一般应略突出于零件表面。螺栓尾端应略突出于螺母端面。外露轴端应突出于包容件的端面,突出值约为倒棱值。内孔表面与壳体凸缘间的壁厚应均勾对称,其凸缘壁厚之差不应大于实际最大壁厚的20%。 3.4.10机床零部件外露结合面的边缘应整齐匀称,不应有明显的错位,门、盖与机床的结合面应贴合。 错位量及贴合缝隙值不应大于表2的规定。 3.5电气系统
机床的电气系统应符合GB5226.1一2008的规定。 3.6数控系统
机床的数控系统应符合GB/T26220一2010的规定。
2
JB/T11769.2—2014
3.7液压、润滑和冷却系统 3.7.1机床的液压系统应符合GB/T23572—一2009的规定。
表2错位量及贴合缝隙值 ≤500
单位为毫米 >3 150 4 2
结合面边缘及门、盖边长尺寸
>1250~3150
>500~1250
错位量错位不匀称量贴合缝隙值缝隙不均匀值
1.5 1 1 1
2 1 1.5 1.5
3 1.5 2 2
注1:当结合面边缘及门、盖边长尺寸的长、宽不一致时,可按长边尺寸确定允许值。 注2:错位不勾称量指外露结合面边缘同一边或对应边最大错位量与最小错位量的差值。 注3:缝隙不均勾值指门、盖间对开缝或其相对机床本体间最大缝隙值与最小缝隙的差值。
3.7.2机床的润滑系统应符合GB/T6576—2002的规定。 3.7.3机床的冷却系统应保证冷却充分、可靠。 3.7.4机床的液压、润滑、冷却系统及其他部位均不应漏(渗)油、漏(渗)水。切削液不应混入液压系统和润滑系统。 3.8安全卫生 3.8.1机床上有可能对人身体健康或对设备易造成损伤的部位,应采取安全措施,机床的安全防护应符合GB15760—2004、GB5226.1—2008的规定。 3.8.2在机床加工区应设置防护罩或挡板,并应具有足够的强度和刚度。防护装置的设置应便汀工件的置换及操作者的观察。 3.8.3外露而易被尘屑磨损的导轨副应安装防护装置。 3.8.4液压系统应能提供稳定的正常工作的压力,当低设定限值时,应发出警告信号或使机床运动停止。 3.8.5采用静压时,应保证静压建立后才能起动,压力变化超过规定或中断时应能保证安全。 3.8.6按GB/T16769—2008的规定测量机床的空运转噪声,其噪声声压级不应超过85dB(A)。机床运转时,不应有异常的尖叫声、冲击声。 3.9加工和装配质量 3.9.1机械加T件、焊接件应符合图样、T艺文件及GB/T23570一2009、GB/T25376—2010等的规定。 机床的装配应符合GB/T25373—2010的规定。 3.9.2机床灰铸铁件应符合JB/T3997—2011的规定。 3.9.3机床的床身、立柱、工作台、工作台壳体、刀架滑板、主传动箱、进给箱、分度蜗轮、刀架壳体、小立柱和拼装床身的工作台底座等重要铸件,应在粗加工后进行热时效或振动时效等时效处理。 3.9.4床身导轨副、立柱导轨副、小立柱导轨副、切向(或组合)刀架导轨副、工作台圆导轨副以及具有A轴的刀架回转导轨副等重要导轨副,应采取符合相应寿命的耐磨措施。 3.9.5滚刀主轴、轴向进给丝杠副、径向进给丝杠副、切向进给丝杠副、分度蜗杆(或齿轮)副、高速负载齿轮副、刀架末端斜齿轮副(或蜗杆副)、工作台定心套等零件应采取耐磨措施,并符合材质及热处理有关标准的规定。 3.9.6传动箱与立柱(或床身)的结合面、主传动锥齿轮座与刀架滑板的结合面、最大T件直径等」 2000mm滚齿机的床身与T作台底座、步进电动机及伺服电动机安装面、滑动导轨的压板结合面等重
3
JB/T11769.2—2014
要固定结合面,其制造及验收应符合GB/T25376—2010和GB/T25373一2010的规定。 3.9.7床身与立柱(或工作台壳体)的结合面,工作台壳体(或床身)与小立柱底面的结合面,分度蜗杆托座、工作台壳体(工作台底座)与调整垫的结合面,小立柱底面与其底座的结合面、滚珠丝杠螺母底座的结合面等特别重要固定结合面,其制造及验收应符合GB/T25376—2010和GB/T25373—2010 的规定。 3.9.8立柱导轨副、工作台圆环导轨副、刀架切向滑动导轨副以及床身导轨副、具有A轴的刀架回转导轨副等滑动导轨以及其余的移置导轨,其制造及验收应符合GB/T25376—2010和GB/T25373一2010 的规定。 3.9.9镶钢或镶铜导轨、拼接导轨的接合处应留有一定的缝隙值。接合处相邻导轨导向面的错位量应符合GB/T25373—2010的规定。 3.9.10主轴系统组装后应做动平衡试验,其运转应平稳、灵活、轻便。 3.9.11 各运动坐标轴安装的滚珠丝杠副组装后应进行运转,其反向间隙值、丝杠轴问窜动量应符合设计规定。 3.9.12机床的清洁度的检测按GB/T25374一2010规定的方法进行,其中工作台和刀架静压腔、润滑系统、液压系统的清洁度按重量法检验,其他部位按目测、手感法检验,不应有脏物。
a)工作台和刀架静压腔的杂质、污物不应超过1500mg: b)机床液压、润滑系统的清洁度:在机床运行30min后,立即在液压系统(或润滑系统)回汕口
处取样,一般不少于200mL,其杂质、污物不应超过120mg/L。
3.9.13分度蜗杆副应达到GB/T10089—1988的4级精度,齿面表面粗糙度Ra上限值蜗杆为0.32um 蜗轮为0.63um。 3.9.14按GB/T17421.1一1998规定的方法,在机床空运转试验前检验分度蜗杆副的啮合问隙,其间隙大小应符合设计规定(在工作台回转约120°的3个位置上分别各检验一次)。 3.10机床的空运转要求 3.10.1运转检验 3.10.1.1在无负荷状态下,机床刀具轴主运动机构应从最低速度起依次运转,每级速度的运转时问不得少」2min。高速运转时问不应少于1h,使主轴承达到稳定温度。 3.10.1.2对.T作台应在无负荷状态下做低、中、高速运转试验,其高速运转时问不少丁10min,运转应正常。 3.10.1.3机床各直线运动部件在全行程上分别做低、中、高进给量(或进给速度)和快速进给的空行程试验,其运动应平稳、灵活,无明显的爬行和振动现象。 3.10.2温升试验 3.10.2.1主轴轴承达到稳定温度时,在靠近刀具主轴轴承的外壳处测量轴承的温度和温升,其值不应超过表3的规定。
表3轴承温度及温升限值
单位为摄氏度
温升
温度
轴承型式
60 65
30 35
滑动轴承滚动轴承
注:机床经过一定时间运转后,其测量温度值.上升幅度不超过每小时5℃时,可认为达到了稳定温度。 3.10.2.2液压系统应在额定工作压力下连续运转,待油液达到稳定温度后,测量油液的温度和温升,其温度值不应超过60℃,温升值不应超过30℃。 4
JB/T11769.2—2014
3.10.3主运动和进给运动的检验(抽查)
检验滚刀主轴转速和进给机构进给量的实际偏差,分别不得超过标牌指示值的土5%和土10%。试验时机床各运动部件运动应平稳,可靠。 3.10.4动作试验
机床动作试验一般包括下述内容: a机床刀具主轴在中等转速下连续起动、停止各10次,动作应准确、无故障。 b)检验立柱(或工作台)的径向进给、快速移动,检验立柱(或工作台)在行程范围内的任意给
定位置的起动和停止,各检验5次,应准确可靠,无故障。 c)检验刀架的轴向进给、快速升降,检验在行程范围内任意给定位置的起动和停止,各检验5次,
应准确可靠,无敌障。 d)检验刀架的切向进给,快速进给,检验在行程范围内任意给定位置的起动和停止,各检验5次
应准确可靠,无故障。 e)检验刀架回转行程的两端和中问位置的夹紧,每个位置不得少于2次,动作应可靠。 f)检验刀架滑板在轴向移动的全行程两端和中问位置的夹紧,每个位置不得少了2次,动作应可
靠。 g)检验小立柱外支架在移动行程两端和中问位置的夹紧,每个位置不得少丁2次,动作应可靠。 h)模拟机床工作状态,操纵机床“急停”按钮(或开关),连续5次,应准确无故障。 i)用数控程序操作机床,在中等速度下分别对各坐标轴进行正、反向起动、停止(或制动)、工作
进给、快速进给及定向试验,各进行10次,动作应灵活、准确、可靠。对无级变速的主运动和进给运动,还应做系统的低,中、高及快速的变换操作试验,动作应灵活可靠。
i)按设计要求,对机床的各坐标轴联动、定位、直线插补、圆弧插补、进给坐标超程保护、坐标
位置显示、回基准点、手动数据输入、程序、序号指示和检索、程序暂停、程序消除等功能分别进行试验,其功能应可靠、动作应灵活、准确。
3.10.5空运转功率试验(抽查)
在滚刀主轴各级转速下,测量机床各级转速的空运转功率,其值不应超过设计规定。 3.10.6整机连续空运转试验
机床模拟工作状态进行连续空运转试验,循环过程中应包括各种程序功能。其连续运转时问不少了 48h。在空运转过程中,各部分工作应正常,运行应平稳。各项功能、性能应可靠,不出现故障,当出现异常或故障时应查明原因并加以排除,然后重新进行试验。各次循环程序之问的休止时问不应超过 1 mine 3.11机床的负荷要求 3.11.1机床最大承载重量的运转试验(抽查)
在机床上装上设计规定的机床最大承载,用低速及设计规定的高速运转机床,检验机床是否平稳可靠;有卸荷装置的机床应按设计要求采用不同的载荷进行试验。 3.11.2机床重切削试验
机床以重切削试验代替主传动系统的最大功率试验和扭矩试验。在试验时,通过改变切削参数,使机床主电动机达到设计功率或刀具主轴的最大设计扭矩。
机床重切削时,各部位工作应正常稳定,无异常尖叫声,试件齿面无明显振纹,各种传动及变速机
5