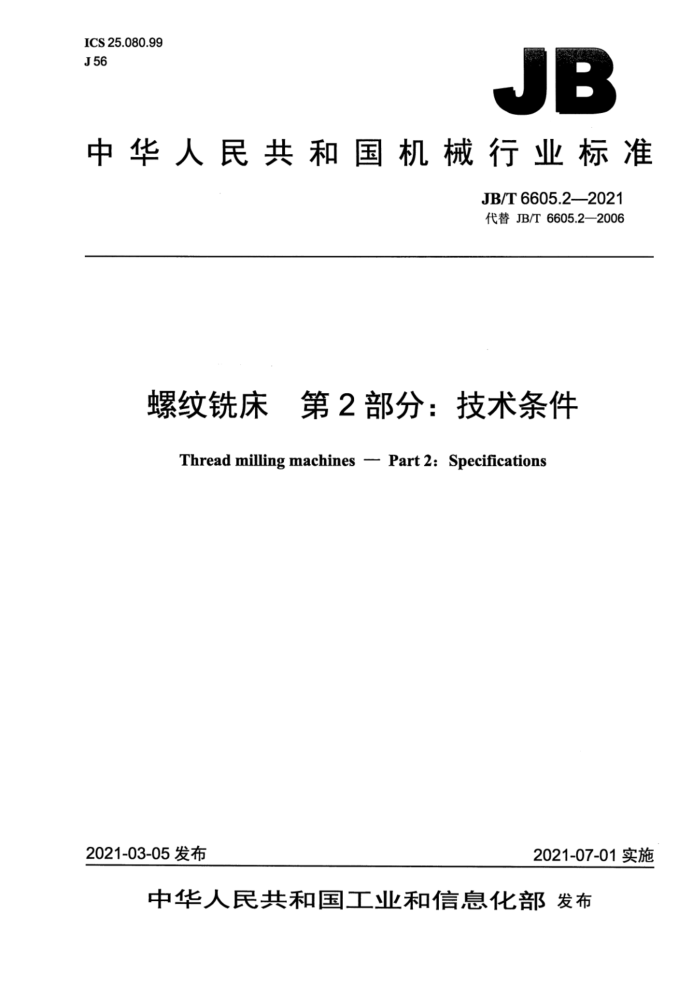
JB
中华人民共和国机械行业标准
JB/T6605.2-2021 代替JB/T6605.2—2006
螺纹铣床 第2 部分:技术条件
Thread milling machines - Part 2: Specifications
2021-03-05发布
2021-07-01实施
目 次
前言 1范围... 2规范性引用文件 3一般要求.. 4附件和工具 5安全卫生 6加工和装配质量 7空运转试验..
7.1 运转试验 7.2 温升试验 7.3 主运动和进给运动的检验(抽查) 7.4 空运转功率试验(抽查) 7.5 动作试验 7.6 整机连续空运转试验 8负荷试验 8.1 承载工件最大重量的运转试验(抽查) 8.2 主传动系统最大功率(设计功率)试验 9最小设定单位检验 9.1 概述.. 9.2 试验方法 9.3 误差计算. 9.4 公差. 9.5检验工具 10精度检验 11 包装
L
图1 最小设定单位检验
表1I 附件和工具表2机床重要部件清洁度要求表3 轴承温度及温升表4 整机连续空运转时间.
前言
JB/T6605《螺纹铣床》分为两个部分:
-第1部分:精度检验;一第2部分:技术条件。
一
本部分为JB/T6605的第2部分。 本部分按照GB/T1.1一2009给出的规则起草。 本部分代替JB/T6605.2—2006《螺纹铣床第2部分:技术条件》,与JB/T6605.2—2006相比主
要技术变化如下:
将规范性引用文件中引用的标准用现行标准代替,并增加引用了GB15760一2004《金属切削机床安全防护通用技术条件》、GB/T17421.5一2015《机床检验通则第5部分:噪声发射的确定》GB/T26220一2010《工业自动化系统与集成机床数值控制数控系统通用技术条件》、JB/T8356一2016《机床包装技术条件》等标准(见第2章);取消了对布局和外观的要求(见2006年版的第5章);增加了以下内容:对机床安全卫生的要求(见第5章)、对数控机床动作试验的要求(见7.5)、 对数控机床整机连续空运转试验的要求(见7.6)、对机床的最小设定单位检验(见第9章》 对机床的包装要求(见第11章)。
本部分由中国机械工业联合会提出。 本部分由全国金属切削机床标准化技术委员会(SAC/TC22)归口。 本部分起草单位:青海第二机床制造有限责任公司、天津第一机床总厂、秦川机床工具集团股份公
司、重庆机床(集团)有限责任公司、宜昌长机科技有限责任公司。
本部分主要起草人:颜芳、高军、全建宁、柴宝连、胡万良、喻可斌、李毅、钟瑞龄。 本部分所代替标准的历次版本发布情况为:
JB/T6605.2—1993、JB/T6605.2—2006。
螺纹铣床第2部分:技术条件
1范围
JB/T6605的本部分规定了螺纹铣床设计、制造、检验与验收的要求。 本部分适用于最大铣削直径至320mm的螺纹铣床(以下简称机床)。
2规范性引用文件
下列文件对于本文件的应用是必不可少的。凡是注日期的引用文件,仅注日期的版本适用于本文件。凡是不注日期的引用文件,其最新版本(包括所有的修改单》适用于本文件。
GB/T5226.1--2019机械电气安全机械电气设备第1部分:通用技术条件 GB/T6576—2002 机床润滑系统 GB/T9061-—2006 金属切削机床 通用技术条件 GB15760—2004 金属切削机床 安全防护通用技术条件 GB/T17421.5一2015机床检验通则第5部分:噪声发射的确定 GB/T23570—2009 金属切削机床焊接件通用技术条件 GB/T23572—2009 金属切削机床 液压系统通用技术条件 GB/T25372—2010 金属切削机床 精度分级 GB/T25373—2010 金属切削机床 装配通用技术条件 GB/T25374—2010 金属切削机床 清洁度的测量方法 GB/T25376--2010 金属切削机床机械加工件通用技术条件 GB/T26220—2010 工业自动化系统与集成机床数值控制数控系统通用技术条件 JB/T6605.1—2021 螺纹铣床第1部分:精度检验 JB/T8356--2016机床包装技术条件
3一般要求
3.1按本部分验收机床时,还应对GB/T9061—2006、GB/T23570—2009、GB/T25373—2010、GB/T 25376一2010等中未经本部分具体化的有关项目进行检验。 3.2验收机床时,按GB/T25372一2010规定的V级精度机床的要求检验。
4附件和工具
4.1 为保证机床的基本性能,应随机供应表1所列附件和工具。
表1附件和工具用途
名称
数量
备注
表1附件和工具(续)用途支承工件安装刀具调整机床
备注
名称顶尖跟刀架拉杆交换齿轮专用扳手地脚螺栓机床垫铁
数量 1套 1套 1件 1套 1套 1套 1套
包括螺母、垫圈
安装机床
注:表中所列为基型产品随机供应的附件和工具,对于基型外的机床按产品相关设计文件的规定供应。 4.2扩大机床使用性能的特殊附件,可根据用户的要求按协议供应。
5安全卫生
5.1机床的安全防护应符合GB15760—2004、GB/T5226.1—2019的规定。 5.2操作手轮、手柄离地面的高度按GB15760一2016的规定考核,手轮、手柄均按“仅调整时使用” 手轮、手柄的要求考核。 5.3在机床加工区应设置防护罩或挡板,并应具有足够的强度和刚性。同时,防护罩或挡板的设置应便于操作者观察加工区。 5.4机床上外露而易被尘屑磨损的导轨副应安装防护装置。 5.5手轮、手柄的操纵力不应超过160N,手轮、手柄的操纵力在行程范围内应均匀。 5.6液压系统应能提供稳定的正常工作的压力,当压力低于设定限值时,应发出警告信号或使机床运动停止。 5.7按GB/T17421.5-2015的规定测量机床的噪声,机床在空运转条件下噪声声压级不应超过83dB(A)。 机床运转时,不应有异常尖叫声、冲击声。
6加工和装配质量
6.1床身、床头箱体、铣头体、铣头箱体、工作台、尾架体等为重要铸件,在粗加工后应进行时效(如人工时效、振动时效等)处理。 6.2床身导轨副、径向进给导轨副等为重要导轨副,应采取耐磨措施,并符合材质及热处理的规定。 6.3焊接件应符合GB/T23570—2009的规定。 6.4工件主轴、刀具主轴、尾架套筒、轴向进给丝杠及螺母、分度蜗杆副、刀具末端传动副、高速齿轮副等主要零件,应采取耐磨措施,并符合材质及热处理的规定。 6.5下列结合面按GB/T25373—2010和GB/T25376—2010中“重要固定结合面”的要求考核:
a)螺母座与床身结合面; b)花键座与床身结合面: c径向进给液压缸与其相配件结合面。
6.6床头箱与床身结合面按GB/T25373—2010和GB/T25376—2010中“特别重要固定结合面”的要求考核。
b)径向进给导轨副。 6.8下列导轨副按GB/T253732010和GB/T25376一2010中“移置导轨”的要求考核:
a)尾架导轨副: b)铣头回转导轨副: c)铣刀主轴刀杆支承导轨副。
6.9径向进给手轮反向空程量不得超过一
8
6.10按GB/T25374一2010的规定检验机床的清洁度,床头箱、铣头、铣头箱、工作台内部、润滑系统、液压系统的清洁度按重量法抽样检验,其中床头箱、铣头、铣头箱、工作台内部的杂质、污物不应超过本部分表2的规定。液压和润滑系统的清洁度:在机床运行30min后,立即在液压或润滑系统回油口处取样,样品一般不少于200mL,其杂质、污物不应超过150mg/L。其他部位按目测手感法检验不应有污物。
表2机床重要部件清洁度要求
单位为毫克
检验部位床头箱铣头铣头箱工作台
污物质量 6 500 800 4000 1200
6.11 机床数控系统的装配应符合GB/T26220-2010的规定。 6.12机床液压系统的装配应符合GB/T23572一2009的规定。 6.13机床润滑系统的装配应符合GB/T6576一2002的规定。
7 空运转试验
7.1运转试验 7.1.1在无负荷状态下,机床主运动机构应做低、中,高速运转,低、中速运转时间不应少于10min 高速运转时间不应少于1h,使主轴轴承达到稳定温度。 7.1.2进给机构做低、中、高进给速度空运转试验,其运动应平稳、灵活,无明显的爬行和振动现象,一般不应少于30min。快速移动机构做快速移动试验,检验进给速度的正确性和变换的灵活可靠性,一般不少于10次。 7.2温升试验 7.2.1主轴轴承达到稳定温度时,在靠近刀具主轴轴承的外壳处测量轴承的温度和温升,温度和温升值不应超过表3的规定。
表3轴承温度及温升
单位为摄氏度
轴承型式滑动轴承滚动轴承
温度 60 70
温升 30 40
7.2.2液压系统在额定工作压力下连续运转至油液达到热平衡后,测量油液的温度和温升,其温度值应≤60℃,温升值应≤30℃。
注:油液达到热平衡时的温度系指温升幅度每小时小于或等于2℃时的温度。 7.3主运动和进给运动的检验(抽查) 7.3.1有级变速传动的各级主轴转速和进给量的实际偏差不应超过标示值的土5% 7.3.2无级变速传动的各级主轴转速和进给量的实际偏差不应超过标示值的土10% 7.4空运转功率试验(抽查)
机床主传动系统在各级转速下空运转至功率稳定后,测量其空运转功率(不包括主电动机空载功率),其值不应超过设计规定。其抽查比例由制造厂根据生产批量及实际检验情况确定。 7.5动作试验
机床的动作试验一般应包括以下内容: a)机床的刀具主轴在中等转速下进行正向,反向的连续起动,停止试验,各不少于10次,动作应
灵活、可靠; b)工件主轴做低、中、高速的变化试验,应准确可靠、无故障; c)以中等进给量使纵向溜板自动进给、停止及在行程范围内的任意位置起动、停止,各动作不少
于5次,在极限行程处不少于15次,动作应准确、可靠; d)机床纵向溜板快速移动,停止各5次,动作应准确、可靠; e)尾架在行程的两端和中间位置各夹紧2次:夹紧机构应可靠: f)铣头箱在行程的两端和中间位置各夹紧2次,夹紧机构应可靠 g)检验装卸工件、刀具和附件等装置,动作应灵活、可靠; h)进行控制装置的各种指示灯的功能试验,功能应可靠; i)进行机床的安全防护、保险装置的功能试验,功能应可靠: j)模拟机床工作状态,操纵机床“急停”按钮,连续5次,动作应准确无误; k)机床按设计要求起动整机自动循环,然后停止,如此循环10次,检验各动作是否灵活:平稳、
可靠。
7.6整机连续空运转试验 7.6.1机床模拟工作状态进行连续空运转试验,循环过程应包括机床的全部功能,其连续空运转无故障时间应符合表4的规定。在空运转过程中,各部分工作应正常,运行应平稳。各项功能、性能应可靠,不出现故障。各次循环之间的休止时间不应超过1min。当机床出现异常或故障时应查明原因并加以排除,然后重新进行试验。
表4整机连续空运转时间
单位为小时
连续运转时间
机床控制型式机械控制电、液控制
4 8 36 48
联动轴数<3 联动轴数≥3
数字控制
8负荷试验
8.1承载工件最大重量的运转试验(抽查)
在机床工件主轴和尾架顶尖间装夹设计规定最大重量的试件,用低速及设计规定的速度运转机床,检验机床应平稳可靠,不得出现爬行和抖动现象。 8.2主传动系统最大功率(设计功率)试验
试验的条件和切削用量应符合设计文件的规定。试验时逐步改变切削深度使机床达到最大功率(设计功率),检验机床在最大功率切削下各部分工作状态的稳定性、金属切除率及电气系统等是否可靠。
9最小设定单位检验
9.1概述
按设计要求,对直线轴坐标进行最小设定单位检验。 9.2试验方法
先以快速使直线运动轴线上的运动部件向正向(或负向)移动一定距离后停止,再向同一方向给出数个最小设定单位的指令,以此位置作为基准,然后仍向同一方向每次给出1个最小设定单位的指令,共给出20个最小设定单位的指令,使运动部件连续移动、停止,并测量其在每个指令下的停止位置,然后从上述的最终位置,继续向同一方向给出数个最小设定单位的指令,使运动部件移动并停止。从此位置再向负向(或正向)给出数个最小设定单位的指令,使运动部件大约返回到上述最终的测量位置,在这些正向和负向的数个最小设定单位指令下运动部件的停止位置均不做测量。然后从上述的最终测量位置开始,仍向负向(或正向)每次给出1个,共给出20个最小设定单位的指令,继续使运动部件连续移动、停止,大约返回到基准位置,测量其在每个指令下的停止位置,如图1所示。
至少在行程的中间及靠近两端的三个位置分别进行测量。每个直线轴均应检验。
实际移动距离
a00 O甲
数个最小设定单位指令下运动部件的停止位置不做测量
中
5
O
-
0
5
+o
测量范围一
600
LO
最小设定单位
门
009
图1最小设定单位检验
9.3误差计算 9.3.1最小设定单位误差Sa