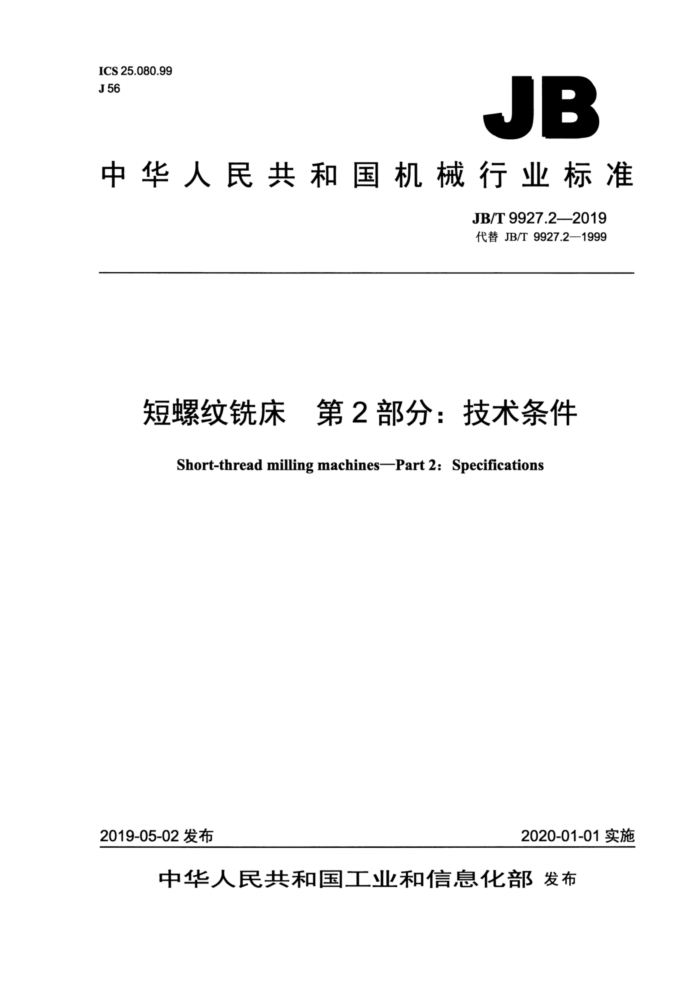
ICS 25.080.99 J 56
JB
中华人民共和国机械行业标准
JB/T 9927.2——2019 代替 JB/T 9927.2—1999
短螺纹铣床 第2部分:技术条件
Short-thread milling machinesPart 2: Specifications
2020-01-01实施
2019-05-02 发布
中华人民共和国工业和信息化部发布
JB/T 9927.2—2019
目 次
前言.. 1范围 2规范性引用文件 3一般要求.. 4附件和工具. 5安全卫生 6加工和装配质量空运转试验.
1
7
7.1运转试验, 7.2 温升试验 7.3 主运动和进给运动的检验(抽查) 7.4动作试验. 7.5 空运转功率试验(抽查) 7.6 整机连续空运转试验 8负荷试验 9精度检验 10 包装
表1附件和工具. 表2轴承温度及温升限值表3铣头径向进给重复定位精度的检验
JB/T 9927.2—2019
前言
JB/T9927《短螺纹铣床》分为两个部分:
第1部分:精度检验;一第2部分:技术条件。 本部分为JB/T9927《短螺纹铣床》的第2部分。 本部分按照GB/T1.1-2009给出的规则起草。 本部分代替JB/T9927.2—1999《短螺纹铣床技术条件》,与JB/T9927.2—1999相比主要技术变
化如下:
本部分名称修改为“短螺纹铣床第2部分:技术条件”;修改了“前言”;将规范性引用文件中引用的标准用现行标准代替,并增加引用了GB5226.1一2008《机械电气安全机械电气设备第1部分:通用技术条件》、GB15760-2004《金属切削机床安全防护通用技术条件》、GB/T17421.5一2015《机床检验通则第5部分:噪声发射的确定》、GB/T 23570—2009《金属切削机床焊接件通用技术条件》、GB/T23571—2009《金属切削机床随机技术文件的编制》、GB/T25372一2010《金属切削机床精度分级》、JB/T3997—2011《金属切削机床灰铸铁件技术条件》、JB/T8356一2016《机床包装技术条件》等标准(见第2 章,1999年版的第2章);增加了机床精度等级的验收要求(见3.2); -增加了“安全卫生”一章(见第5章); -增加了焊接件、灰铸铁件的加工要求(见6.1、6.2);增加了“运转试验”和“主运动和进给运动的检验”(见7.1、7.3;修改了机床动作试验的内容(见7.4,1999年版的6.3); -增加了机床的包装要求(见第10章)。
本部分由中国机械工业联合会提出。 本部分由全国金属切削机床标准化技术委员会(SAC/TC22)归口。 本部分起草单位:青海第二机床制造有限责任公司、重庆机床(集团)有限责任公司。 本部分主要起草人:颜芳、陶文、高军、喻可斌、李毅。 本部分所代替标准的历次版本发布情况为:
ZBn J54 012—1988; -JB/T 9927.2—1999。
II
JB/T 9927.2—2019
短螺纹铣床第2部分: 技术条件
1范围
JB/T9927的本部分规定了短螺纹铣床设计、制造、检验和验收的要求。 本部分适用于最大铣削直径至200mm、最大铣削长度至80mm、最大工件长度至2500mm、采用
梳洗法加工普通螺纹的螺纹铣床(以下简称机床)。
2 规范性引用文件
下列文件对于本文件的应用是必不可少的。凡是注日期的引用文件,仅注日期的版本适用于本文件。 凡是不注日期的引用文件,其最新版本(包括所有的修改单)适用于本文件。
GB5226.1一2008机械电气安全机械电气设备第1部分:通用技术条件 GB/T9061-2006金属切削机床 通用技术条件 GB 15760—2004 金属切削机床安全防护通用技术条件 GB/T 17421.5-2015 机床检验通则第5部分:噪声发射的确定 GB/T23570—2009 金属切削机床焊接件通用技术条件 GB/T25372—2010 金属切削机床 精度分级 GB/T 25373—2010 金属切削机床 装配通用技术条件 GB/T 25374—2010 金属切削机床 清洁度的测量方法 GB/T 25376—2010 金属切削机床 机械加工件通用技术条件 JB/T 3997—2011 金属切削机床灰铸铁件技术条件 JB/T8356—2016 机床包装技术条件 JB/T9927.1一2019短螺纹铣床第1部分:精度检验
3一般要求
3.1按本部分验收机床时,还应对GB5226.1—2008、GB/T9061—2006、GB/T23570-2009、GB/T 25373-2010、GB/T25376一2010中未经本部分具体化的有关项目进行检验 3.2验收机床时,按GB/T25372一2010规定的V级精度机床的要求检验。
4附件和工具
4.1机床应随机供应表1所列附件和工具。
表1附件和工具
数量 1套 1 件
名称工具心轴三爪自定心卡盘
1
JB/T 9927.2—2019
表1附件和工具 (续)
数量 1 件 1套 1套 1套
名称卡盘接盘顶尖拔盘专用扳手
注:表中所列为基型产品随机供应的附件和工具。 4.2扩大机床使用性能的特殊附件,可根据用户的要求按协议供应。
5安全卫生
5.1机床的安全防护应符合GB15760—2004、GB5226.1—2008的规定。 5.2在机床加工区应设置防护罩或挡板,并应具有足够的强度和刚性。防护装置的设置应便于工件的置换以及操作者的观察。 5.3机床上外露而易被尘屑磨损的导轨副应安装防护装置。 5.4手轮、手柄的操纵力不应超过160N,手轮、手柄的操纵力在行程范围内应均匀。 5.5液压系统应能提供稳定的正常工作的压力,当压力低于设定限值时,应发出警告信号或使机床运动停止。 5.6机床的噪声声压级在空运转条件下检验,测量方法应符合GB/T17421.5一2015的规定,其噪声声压级不应超过83dB(A)。机床运转时,不应有异常尖叫声、冲击声。
6加工和装配质量
6.1机械加工件、焊接件应符合图样、工艺文件及GB/T25370—2009、GB/T23576—2010的规定。机床的装配应符合GB/T25373-2010的规定。 6.2机床灰铸铁件应符合JB/T3997一2011的规定。 6.3床身、床头箱体、铣头箱体、工作台、尾架体、料筒等为重要铸件,在粗加工后应进行时效(如人工时效、振动时效等)处理。 6.4床身导轨为重要导轨副,应采取耐磨措施,并符合材质及热处理的有关标准规定。 6.5工件主轴、刀具主轴等主要零件应采取与寿命相适应的耐磨措施。 6.6下列结合面按GB/T25373一2010和GB/T25376一2010中“重要固定结合面”的要求检验:
a)料筒支架与床身结合面; b)传动杠支架与床身结合面; c)纵向进给液压缸与其固定装置结合面。
6.7床头箱与床身结合面按GB/T25373—2010和GB/T25376—2010中规定的特别重要固定结合面” 的要求检验。 6.8下列配合导轨按GB/T25373一2010和GB/T25376一2010中“静压、滑动、滚动导轨”的要求检验:
a)床身纵向导轨与工作台相配的表面; b)圆周进给液压缸体与滑枕相配的表面。
6.9下列配合导轨按GB/T25373—2010和GB/T25376—2010中“移置导轨”的要求检验: 2
JB/T 9927.2—2019
a)床身纵向导轨与尾架相配的表面; b)径向进给用导轨与其相配件的表面; c)刀具支架与主轴滑动轴承座相配的表面。
6.10径向进给手轮反向空程量不得超过-
1
4
6.11机床应按GB/T25374一2010规定的方法进行清洁度检验,其中床头箱、铣头部件内部清洁度按质量法抽样检验,其杂质、污物含量:床头箱不应超过6500mg,铣头不应超过2000mg。其他部位按目测、手感法检验,不应有污物。
7空运转试验
7.1运转试验 7.1.1在无负荷状态下,机床主运动机构应做低、中、高速运转,每级速度的运转时间不应少于2min,最高速运转时间不应少于1h,使主轴轴承达到稳定温度。 7.1.2进给机构做低、中、高进给速度空行程试验,其运动应平稳、灵活,无明显的爬行和振动现象,试验时间一般不应少于30min。快速移动机构做快速移动试验,检验进给速度的正确性和变换的灵活可靠性,试验次数一般不少于10次。 7.2温升试验
主轴轴承达到稳定温度时,检查其温度和温升,温度和温升值不应超过表2的规定。
表2轴承温度及温升限值
单位为摄氏度
轴承型式滑动轴承滚动轴承
温度 60 70
温升 30 40
注:机床经过一定时间运转后,当其齿轮温度值上升幅度不超过5℃/h时,一般可认为已达到稳定温度。
7.3主运动和进给运动的检验(抽查)
7.3.1有级变速传动的各级主轴转速和进给量的实际偏差不应超过标示值的土5%。 7.3.2无级变速传动的各级主轴转速和进给量的实际偏差不应超过标示值的土10%。 7.4动作试验
机床的动作试验一般应包括以下内容: a)机床的刀具主轴在中等转速下进行正向、反向的连续起动、停止试验,各不少于10次,动作应
灵活、可靠; b)检验进给运动的起动、停止和工作循环动作的灵活性; c)反复变换主运动和进给运动的速度,检验变速机构动作是否平稳、可靠和指示的准确性及夹紧
机构的可靠性; d)检验装卸工件、刀具和附件等装置的灵活、可靠性; e)模拟机床工作状态,操作机床“急停”按钮(或开关),连续10次,其动作应可靠。
3
JB/T 9927.2—2019
7.5空运转功率试验(抽查)
机床主传动系统在各级速度下空运转至功率稳定后,测量其空运转功率(不包括主电动机空载功率),
其值不应超过设计规定。其抽查比例由制造厂根据生产批量及实际检验情况确定。
7.6整机连续空运转试验 7.6.1机床模拟工作状态进行连续空运转试验,循环过程中应包括机床的全部功能,其连续空运转无故障时间不少于8h。在空运转过程中,各部分工作应正常,运行应平稳。各项功能、性能应可靠,不出现故障。各次循环之间的休止时间不应超过1min。当机床出现异常或故障时应查明原因并加以排除,然后重新进行试验。 7.6.2在整机连续空运转过程中,机床的液压、润滑、冷却系统和其他部位均不应渗漏;转动部位的油不应甩出;润滑油路应畅通,冷却液应充分;切削液不应混入液压和润滑系统,机床各部分工作应正常。
8负荷试验
本系列机床采用切削方法进行机床主传动系统最大功率试验。其切削条件及规范均按设计文件规定,逐步改变切削深度使机床达到最大功率(设计功率),检验机床在最大功率切削下各部分工作状态的稳定性、金属切除率及电气系统等是否可靠。
9精度检验
9.1机床的几何精度及工作精度检验应符合JB/T9927.1一2019的规定。 9.2以下四项几何精度应在机床以中速运转达到稳定温度时检验:
a)工件主轴轴线和尾架套筒锥孔轴线的等高度; b)刀具主轴锥孔轴线的径向圆跳动; c)刀具主轴锥孔轴线对工作台移动的平行度; d)刀具主轴锥孔轴线与刀具托架轴承孔轴线的同轴度。
9.3工作精度检验时,精铣螺纹表面粗糙度Ra最大允许值为3.2μm。 9.4检验系统径向进给的重复定位精度,结果应符合表3的规定。
表3铣头径向进给重复定位精度的检验
单位为毫米允差
检验项目
检验工具
检验方法
在机床的不动部件上固定指示器,使其测头触及铣头的某一固定点。铣头径向进给至少7次重复定位误差以指示器读数的最大差值计
铣头径向进给的重复定位精度
指示器
0.015
10包装
10.1 机床在包装前,应按相关规定进行防锈处理。 10.2机床的包装应符合JB/T8356一2016的规定。
4
JB/T 9927.2-2019
3出厂的机床包装箱内,应提供一套随机技术文件。机床随机技术文件应至少包括使用说明书、合
10.3
格证明书和装箱单,必要时还应提供机床的维修配件目录等技术文件。机床随机技术文件的编制方法宜符合GB/T23571—2009的规定。
5