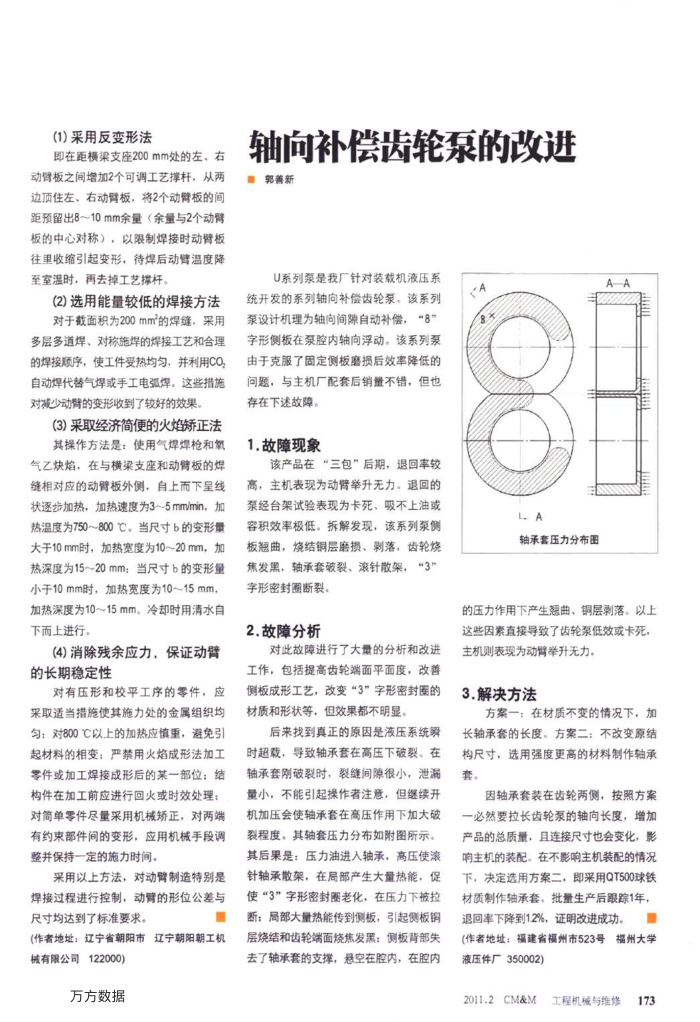
(1)采用反变形法
即在距横渠支座200mm处的左、右动臂板之间增加2个可调工艺撑杆,从两边顶住左、右动胃板,将2个动臂板的间距预留出8~10mm余量(余量与2个动臂板的中心对称),以限制焊接时动臂板往里收缩引起变形,待焊后动臂温度降至室温时,再去掉工艺撑杆。
(2)选用能量较低的焊接方法对于截面积为200mm的焊缝,采用
多层多道焊、对称施焊的焊接工艺和合理的焊接顺序,使工件受热均匀,并利用CO, 自动焊代替气焊或手工电弧焊。这些措施对减少动臂的变形收到了较好的效果。
(3)采取经济简便的火焰矫正法其操作方法是:使用气焊焊枪和氧
气乙炔焰,在与横梁支座和动臂板的焊缝相对应的动臂板外侧,自上而下呈线状逐步加热,加热速度为3~5mm/min,加热温度为750~800℃。当尺寸b的变形量大于10mm时,加热宽度为10~20mm,加热深度为15~20mm;当尺寸b的变形量小于10mm时,加热宽度为10~15mm,加热深度为10~15mm。冷却时用清水自下而上进行。
(4)消除残余应力,保证动臂的长期稳定性
对有压形和校平工序的零件,应采取适当措施使其施力处的金属组织均匀:对800℃以上的加热应慎重,避免引起材料的相变:严禁用火焰成形法加工零件或加工焊接成形后的某一部位:结构件在加工前应进行回火或时效处理:对简单零件尽量采用机械矫正,对两端有约束部件间的变形,应用机械手段调整并保持一定的施力时间。
采用以上方法,对动臂制造特别是焊接过程进行控制,动臂的形位公差与
尺寸均达到了标准要求。(作者地址:辽宁省朝阳市
辽宁朝阳朝工机
械有限公司122000)
万方数据
轴向补偿齿轮泵的改进 ■郭善新
U系列泵是我厂针对装载机液压系统开发的系列轴向补偿齿轮泵。该系列泵设计机理为轴向间隙自动补偿,“8 字形侧板在泵腔内轴向浮动,该系列泵由于克服了固定侧板磨损后效率降低的问题,与主机厂配套后销量不错,但也
存在下述故障, 1.故障现象
该产品在“三包”后期,退回率较高,主机表现为动臂举升无力。退回的泵经台架试验表现为卡死、吸不上油或容积效率极低。拆解发现,该系列泵侧板题曲,烧结铜层磨损、剥落,齿轮烧焦发黑,轴承套破裂、滚针散架,“3”
字形密封圈断裂。 2.故障分析
对此故障进行了大量的分析和改进工作,包括提高齿轮端面平面度,改善侧板成形工艺,改变“3”字形密封医的材质和形状等,但效果都不明显。
后来找到真正的原因是液压系统职时超载,导致轴承套在高压下破裂、在轴承套刚破裂时,裂缝间隙很小,泄满量小,不能引起操作者注意,但继续开机加压会使轴承套在高压作用下加大破裂程度。其轴套压力分布如附图所示。其后果是:压力油进入轴承,高压使滚针轴承散架,在局部产生大量热能,促使“3”字形密封老化,在压力下被拉断:局部大量热能传到侧板,引起侧板铜层烧结和齿轮端面烧焦发黑:侧板背部失去了轴承套的支撑,悬空在腔内,在腔内
rA
LA
轴承套压力分布图
AA
的压力作用下产生翘曲、铜层剥落。以上这些因素直接导致了齿轮泵低效或卡死,
主机则表现为动臂举升无力, 3.解决方法
方案一:在材质不变的情况下,加长轴承套的长度。方案二:不改变原结构尺寸,选用强度更高的材料制作轴承套。
因轴承套装在齿轮两侧,按照方案
一必然要拉长齿轮泵的轴向长度,增加产品的总质量,且连接尺寸也会变化,影响主机的装配。在不影响主机装配的情况下,决定选用方案二,即采用QT500球铁材质制作轴承套。批量生产后跟踪1年,退回率下降到12%,证明改进成功。
(作者地址:福建省福州市523号福州大学液压件厂350002)
2011.2CM&M
工程机械与维修
173