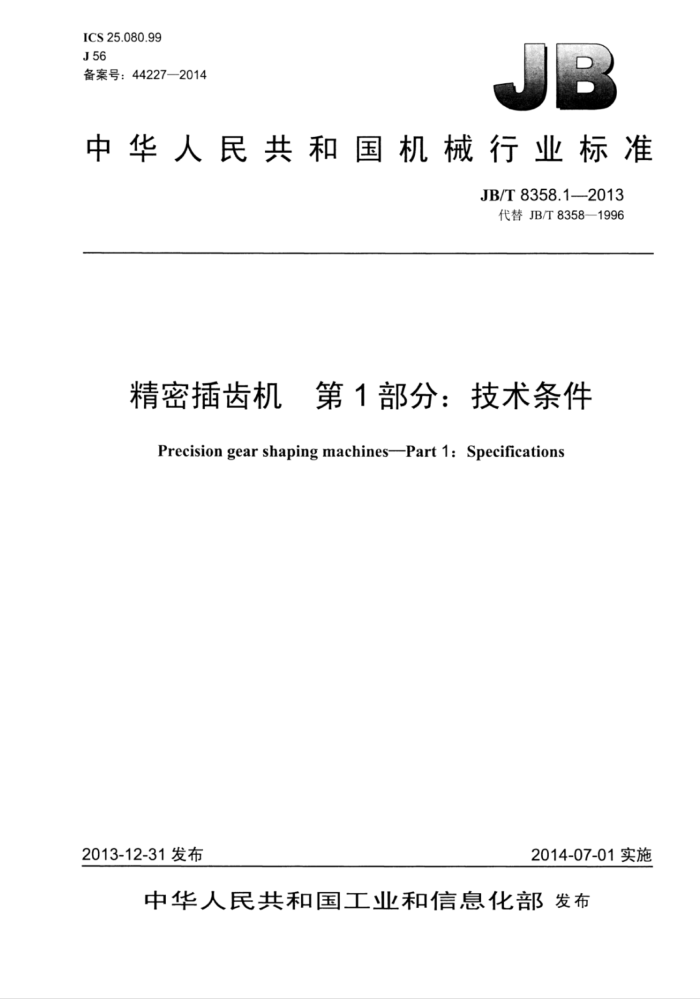
ICS 25.080.99 J56 备案号:44227—2014
中华人民共和国机械行业标准
JB/T8358.1—2013 代替JB/T8358—1996
精密插齿机 ,第1部分:技术条件 Precision gear shaping machines-Part 1: Specifications
2014-07-01实施
2013-12-31发布
中华人民共和国工业和信息化部发布
JB/T8358.1-2013
目 次
前言范围..
I
1 2 3
规范性引用文件技术要求.. 3.1 一般要求. 3.2 附件和工具 3.3 布局和外观. 3.4 电气系统. 3.5 数控系统. 3.6 液压、润滑和冷却系统. 3.7 安全卫生 3.8 加工和装配质量检验与验收
E
4
4.1 概述 4.2 一般要求, 4.3 外观检验, 4.4 附件和工具的检验。 4.5 参数检验(抽查) 4.6 机床的空运转试验. 4.7 机床的负荷试验, 4.8 机床的精度检验. 4.9 其他 5包装表1附件和工具表2错位量及贴合缝隙值表3脏物质量限值表4轴承温度及温升限值.
..4
5
D .6
JB/T8358.1—2013
前言
JB/T8358《精密插齿机》分为两个部分:
第1部分:技术条件:第2部分:精度检验。
本部分为JB/T8358的第1部分。 本部分按照GB/T1.1一2009给出的规则起草。 本部分代替JB/T8358一1996《精密插齿机技术条件》,与JB/T8358一1996相比主要技术变化如下:
修改了标准的适用范围,由“适用于最大工件直径200mm~3150mm的精密插齿机修改为 “适用于最大工件直径125mm~3200mm的精密插齿机(见第1章,1996年版的第1章);一可用了最新版的相关标准(见第2章,1996年版的第2章);增加了“布局和外观”(见3.3); -增加了“电气系统”(见3.4);增加了“数控系统”(见3.5》;增加了“液压、润滑和冷却系统”(见3.6); -删除了“安全卫生”中的具体条款,这些条款在本部分I用的强制性国家标准GB15760中已有详细规定(见3.7,1996年版的第5章): -增加了“包装”(见第5章);删除了1996年版的附加说明。
-
本部分由中国机械工业联合会提出。 本部分由全国金属切削机床标准化技术委员会(SAC/TC22)归口。 本部分起草单位:南京二机齿轮机床有限公司、天津第一机床总厂、宜昌长机科技有限责任公司、
重庆机床(集团)有限责任公司。
本部分主要起草人:李光华,刘艳、刘德全、钟瑞龄、喻可斌。 本部分所代替标准的历次版本发布情况为:
ZBJ56006-1988; JB/T8358—1996。
II
JB/T8358.1-2013
精密插齿机第1部分:技术条件
1范围
JB/T8358的本部分规定了精密插齿机设计、制造和验收的要求。 本部分适用于最大工件直径125mm~3200mm的精密插齿机,也适用于数控精密插齿机(以下简
称“机床”)。
2规范性引用文件
下列文件对于本文件的应用是必不可少的。凡是注日期的引用文件,仅注日期的版本适用于本文件。 凡是不注日期的引用文件,其最新版本(包括所有的修改单)适用于本文件。
GB5226.1一2008机械电气安全机械电气设备第1部分:通用技术条件 GB/T6576—2002 机床润滑系统 GB/T90612006 金属切削机床 通用技术条件 GB15760—2004 金属切削机床安全防护通用技术条件 GB/T16769—2008 金属切削机床噪声声压级测量方法 GB/T23570—2009 金属切削机床焊接件通用技术条件 GB/T23572-2009 金属切削机床液压系统通用技术条件 GB/T25372—2010 金属切削机床 精度分级 GB/T25373—2010 金属切削机床 装配通用技术条件 GB/T25374—2010 金属切削机床 清洁度的测量方法 GB/T25376—2010 金属切削机床机械加工件通用技术条件 GB/T26220—2010 工业自动化系统与集成机床数值控制数控系统通用技术条件 JB/T6342.12006 数控插齿机第1部分:精度检验 JB/T8356.1—1996 机床包装技术条件 JB/T8356.2—1996 机床包装箱 JB/T8358.2—2006 精密插齿机第2部分:精度
3技术要求
3.1一般要求
本部分是对GB/T9061—2006、GB/T23570-2009、GB/T25373—2010、GB/T25376—2010等标准的具体化和补充,机床的设计与制造除应符合本部分的规定外,还应符合上述标准中未经本部分具体化的其他技术要求。 3.2附件和工具 3.2.1机床应随行供应表1所列的附件和工具。 3.2.2扩大机床性能的特殊附件,可根据用户要求按协议供应。
-
JB/T8358.12013
表1附件和工具
名称
用 途安装机床用调整机床用
数 量 1套 1套 1套 1套 1套
调整垫铁、地脚螺栓或减振垫铁
专用扳于交换齿轮螺母』垫圈
安装刀具用安装工件用
拉杆(包括螺栓和螺母)
3.3 布局和外观 3.3.1 机床布局应合理、造型美观、色泽和谐,符合人类工效学原则并便于调整及维修。 3.3.2 机床外观表面不应有未规定的凸起、凹陷、粗糙不平和其他损伤。 3.3.3 机床的防护罩表面应平整、匀称、不应翘山、凹陷。 3.3.4 机床外露零件表面不应有硫碰、锈蚀,螺钉、铆钉、销子端部不应有扭伤、锤伤等缺陷。 3.3.5 电镀件、发蓝件、发黑件色调应一致,防护层不应有褪色、脱落现象。 3.3.6 机床可拆卸的装配结合面的接缝处,在涂漆以后,应切开,切开时不应扯破边缘。 3.3.7 机床涂漆层应平整,光泽应均匀一致,涂漆表面不应有起泡、流挂、起皮及脱落现象。 3.3.8机床的各种信息标志及标牌应固定在机床相应的明显位置,且清晰耐久,不歪斜。 3.3.9机床电气、液压、润滑及冷却等管道的外露部分,应布置紧凑、排列整齐,必要时应用管夹固定,软管不应扭山、折叠及断裂。 3.3.10装入沉孔的螺钉不应突出于零件表面,其头部与沉孔之问不应有明显的偏心。固定销一般应略突出于零件表面。螺栓尾端应略突出于螺母端面。外露轴端应突出于包容件的端面,突出值约为倒棱值。 内孔表面与壳体凸缘问的壁厚应均匀对称,其凸缘壁厚之差不应大于实际最大壁厚的25%。 3.3.11机床零部件外露结合面的边缘整齐匀称,不应有明显的错位。门、盖与机床的结合面应贴合。 错位量及贴合缝隙值不应大于表2的规定。
表2错位量及贴合缝隙值
单位为毫米 >3 150 4
结合面边缘及门、盖边长尺寸
>500~1250
≤500 1.5 1 1 1
>1250~3150
错位量错位不勾称量贴合缝隙值缝隙不均匀值
2 1 1.5 1.5
3 1.5 2 2
注1:当结合面边缘及门、盖尺寸的长、宽不一致时,可按长边尺寸确定允许值。 注2:错位不匀称量指外露集合面边缘同一边或对应边最大错位量与最小错位量之差值。 注3:缝隙不均匀值指门、盖间对开缝或其相对机床本体间最大缝隙值与最小缝隙值之差值。
3.4电气系统
机床的电气系统应符合GB5226.1一2008的规定。 3.5数控系统
机床的数控系统应符合GB/T26220—2010的有关规定。
2
JB/T8358.1—2013
3.6液压、润滑和冷却系统 3.6.1机床的液压系统应符合GB/T235722009的规定。 3.6.2机床的润滑系统应符合GB/T6576—2002的规定。 3.6.3机床的冷却系统应保证冷却充分、可靠。 3.6.4机床的液压、润滑、冷却系统及其他部位均不应漏(渗)汕、漏(渗)水。切削液不应混入液压系统和润滑系统。 3.7安全卫生
机床上有可能对人身体健康或对设备易造成损伤的部位,应采取安全措施,机床的安全防护应符合 GB15760——2004和GB5226.1--2008的规定。 3.8加工和装配质量 3.8.1机械加工件、焊接件应符合图样、工艺文件及GB/T23570—2009、GB/T25376一2010的规定。 机床装配应符合GB/T25373一2010的规定。 3.8.2刀架体、工作台壳体、立柱、立柱滑板、刀架滑座、工作台主轴、床身、中床身、工作台分度蜗轮、刀架分度蜗轮等为重要零件,应在粗加工后进行时效处理(如人工时效、振动时效等)。 3.8.3刀具主轴往复运动导轨副为重要导轨副,刀具主轴往复运动导轨副和主轴轴承应采取耐磨措施。 3.8.4刀架分度蜗杆副、工作台分度蜗杆副、让刀凸轮、径向进给凸轮、刀具主轴、刀具套等主要零件应采取与机床寿命相应的耐磨措施。 3.8.5驱动箱、传动箱等箱体与立柱或床身的结合面按GB/T25373—2010和GB/T25376—2010中重要固定结合面的要求考核。 3.8.6下列结合面按GB/T25373—2010和GB/T25376—2010中特别重要固定结合面的要求考核。
a)对于工作台作径向进给的机床,床身与中床身(或立柱)的结合面: b)对于立柱作径向进给的机床,立柱与中床身、工作台体与床身的结合面。
3.8.7立柱导轨副、工作台圆导轨副、床身导轨副、刀架让刀运动导轨副、刀具主轴往复运动导轨副等按GB/T25373—2010和GB/T25376—2010中滑动导轨的要求考核。其余按移置导轨的要求考核。 3.8.8带刻度装置的径向进给手轮或手柄,其反向空程量不应超过1/4r。 3.8.9机床清洁度按GB/T25374一2010规定的方法检验,其中工作台、刀架内部、润滑系统、液压系统的清洁度按重量法检验,其他部位按目测、手感法检验,不应有脏物。
a)采用重量法检测时,刀架、工作台内部的清洁度按清洗油液中所含脏物重量来确定,其清洁度
值不超过表3的规定。
表3脏物质量限值
最大工件直径mm
检测部位
>125~320
>320~500 脏物质量mg
<125
>1 250
>500~1250
刀架工作台 b)机床液压、润滑系统的清洁度:在机床开车运行30min后,立即在液压系统(或润滑系统)的
3 200 2400
4800 4 000
13 600 11 200
7200 5 600
9 600 8000
回油处取样,一般不应少于200mL,其杂质污物不应超过120mg/L。
3
JB/T8358.1—2013
4检验与验收
4.1概述 4.1.1每台机床应在制造厂经检验合格后出厂。特殊情况下经用户同意可在机床使用处进行检验。当在机床使用处验收机床时,其验收的项目由用户与制造厂商定。 4.1.2机床检验分为型式试验和出厂检验。 4.1.2.1属于下列形式之一时,应进行型式试验
a)新产品试制、定型鉴定: b)机床结构、性能较基型有重大改动。
4.1.2.2机床出厂检验一般包括以下内容:
a)外观检验: b)附件和工具检验; c)参数检验(抽查): d)机床的空运转试验(含抽查项): e)机床的负荷试验(含抽查项) f)机床的精度检验; g)其他。
4.2一般要求 4.2.1本部分是对GB/T9061—2006、GB/T23570—2009、GB/T25373—2010、GB/T25376—2010等标准的具体化和补充。按本部分检验与验收机床时,应同时对上述标准中未经本部分具体化的其余有关验收项目进行检验。 4.2.2验收机床时,按GB/T25372一2010规定的IV级精度机床的要求检验 4.3外观检验
按3.3评定及检验机床的布局和外观质量。 4.4附件和工具的检验
按3.2检验随行供应的附件和工具是否符合规定。 4.5参数检验(抽查)
按设计文件检验机床的参数以及机床与工夹量具、附件等连接部位的型式和尺寸。 4.6机床的空运转试验 4.6.1运转检验 4.6.1.1在无负荷状态下,机床刀具轴主运动机构应从最低速度起依次运转,每级速度的运转时问不得少于1h。用交换齿轮、带传动变速和无级变速的机床可作低、中、高速运转。高速运转时间不应少于2h,使主轴轴承达到稳定温度。 4.6.1.2进给机构按其各项功能依次做变换进给量的空运转检查,批量产品检验时可仅做低中、高进给量检查。其高速运转时间不少于10min,运转应正常。 4.6.2温升试验 4.6.2.1主轴轴承达到稳定温度时,在靠近刀具主轴轴承的外壳处测量轴承的温度和温升,其值不应 4
JB/T8358.1—2013
超过表4的规定。
表4轴承温度及温升限值
单位为摄氏度
轴承型式滑动轴承滚动轴承
温度
温 升 25 35
55 65
注:机床经过一定时间运转后,其测量温度值上升幅度不超过每小时5℃时,可认为达到了稳定温度。 4.6.2.2液压系统应在额定工作压力下连续运转,待油液达到稳定温度后,测量油液的温度和温升,其温度值不应朝超过60℃,温升不应超过30℃。 4.6.3主运动和进给运动的检验(抽查)
检验主轴转速和进给机构进给量的实际偏差,不得超过标牌指示值的土5%。 4.6.4动作试验
机床动作试验一般包括下述内容: a)在中等速度条件下,试验刀具主轴作往复运动起动、停止各10次,检查主运动和让刀运动的动
作灵活和可靠。 b)在适当圆周进给速度条件下,试验刀具主轴圆周进给运动的起动、停止各10次,检查圆周进给
运动和分齿运动的可靠。 c)试验立柱(或工作台)径向运动10次,检查快速趋近、快速返回,以及径向进给运动的可靠;
试验径向微量进给运动10次,应平稳、灵活,无阻滞现象。 d)有上停机构的机床撤动上停按钮再作自动循环10次,检验上停机构的可靠性和所停位置的准确
性。 e)检验自动排屑装置运动的可靠。 f)检验主运动等自动变速的可靠。
4.6.5安全防护装置的检验
按3.7的要求检验安全防护装置是否齐备、可靠。 4.6.6噪声检验
按GB/T16769一2008的规定测量机床的空运转噪声,其噪声声压级不应超过83dB(A)。 4.6.7空运转功率试验(抽查)
机床主传动系统在各级速度下空运转至功率稳定后,测量主运动系统的空运转功率(不包括主电机空载功率),其值不应超过设计规定。 4.6.8电气系统的检验
机床电气系统应符合GB5226.1一2008等有关标准的规定,其功能应可靠、稳定,满足机床使用性能的要求。 4.6.9数控系统的检验
机床数控系统应符合GB/T26220一2010的规定,其与主机连接后应可靠。稳定。
5