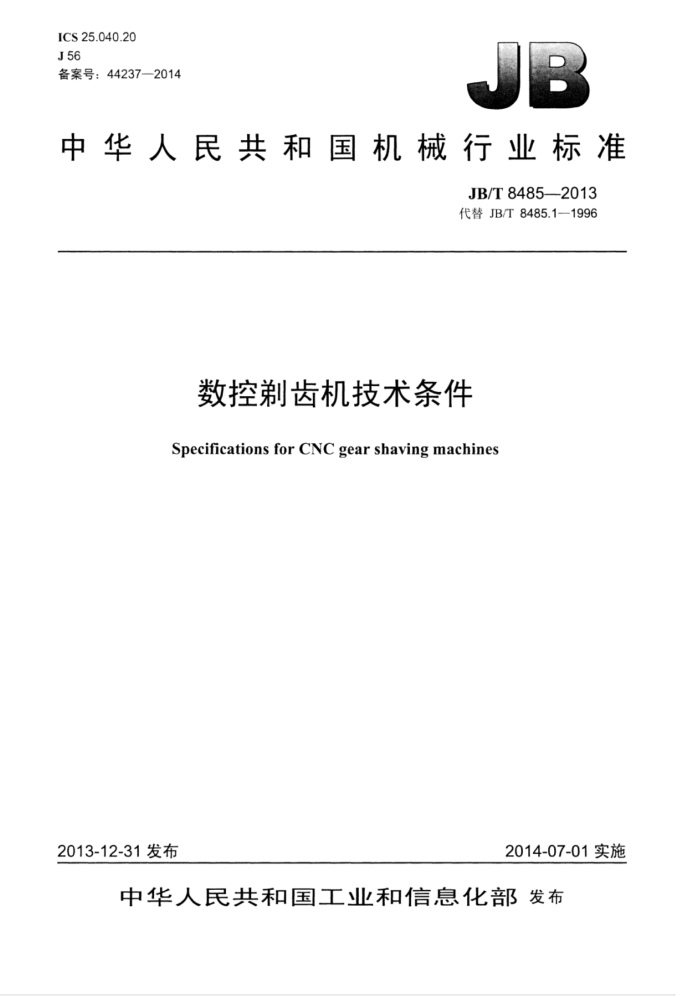
ICS25.040.20 J56 备案号:44237—2014
中华人民共和国机械行业标准
JB/T8485—2013 代替JB/T8485.1—1996
数控剃齿机技术条件
Specifications for CNC gear shaving machines
2014-07-01实施
2013-12-31发布
中华人民共和国工业和信息化部发布
JB/T8485—2013
目 次
前言 1范围.. 2规范性引用文件 3技术要求 3.1 一般要求.. 3.2 附件和工具 3.3 布局和外观. 3.4 电气系统. 3.5 数控系统. 3.6 液压、润滑和冷却系统. 3.7 安全卫生 3.8 加工和装配质量 4检验与验收 4.1 概述. 4.2 一般要求 4.3 外观检验.. 4.4 附件和工具的检验 4.5 参数检验(抽查) 4.6 机床的空运转试验 4.7 机床的负荷试验. 4.8 机床的最小设定单位检验 4.9 机床的精度检验 4.10 其他 5包装. 表1附件和工具。 表2错位量及贴合缝隙值表3脏物质量限值表4轴承温度及温升限值
I
L
一
一
-
+
JB/T8485—2013
前言
本标准按照GB/T1.1一2009给出的规则起草。 本标准代替JB/T8485.1-1996《数控剃齿机 技术条件》,与JB/T8485.1—1996相比主要技术变化
如下:
一引用了最新版的相关标准(见第2章,1996年版的第2章):一增加了“布局和外观”(见3.3);增加了“电气系统”(见3.4);增加了“数控系统”(见3.5):
-增加了“液压、润滑和冷却系统”(见3.6);一删除了“安全卫生”中的具体条款,这些条款在本标准引用的强制性国家标准GB15760中已
有详细规定(见3.7,1996年版的第5章)一一修改了“整机连续空运转时问”,由“24h”修改为“36h”(见4.6.11,1996年版的7.6);
增加了“包装”(见第5章)。 本标准由中国机械工业联合会提出。 本标准由全国金属切削机床标准化技术委员会(SAC/TC22)归口。 本标准起草单位:重庆机床(集团)有限责任公司、南京二机齿轮机床有限责任公司。 本标准主要起草人:李毅、喻可斌、张大鹏、李光华、蒋小彦。 本标准所代替标准的历次版本发布情况为:
JB/T8485.1—1996。
II
JB/T8485—2013
数控剃齿机技术条件
1范围
本标准规定了数控剃齿机设计、制造、检验与验收的要求。 本标准适用于最大工件直径125mm~500mm的数控剃齿机(以下简称机床")。
2规范性引用文件
下列文件对于本文件的应用是必不可少的。凡是注日期的引用文件,仅注日期的版本适用于本文件。 凡是不注日期的引用文件,其最新版本(包括所有的修改单)适用于本文件。
GB5226.1—2008 3机械电气安全机械电气设备第1部分:通用技术条件 GB/T6576-2002机床润滑系统 GB/T9061-2006 金属切削机床通用技术条件 GB/T10095.1一2008圆柱齿轮精度制第1部分:轮齿同侧齿面偏差的定义和允许值 GB15760一2004金属切削机床安全防护通用技术条件 GB/T167692008 金属切削机床噪声声压级测量方法 GB/T21946—2008 数控剃齿机精度检验 GB/T23570-2009 金属切削机床焊接件通用技术条件 GB/T23572—2009 金属切削机床液压系统通用技术条件 GB/T25372—2010 金属切削机床 精度分级 GB/T25373—2010 金属切削机床 装配通用技术条件 GB/T25374—2010 金属切削机床清洁度的测量方法 GB/T25376—2010 金属切削机床机械加工件通用技术条件 GB/T26220--2010 工业自动化系统与集成机床数值控制数控系统通用技术条件 JB/T3997—2011 金属切削机床灰铸铁件技术条件 JB/T8356.1—1996 机床包装技术条件 JB/T8356.2—1996 机床包装箱
3技术要求
3.1一般要求
本标准是对GB/T9061—2006、GB/T23570—2009、GB/T25373—2010、GB/T25376—2010等标准的具体化和补充,机床的设计与制造除应符合本标准的规定外,还应符合上述标准中未经本标准具体化的其他技术要求。 3.2附件和工具 3.2.1机床应随行供应表1所列的附件和工具。 3.2.2扩大机床性能的特殊附件,可根据用户要求按协议供应。
I
JB/T8485—2013
表1附件和工具用途调整机床用安装工件心轴用安装、调整工件用安装、调整刀具用
名称交换齿轮工件托架工件定位尺刀具主轴垫圈
备注全数控剃齿机不附
数 量 1套 1套 1套 1套 1套 1套 1件
垫铁、地脚螺栓、螺母、垫圈
安装机床用调整、操作机床用
专用扳手千分表
机床检测用
3.3 布局和外观 3.3.1 机床应布局合理、造型美观、色彩和谐,符合人类工效学原则并便于调整及维修。 3.3.2 机床外观表面,不应有未规定的凸起、凹陷、粗糙不平和其他损伤。 3.3.3 机床的防护罩及防护装置应表面平整、匀称,不应翘曲、凹陷。 3.3.4 机床外露零件表面不应有硫碰、锈蚀,螺钉、铆钉、销子端部不应有扭伤、锤伤等缺陷。 3.3.5 金属手轮轮缘和操纵手柄表面应涂层防锈。电镀件、发蓝件、发黑件色调应一致,防护层不应有褪色、脱落现象。 3.3.6 机床涂漆颜色及光泽应均匀一致、涂漆层应平整,涂漆表面不应有起泡及脱落等缺陷。机床可拆卸的装配结合面的接缝处,在涂漆以后,应切开,切开时不应扯破边缘。 3.3.7 机床的各种信息标志及标牌应在机床明显位置平整固定,清晰耐久,不歪斜。 3.3.8# 机床电气、液压、润滑及冷却等的管道的外露部分,应布置紧凑、排列整齐,必要时应用管夹固定,软管不应扭曲:折叠及断裂。 3.3.9装入沉孔的螺钉不应突出于零件表面,其头部与沉孔之问不应有明显的偏心,固定销一般应略突出于零件表面。螺栓尾端应略突出于螺母端面。外露轴端应突出于包容件的端面,突出值约为倒棱值。 内孔表面与壳体凸缘间的壁厚应均匀对称,其凸缘壁厚之差不应大于实际最大壁厚的25%。 3.3.10机床零部件外露结合面的边缘应整齐匀称,不应有明显的错位,门、盖与机床的结合面应贴合。 错位量及贴合缝隙值不应大于表2的规定。
表2错位量及贴合缝隙值
单位为毫米 >1250 3 1.5 2 2
≤500 1.5 1 1 1
结合面边缘及门、盖边长尺寸
>500~1250
错位量错位不匀称量贴合缝隙值缝隙不均勾值
2 1 1.5 1.5
注1:当结合面边缘及门、盖边长尺寸的长、宽不一致时,可按长边尺寸确定允许值。 注2:错位不勾称量指外露结合面边缘同一边或对应边最大错位量与最小错位量之差值。 注3:缝隙不均匀值指门、盖间对开缝或其相对机床本体间最大缝隙值与最小缝隙之差值。
3.4电气系统
机床的电气系统应符合GB5226.1一2008的规定。
2
JB/T8485—2013
3.5数控系统
机床的数控系统应符合GB/T26220—2010的有关规定。 3.6液压、润滑和冷却系统 3.6.1机床的液压系统应符合GB/T23572—2009的规定。 3.6.2机床的润滑系统应符合GB/T6576一2002的规定。 3.6.3机床的冷却系统应保证冷却充分、可靠。 3.6.4机床的液压、润滑、冷却系统及其他部位均不应漏(渗)油、漏(渗)水。切削液不应混入液压系统和润滑系统。 3.7安全卫生
机床上有可能对人身体健康或对设备易造成损伤的部位,应采取安全措施,机床的安全防护应符合 GB15760—2004GB5226.1-2008的规定。 3.8加工和装配质量 3.8.1# 机械加工件、焊接件应符合图样、工艺文件及GB/T23570—2009、GB/T25376—2010等的有关规定。机床的装配应符合GB/T25373一2010的规定。 3.8.27 机床灰铸铁件应符合JB/T3997—2011的规定。 3.8.37 机床的床身、立柱、工作台、垂直滑板体、刀架体、纵向滑板体、摇架、顶尖座等零件为重要铸件,应在粗加工后进行热时效或振动时效等时效处理。 3.8.4纵向滑板导轨副、垂直滑板导轨副、鼓形机构导轨副为重要导轨副,应采取耐磨措施,并符合材质及热处理有关标准的规定。 3.8.5垂直进给丝杠副、主传动齿轮副、刀具主轴、顶尖等零件应采取耐磨措施,并符合材质及热处理有关标准的规定。 3.8.6立柱与床身的结合面,主传动箱与立柱的结合面,固定垂直丝杠的箱体与立柱的结合面等重要固定结合面,其制造及验收应符合GB/T25376—2010和GB/T25373—2010的规定。 3.8.7 纵向滑板导轨副、垂直滑板导轨副、鼓形机构导轨副等滑(滚)动导轨,其制造及验收应符合 GB/T25376—2010和GB/T25373—2010的规定。 3.8.8顶尖座导轨副、刀架回转副、转座体回转副等移置导轨,其制造及验收应符合GB/T25376-一2010 和GB/T25373—2010的规定。 3.8.9各运动坐标轴的滚珠丝杠副安装后的轴向窜动量由设计规定。 3.8.10机床的清洁度的检测按GB/T25374一2010规定的方法进行,其中刀架内部、润滑系统、液压系统的清洁度按重量法检验,其他部位按目测、手感法检验,不应有脏物。
a)刀架内部的杂质、污物不应超过表3的规定。
表3脏物质量限值
最大工件直径mm
<200
部件名称
≥200
脏物质量mg
刀架
6 000
8000
b)机床液压、润滑系统的清洁度:在机床运行30min后,立即在液压系统(或润滑系统)回油口
处取样,一般不少于200mL,其杂质、污物不应超过150mg/L。
3
JB/T84852013
4检验与验收
4.1概述 4.1.1每台机床应在制造厂经检验合格后出厂。特殊情况下经用户同意可在机床使用处进行检验。当在机床使用处验收机床时,其验收的项目由用户与制造厂商定。 4.1.2机床检验分为型式试验和出厂检验。 4.1.2.1属于下列形式之一时,应进行型式试验:
a)新产品试制、定型鉴定; b)机床结构、性能较基型有重大改动。
4.1.2.2机床出厂检验一般包括以下内容:
a)外观检验: b)附件和工具检验: c)参数检验(抽查): d)机床的空运转试验(含抽查项): e)机床的负荷试验(含抽查项); f)机床的最小设定单位检验; g)机床的精度检验: h)其他。
4.2一般要求 4.2.1本标准是对GB/T9061—2006、GB/T23570—2009、GB/T25373—2010、GB/T25376—2010等标准的具体化和补充。按本标准检验与验收机床时,应同时对上述标准中未经本标准具体化的其余有关验收项目进行检验。 4.2.2验收机床时,按GB/T25372一2010规定的IV级精度机床的要求检验。 4.2.3机床检验时,应注意防止气流、光线和热辐射的干扰,应防止受环境温度变化的影响,有恒温要求的机床应在规定的恒温条件下进行检验,检具在使用前应与机床等温。 4.2.4检验与验收前,应将机床安置在适当的基础上,按照制造商的使用说明书调平机床,并应符合 GB/T21946—2008规定的安装要求。 4.2.5检验过程中,不应调整影响机床精度和性能的机构和零件。用地脚螺栓紧固的机床,在检验过程中不应重新调整安装水平。否则,应复检调整后受到影响的有关项目。 4.2.6检验原则上是在制造完毕的成品上进行,特殊情况下可按制造商的使用说明书拆卸某些零、部件。 4.2.7机床由于结构上的限制或不具备规定的测试工具时,可用与标准有等同效果的方法代替。 4.3外观检验
按3.3评定及检验机床的布局和外观质量。 4.4附件和工具的检验
按3.2检验随行供应的附件和工具是否符合规定 4.5参数检验(抽查)
按设计文件检验机床的参数以及机床与工夹量具、附件等连接部位的型式和尺寸。
4
JB/T8485—2013
4.6机床的空运转试验 4.6.1运转检验 4.6.1.1在无负荷状态下,机床刀具轴主运动机构应从最低速度起依次运转,每级速度的运转时问不得少于2min。无级调速的机床应作低中、高速运转。高速运转时间不应少于1h,使主轴轴承达到稳定温度。 4.6.1.2机床各直线运动部件在全行程上分别做低、中、高进给速度和快速进给的空行程试验,其运动应平稳,灵活,无明显的爬行和振动现象。 4.6.2温升试验 4.6.2.1主轴轴承达到稳定温度时,在靠近刀具主轴轴承的外壳处测量轴承的温度和温升,其值不应超过表4的规定。
单位为摄氏度
表4轴承温度及温升限值
温度 55 65
温升 25 35
轴承型式滑动轴承滚动轴承
注:机床经过一定时间运转后,其测量温度值升幅度不超过每小时5℃时,可认为达到了稳定温度 4.6.2.2液压系统应在额定工作压力下连续运转,待油液达到稳定温度后,测量油液的温度和温升,其温度值不应超过60℃,温升值不应超过30℃。 4.6.3主运动和进给运动的检验(抽查)
检验各级主轴转速和进给机构进给量的实际偏差,不得超过标牌指示值的土5%。试验时机床各运动
部件运动应平稳、可靠。 4.6.4动作试验
机床动作试验一般包括下述内容: a)机床刀具主轴在中等转速下连续起动、停止各10次,动作应准确、无故障。 b)检验纵向滑板(或工作台)的自动进给、快速移动及断开,检验纵向滑板(或工作台)在行程
范围内的任意给定位置的起动和停止,各检验5次,应准确可靠、无故障。 c)检验顶尖座在全部移动行程的两端和中问位置的夹紧,每个位置不得少于2次,动作应可靠。 d)检验工件的夹紧、放松各5次,应准确无故障。 e)模拟机床工作状态,操纵机床“急停”按钮(或开关),连续5次,应准确无故障。 f)用数控程序操作机床,在中等速度下分别对各坐标轴进行正、反向起动、停止(或制动)、工作
进给、快速进给及定向试验,各进行10次,动作应灵活、准确、可靠。对无级变速的主运动和进给运动,还应作系统的低、中、高及快速的变换操作试验,动作应灵活可靠。
g)按设计要求,对机床的各自动循环进行试验,工作应正常,性能应可靠、运行应平稳。 4.6.5安全防护装置的检验
按3.7的要求检验安全防护装置是否齐备、可靠。 4.6.6噪声检验
按GB/T16769—2008的规定测量机床的空运转噪声,其噪声声压级不应超过83dB(A)。机床运
n