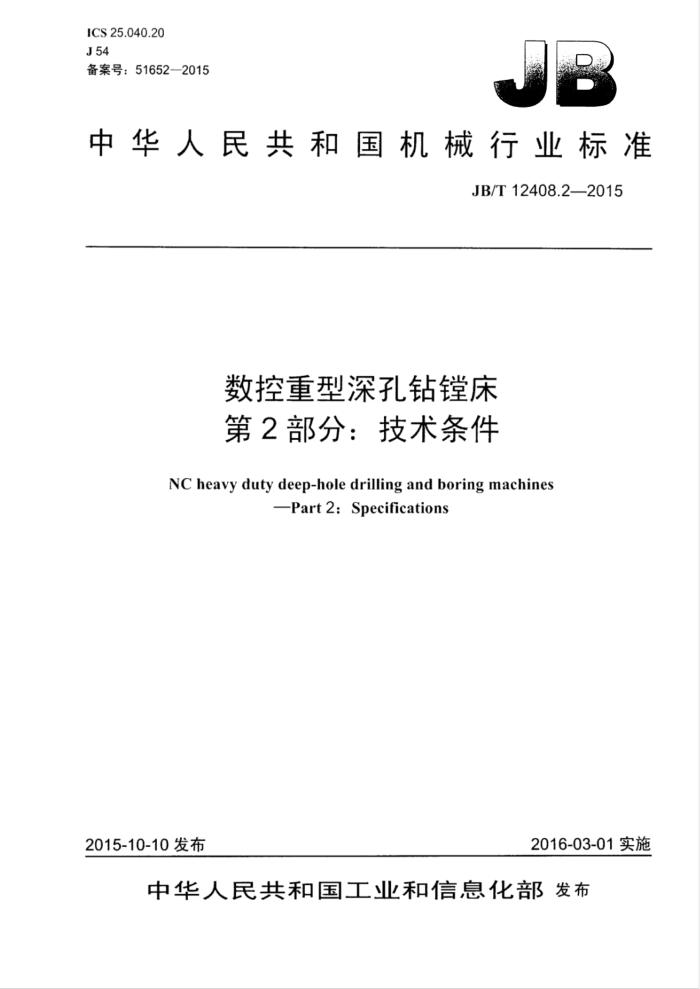
ICS25.040.20 J54 备案号:51652—2015
中华人民共和国机械行业标准
JB/T12408.22015
数控重型深孔钻床第2部分:技术条件
NC heavy duty deep-hole drilling and boring machines
一Part2:Specifications
2016-03-01实施
2015-10-10发布
中华人民共和国工业和信息化部发布
JB/T12408.2—2015
目 次
前.
范圃规范性用文件
1
3 一股要求 4. 附件和具 5 安个H生 6 加工和装配质品.
机床车运转试验. 机床负荷试验机床精度检验 9.1 儿何情度检验 9.2 作精度检验 9.3 原点返叫试验 9.4 最小设定单位试验
8 9
一
4
JB/T12408.2—2015
前言
JB/T12408《数控重型深孔销障床》分为两个部分:一第1部分:精度检验:
第2部分:技术条件。 本部分为JB/T12408的第2部分。 本部分按照GB/T1.1一2009给H的规则起草。 本部分由机械「业联合会提山。 本部分山金国金属切机床标准化技术委员会(SAC/TC22)本部分起革单位:齐币数控装备股份有限公司、武汉正型机床集4有限公司。 部分要起草人:杨华眸、斌、湖巍,明珠、伊竞平。 本部分为直次发有。
II
JB/T12408.22015
数控重型深孔钻床第2部分:技术条件
1范围
JB/T12408的本部分规定了数控重型深孔钻镜床制造和验收的要求。 本部分适川」最人错于直径为250mm2000mm,最人镜深度为3000mm~25000mm、最人
钻孔径为60mm200mm的「件辅箱固定型和移动型般用途的数控重型深孔销镗床(以下简称机床)。
2规范性引用文件
下列文件对本文件的应川是必不町少的。凡是注印期的别用文件,仪注期的版本适川」本文件。 凡是不期的用文,正最新版不(也括所有的修改单)适用本文件
GB5226.1--2008 机械地安个机械地设备第1部分:通用技术条件 GB/T6576-—2002 机床润滑系统 GB/T9061--2006 金底助削机床通用技术条件 GB15760—2004 金腐切削机床安企防护通用技术条件 GB/T16769-—2008 金属切削机床噪雷用级测量方法 GB/T23570-2009 金属切削机床焊接件通用技术条件 GB/T23572—2009 金属切削机床 液压系统通用技术条件 GB/T23575—2009 金腐切削机床 圆锥表面涂色法检验及评定 GB/T25373—2010 金属切削机床 装配通用技术条件 GB/T25374—2010 金属切削机床 清洁度的测量方法 GB/T25375-2010 金属切削机床 结合面涂色法检验及评定 GB/T25376-—2010 金属切削机床 机械加工件通用技术条件 JB/T12408.1-2015 数控重型深孔钻镜床第1部分:精度检验
3一般要求
按本部分验收机床时,同时对GB/T90612006,GB/T235702009,GB/T253762010-GB/T
25373一2010等标准中未经本部分具体化的具余项自进行检验。
4附件和工具
4.1应随机供以下列附件和工具:
a)专用工具一套: b)地脚螺栓、螺、垫圈、调整垫铁一套。
4.2扩大机床使用性能的特殊附件,应根据用户要求按协议供应。 4.3机床的标准附件和下具,均应保证连接部位的互换性和使用性能。
JB/T12408.2—2015
5安全卫生
5.1# 机床地系统的安个符合GB5226.1-2008的规定。 5.2机床液系统的安个应符个GB235722009的规定。 5.3 机床润清滑系统的安全符合GB/T6576一2002的规定。 5.4的安个防护除以符合GB15760-一2004的规定外,还符合下列要求:
a)钻杆箱以设有极限位置的安全保险装置: b)件正轴箱滑板、钻箱滑板、钻杆心架、导间中心架与导轨结合的两端均应设置防护装
置
5.5应按GB16769一2008的规定检验机未的噪。机床噪测量在工件正轴箱和钻箱等正运动正、反转的低、、高速和钻箱的进给运动在速时的空运转条件下进行,整机噪南主级不应超过 85dB(A电动机部位噪级不超过90dB(A) 5.6在作行程范捆内,手轮、手柄的操纵力以均匀不以超过表1的规定。
表1
单位为
名称
操纵力
厂件主轴箱、钻箱变速于柄 J架叫转、移动于轮、于柄
120 200
「作心架、钻干中心架移动于轮、手柄
6加工和装配质量
6.1「件床身、钻杆床身。件主轴箱体及其滑板、钻杆箱体及其滑板。导间叶心架正体与下体等为重要零件,料加厂后应进行热时效或振动时效处理,或采取其他消除内应力的措施。 6.2件正轴箱轴副、钻杆箱主轴副、高速重载齿轮、床身丝杠副等主要零件,以采取与寿命相适应的耐磨措施。 6.31件上轴箱滑板、钻杆箱滑板、导问中心架下体等与床身导轨结合的导轨副为重要导轨副,应采取与寿命相适的耐磨措施。 6.4下列结合面以按“重要固定结合面”的要求考核:
a)工件主轴箱与主轴箱底座(或滑板)的结合面: b)钻杆箱与滑板的结合面: c)工件中心架上体与下体的结合面: d)进给箱与滑板的结合面: e)钻杆中心架上体与下体的结合面: f)丝杜支架与床身的结合面: g)齿条与床身的结合面; h)拼接床身的结合面。 重要固定结合面应紧密贴合,紧固后用0.04mm塞尺检验时不应插入,局部(2处~3处)允许插
入深度不大」20mm。插入部位若长度小』或等了结合面长度的1/5,但不大」100mm:则按一处缺陷计。 6.5导同中心架上体与下体的结合面应按“特别重要固定结合面”的要求考核。 6.6下列导轨副按“滑动导轨”的要求考核:
a)钻杆箱导轨副:
2
JB/T12408.2—2015
b)钻杆中心架导轨副。 6.7下列导轨副应按“移置导轨的要求考核
a)1件心架导轨副: b)1件轴箱导轨副: c)导向中心架导轨副。
6.8滑动导轨、移置导轨和特别重要固定结合面应做涂色法检验,检验及评定方法应符合GB/T25375 2010的规定,接触指标按GB/T25373一2010表2或表3规定的V级精度等级机床考核。 6.9滑动导轨、移置导轨和特别重要固定结合面除用涂色法检验外,还以用塞尺检验,按GB/T25373 -2010表4或表5规定的V级精度等级机床考核。 6.10件主轴维孔、钻杆正轴孔以做涂色法检验,检验及评定方法应符合GB/23575-一2009的规定,锥体的接触靠近人端,接触指标按GB/T25376一2010表2规定的V级精度等级机床考核。 6.11下列重要定位销以做涂色法检验,其接触长度不以小」1作长度的60%,检验及评定方法应符合 GB/T23575—2009的规定。
a)1件正轴箱与1轴箱底座(或滑板)的定位销: b)销箱与滑板的定位销: c)导间中心架上体与下体的定位销: d)进给箱与滑板的定位销: e)钻料中心架上体与下体的定位销; f)丝支架与床身的定位销:)条床身的定位销; h)拼接床身的定位销:)【件正轴箱滑板与丝杠螺支架的定位销:)工件主轴轴瓦与厂件轴箱体的定位销: k)钻杆主轴轴瓦与钻杆箱体的定位销。
6.12导轨、丝杠等易被尘屑磨损的部位宜采取防护装置。 6.13带刻度装置的手轮、手柄的反向空程量以不超过1/4转。 6.14以按GB/25374-一2010的规定检验清洁度。件主轴箱、钻杆箱、钻杆进给箱、液用汕箱内部清洁度按重量法抽样检验(抽查),其杂质、污物限值:工件正轴箱、钻杆箱、钻杆进给箱不应超过 400mg/L,液压汕箱不应超过200mg/L(抽查)。其他部位按目测手感法检验,不有污物。
7机床空运转试验
7.1T件主轴、钻杆主轴从最低速度起依次运转,每级速度的运转时问不应少了2min。无级调速的机床可做低、中、高速运转。最高速度运转不应少丁1h,使主轴轴承达到稳定温度,在靠近正轴轴承部位测量轴承的温度和温升,其值不应超过表2的规定。
表2 温度 60 70
单位为摄氏度
轴承型式滑动轴承滚动轴承
温川 30 40
-
1
注:机床经过一定时间的运转后,当其测量温度值1幅度不超过5℃/h时,一般认为已达到稳定温度 7.2在空运转条件下,有级传动的工件上轴、钻杆主轴转速和钻杆进给量的实际偏差,不应超过标牌指示值的-2%一6%:无级变速传动的工件主轴、钻杆上轴转速和钻杆进给量的实际偏差,不应超过指
3
JB/T12408.2-2015
小值的土10% 7.3用一种适当的速度对件轴箱和钻杆箱等1运动和进给运动进行正间、反间的连续起动、停!(包括制动:点动)1次的动作试验。 7.4销杆进给箱应做低、十、高进给速度的牢运转试验,充许与件主轴箱、钻杆箱的运动试验同司时进行,档试验时间不应少」2min。 7.51件正轴箱(移动型)、钻杆箱、导间中心架、钻杆心架(箱飘动)应做正间、反间快速移动试验,往复次数不应少」次,其行程不应少」全行程之。 7.61传动系统牢运转功率按设计规定考核。 7.7 各项空运转试验时,各操作机构的动作灵活、平稳、安全、尚靠。
8机床负荷试验
8.1本系列机床应做下列负荷试验,“制造厂不其备试验条件时,经川广同意,试验可用厂进行。
a)机床承载件最人平量的运转试验(插抑#: b)机床正传动系统最人转知试验: c)机床战人切利抗力试验: d)机床主传动系统最人功率试验()。
82对机床承载正件最人重量的运转试验,应盘利心架火持!件,用低速及设训规定的高速运转,运转时间不少」0min 8.3机床传动系统的最人转知、最人切抗力试验用强力钻刷内孔(或设训规定)的方法进行。 8.4机床传动系统最人功率试验,在正轴转速范间内选川:适光正轴转速,采用销别方法进行。 8.5机床1:传动系统的最大转知、最人切削抗力和最人功率试验,其试验材料、切制规范等按设计-文件规定。
注:最人功率系指设计功率。 8.6各项负荷试验时,机床厂作平稳、尚靠。
9机床精度检验
9.1几何精度检验
机床精度检验应按JB/T12408.1-2015的规定进行。H十G10、G15、G20、G21项以在中速稳定温度时检验。 9.2工作精度检验
工作精度检验时刀具的材料、型式和切削用量由制造厂规定,试件表面粗糙度Ra最大允许值为2.5μm。 9.3原点返回试验 9.3.1试验方法
各直线坐标上的运动部件,从行程上的任意点,按相同的移动方向,以快速进行5次返回原点Po 的试验。测量每次实际位置Pio与原点理论位置Po的偏差Xio(i=1,2,,5),如图1所示。
各直线坐标至少在行程的中问及靠近两端的任意三个位置进行试验。
4
JB/T12408.2—2015
i= Q
2 9 Q 4Q 50
tic 图1
9.3.2误差计算方法
各点线整标中,原点返回试验时的标准不确定度的最大值的4倍即为原点返叫误差,误差以一个位置的最人误券值计。 9.3.3允差
允差按制造广设订规定。 9.3.4检验工具
激光干涉仪或读数最微镜利金属线纹尺。 9.4最小设定单位试验 9.4.1试验方法
先以快速使点线整标的运动部件向正(或负)向移动:定距离,停山后,向同方向给比数个最小设定单位的指令,再停山,以此位置为基准位置,每次给出一个,共给出20个最小设定单位的指令,使运动部件向同方向移动,测量各个指令的停山位置。从正述的最终位置,继续向同方向给出数个最小设定单位指令,停后,向负(或正)向给出数个最小设定单位的指令,使运动部件约返间到上述最终的测量位置,这些正向和负问的数个最小设定单位指令的停位置不做测量。然后从上述的最终位置开始,每次给出一个,共给出20个最小设定单位的指令,使其继续向负(或正)向移动,测量各指令的停位置,如图2所示。
各直线坐标均以在行程的中间及两端三个位置上分别进行试验。 9.4.2误差计算
误差分为最小设定单位误差和最小设定单位相对误差,分别按公式(1)、公式(2)进行计算,以个位置上的最大误差值作为该项的误差。 9.4.2.1最小设定单位误差S按公式(1)计算。
Sa=L-m
(1)
式中: L
一个最小设定单位指令的实际位移(实际位移的方向如与给出的方向相反,其位移以为负值),单位为毫米(mm):个最小设定单位指令的理论位移,单位为毫米(mm)。
一
m
5