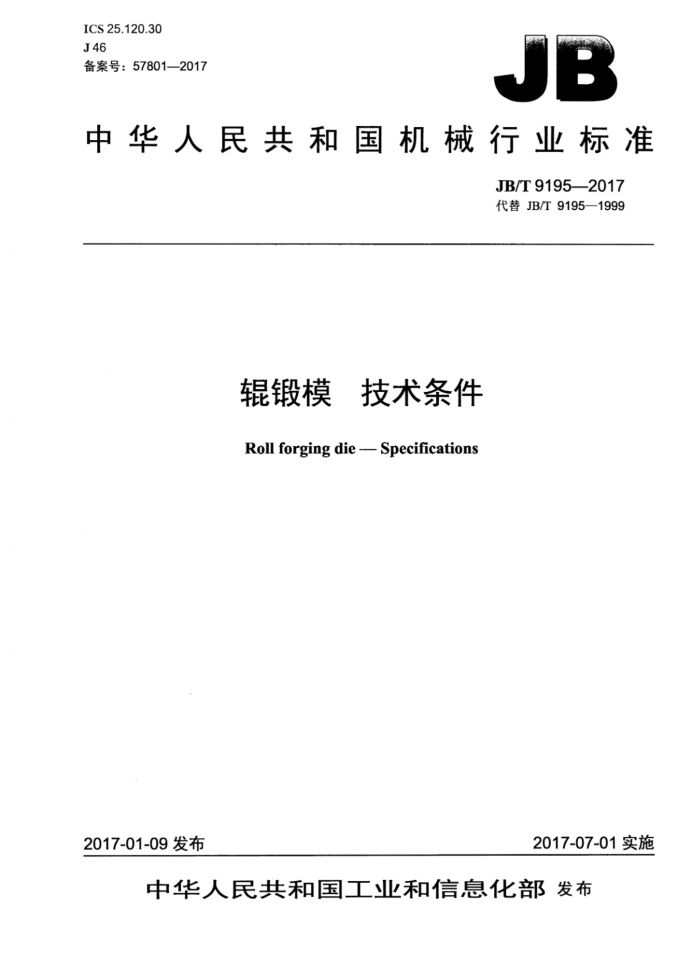
ICS25.120.30 J46 备案号:57801—2017
JB
中华人民共和国机械行业标准
JB/T9195—2017 代替JB/T9195—1999
辊锻模 技术条件
Rollforgingdie-Specifications
2017-01-09发布
2017-07-01实施
中华人民共和国工业和信息化部发布
JB/T91952017
目 次
前言 1范围 2 规范性引用文件 3 要求
-
3.1 材料要求 3.2 零件要求.. 3.3装配要求... 4检验方法.. 5验收.. 6标志、包装和运输,
.
表1辊锻模主要零件的推荐材料及热处理硬度表2型槽尺寸的极限偏差
JB/T9195—2017
前言
本标准按照GB/T1.1-—2009给出的规则起草。 本标准代替JB/T9195—1999《辊锻模通用技术条件》,与JB/T9195—1999相比,主要技术变化
如下:
一将《辊锻模 通用技术条件》更名为《辊锻模技术条件》;一将规范性引用文件中注日期引用的文件改为现行版本;按现行国家标准对内容、结构及表格进行了必要的修改和完善;一增加了“验收”部分的内容。 本标准由中国机械工业联合会提出。 本标准由全国模具标准化技术委员会(SAC/TC33)归口。 本标准起草单位:安徽省瑞杰锻造有限责任公司、桂林电器科学研究院有限公司、南京东模机电科
技有限公司、北京机电研究所、华中科技大学。
本标准主要起草人:吕美莲、朱磊文、陈东辉、蒋鹏、王新云、刘春超、王冲、陈清华、贺小毛。 本标准所代替标准的历次版本发布情况为:
ZB/TJ46003—1990; JB/T9195—1999。
II
JB/T9195—2017
辊锻模 技术条件
1范围
本标准规定了辊锻模的要求、检验方法、验收、标志、包装和运输。 本标准适用于辊锻模。
2规范性引用文件
下列文件对于本文件的应用是必不可少的。凡是注日期的引用文件,仅注日期的版本适用于本文件。凡是不注日期的引用文件,其最新版本(包括所有的修改单)适用于本文件。
GB/T191包装储运图示标志 GB/T230.1金属材料洛氏硬度试验 第1部分:试验方法(A、B、C、D、E、F、G、H、K、
N、T标尺)
GB/T231.1 金属材料布氏硬度试验第1部分:试验方法 GB825吊环螺钉 GB/T1184—1996 形状和位置公差未注公差值 GB/T1801—2009 产品几何技术规范(GPS)极限与配合公差带和配合的选择 GB/T1804—2000 一般公差未注公差的线性和角度尺寸的公差 GB/T3098.1—2010 紧固件机械性能螺栓、螺钉和螺柱 GB/T11880—2008 模锻锤和大型机械锻压机用模块技术条件 GB/T14979 钢的共晶碳化物不均匀度评定法 JB/T9194锻模辊锻模结构型式及尺寸
3要求
3.1材料要求 3.1.1辊锻模零件所选用的材料应符合相应牌号的技术标准。 3.1.2辊锻模材料应进行超声探伤,探伤结果应符合GB/T11880—2008中3.8的规定。 3.1.3辊锻模主要零件的推荐材料及热处理硬度见表1。可采用性能高于表1推荐的材料。
表1辊锻模主要零件的推荐材料及热处理硬度
硬度 42 HRC ~ 45 HRC 28 HRC ~ 32 HRC
材料牌号
主要零件扇形模块
5CrNiMo、5CrMnMo、3Cr2W8V
压紧环、挡环、定位环
45、40Cr
3.1.4辊锻模所使用的合金工具钢不应有网状碳化物,共晶碳化物不均匀度应不大于GB/T 14979--1994附录A中3级的规定。 3.1.5辊锻模毛坏的锻造比应符合GB/T118802008中3.6的规定。
1
JB/T9195—2017
3.2 零件要求
3.2.1 扇形模块的形状和尺寸应符合JB/T9194的规定。 3.2.2 模块型槽尺寸的极限偏差应符合表2的规定。
表2型槽尺寸的极限偏差
单位为毫米
制坏
预成型
终成型
公称尺寸
长度 宽度 深度 宽度 深度 长度 宽度 深度 长度
1.10 ±0.43 +0.43
+2.20
+0.18 0.11 +0.21 0.13
+0.18 0.11
+0.11 0.07
≤18
±1.10
±0.11
±0.11
0.27 +0.52 0.33 +0.62 +0.25 0.39
+2.60 1.30 +3.20 1.60 +3.80 1.90 +4.40 2.20
±0.13 +0.21 +0.13 ±0.13
±1.30
±0.52
>18~30
0.13 +0.25 0.16 +0.30 0.19 +0.35 +0.22 0.22
0.08 +0.16 0.10 +0.19 0.12
>30~50
±0.62
±1.60
±0.16
±0.16
0.16 +0.30
+0.74 0.46 0.19 +0.87
>50~80
±1.90
±0.74
±0.19
±0.19
+0.35 0.22
>80~120
±2.20
±0.22
±0.87
±0.22
0.54
0.14
±1.00 +1.00 +0.40 ±0.25 +0.40 +0.25 ±0.25
>120~180
±2.50
0.63 0.25 +1.15 0.72 +1.30 0.81 +1.40 0.89 +1.55 0.97 +1.75 1.10 +2.00 1.25 +2.30 1.40
0.25 +0.46 0.29 +0.52 0.32 +0.57 0.36 +0.63 0.40 +0.70 0.44 +0.80 0.50 +0.90 0.56
0.16
>180~250
±2.90
±0.29
±0.29
±3.20
>250~315
±0.32
±0.32
>315~400 ±3.60
±0.36
±0.36
>400~500
±4.00
±0.40
±0.40
±4.40
>500~630
±0.44
±0.44
>630~800 ±5.00
±0.50
±0.50
-
>800~1000 ±5.60
±0.56
±0.56
注:沿辊锻方向为长度方向,与其垂直的方向为宽度方向。 3.2.3 零件未注公差的尺寸极限偏差应符合GB/T1804一2000中m级的规定。 3.2.4 4零件未注的形状和位置公差值应符合GB/T1184一1996中K级的规定。 3.2.5 5零件的所有凹角应圆滑过渡。 3.2.6 6零件不应有裂纹,工作表面不应有划痕、机械损伤、锈蚀等缺陷。 3.2.7 扇形模块成形表面的表面粗糙度Ra宜为1.6um,其他表面的表面粗糙度应符合JB/T9194的规定。 3.2.8 3紧固件性能等级应为GB/T3098.1-2010中的10.9级。
2
JB/T9195—2017
3.2.9 9质量超过15kg的模具应设置起吊孔,确保安全吊装,吊环螺钉应符合GB825的规定。 3.3装配要求 3.3.1 螺钉和销钉的端面不应凸出模具表面,直不应松动。 3.3.2 扇形模块与锻辊的配合公差应符合GB/T1801一2009表1中H9/h9的规定。
4检验方法
4.1布氏硬度的检验应符合GB/T231.1的规定,洛氏硬度的检验应符合GB/T230.1的规定。 4.2模块型槽的形状和尺寸应采用样板和通用量具检测。 4.3对于模具表面粗糙度,Ra1.6μm以下的表面宜采用表面粗糙度测量仪检测,其余表面宜采用表面粗糙度比较样块目测检验。
5验收
5.1验收应包括以下内容:
a)尺寸、外观检验; b)试模和辑锻件质量符合性检验: c)模具质量稳定性检验。
5.2模具供方和顾客应按模具图样对模具进行外观与尺寸检验。供方应向顾客提供原材料质量保证书,热处理检验报告及超声波探伤检测报告。 5.3完成5.2项目检验并确认合格后,可进行试模和锻件质量符合性检验,具体要求如下:
a)试模应严格遵守辊锻成形工艺规程; b)试模所用材料应符合辊锻件图样的规定: c)辊锻模装机后应先空载运行,确认辊锻模运转正常,无干涉; d)试模运行稳定后,应抽取3~10个锻件进行检验。
5.4模具质量稳定性检验的生产批量应为100模次,或由模具供方和顾客商定。 5.5模具供方和顾客确认产品合格后,供方应开具模具合格证随模具交付顾客,并提供由供方和顾客商定的工艺资料。
6标志、包装和运输
6.1在模具非工作面的明显处应有标志。标志宜有下列内容:
a)模具名称及编号; b)模具质量; c)供方名称: d)出厂日期。
6.2模具交付前应清洗于净,所有工作表面应涂覆防锈剂。 6.3出厂模具根据运输要求进行包装,应防潮、防磕碰。外包装应按GB/T191的规定设置防潮、防倒置等标记。
3
中华人民共和国
机械行业标准辊锻模技术条件 JB/T9195—2017
*
机械工业出版社出版发行北京市百万庄大街22号
邮政编码:100037
*
210mm×297mm·0.5印张·11千字
2017年7月第1版第1次印刷
定价:12.00元
*
书号:15111·14253 网址:http:/www.cmpbook.com 编辑部电话:(010)88379399 直销中心电话:(010)88379399
封面无防伪标均为盗版
JB/T9195-2017 打印日期:2018年3月21日F009A
版权专有 侵权必究
ICS25.120.30 J46 备案号:57801—2017
JB
中华人民共和国机械行业标准
JB/T9195—2017 代替JB/T9195—1999
辊锻模 技术条件
Rollforgingdie-Specifications
2017-01-09发布
2017-07-01实施
中华人民共和国工业和信息化部发布
JB/T91952017
目 次
前言 1范围 2 规范性引用文件 3 要求
-
3.1 材料要求 3.2 零件要求.. 3.3装配要求... 4检验方法.. 5验收.. 6标志、包装和运输,
.
表1辊锻模主要零件的推荐材料及热处理硬度表2型槽尺寸的极限偏差
JB/T9195—2017
前言
本标准按照GB/T1.1-—2009给出的规则起草。 本标准代替JB/T9195—1999《辊锻模通用技术条件》,与JB/T9195—1999相比,主要技术变化
如下:
一将《辊锻模 通用技术条件》更名为《辊锻模技术条件》;一将规范性引用文件中注日期引用的文件改为现行版本;按现行国家标准对内容、结构及表格进行了必要的修改和完善;一增加了“验收”部分的内容。 本标准由中国机械工业联合会提出。 本标准由全国模具标准化技术委员会(SAC/TC33)归口。 本标准起草单位:安徽省瑞杰锻造有限责任公司、桂林电器科学研究院有限公司、南京东模机电科
技有限公司、北京机电研究所、华中科技大学。
本标准主要起草人:吕美莲、朱磊文、陈东辉、蒋鹏、王新云、刘春超、王冲、陈清华、贺小毛。 本标准所代替标准的历次版本发布情况为:
ZB/TJ46003—1990; JB/T9195—1999。
II
JB/T9195—2017
辊锻模 技术条件
1范围
本标准规定了辊锻模的要求、检验方法、验收、标志、包装和运输。 本标准适用于辊锻模。
2规范性引用文件
下列文件对于本文件的应用是必不可少的。凡是注日期的引用文件,仅注日期的版本适用于本文件。凡是不注日期的引用文件,其最新版本(包括所有的修改单)适用于本文件。
GB/T191包装储运图示标志 GB/T230.1金属材料洛氏硬度试验 第1部分:试验方法(A、B、C、D、E、F、G、H、K、
N、T标尺)
GB/T231.1 金属材料布氏硬度试验第1部分:试验方法 GB825吊环螺钉 GB/T1184—1996 形状和位置公差未注公差值 GB/T1801—2009 产品几何技术规范(GPS)极限与配合公差带和配合的选择 GB/T1804—2000 一般公差未注公差的线性和角度尺寸的公差 GB/T3098.1—2010 紧固件机械性能螺栓、螺钉和螺柱 GB/T11880—2008 模锻锤和大型机械锻压机用模块技术条件 GB/T14979 钢的共晶碳化物不均匀度评定法 JB/T9194锻模辊锻模结构型式及尺寸
3要求
3.1材料要求 3.1.1辊锻模零件所选用的材料应符合相应牌号的技术标准。 3.1.2辊锻模材料应进行超声探伤,探伤结果应符合GB/T11880—2008中3.8的规定。 3.1.3辊锻模主要零件的推荐材料及热处理硬度见表1。可采用性能高于表1推荐的材料。
表1辊锻模主要零件的推荐材料及热处理硬度
硬度 42 HRC ~ 45 HRC 28 HRC ~ 32 HRC
材料牌号
主要零件扇形模块
5CrNiMo、5CrMnMo、3Cr2W8V
压紧环、挡环、定位环
45、40Cr
3.1.4辊锻模所使用的合金工具钢不应有网状碳化物,共晶碳化物不均匀度应不大于GB/T 14979--1994附录A中3级的规定。 3.1.5辊锻模毛坏的锻造比应符合GB/T118802008中3.6的规定。
1
JB/T9195—2017
3.2 零件要求
3.2.1 扇形模块的形状和尺寸应符合JB/T9194的规定。 3.2.2 模块型槽尺寸的极限偏差应符合表2的规定。
表2型槽尺寸的极限偏差
单位为毫米
制坏
预成型
终成型
公称尺寸
长度 宽度 深度 宽度 深度 长度 宽度 深度 长度
1.10 ±0.43 +0.43
+2.20
+0.18 0.11 +0.21 0.13
+0.18 0.11
+0.11 0.07
≤18
±1.10
±0.11
±0.11
0.27 +0.52 0.33 +0.62 +0.25 0.39
+2.60 1.30 +3.20 1.60 +3.80 1.90 +4.40 2.20
±0.13 +0.21 +0.13 ±0.13
±1.30
±0.52
>18~30
0.13 +0.25 0.16 +0.30 0.19 +0.35 +0.22 0.22
0.08 +0.16 0.10 +0.19 0.12
>30~50
±0.62
±1.60
±0.16
±0.16
0.16 +0.30
+0.74 0.46 0.19 +0.87
>50~80
±1.90
±0.74
±0.19
±0.19
+0.35 0.22
>80~120
±2.20
±0.22
±0.87
±0.22
0.54
0.14
±1.00 +1.00 +0.40 ±0.25 +0.40 +0.25 ±0.25
>120~180
±2.50
0.63 0.25 +1.15 0.72 +1.30 0.81 +1.40 0.89 +1.55 0.97 +1.75 1.10 +2.00 1.25 +2.30 1.40
0.25 +0.46 0.29 +0.52 0.32 +0.57 0.36 +0.63 0.40 +0.70 0.44 +0.80 0.50 +0.90 0.56
0.16
>180~250
±2.90
±0.29
±0.29
±3.20
>250~315
±0.32
±0.32
>315~400 ±3.60
±0.36
±0.36
>400~500
±4.00
±0.40
±0.40
±4.40
>500~630
±0.44
±0.44
>630~800 ±5.00
±0.50
±0.50
-
>800~1000 ±5.60
±0.56
±0.56
注:沿辊锻方向为长度方向,与其垂直的方向为宽度方向。 3.2.3 零件未注公差的尺寸极限偏差应符合GB/T1804一2000中m级的规定。 3.2.4 4零件未注的形状和位置公差值应符合GB/T1184一1996中K级的规定。 3.2.5 5零件的所有凹角应圆滑过渡。 3.2.6 6零件不应有裂纹,工作表面不应有划痕、机械损伤、锈蚀等缺陷。 3.2.7 扇形模块成形表面的表面粗糙度Ra宜为1.6um,其他表面的表面粗糙度应符合JB/T9194的规定。 3.2.8 3紧固件性能等级应为GB/T3098.1-2010中的10.9级。
2
JB/T9195—2017
3.2.9 9质量超过15kg的模具应设置起吊孔,确保安全吊装,吊环螺钉应符合GB825的规定。 3.3装配要求 3.3.1 螺钉和销钉的端面不应凸出模具表面,直不应松动。 3.3.2 扇形模块与锻辊的配合公差应符合GB/T1801一2009表1中H9/h9的规定。
4检验方法
4.1布氏硬度的检验应符合GB/T231.1的规定,洛氏硬度的检验应符合GB/T230.1的规定。 4.2模块型槽的形状和尺寸应采用样板和通用量具检测。 4.3对于模具表面粗糙度,Ra1.6μm以下的表面宜采用表面粗糙度测量仪检测,其余表面宜采用表面粗糙度比较样块目测检验。
5验收
5.1验收应包括以下内容:
a)尺寸、外观检验; b)试模和辑锻件质量符合性检验: c)模具质量稳定性检验。
5.2模具供方和顾客应按模具图样对模具进行外观与尺寸检验。供方应向顾客提供原材料质量保证书,热处理检验报告及超声波探伤检测报告。 5.3完成5.2项目检验并确认合格后,可进行试模和锻件质量符合性检验,具体要求如下:
a)试模应严格遵守辊锻成形工艺规程; b)试模所用材料应符合辊锻件图样的规定: c)辊锻模装机后应先空载运行,确认辊锻模运转正常,无干涉; d)试模运行稳定后,应抽取3~10个锻件进行检验。
5.4模具质量稳定性检验的生产批量应为100模次,或由模具供方和顾客商定。 5.5模具供方和顾客确认产品合格后,供方应开具模具合格证随模具交付顾客,并提供由供方和顾客商定的工艺资料。
6标志、包装和运输
6.1在模具非工作面的明显处应有标志。标志宜有下列内容:
a)模具名称及编号; b)模具质量; c)供方名称: d)出厂日期。
6.2模具交付前应清洗于净,所有工作表面应涂覆防锈剂。 6.3出厂模具根据运输要求进行包装,应防潮、防磕碰。外包装应按GB/T191的规定设置防潮、防倒置等标记。
3
中华人民共和国
机械行业标准辊锻模技术条件 JB/T9195—2017
*
机械工业出版社出版发行北京市百万庄大街22号
邮政编码:100037
*
210mm×297mm·0.5印张·11千字
2017年7月第1版第1次印刷
定价:12.00元
*
书号:15111·14253 网址:http:/www.cmpbook.com 编辑部电话:(010)88379399 直销中心电话:(010)88379399
封面无防伪标均为盗版
JB/T9195-2017 打印日期:2018年3月21日F009A
版权专有 侵权必究