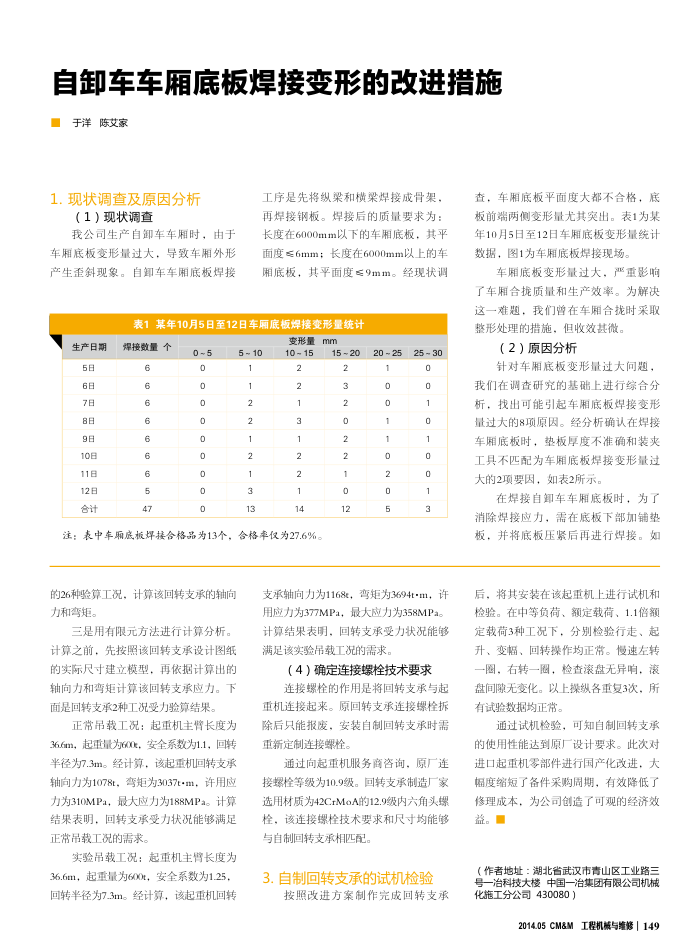
自卸车车厢底板焊接变形的改进措施于洋陈艾家
1.现状调查及原因分析
(1)现状调查
我公司生产自卸车车厢时,由于车厢底板变形量过大,导致车厢外形产生垂斜现象。自卸车车厢底板焊接
工序是先将纵梁和横架焊接成骨架,再焊接钢板。焊接后的质量要求为:长度在6000mm以下的车厢底板,其平面度≤6mm;长度在6000mm以上的车厢底板,其平面度≤9mm。经现状调
表1某年10月5日至12日车厢底板焊接变形量统计
生产日期 5日 6日 7日 8日 9日 10日 11日 12日合计
焊接数量个
6 6 6 6 6 6 6 5 47
0~5 0 0 0 0 0 0 0 0
5 ~ 10 1 1 2 2 1 2 1 3 13
变形量mm
15 ~20
10~15
2 2 1 3 1 2 2 1 14
注:表中车厢底板焊接合格品为13个,
合格率仅为27.6%。
的26种验算工况,计算该回转支承的轴向力和弯矩。
三是用有限元方法进行计算分析计算之前,先按照该回转支承设计图纸的实际尺寸建立模型,再依据计算出的轴向力和弯矩计算该回转支承应力。下面是回转支承2种工况受力验算结果。
正常吊载工况:起重机主臂长度为 36.6m,起重量为600,安全系数为1.1,回转半径为7.3m。经计算,该起重机回转支承轴向力为1078t,弯矩为3037t+m,许用应力为310MPa,最大应力为188MPa。计算结果表明,回转支承受力状况能够满足正常吊载工况的需求。
实验吊载工况:起重机主臂长度为 36.6m,起重量为600t,安全系数为1.25,回转半径为7.3m。经计算,该起重机回转
2 3 2 0 2 2 1 0 12
20 ~ 25
25~30
1 0 0
1 0 2 0 5
0 0 1 0 1 0 0 1 3
支承轴向力为1168t,弯矩为3694t*m,许用应力为377MPa,最大应力为358MPa。计算结果表明,回转支承受力状况能够满足该实验吊载工况的需求。
(4)确定连接螺栓技术要求
连接螺栓的作用是将回转支承与起重机连接起来。原回转支承连接螺栓折除后只能报废,安装自制回转支承时需重新定制连接螺栓。
通过向起重机服务商咨询,原厂连接螺栓等级为10.9级。回转支承制造厂家选用材质为42CrMoA的12.9级内六角头螺栓,该连接螺栓技术要求和尺寸均能够与自制回转支承相匹配。
3.自制回转支承的试机检验
按照改进方案制作完成回转支承
查,车厢底板平面度大都不合格,底板前端两侧变形量尤其突出。表1为某年10月5日至12日车厢底板变形量统计数据,图1为车厢底板焊接现场。
车厢底板变形量过大,严重影响了车厢合拢质量和生产效率。为解决这一难题,我们曾在车厢合拢时采取整形处理的措施,但收效甚微。
(2)原因分析
针对车底板变形量过大问题,我们在调查研究的基础上进行综合分析,找出可能引起车厢底板焊接变形量过大的8项原因。经分析确认在焊接车厢底板时,势板厚度不准确和装夹工具不匹配为车厢底板焊接变形量过大的2项要因,如表2所示。
在焊接自卸车车厢底板时,为了消除焊接应力,需在底板下部加铺势板,并将底板压紧后再进行焊接。如
后,将其安装在该起重机上进行试机和检验。在中等负荷、额定载荷、1.1倍额定载荷3种工况下,分别检验行走、起升、变幅、回转操作均正常。慢速左转一圈,右转一圈,检查滚盘无异响,滚盘间隙无变化。以上操纵各重复3次,所有试验数据均正常。
通过试机检验,可知自制回转支承的使用性能达到原厂设计要求。此次对进口起重机零部件进行国产化改进,大幅度缩短了备件采购周期,有效降低了修理成本,为公司创造了可观的经济效益。
(作者地址:湖北省武汉市青山区工业路三号一冶科技大楼中国一治集团有限公司机械化施工分公司430080)
2014.05CM&M工程机械与维修|149