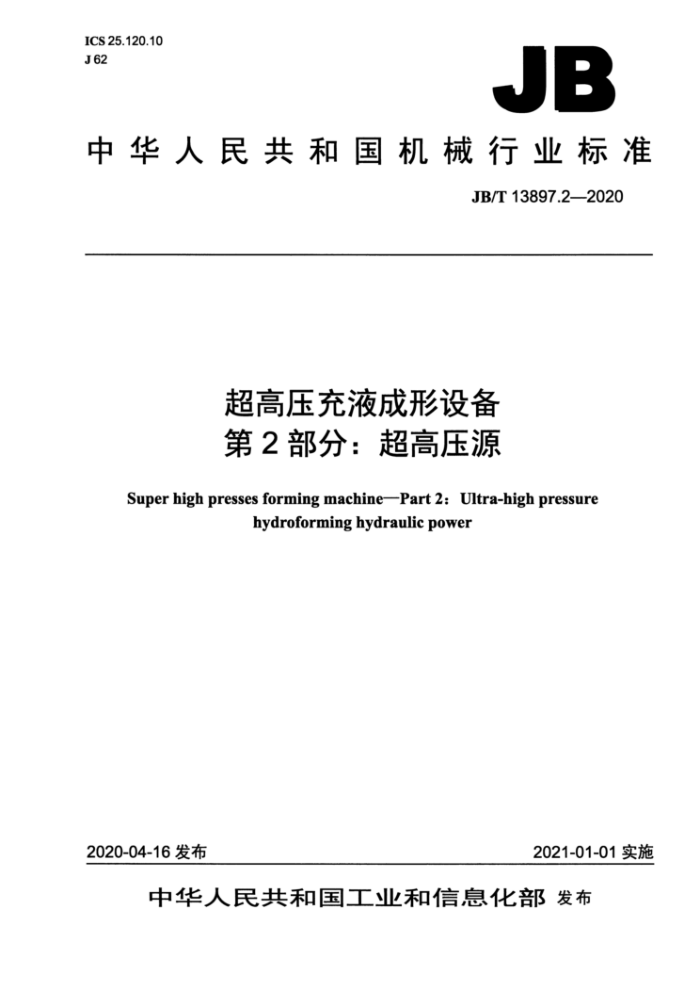
ICS25.120.10 J62
JB
中华人民共和国机械行业标准
JB/T13897.2—2020
超高压充液成形设备第2部分:超高压源
Super high presses forming machine--Part 2: Ultra-high pressure
hydroforminghydraulicpower
2021-01-01实施
2020-04-16发布
中华人民共和国工业和信息化部发布
JB/T13897.2—2020
目 次
前言 1范围 2规范性引用文件 3术语和定义 4技术要求.. 4.1-般要求 4.2 温升.. 4.3 冷却.. 4.4 油箱.. 4.5 液压元件 4.6 操作.. 4.7 压力控制. 4.8 连接接口.. 4.9 耐压试验 4.10 外观 4.11 液压泵与动力源, 4.12 管路
I
JB/T13897.2—2020
前言
JB/T13897《超高压充液成形设备》分为三个部分:
第1部分:通用技术条件;一第2部分:超高压源;一第3部分:模具及模架联接要求。
-
-
本部分为JB/T13897的第2部分。 本部分按照GB/T1.1一2009给出的规则起草。 本部分由中国机械工业联合会提出。 本部分由全国锻压机械标准化技术委员会(SAC/TC220)归口。 本部分起草单位:佛山市康思达液压机械有限公司、济南铸锻所检验检测科技有限公司、合肥合锻
智能装备股份有限公司、厦门瑞德利校准检测技术有限公司、深圳国技仪器有限公司、嵊州市机械行业协会。
本部分主要起草人:张悦、陈国华、马立强、李贵闪、杨图强、朱平、楼宇。 本部分为首次发布。
II
JB/T13897.2—2020
超高压充液成形设备第2部分:超高压源
1范围
JB/T13897的本部分规定了超高压充液成形设备的超高压源的术语和定义、技术要求。 本部分适用于超高压充液成形设备的液压超高压源。
2规范性引用文件
下列文件对于本文件的应用是必不可少的。凡是注日期的引用文件,仅注日期的版本适用于本文件。凡是不注日期的引用文件,其最新版本(包括所有的修改单)适用于本文件。
GB/T3766液压传动系统及其元件的通用规则和安全要求 GB/T7935 5液压元件通用技术条件 JB/T1829 锻压机械通用技术条件
3术语和定义
下列术语和定义适用于本文件。
3.1
超高压充液成形超高压源superhighpresseshydroforminghydraulicpower 由增压器、液压动力站(液压动力站由液压泵装置、油箱、蓄能器、管路及附件等组成)和液压控
制回路组成,向超高压充液成形设备提供液压能源。
4技术要求
4.1一般要求 4.1.1 液压系统应符合GB/T3766的规定。 4.1.2设计系统时,应考虑各种可能发生的事故。元件的选择、应用、配置和调节等,应首先考虑人员安全和事故发生时设备损坏最小。 4.1.3超高压液体最高压力一般不低于100MPa,并且超高压源应具备数控化控制超高压液体压力、 位移及速度的功能。 4.1.4系统中应有过压保护装置。 4.1.5设计系统时,应使元件位于易装拆之处,并必须能安全地调整与工作。 4.1.6 系统的设计与调整,必须使冲击压力最小。冲击压力和失压不应引起危险。 4.1.7 系统中所有元件必须按制造厂的规定进行操作。 4.1.8 油箱尽量装于泵体之上,以获得液体流动的最佳条件。 4.1.9动力装置基座应安装在固定于地基上的防振支架上,减少振动。 4.1.10 动力装置设计应满足紧凑性,减少占用地面空间。规划安装时,应考虑移除和组装的高度 4.1.11动力装置应加装降噪板,降低噪声声压级。 4.1.12对于在严重污染、高湿度、易燃环境及高海拔(1000m以上)、严寒地带等特殊情况下使用的
1
J8/T13897.22020
超高压藏:制造厂和设计单位与用户必商定特案场合夜用要求。 1.13超高压被体压力、创推红压力和侧向进给意度、位移的实际工作曲线:与预设菌统之间的误装应小于2%(预设总时间为T:超始与结感的各775不做考核)。 4.1.14液压红中的主放压红和倒推红试验压力应取不小于工作压力的125倍。就验压力保压时闻不应少于10ain 4.1.15液压红中的增压器翻进行题产检勤,其武验压力应取最大工作压力的1.1倍。试验压力保压时间为3m 4.1.16超高压减室器进行超产检测,其试验压力应取最大工作压力的1.1倍。试验压力保压时间为 3mine 4.2温升
设计超高压额时,须特发热减少到最小,并能得到有效的散热。抽箱内的滴溢蒸(求演压泵入口的纳温)最高不应超过60C,且不应低于15C。特殊条件下可选用其做工作液。使用热交换题和加热器时象如下
息)在使用热交换翻的地方,可采用自动热控赖置,并应分则设暨工作轴减和冷却介质的划溢点 b)在使用加热器时,其表面轻散功率不应超过0.7Wlx。
43冷知 4.3.1系统内由动力种换的内能题过热交换器滑微,热交换器安装在流遇系统上。确保大的30%装机功率的能量通过热交换器病效。 4.32首送的冷都介质为清错的软水:采用泉水:携流,柯洗水等:错基分析以帮定冷知材料。 4.3.3耗水虚取快于动力装值负荷和入口想度的整异。 4.3.4保证抽错内的油湿(欢我压系入口的轴覆)最高不应超过60C。 44油腩
超高压派中的油销应符合下达要求 &)开式油精应设置注油器、空气滤清器和就油摄:后两者的藏盈。过盗清洁度和压力摄火等应与
有关液压元件都件的技术要求相适应,且其应有足够的纳坊容量。挖油暑和空气就清器的最大压力失,应不响滚压靠的正常工作。
b)抽精内清减的微环流选应校镜:以便使摄入的气拍易于析出剂较量杂质品于沉旋。 )聚的进油口应用搭流板观其偿指随与回油口分开,如采用挡减板,它的安最设应不就碍油箱的
精洗)在正常工作情况或维修条件下,油箱须能容纳全部从系统中就入的工作满液。 )摘箱上的拍位指示解(抽标)位置,应便于检套。在签个工作周期内,均须使放位保持在安全
的工作高度上,并有足够的空间,以防止油液因热膝账丽外避和分空气。 可拆式油箱整板的用边,须能防止激,的污油波直提进入油箱,在整板上组装液压元件时
益极要有足够的顾度,并应生意减少结构上产生的额动导操产。 )进入油领盖板的管路均须采取有效密射措送。 1)轴错的底部应高于地面150以上,抽箱底板的形状应便子排效拌全部油液。 1)根据祝在缺特整上设置必要的摘洗孔。 )回抽替略的终应在最低波面以下。 1)油箱内衰面上涂敏的膝料,须与使用的工作油减相适应;润箱内表面不养题涂料时,须采取其
防舒措施(但不许污染工作油液)。
2
JB/T13897.2—2020
4.5液压元件
4.5.1液压元件应符合GB/T7935的规定。当采用插装或叠加的液压元件时,在执行液压元件与它相应的流量控制元件之间,一般应设置一个方便的测试口。在出口节流系统中,有关执行元件进口处一般应设置一个方便的测试口。 4.5.2安全阀(包括作安全阀用的溢流阀)的开启压力一般不应大于额定压力的1.1倍,工作应灵敏、 可靠。为防止随意调压引起事故,须设有防护措施。 4.5.3调压阀的技术要求应符合有关标准的规定,并须满足液压机调压范围的要求,与压力继电器配合调压者,其重复精度应符合设计的规定。 4.5.4以单向阀和液压系统密闭性保压的液压机,其保压性能应符合规定,有特殊保压要求者,应在合同或协议中注明。 4.5.5支承阀的支承性能应符合设计的要求。 4.5.6压力表开关关闭时须能完全截止。装有阻尼垫圈或阻尼装置者应灵敏、可靠。 4.5.7 蓄能器的工作压力和容量应符合标准和设计要求。 4.5.8 压力表的量程一般应为额定压力的1.5倍~2倍。 4.5.9 增压器、超高压液室和超高压管道应用超声检测仪进行检验。 4.6操作 4.6.1 动力装置和相关电器柜应配备互连线路。 4.6.2开关柜应提供包含所有操作及显示要素的在操作平台,并能够单独安装。 4.7压力控制 4.7.1 高压泵需安装手动压力调节器;如果有需要可安装遥控电动调节器。 4.7.2为保证压力安全,液压系统应设置足够流量的安全阀,也可在泵体上安装泄压阀。 4.8连接接口
超高压源与各系统、设备、附件的连接接口应有通用性,并具有方便、可靠、快速的能力。各相关系统和设备的接口通径及接头标准与超高压源相一致。 4.9耐压试验 4.9.1承受液压的铸铁、铸钢和焊接的压力容器,其材质和焊缝应符合技术文件的规定,并须在装配前做耐压试验。锻造的压力容器必要时也应做耐压试验。 4.9.2自制液压元件的耐压试验压力和保压时间,应符合相关液压元件技术文件的规定。 4.9.3自制液压缸类压力容器应进行耐压试验,保压不少于10min,不应有渗漏、永久变形及损坏。 耐压试验压力应符合下列要求:
a)当额定压力小于20MPa时,耐压试验压力应为其1.5倍; b)当额定压力大于或等于20MPa时,耐压试验压力应为其1.25倍。
4.9.4调节主液压缸至最大工作压力的1.25倍,保压10min,不应有渗漏、永久变形及损坏。 4.9.5调节压边缸、侧推缸至最大工作压力的1.25倍,保压10min,不应有渗漏、永久变形及损坏。 4.9.6调节增压器至最大工作压力的1.1倍,保压3min,试验前后测量增压器缸筒外径中段前后尺寸偏差,应符合技术文件的要求。 4.9.7 调节超高压液室和超高压管至最大工作压力的1.1倍,保压3min,不应有渗漏、永久变形及损坏。
3
JB/T13897.2—2020
4.10外观 4.10.1外表面不应有图样上未规定的凸起、凹陷、粗糙不平和其他损伤。 4.10.2结合面的边缘应整齐匀称,不应有明显的错位,门、盖与结合面不应有明显的缝隙。 4.10.3外露的焊缝应修整平直、均匀。 4.10.4液压管路、润滑管路和电气线路等沿外廓安装时,应排列整齐。 4.10.5 沉头螺钉不应凸出零件表面,其头部与沉孔之间不应有明显的偏心。定位销应略凸出零件表面。 螺栓尾端应凸出螺母,但凸出部分不应过长和参差不齐。 4.10.6 :涂漆要求应符合JB/T1829的规定。 4.10.7标牌、商标等应固定在液压机的明显位置。各种标牌的固定位置应正确、牢固、平直、整齐,并应清晰、耐久。 4.11 液压泵与动力源 4.11.1联轴器的型式与安装要求必须符合液压泵和原动机制造厂的规定。 4.11.2液压泵与原动机的安装底座必须具有足够的刚性,以保证两者运转时始终同轴。 4.11.3外露的旋转轴和联轴器必须有防护罩。 4.12管路 4.12.1液压泵进油管路的进油压力与其他条件均应符合泵制造厂的规定。进油管路应尽量短而直,避免断面突变。 4.12.2 进油管路、滤油器不应吸入空气,并且不应有聚集空气的死角。