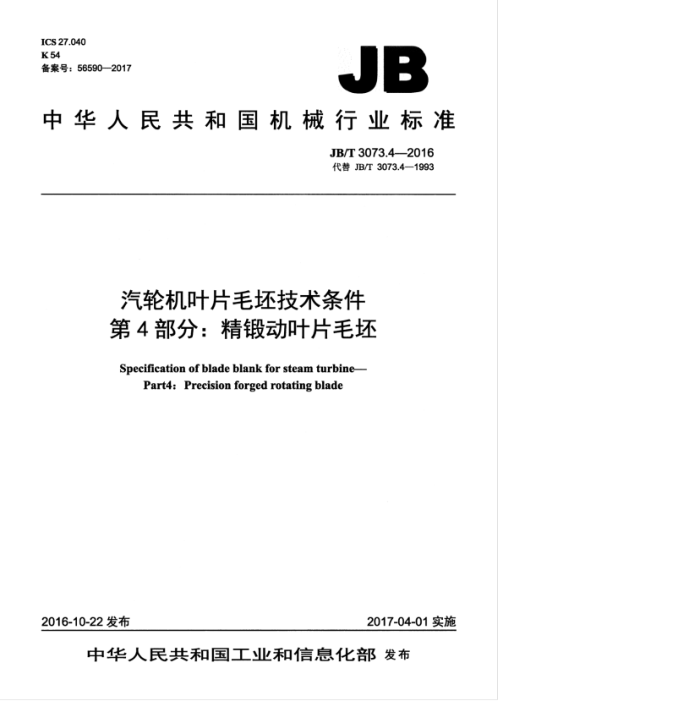
ICS27.040 K 54 备案号:56590—2017
JB
中华人民共和国机械行业标准
JB/T3073.4-2016 代替JB/T3073.4—1993
汽轮机叶片毛技术条件第4部分:精锻动叶片毛坏
Specification of blade blank for steam turbine
Part4: Precision forged rotating blade
2017-04-01实施
2016-10-22发布
中华人民共和国工业和信息化部发布
JB/T3073.42016
目 次
前言 1 范围 2规范性引用文件 3技术要求
二
3.1 原材料。 3.2 毛坏技术要求..
2
4试验方法.
二
验收要求. 标记、质量证明书和包装 6.1 标记 6.2 质量证明书 6.3 包装.
S 6
S
1
7 1
表1 化学成分. 表2非金属夹杂物表3热处理制度. 表4力学性能. 表5试验方法. 表6叶型型线部分公差
+
2
*3
4
6
JB/T3073.4—2016
前言
JB/T3073《汽轮机叶片毛坏技术条件》分为五个部分:
第1部分:模锻静叶片毛坏:一第2部分:模锻动叶片毛坏:一第3部分:热轧(锻)静叶片毛坏:
一第4部分:精锻动叶片毛坏;第5部分:汽轮机用铸造静叶片技术条件。
本部分为JB/T3073的第4部分。 本部分按照GB/T1.1一2009给出的规则起草。 本部分代替JB/T3073.4一1993《汽轮机精锻动叶片技术条件》,与JB/T3073.4一1993相比主要
技术变化如下:
将本部分名称改为汽轮机叶片毛坏技术条件第4部分:精锻动叶片毛坏”:调整了规范性引用文件(见第2章);增加了14Cr12Ni3Mo2VN、05Cr17Ni4Cu4Nb两种叶片材料牌号(见表1):更改了非金属夹杂物检验级别的要求(见3.1.4,1993年版的3.4.1);增加了对原材料晶粒度、6铁素体的检验要求(见3.1.5): -增加了叶片叶身精锻面的表面检查要求(见5.3):取消了JB/T3073.4一1993中第5章。
本部分由中国机械工业联合会提出。 本部分由全国汽轮机标准化技术委员会(SAC/TC172)归口。 本部分起草单位:南京汽轮电机(集团)有限责任公司、上海发电设备成套设计研究院。 本部分主要起草人:徐化宇、丁锐、闫勤学、王文敏、孙文健、吴根红、方崇华。 本部分所代替标准的历次版本发布情况为:
JB/T3073.4—1982-JB/T3073.41993。
Ⅱ
JB/T3073.4—2016
汽轮机叶片毛技条件第4部分:精锻动叶片毛坏
1范围
JB/T3073的本部分规定了精锻动叶片毛坏的技术要求、试验方法、验收要求、标记、质量证明书和包装。
本部分适用于汽轮机用精锻动叶片毛坏(以下简称毛坏),其他用途叶片毛坏可参照执行。
2规范性引用文件
下列文件对于本文件的应用是必不可少的。凡是注日期的引用文件,仅注日期的版本适用于本文件。凡是不注日期的引用文件,其最新版本(包括所有的修改单)适用于本文件。
GB/T222钢的成品化学成分充许偏差 GB/T223(所有部分)钢铁及合金化学分析方法 GB/T226 钢的低倍组织及缺陷酸蚀检验法 GB/T228.1金属材料拉伸试验第1部分:室温试验方法 GB/T229金属材料夏比摆锤冲击试验方法 GB/T231.1金属材料布氏硬度试验第1部分:试验方法 GB/T1979一2001结构钢低倍组织缺陷评级图 GB/T2975 钢及钢产品力学性能试验取样位置及试样制备 GB/T4162一2008锻轧钢棒超声检测方法 GB/T6394—2002 2金属平均晶粒度测定法 GB/T8732一2014汽轮机叶片用钢 GB/T10561 钢中非金属夹杂物含量的测定标准评级图显微检验法 GB/T11170 不锈钢多元素含量的测定火花放电原子发射光谱法(常规法) GB/T13298 金属显微组织检验方法 GB/T200664 钢和铁化学成分测定用试样的取样和制样方法 JB/T9628汽轮机叶片磁粉探伤方法 YB/T4402 马氏体不锈钢中6铁素体含量金相测定法
3技术要求
3.1原材料 3.1.1超声检测
叶片用原材料需进行超声检测,超声检测方法按GB/T4162一2008的规定,验收级别为A级。 3.1.2化学成分 3.1.2.1应按炉批号逐炉检验化学成分,原材料的化学成分(熔炼分析)应符合表1的规定,有特殊要求时由供需双方商定。
1
JB/T3073.4
N
表1 化学成分
(质量分数,%)
-2016
Cr Ni Mo V W Cu P s Al Ti N Nb+Ta 11.50
材料牌号
旧材料牌号
c Mn si 0.10
~ ≤0.60 ≤0.6 1 ≤0.60 0.15
≤0.30 ≤0.030 ≤0.020
12Cr13
1Cr13
13.50 12.00
0.16 ~ ≤0.60 ≤0.60 ~ ≤0.60 0.24
20Cr13
2Cr13
≤0.30 ≤0.030 ≤0.020
14.00 10.00
0.11 ~ ≤0.60 0.50 ~ ≤0.60 ~ ~
0.50 0.25
14Cr11MoV
1Crl1Mov
≤0.30 <0.030 ≤0.020
0.70 0.40
0.18 0.12 0.50
11.50 11.00 0.40 0.50 0.15 0.70
15Cr12WMov 1Cr12W1Mov ~ ~ ≤0.50 ~ ~ ~ ~ ~ ≤0.30 ≤0.030 ≤0.020
13.00 0.80 0.70 0.30 1.10 15.00
0.18 0.90
3.00 ~ ≤0.030 ≤0.020 ≤0.050 ≤0.050 ≤0.050 ~ 3.70
0.15 0.35
3.80~ 4.50
05Cr17Ni4Cu4Nb OCr17Ni4Cu4Nb ≤0.055 ≤0.50 ≤1.00 ~
16.00 11.0 2.0 1.50 0.25
0.01
0.10 0.50
14Cr12Ni3Mo2VN 1Cr12Ni3Mo2VN
~ ≤0.30
≤0.15 ≤0.020 ≤0.015 ≤0.04 ≤0.02 ~
~ ~ ~
0.17 0.90
12.75 3.0 2.00 0.40
0.05
JB/T3073.4—2016
3.1.2.2成品化学成分偏差值应符合GB/T222的规定。 3.1.3低倍组织
按炉批号抽检低倍组织。原材料的横截面酸浸低倍组织应均匀,不允许有目视可见的气泡、缩孔夹杂夹渣及裂纹等冶金缺陷。一般疏松,中心疏松和偏析均不大于GB/T1979一2001中的2级。
3.1.4非金属央杂物
按炉批号抽检非金属夹杂物。各类非金属夹杂物应符合表2的规定,有特殊要求时由供需双方商定。
表2非金属夹杂物
A类(硫化物类)细系
B类(氧化物类)细系
C类(硅酸盐类)细系
D类(球状氧化物类)细系
类别级别 ≤15 3.1.5 显微组织 3.1.5.1按炉批号抽检晶粒度。原材料的平均晶粒度不得粗于GB/T6394一2002中的4级。 3.1.5.2 原材料应按照YB/T4402规定的方法检测8铁素体含量:铁素体含量最严重视场应不超过3% 3.1.6入厂复验
粗系 ≤1.0
粗系 ≤1.0
粗系 ≤1.0
粗系 ≤1.0
≤1.5
≤1.5
≤1.5
原材料按熔炼炉号逐炉进行入厂复验,经复验合格后方可投料使用。原材料入厂复验的取样部位和数量按GB/T8732—2014的规定 3.2毛坏技术要求 3.2.1化学成分
供方提供原材料的复验结果,需方必要时在毛坏上进行抽检,各次检验均应符合本标准中3.1.2的规定。化学分析按GB/T11170的规定。有异议时:则应按GB/T223仲裁分析。分析取样方法按GB/T 20066的规定。 3.2.2组批规则
毛坏应按熔炼炉号投料:不得混批。锻造后应逐件在锻件图样指定部位标刻熔炼炉号或代号
3.2.3热处理制度
毛坏锻造后应在24五内进行热处理,推荐的热处理制度见表3。
表3热处理制度
性能处理
推荐的 推荐的高温 后强度等级 推荐的淬火 推荐的回火退火制度 回火制度 (Rpo.2) (固溶、调整) (时效)
材料牌号
旧材料牌号
制度 980℃~1040℃ 660℃~770℃
制度
MPa 440
800℃~900℃ 700℃~770℃
12Cr13
1Cr13
缓冷 800℃~900℃ 700℃~770℃
油冷 950℃~1020℃ 660℃~770℃ 空、油冷
空冷
空冷
490
20Cr13
2Cr13
缓冷
空冷
空冷
3
JB/T3073.4-2016
表3热处理制度(续)
性能处理
推荐的 推荐的高温 后强度等级 推荐的痒火 推荐的回火
材料牌号
退火制度 回火制度 (Rpo.2) (固溶、调整) (时效)
旧材料牌号
制度
制度
MPa
2Cr13 800℃~900℃700℃~770℃ 590 980℃~1030℃ 640℃~720℃
20Cr13
缓冷
空冷
油冷空、油冷
空冷 700℃~750℃
800℃~900℃700℃~770℃ 490 1000℃~1050℃ 空冷缓冷
14Cr11MoV
1CrllMoV
空冷
1000℃~1030℃ 660℃700℃
590
油冷 1000℃1050℃ 680℃~740℃
空冷
590
油冷 1000℃~1050℃ 660℃700℃
空冷空冷 ≥560°℃ 空冷,二次
800℃~900℃700℃~770℃
15Cr12WMoV 1Cr12W1MoV
缓冷 860℃~930℃650℃~750℃
空冷
635
油冷 990℃~1030℃
14Cr12Ni3Mo2VN1Cr12Ni3Mo2VN
760
缓冷
空冷
油冷
固溶1025℃~1055℃ 645℃~655℃
590
空、油冷固溶1025℃~1055℃ 600℃~610℃
空冷
740℃~850℃650℃~680℃
05Cr17Ni4Cu4Nb0Cr17Ni4Cu4Nb
760
空、油冷+调整 810℃~820℃ 565℃~575℃ 空、油冷
缓冷
空冷
空冷
890
空冷
3.2.4校正与去应力
经性能热处理后,当毛坏变形超出图样的要求时可进行冷、热校正,冷校正后需进行去应力热处理:热校正温度和去应力退火温度应比原回火温度低30℃~50℃。 3.2.5 5力学性能 3.2.5.1 毛坏最终热处理后应逐件进行硬度测试,其硬度值应符合表4的规定。
表4力学性能
旧材料牌号 类别 Rpo2/MPa R./MPa A/% Z/% KV/J 硬度HBW 1Cr13
材料牌号 12Cr13 20Cr13
≥440 ≥490 ≥590 ≥490 ≥590 ≥590 ≥635
≥620 ≥20 ≥60 ≥35 192~241 ≥665 ≥16 ≥50 ≥27 212~262 ≥735 ≥15 ≥50 ≥27 229~277 ≥685 ≥16 ≥56 ≥27 212~262 ≥735 ≥15 ≥50 ≥27 229~277 ≥735 ≥15 V45 ≥27 229~277 ≥785 ≥15 ≥45 ≥27 248~293
1 Ⅱ I Ⅱ I Ⅱ I ≥590~800 ≥900 ≥16 55
2Cr13
14Cr11MoV
1CrllMoV
15Cr12WMoV
1Cr12W1MoV
262~302 293~341 277~321
05Cr17Ni4Cu4Nb OCr17Ni4Cu4Nb I ≥890~980 ≥950~1020 ≥16 ≥55
亚 ≥755~890 ≥890~1030 ≥16 ≥55
Rpo.02 ≥760 ≥1100 ≥13 ≥40 ≥54 331~363
14Cr12Ni3Mo2VN1Cr12Ni3Mo2VN
注:表中所列出的布氏硬度值范围不作验收依据,仅作为检查毛坏热处理均匀性是否送验力学性能以及选取力学性
能试样的依据。
4