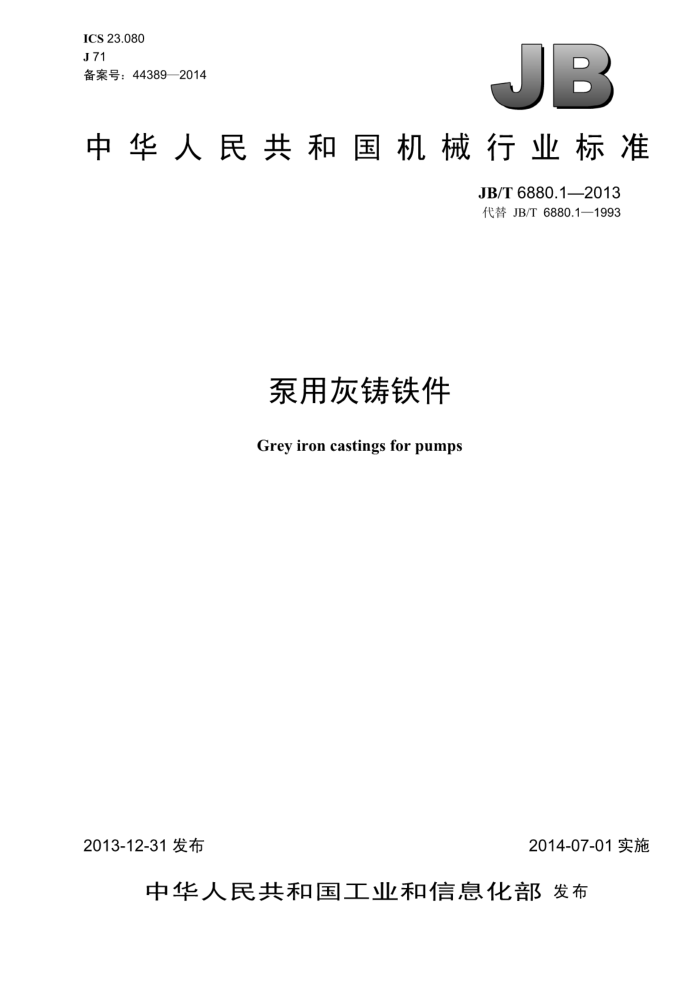
ICS 23.080 J71 备案号:44389—2014
JB
中华人民共和国机械行业标准
JB/T6880.1—2013 代替JB/T6880.1—1993
泵用灰铸铁件 Greyiron castingsforpumps
2013-12-31 发布
2014-07-01实施
中华人民共和国工业和信息化部发布
JB/T6880.1—2013
目 次
前言
范围. 规范性引用文件术语和定义牌号... 技术要求.. 试验方法. 7 检验规则
1
3
4 5 6
铸件标志、包装和储运附录A(规范性附录)泵用灰铸铁件焊补图A.1 坡口. 表1 般部位尺寸公差,表2铸件的表面粗糙度. 表3铸造缺陷.. 表A.1 焊补方法的适用范围. 表A.2 焊丝、焊炬和氧气压力表A.3 焊条直径和焊接电流表A.4 焊条的选用表A.5 焊补通知单及焊补记录
8
f
10
JB/T6880.1—2013
前 言
本标准按照GB/T1.1一2009给出的规则起草。 本标准代替JB/T6880.1一1993《泵用灰铸铁件》,与JB/T6880.1一1993相比主要技术变化如下:
修改了范围(见第1章,1993年版的第1章); -增加了标准GB/T5116(见第2章);删除了GB/T11350(见第2章,1993年版的第2章);增加了术语和定义(见第3章)。
本标准由中国机械工业联合会提出。 本标准由全国泵标准化技术委员会(SAC/TC211)归口。 本标准起草单位:上海连成(集团)有限公司、浙江新界泵业股份有限公司、福建立松金属工业有
限公司、沈阳水泵研究所。
本标准主要起草人:宋青松、许敏田、阮庭春、栾七一、许维良、张文达、李震县。 本标准所代替标准的历次版本发布情况为:
JB/T6880.1—1993
II
JB/T6880.1—2013
泵用灰铸铁件
1范围
本标准规定了泵用灰铸铁件(以下简称铸件)的术语和定义、牌号、技术要求、试验方法、检验规则、铸件标志、包装和储运要求。
本标准适用于砂型或导热性与砂型相当的铸型中铸造、图样或其他技术文件中对补焊无特殊要求和
规定的泵用灰铸铁件,使用其他铸型铸造的泵用灰铸铁件,也可参照使用,
规范性引用文件
-
下列文件对于本文件的应用是必不可少的。凡是注日期的引用文件,仅注日期的版本适用于本文
件。凡是不注日期的引用文件,其最新版本(包括所有的修改单)适用于本文件
GB/T 5611 铸造术语 GB/T 6060.1 表面粗糙度比较样块铸造表面 GB/T 6414—1999 铸件尺寸公差与机械加工余量 GB/T9439—2010 灰铸铁件 GB/T11351—1989 铸件重量公差 JB/T 5413 混流泵、轴流泵开式叶片验收技术条件 JB/T 6879 离心泵铸件过流部位尺寸公差
3 术语和定义
GB/T5611界定的以及下列术语和定义适用于本文件。
3.1
错型值 shiftvalue 由于合型时错位,铸件的一部分与另一部分在分型面处相互错开的差值。
4牌号
铸铁牌号应符合GB/T9439一2010中第4章的规定。
5 技术要求
5.1 生产方法和化学成分
生产方法和化学成分应符合GB/T9439一2010中6.1和6.2的规定。 5.2力学性能
力学性能应符合GB/T9439一2010中7.1的规定。
1
JB/T6880.1—2013
5.3金相组织
金相组织应符合GB/T9439—2010中7.2的规定。 5.4热处理
铸件宜做去应力退火处理,具体要求由供需双方商定。 5.5几何形状和尺寸
铸件的几何形状和尺寸应符合图样要求。 5.6尺寸公差 5.6.1一般部位尺寸公差,应不低于表1中的规定,公差带设置应对称于铸件基本尺寸。 5.6.2当表1规定的尺寸公差不能满足要求或由于铸件为小批、单件必须考虑经济因素时,应根据GB/T 6414一1999中表A.1或表A.2规定的工艺方法所能达到的公差等级,在图样或双方商定的协议中另行规定。 5.6.3 过流部位尺寸公差应符合如下规定:
a)离心泵铸件过流部位尺寸公差符合JB/T6879的规定; b)混流泵、轴流泵开式叶片符合JB/T5413的规定; c)特殊要求应在图样中注明。
表1一般部位尺寸公差
单位为毫米
适用部位
铸件尺寸公差
1.连接处的外缘部位a 2.小于或等于16的壁厚 1.除连接外缘以外的其余部位 2.承受流体压力且大于16的壁厚 3.不承受流体压力,尺寸在16~25的壁厚不承受流体压力且大于25的壁厚
CT 11
CT 12
CT 13 连接处的外缘部位是指泵在装配中,零件结合处外需要相互对齐的部位(包括泵与附件的连接法兰盘外缘)。
?
5.7错型值
铸件错型值应位于表1规定的尺寸公差之内。当进一步限制错型值时,应在图样上注明。 5.8机械加工余量
铸件的机械加工余量应符合GB/T6414的规定。加工余量等级,可根据表1中规定的CT12级按 GB/T6414一1999中第10章的规定选取,特殊要求时,应在图样或技术文件(包括协议)中注明。 5.9重量公差 5.9.1铸件重量公差应符合GB/T11351一1989中的规定,铸件重量公差等级应不低于MT13级 5.9.2 铸件重量上极限偏差和下极限偏差要求不相同或有特殊要求时,应在图样或协议中注明。 5.9.3 当铸件重量公差作为验收依据时,应在图样或技术文件(包括协议)中注明。 5.10 表面质量 5.10.1铸件的表面粗糙度,如果在图样上未进行标注,应不低于表2的规定。 2
JB/T6880.1—2013
表2铸件的表面粗糙度
部位铸件最大尺寸mm 表面粗糙度Ra um
过流表面 >250~1000
外观表面任何尺寸
≤250 12.5
>1 000 50
25
50
5.10.2混流泵、轴流泵开式叶片过流表面粗糙度,应符合JB/T5413的规定、 5.10.3铸件上的型砂、芯砂、芯骨、黏砂及内腔夹杂物等应清理干净。铸件表面的多肉、结疤、浇冒口应进行清除和修整,使之与母体平整圆滑过渡。 5.11缺陷 5.11.1 铸件不允许存在有影响使用性能的裂纹、冷隔、缩松等缺陷。 5.11.2缺陷尺寸的确定与计算:
a)形状呈圆形的,按径向最大尺寸确定; b)形状不呈圆形的,按式(1)计算。
D=VLB .
(1)
式中: D 缺陷尺寸,单位为毫米(mm); L 一缺陷长度方向最大尺寸,单位为毫米(mm);
一缺陷宽度方向最大尺寸,单位为毫米(mm)。
B-
5.11.3缺陷所在面尺寸的确定:
a)形状为圆形的平面,按外径计算; b)形状不是圆形的平面,按宽度方向的最大尺寸确定; c)形状为曲面的表面,如外圆表面、内圆表面、壳体流道等,圆形的按直径计算,不是圆形的按
径向的最小尺寸确定。
5.11.44 铸件非加工表面和加工后的表面,存在的铸造缺陷应不超过表3的规定。
表3铸造缺陷
缺陷所在面的同一表面上允许存在的铸造缺陷处数
缺陷尺寸
缺陷所在面
缺陷深度
缺陷间距
>250 mm~ 630 mm
≤250mm
>630 mm
最大不超过3mm,并且不超过所在面最 最深不超
1.缺陷的边缘。距离所在面的边缘,不得小
静密封面
过5mm,并
小尺寸的1/5
≤1处 ≤2处 ≤3处 于缺陷尺寸的2倍
2.缺陷的边缘至所在面的边缘距离不小于其中较大缺陷尺寸的2倍 1.缺陷的边缘。距离所在面的边缘,不得小于缺陷尺寸的2倍 2.缺陷的边缘至所在面的边缘距离不小于其中较大缺陷尺寸的2倍
加 定心、定位、配合面 最大不超过5mm,
且不超过壁
并且不超过所在面最厚的1/5 小尺寸的1/4
T 后
结合面的 传递力矩的零件(在表 不影响外观的情况下) 最大不超过2mm 最深不超面 和受冲刷的部位
过5mm,并
≤1处 ≤2处
≤3处
最大不超过6mm,上 且不超过壁并且不超过所在面最厚的1/5 小尺寸的1/5
不影响使用强度和外观的其余加工表面
3
JB/T6880.1—2013
表3铸造缺陷(续)
缺陷所在面的同一表面上允许存在的铸造缺陷处数
缺陷尺寸
缺陷间距
缺陷所在面
缺陷深度
>250mm~
≤250mm
630 mm >630 mm
1.缺陷的边缘。距离所在面的边缘,不得小于缺陷尺寸的2倍 2.缺陷的边缘至边缘距离不小于其中较大缺陷尺寸的2倍
非 承受流体压力的面 最大不超过6mm,
并且不超过所在面最 最深不超小尺寸的1/10
加 及流体的过流面 -
过5mm,并
≤1处
≤2处
≤3处
不影响使用强度和 最大不超过8mm, 且不超过壁外观的其余非加工表并且不超过所在面最厚的1/5
表面
小尺寸的1/5
面注:为获得好的外观质量,对表3规定的铸造缺陷,最好用色泽相近的填补剂进行填补,
5.11.5铸件经过精加工后,属下列类型的泵件部位,不允许残留铸造缺陷,具体部位如下:
a)动摩擦部位,如装填料处的轴套,往复泵缸体内孔等摩擦表面; b)动密封部位,如密封环、平衡盘等动密封表面; c)安全性要求高的部位,如往复泵的高压泵缸体等。
5.12特殊要求
需方对水压试验、气压试验、无损检测等有要求时,应在图样中注明或在订货协议时商定, 5.13缺陷的修补 5.13.1铸件缺陷超出表3的规定时,在能够确保使用强度和使用功能并且不因铸件的焊补而影响泵件最终精度的情况下,允许进行焊补。焊补应符合附录A的规定。 5.13.2铸件出现局部裂纹、冷隔,一般情况下不允许焊补。当铸件具有较大的焊补价值,进行焊补时,应在能够保证使用强度、使用寿命、安全可靠的情况下方可焊补。 5.13.3图样中规定不准许焊补的零件或部位,不应进行焊补。
6试验方法
6.1试棒(块)和试样
试棒(块)和试样的制备应按GB/T9439一2010中8.2的规定执行。 6.2力学性能试验
拉伸试验应按GB/T9439一2010中9.1的规定执行。 硬度的测试应按GB/T9439一2010中9.3的规定执行。
6.3化学分析
化学分析应按GB/T9439—2010中9.5的规定执行。 6.4金相检验
金相检验应按GB/T9439—2010中9.6的规定执行。
4
JB/T6880.1—2013
6.5几何形状和尺寸检验
铸件几何形状和尺寸的检验,应选择相应精度的检测量具。对不能用量具直接检验的部位或相关尺寸,可采用样板或划线检验。 6.6公称重量
铸件公称重量的确定方法应符合GB/T11351一1989中3.2的规定。 6.7表面质量
铸件的表面质量按GB/T9439—2010中7.7的规定执行。 6.8铸造缺陷
铸造缺陷的检验应按GB/T9439—2010中7.8的规定执行。 6.9特殊要求检验
特殊要求的检验,根据本标准5.12的规定,按供需双方商定的协议或有关规定进行检验。 6.10 缺陷焊补检验
铸件缺陷焊补的检验,应符合附录A的规定。
7检验规则
7.1 检验权利
检验权利按GB/T9439—2010中10.1的规定执行 7.2检验地点
检验地点按GB/T9439—2010中10.2的规定执行。 7.3取样批次的划分
取样批次的划分按GB/T9439一2010中10.3的规定执行。 7.4检验项目
检验项目为: a)拉伸试验按GB/T9439一2010中9.1的规定执行; b)硬度的测试按GB/T9439—2010中9.2的规定执行; c)金相检验按GB/T9439一2010中9.6的规定执行。
7.5试验结果的评定
试验结果的评定按GB/T9439一2010中10.5的规定执行。 7.6几何形状和尺寸检验
铸件的几何形状和尺寸按图样进行检验。首批铸件和重要件应按图样逐件进行检验。一般铸件及用保证尺寸稳定方法生产出来的铸件,可以抽检,抽检方法按供需双方商定进行。
5