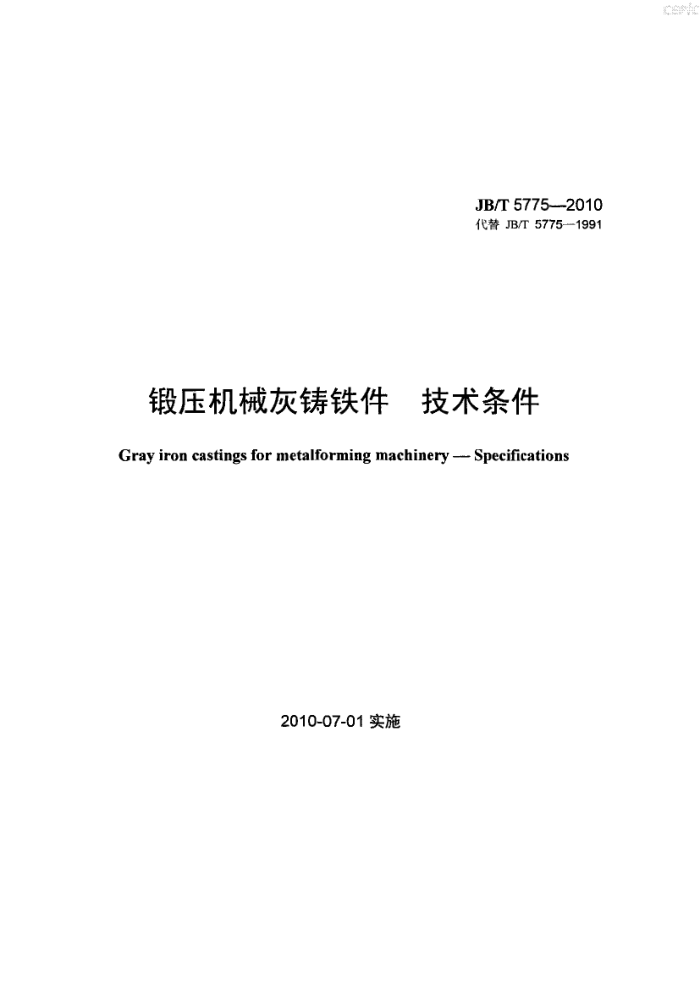
T
JB/T5775-2010 代替JB/T5775-1991
锻压机械灰铸铁件 技术条件
Gray iron castings for metalforming machinery --- Specifications
2010-07-01实施
JB/T5775—2010
目 次
前言范围.
ⅢI
1 2 规范性引用文件 3 牌号及其选择 4 技术要求
5 试验方法.. 6检验规则..
标志和质量合格证明书 8包装、运输和贮存附录A(资料性附录)灰铸铁牌号的选择 A.1 铸件壁厚和抗拉强度的关系, A.2 硬度和抗拉强度的关系, A.3 灰铸铁牌号的选择图1 单铸试棒. 图2 附铸试棒,图3 附铸试块.. 图4 A型试样图5 B型试样图6 布氏硬度试块图A.1 硬度和抗拉强度的关系表 1 各牌号的抗拉强度表 2 各牌号的抗拉强度表 3 铸件硬度分级表4 导轨表面硬度允差,表 5 铸件尺寸公差值表6 铸件尺寸公差等级,表7 错型值表8 试样尺寸. 表 A.1 铸件抗拉强度表A.2 硬度和抗拉强度间的关系.
7
10
10 10
.6
**.6
.6
11
P
.3 4
10 .12
JB/T5775—2010
前言
本标准代替JB/T5775一1991《锻压机械灰铸铁件 技术条件》。 本标准与JB/T5775一1991相比,主要变化如下:一更新了规范性引用文件; —删除了HT100牌号;
提高了铸件尺寸公差等级要求。 本标准的附录A为资料性附录。 本标准由中国机械工业联合会提出。 本标准由全国锻压机械标准化技术委员会(SAC/TC220)归口。 本标准起草单位:青岛琴达铸造有限公司、青岛正大铸造有限公司、青岛青锻锻压机械有限公司、
济南铸造锻压机械研究所。
本标准起草人:张建栋、宋敬清、房清亮、马立强、宋明正、邢吉柏、李淑君。 本标准所代替标准的历次版本发布情况:
JB/T5775-1991。
III
C
JB/T5775-—2010
锻压机械灰铸铁件技术条件
1范围
本标准规定了锻压机械灰铸铁件的牌号、技术要求、试验方法、检验规则、标志以及包装、运输和贮存,本标准适用于在砂型中或导热性与砂型相当的铸型中铸造的各种锻压机械灰铸铁件(以下简称铸
件),对用其他铸型铸造的铸件亦可参照使用。 2规范性引用文件
下列文件中的条款通过本标准的引用而成为本标准的条款。凡是注日期的引用文件,其随后所有的修改单(不包括勘误的内容)或修订版均不适用于本标准,然而,鼓励根据本标准达成协议的各方研究是否可使用这些文件的最新版本。凡是不注日期的引用文件,其最新版本适用于本标准。
GB/T223.3钢铁及合金化学分析方法二安替比林甲烷磷钼酸重量法测定磷量(GB/T223.3— 1988,neqASTME30:1980)
GB/T223.4钢铁及合金锰含量的测定电位滴定或可视滴定法 GB/T223.5钢铁酸溶硅和全硅含量的测定还原型硅钼酸盐分光光度法(GB/T223.5一2008,
ISO4829-1:1986,MOD)
GB/T223.59 钢铁及合金磷含量的测定磷钼蓝分光光度法和锑磷钼蓝分光光度法 GB/T223.61 钢铁及合金化学分析方法磷钼酸铵容量法测定磷量 GB/T223.62 钢铁及合金化学分析方法乙酸丁脂萃取光度法测定磷量 GB/T223.63 钢铁及合金化学分析方法高碘酸钠(钾)光度法测定锰量(GB/T223.63一1988,
neqASTME350:1985)
GB/T223.72钢铁及合金硫含量的测定重量法 GB/T231.1金属材料布氏硬度试验第1部分:试验方法(GB/T231.1--2009,ISO6506-1:2005,MOD) GB/T231.2金属布氏硬度试验第2部分:硬度计的检验与校准(GB/T231.2-2002,ISO6506-2:
1999,MOD)
GB/T231.3金属布氏硬度试验第3部分:标准硬度块的标定(GB/T231.3一2002,ISO6506-3: 1999,MOD)
GB/T6060.1 表面粗糙度比较样块铸造表面(GB/T6060.1--1997,eqvISO2632-3:1979) GB/T7216灰铸铁金相检验(GB/T7216—2009,ISO945-1:2008,MOD) GB/T11351铸件重量公差 JB/T7945--1999灰铸铁力学性能试验方法
3牌号及其选择 3.1牌号
本标准根据直径30mm的单铸试棒(见图1)加工成的试样测定的抗拉强度,选用灰铸铁HT150、 HT200、HT250、HT300和HT350五个牌号。 3.2牌号的选择
根据对灰铸铁抗拉强度和硬度的要求,可按照硬度和抗拉强度之间的关系以及铸件壁厚与抗拉强度的关系(见附录A)选择铸件采用的牌号。
带有导轨的铸件和有硬度要求的重要铸件,应选用HT250及其以上牌号的铸件。
-
T
JB/T57752010
4技术要求
4.1 生产方法和化学成分
生产方法和化学成分由供方自行决定,但必须达到本标准规定的牌号和抗拉强度指标。 铸件的化学成分不作为判定灰铸铁是否合格的依据,需方对化学成分有特殊要求的除外。
4.2 抗拉强度 4.2.1单铸试棒试样测定的抗拉强度
铸件的抗拉强度一般用单铸试棒加工成的试样测定。各种牌号铸件由直径30mm的单铸试棒加工成的试样来测定抗拉强度,其数值应符合表1的规定。
表1各牌号的抗拉强度
最小抗拉强度Ra
牌号 HT150 HT200 HT250 HT300 HT350
MPa 150 200 250 300 350
注:验收时,n牌号的铸件,其抗拉强度应在n~(n十100)MPa的范围内。 4.2.2 附铸试棒(块)试样测定的抗拉强度
当铸件壁厚超过20mm,而其重量又超过200kg,并有特殊要求时,经供需双方协商同意,亦可采用附铸试棒(块)加工成的试样来测定抗拉强度,其数值应符合表2的规定。
表2 各牌号的抗拉强度
最小抗拉强度Ra
MPa
铸件壁厚 mm
牌号
附铸试棒(块)
铸件 110 95 80 155 130 115 195 170 155 240 210 195 280 250 225
30mm(R15mm) 50mm(R25mm)
120 .110
>20~40 >40~80 >80~150 >150~300 >20~40 >40~80 >80~150 >150~300 >20~40 >40~80 >80~150 >150~300 >20~40 >40~80 >80~150 >150~300 >20~40 >40~80 >80~150 >150~300
HT150
100 90
170 150
HT200
140 130 -
-
210 190 一
HT250
170 160
/
250 220
-
HT300
210 190
290 260
HT350
230 210
-
注:当铸件壁厚超过300mm时,其力学性能可由供双方协商确定。
2
JB/T5775—2010
4.2.3铸件不同壁厚的抗拉强度
铸件的抗拉强度与铸件壁厚有关,同一牌号的铸件在不同的壁厚处具有不同的抗拉强度,其抗拉强度值参见表A.1。
当从铸件上切取试样测定铸件材质时,铸件的抗拉强度应符合表A.1规定的数值,经供需双方同意,可以此作为验收依据。 4.3硬度 4.3.1铸件的布氏硬度分为六级,见表3。
表3铸件硬度分级
铸件上的硬度范围
硬度分级 H155 H175 H195 H215 H235 H255
HBW 100~210 100~260 120~275 145~275 165~275 185~275
注:硬度分级是指铸件在规定测试位置上所能达到的平均硬度值,如采用其他硬度分级,则其硬度范围应当是平均
值土20HBW。
4.3.2 铸件一般不验收硬度,如需方有硬度要求,应按表3选定硬度级别,并规定测试位置。 4.3.3铸件加工面的毛坏硬度有要求时,-般不应超过255HBW。 4.3.4铸件上的导轨硬度: 4.3.4.1带有导轨的铸件,有硬度要求时,应在技术文件上规定导轨的装配硬度,并通过试验和协商,确定毛坏硬度。 4.3.4.2铸件上导轨表面的硬度允差,在导轨壁厚基本均勾条件下,在同一范围内,应符合表4的规定。 导轨壁厚不均匀或厚度(高度)大于60mm时,硬度允差可另行规定。
表4导轨表面硬度允差
导轨长度 mm ≤2000 >2 000
硬度允差 HBW 25 35
4.3.4.3导轨采用镶、贴耐磨材料时,不检验铸件上导轨基面硬度。 4.3.4.4采用表面淬火处理的导轨,淬火前的导轨表面硬度一般应不低于180HBW。若导轨淬火处的厚度超过60mm时,硬度可另行规定。淬火后的硬度要求应在图样和技术文件上规定。 4.4金相组织和热处理
采用表面淬火处理的导轨铸件对金相组织有要求时,应符合GB/T7216的规定或满足合同约定的要求。 对铸件热处理有要求时,应按有关规定或工艺文件规定进行。
3
4.5尺寸精度 4.5.1铸件尺寸公差值见表5。表中公差对称于铸件尺寸分布,即将公差的一半取正值,另一半取负值。亦可以由供需双方商定取全值,并在图样上注明或在工艺文件上规定。
表5铸件尺寸公差值
单位:mm
铸件的基本尺寸 ≤10 >10~16
公差等级CT 6 7 8 9 10 11 12 13
2
3
5 0.36 0.52 0.74 1.0 1.5 2.0 2.8 4.2 0.38 0.54 0.78 1.1 1.6 2.2 3.0 4.4
4 一
-
.
3
信车产
JB/T5775-2010
表5 铸件尺寸公差值(续)
铸件的基本尺寸 >16~~25 >25~40 >40~63 >63~100 >100~~160 >160~250 >250~400 >400~630 >630-~1000 >1000~1600 >1600~2 500 >2500~4000 >4000~6300 >6300~10000 4.5.2 铸件主要尺寸精度应按表6选定公差等级;铸件一般尺寸精度可以降低一个等级; 非加工壁厚和铸筋厚度的尺寸精度可以降低两个等级。
公差等级 CT
2
7 8
10 11 12 13
6
9
3
4
5
0.42 0.58 0.82 1.2 1.7 2.4 3.2 4.6 6 0.46 0.64 0.90 1.3 1.8 2.6 3.6 5.0 7 0.50 0.70 1.00 1.4 2.0 2.8 4.0 5.6 8 0.56 0.78 1.10 1.6 2.2 3.2 4.4 6 9 0.62 0.88 1.20 1.8 2.5 3.6 5.0 7 10 0.70 1.00 1.40 2.0 2.8 4.0 5.6 8 11 0.78 1.10 1.60 2.2 3.2 4.4 6.2 9 12 0.90 1.20 1.80 2.6 3.6 5 7 10 14 1.00 1.40 2.00 2.8 4.0 6 8 11 16
1.60 2.20 3.2 4.6 7 9 13 18
2.60 3.8 5.4 8 10 15 21
4.4 6.2 9 12 17 24
7.0 10 14 20 28
11 16 23 32
表6 铸件尺寸公差等级
公差等级 CT
生产方式成批大量生产单件小批生产
砂型手工造型
自硬砂或机器造型
9~11 11 ~ 13
6~8 9~11
4.5.3铸件主要尺寸中的加工基准面尺寸的公差值由供方自行确定,也可由供需双方协商确定。 4.6铸件重量公差要求
铸件的重量公差应符合GB/T11351的规定, 4.7外观质量 4.7.1挠曲变形
对于长铸件,在1000mm长度上,其挠曲度变形一般应不超过1.5mm,每增大1000mm,允许增加1.5mm, 但应满足切削加工要求。 4.7.2错型
铸件非加工外表面错型值应符合表7的规定。
表7错型值
单位:mm
非加工外表面错型值
铸件最大长度
≤1.0 ≤1.5 ≤2.0 ≤3.0 ≤4.0 ≤5.0
≤250 >250~630 >630~1600 >1600~4 000 >4 000~6300
>6 300
4
CR
JB/T5775—2010
4.7.3表面粗糙度
铸件非加工表面粗糙度应符合GB/T6060.1的规定。 4.8铸件清理、缺陷和修补 4.8.1清理 4.8.1.1铸件上的型砂和粘结物应清理干净。 4.8.1.2铸件的油池、油箱、油通道等部位必须仔细清理,不得留有粘砂和阻塞油路的飞边、毛刺。 4.8.1.3影响外观的非加工部位浇口、冒口和飞边、毛刺应修理平整,其偏差为-2mm, 4.8.1.4加工面上的浇口、冒口和飞边、毛刺:允许有定残留量。 4.8.2缺陷 4.8.2.1铸件不应有影响结构强度和使用性能以及外观的铸造缺陷,但允许存在深度不超过实际加工余量的铸造缺陷。 4.8.2.2导轨表面和重要配合面不应有肉眼明显易见的疏松。 4.8.2.3泵体、阀体和缸筒类铸件不应有降低耐压强度的铸造缺陷,在规定的试验压力下,不应有渗漏现象。 4.8.2.4铸件的储油部位,不应有漏油、渗油现象。 4.8.3修补
对不影响使用和外观的铸件缺陷,在保证使用质量的条件下,允许按有关规定进行修补。 4.9时效 4.9.1铸件应进行时效处理,以消除内应力。 4.9.2采用热时效处理,应按热时效有关工艺规定进行; 4.9.3对于采用其他消除应力和稳定化措施的铸件,应按相应技术要求处理。 4.10底漆
铸件非加工面,应进行除锈处理和涂防锈底漆,除锈要彻底、干净,喷刷要均匀,不应有起皱、堆积、流挂、露底等现象。 5试验方法 5.1抗拉强度试棒和试样的制备 5.1.1单铸试棒的制备
a)单铸试棒(见图1)应在干砂型或与铸件相同砂型中竖浇,同一铸型可同时浇注若干试棒,各
个试棒间的距离应不小于50mm; b)应使用浇注铸件的同一批铁水浇注:
A
A
50 030*a
50
图1单铸试棒
5
T
JB/T5775-2010 代替JB/T5775-1991
锻压机械灰铸铁件 技术条件
Gray iron castings for metalforming machinery --- Specifications
2010-07-01实施
JB/T5775—2010
目 次
前言范围.
ⅢI
1 2 规范性引用文件 3 牌号及其选择 4 技术要求
5 试验方法.. 6检验规则..
标志和质量合格证明书 8包装、运输和贮存附录A(资料性附录)灰铸铁牌号的选择 A.1 铸件壁厚和抗拉强度的关系, A.2 硬度和抗拉强度的关系, A.3 灰铸铁牌号的选择图1 单铸试棒. 图2 附铸试棒,图3 附铸试块.. 图4 A型试样图5 B型试样图6 布氏硬度试块图A.1 硬度和抗拉强度的关系表 1 各牌号的抗拉强度表 2 各牌号的抗拉强度表 3 铸件硬度分级表4 导轨表面硬度允差,表 5 铸件尺寸公差值表6 铸件尺寸公差等级,表7 错型值表8 试样尺寸. 表 A.1 铸件抗拉强度表A.2 硬度和抗拉强度间的关系.
7
10
10 10
.6
**.6
.6
11
P
.3 4
10 .12
JB/T5775—2010
前言
本标准代替JB/T5775一1991《锻压机械灰铸铁件 技术条件》。 本标准与JB/T5775一1991相比,主要变化如下:一更新了规范性引用文件; —删除了HT100牌号;
提高了铸件尺寸公差等级要求。 本标准的附录A为资料性附录。 本标准由中国机械工业联合会提出。 本标准由全国锻压机械标准化技术委员会(SAC/TC220)归口。 本标准起草单位:青岛琴达铸造有限公司、青岛正大铸造有限公司、青岛青锻锻压机械有限公司、
济南铸造锻压机械研究所。
本标准起草人:张建栋、宋敬清、房清亮、马立强、宋明正、邢吉柏、李淑君。 本标准所代替标准的历次版本发布情况:
JB/T5775-1991。
III
C
JB/T5775-—2010
锻压机械灰铸铁件技术条件
1范围
本标准规定了锻压机械灰铸铁件的牌号、技术要求、试验方法、检验规则、标志以及包装、运输和贮存,本标准适用于在砂型中或导热性与砂型相当的铸型中铸造的各种锻压机械灰铸铁件(以下简称铸
件),对用其他铸型铸造的铸件亦可参照使用。 2规范性引用文件
下列文件中的条款通过本标准的引用而成为本标准的条款。凡是注日期的引用文件,其随后所有的修改单(不包括勘误的内容)或修订版均不适用于本标准,然而,鼓励根据本标准达成协议的各方研究是否可使用这些文件的最新版本。凡是不注日期的引用文件,其最新版本适用于本标准。
GB/T223.3钢铁及合金化学分析方法二安替比林甲烷磷钼酸重量法测定磷量(GB/T223.3— 1988,neqASTME30:1980)
GB/T223.4钢铁及合金锰含量的测定电位滴定或可视滴定法 GB/T223.5钢铁酸溶硅和全硅含量的测定还原型硅钼酸盐分光光度法(GB/T223.5一2008,
ISO4829-1:1986,MOD)
GB/T223.59 钢铁及合金磷含量的测定磷钼蓝分光光度法和锑磷钼蓝分光光度法 GB/T223.61 钢铁及合金化学分析方法磷钼酸铵容量法测定磷量 GB/T223.62 钢铁及合金化学分析方法乙酸丁脂萃取光度法测定磷量 GB/T223.63 钢铁及合金化学分析方法高碘酸钠(钾)光度法测定锰量(GB/T223.63一1988,
neqASTME350:1985)
GB/T223.72钢铁及合金硫含量的测定重量法 GB/T231.1金属材料布氏硬度试验第1部分:试验方法(GB/T231.1--2009,ISO6506-1:2005,MOD) GB/T231.2金属布氏硬度试验第2部分:硬度计的检验与校准(GB/T231.2-2002,ISO6506-2:
1999,MOD)
GB/T231.3金属布氏硬度试验第3部分:标准硬度块的标定(GB/T231.3一2002,ISO6506-3: 1999,MOD)
GB/T6060.1 表面粗糙度比较样块铸造表面(GB/T6060.1--1997,eqvISO2632-3:1979) GB/T7216灰铸铁金相检验(GB/T7216—2009,ISO945-1:2008,MOD) GB/T11351铸件重量公差 JB/T7945--1999灰铸铁力学性能试验方法
3牌号及其选择 3.1牌号
本标准根据直径30mm的单铸试棒(见图1)加工成的试样测定的抗拉强度,选用灰铸铁HT150、 HT200、HT250、HT300和HT350五个牌号。 3.2牌号的选择
根据对灰铸铁抗拉强度和硬度的要求,可按照硬度和抗拉强度之间的关系以及铸件壁厚与抗拉强度的关系(见附录A)选择铸件采用的牌号。
带有导轨的铸件和有硬度要求的重要铸件,应选用HT250及其以上牌号的铸件。
-
T
JB/T57752010
4技术要求
4.1 生产方法和化学成分
生产方法和化学成分由供方自行决定,但必须达到本标准规定的牌号和抗拉强度指标。 铸件的化学成分不作为判定灰铸铁是否合格的依据,需方对化学成分有特殊要求的除外。
4.2 抗拉强度 4.2.1单铸试棒试样测定的抗拉强度
铸件的抗拉强度一般用单铸试棒加工成的试样测定。各种牌号铸件由直径30mm的单铸试棒加工成的试样来测定抗拉强度,其数值应符合表1的规定。
表1各牌号的抗拉强度
最小抗拉强度Ra
牌号 HT150 HT200 HT250 HT300 HT350
MPa 150 200 250 300 350
注:验收时,n牌号的铸件,其抗拉强度应在n~(n十100)MPa的范围内。 4.2.2 附铸试棒(块)试样测定的抗拉强度
当铸件壁厚超过20mm,而其重量又超过200kg,并有特殊要求时,经供需双方协商同意,亦可采用附铸试棒(块)加工成的试样来测定抗拉强度,其数值应符合表2的规定。
表2 各牌号的抗拉强度
最小抗拉强度Ra
MPa
铸件壁厚 mm
牌号
附铸试棒(块)
铸件 110 95 80 155 130 115 195 170 155 240 210 195 280 250 225
30mm(R15mm) 50mm(R25mm)
120 .110
>20~40 >40~80 >80~150 >150~300 >20~40 >40~80 >80~150 >150~300 >20~40 >40~80 >80~150 >150~300 >20~40 >40~80 >80~150 >150~300 >20~40 >40~80 >80~150 >150~300
HT150
100 90
170 150
HT200
140 130 -
-
210 190 一
HT250
170 160
/
250 220
-
HT300
210 190
290 260
HT350
230 210
-
注:当铸件壁厚超过300mm时,其力学性能可由供双方协商确定。
2
JB/T5775—2010
4.2.3铸件不同壁厚的抗拉强度
铸件的抗拉强度与铸件壁厚有关,同一牌号的铸件在不同的壁厚处具有不同的抗拉强度,其抗拉强度值参见表A.1。
当从铸件上切取试样测定铸件材质时,铸件的抗拉强度应符合表A.1规定的数值,经供需双方同意,可以此作为验收依据。 4.3硬度 4.3.1铸件的布氏硬度分为六级,见表3。
表3铸件硬度分级
铸件上的硬度范围
硬度分级 H155 H175 H195 H215 H235 H255
HBW 100~210 100~260 120~275 145~275 165~275 185~275
注:硬度分级是指铸件在规定测试位置上所能达到的平均硬度值,如采用其他硬度分级,则其硬度范围应当是平均
值土20HBW。
4.3.2 铸件一般不验收硬度,如需方有硬度要求,应按表3选定硬度级别,并规定测试位置。 4.3.3铸件加工面的毛坏硬度有要求时,-般不应超过255HBW。 4.3.4铸件上的导轨硬度: 4.3.4.1带有导轨的铸件,有硬度要求时,应在技术文件上规定导轨的装配硬度,并通过试验和协商,确定毛坏硬度。 4.3.4.2铸件上导轨表面的硬度允差,在导轨壁厚基本均勾条件下,在同一范围内,应符合表4的规定。 导轨壁厚不均匀或厚度(高度)大于60mm时,硬度允差可另行规定。
表4导轨表面硬度允差
导轨长度 mm ≤2000 >2 000
硬度允差 HBW 25 35
4.3.4.3导轨采用镶、贴耐磨材料时,不检验铸件上导轨基面硬度。 4.3.4.4采用表面淬火处理的导轨,淬火前的导轨表面硬度一般应不低于180HBW。若导轨淬火处的厚度超过60mm时,硬度可另行规定。淬火后的硬度要求应在图样和技术文件上规定。 4.4金相组织和热处理
采用表面淬火处理的导轨铸件对金相组织有要求时,应符合GB/T7216的规定或满足合同约定的要求。 对铸件热处理有要求时,应按有关规定或工艺文件规定进行。
3
4.5尺寸精度 4.5.1铸件尺寸公差值见表5。表中公差对称于铸件尺寸分布,即将公差的一半取正值,另一半取负值。亦可以由供需双方商定取全值,并在图样上注明或在工艺文件上规定。
表5铸件尺寸公差值
单位:mm
铸件的基本尺寸 ≤10 >10~16
公差等级CT 6 7 8 9 10 11 12 13
2
3
5 0.36 0.52 0.74 1.0 1.5 2.0 2.8 4.2 0.38 0.54 0.78 1.1 1.6 2.2 3.0 4.4
4 一
-
.
3
信车产
JB/T5775-2010
表5 铸件尺寸公差值(续)
铸件的基本尺寸 >16~~25 >25~40 >40~63 >63~100 >100~~160 >160~250 >250~400 >400~630 >630-~1000 >1000~1600 >1600~2 500 >2500~4000 >4000~6300 >6300~10000 4.5.2 铸件主要尺寸精度应按表6选定公差等级;铸件一般尺寸精度可以降低一个等级; 非加工壁厚和铸筋厚度的尺寸精度可以降低两个等级。
公差等级 CT
2
7 8
10 11 12 13
6
9
3
4
5
0.42 0.58 0.82 1.2 1.7 2.4 3.2 4.6 6 0.46 0.64 0.90 1.3 1.8 2.6 3.6 5.0 7 0.50 0.70 1.00 1.4 2.0 2.8 4.0 5.6 8 0.56 0.78 1.10 1.6 2.2 3.2 4.4 6 9 0.62 0.88 1.20 1.8 2.5 3.6 5.0 7 10 0.70 1.00 1.40 2.0 2.8 4.0 5.6 8 11 0.78 1.10 1.60 2.2 3.2 4.4 6.2 9 12 0.90 1.20 1.80 2.6 3.6 5 7 10 14 1.00 1.40 2.00 2.8 4.0 6 8 11 16
1.60 2.20 3.2 4.6 7 9 13 18
2.60 3.8 5.4 8 10 15 21
4.4 6.2 9 12 17 24
7.0 10 14 20 28
11 16 23 32
表6 铸件尺寸公差等级
公差等级 CT
生产方式成批大量生产单件小批生产
砂型手工造型
自硬砂或机器造型
9~11 11 ~ 13
6~8 9~11
4.5.3铸件主要尺寸中的加工基准面尺寸的公差值由供方自行确定,也可由供需双方协商确定。 4.6铸件重量公差要求
铸件的重量公差应符合GB/T11351的规定, 4.7外观质量 4.7.1挠曲变形
对于长铸件,在1000mm长度上,其挠曲度变形一般应不超过1.5mm,每增大1000mm,允许增加1.5mm, 但应满足切削加工要求。 4.7.2错型
铸件非加工外表面错型值应符合表7的规定。
表7错型值
单位:mm
非加工外表面错型值
铸件最大长度
≤1.0 ≤1.5 ≤2.0 ≤3.0 ≤4.0 ≤5.0
≤250 >250~630 >630~1600 >1600~4 000 >4 000~6300
>6 300
4
CR
JB/T5775—2010
4.7.3表面粗糙度
铸件非加工表面粗糙度应符合GB/T6060.1的规定。 4.8铸件清理、缺陷和修补 4.8.1清理 4.8.1.1铸件上的型砂和粘结物应清理干净。 4.8.1.2铸件的油池、油箱、油通道等部位必须仔细清理,不得留有粘砂和阻塞油路的飞边、毛刺。 4.8.1.3影响外观的非加工部位浇口、冒口和飞边、毛刺应修理平整,其偏差为-2mm, 4.8.1.4加工面上的浇口、冒口和飞边、毛刺:允许有定残留量。 4.8.2缺陷 4.8.2.1铸件不应有影响结构强度和使用性能以及外观的铸造缺陷,但允许存在深度不超过实际加工余量的铸造缺陷。 4.8.2.2导轨表面和重要配合面不应有肉眼明显易见的疏松。 4.8.2.3泵体、阀体和缸筒类铸件不应有降低耐压强度的铸造缺陷,在规定的试验压力下,不应有渗漏现象。 4.8.2.4铸件的储油部位,不应有漏油、渗油现象。 4.8.3修补
对不影响使用和外观的铸件缺陷,在保证使用质量的条件下,允许按有关规定进行修补。 4.9时效 4.9.1铸件应进行时效处理,以消除内应力。 4.9.2采用热时效处理,应按热时效有关工艺规定进行; 4.9.3对于采用其他消除应力和稳定化措施的铸件,应按相应技术要求处理。 4.10底漆
铸件非加工面,应进行除锈处理和涂防锈底漆,除锈要彻底、干净,喷刷要均匀,不应有起皱、堆积、流挂、露底等现象。 5试验方法 5.1抗拉强度试棒和试样的制备 5.1.1单铸试棒的制备
a)单铸试棒(见图1)应在干砂型或与铸件相同砂型中竖浇,同一铸型可同时浇注若干试棒,各
个试棒间的距离应不小于50mm; b)应使用浇注铸件的同一批铁水浇注:
A
A
50 030*a
50
图1单铸试棒
5