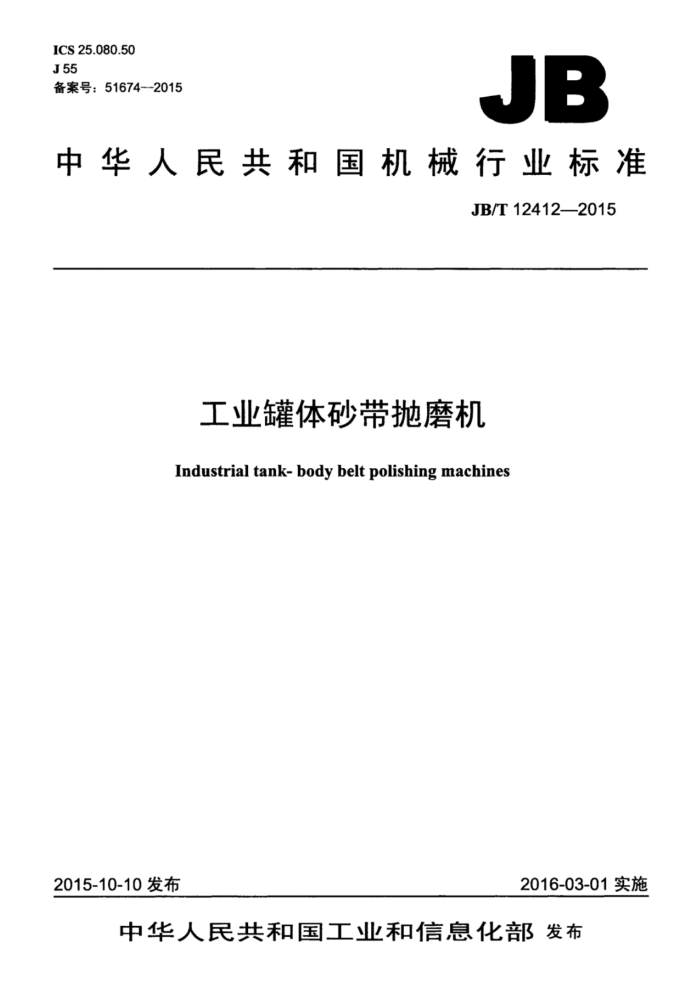
ICS25.080.50 J55 备案号:51674-2015
JB
中华人民共和国机械行业标准
JB/T12412—2015
工业罐体砂带抛磨机
Industrial tank- body belt polishing machines
2015-10-10发布
2016-03-01实施
中华人民共和国工业和信息化部发布
JB/T12412—2015
目 次
前言 1范围 2规范性引用文件 3型号及参数 3..1型号.. 3.2参数 4结构示例... 5技术要求
II
5.1外观... 5.2加工和装配质量 5.3附件和工具
6安全卫生
机床试验方法.
7
7.1 温度和温升试验 7.2 空运转功率试验 7.3 机床功能试验 7.4 机床空运转试验 7.5 机床负荷试验(抽查) 7.6 磨削压力
8检验规则. 8.1 检验分类 8.2出厂检验 8.3琴 型式检验 8.4精度检验项目 9随机文件、包装、标志、运输和贮存图1机床结构示例
表1主要参数表2几何精度检验. 表3机床工作精度.
JB/T12412—2015
前 言
本标准按照GB/T1.1一2009给出的规则起草。 本标准由中国机械工业联合会提出。 本标准由全国金属切削机床标准化技术委员会(SAC/TC22》归口本标准起草单位:重庆三磨海达磨床有限公司,重庆大学机械传动国家重点实验室。 本标准主要起草人:杨俊峰、黄云、李伟、李平、马昌林、罗小龙。 本标准为首次发布。
II
JB/T12412---2015
工业罐体砂带抛磨机
1范围
本标准规定了工业罐体砂带抛磨机的参数、制造与验收技术要求,几何精度和工作精度的要求和检验方法及相应的允差。
本标准适用于最大加工直径1000mm8000mm的工业罐体砂带抛磨机(以下简称机床)。
2规范性引用文件
下列文件对于本文件的应用是必不可少的。凡是注日期的引用文件,仅注日期的版本适用于本文件。 凡是不注日期的引用文件,其最新版本(包括所有的修改单)适用于本文件。
GB/T191—2008包装储运图示标志 GB/T3167一2015金属切削机床操作指示图形符号 GB5226.1一2008机械电气安全机械电气设备第1部分:通用技术条件 GB/T7932--2003气动系统通用技术条件 GB/T9239.1--2006机械振动恒态(刚性)转子平衡品质要求第1部分:规范与平衡允差的
检验
GB/T15375-2008金属切削机床型号编制方法 GB15760一2004金属切削机床安全防护通用技术条件 GB/T16769一2008金属切削机床噪声声压级测量方法 GB/T17421.1-1998机床检验通则第1部分:在无负荷或精加工条件下机床的几何精度 GB/T25373一2010金属切削机床装配通用技术条件 JB/T8356.1-1996 机床包装技术条件 JB/T8356.2—1996机床包装箱
3型号及参数
3.1型号
机床型号编制应符合GB/T15375-2008的规定。 3.2参数
机床的主要参数按表1的规定。
表1主要参数
参数值 ≥±1000$4000 04000~08000
序号 1 2
主要参数名称加工工件直径 mm 加工工件高度 mm 工件最大重量kg
<$1000 ≤700 ≤300
≤1800 ≤3000
≤2500 ≤8000
3
1
JB/T12412—2015
4结构示例
机床的结构示例如图1所示。
说明:
一大立柱: 4磨头 2横梁:
1
5-工件
小立柱: 6 转台。
图1机床结构示例
5技术要求
5.1外观 5.1.1机床外观表面不应有未规定的凸起、凹陷、粗糙不平和其他缺陷。 5.1.2机床的防护罩及防护装置表面应平整、匀称,不应有翘曲、凹陷。 5.1.3机床外露零件表面不应有磕碰、锈蚀,螺钉、铆钉、销子端部不应有扭伤、锤伤等缺陷。 5.1.4金属手轮轮缘和操纵手柄应有涂层防锈。电镀件、发黑件色调应一致,防护层不应有褪色,脱落现象。 5.1.5机床涂漆颜色及光泽应均匀一致,涂漆层应平整,涂漆表面不应有起泡及脱落等缺陷。机床可拆卸的装配结合面的接缝处,在涂漆以后,应切开,切开时不应扯破边缘。 5.1.6机床的各种信息标志及标牌应在机床明显位置平整固定,清晰耐久:不歪斜。 5.1.7机床电气、液压、润滑及冷却等的管道的外露部分,应布置紧凑、排列整齐,必要时应用管夹固定,软管不应扭曲、折叠及断裂。 5.2加工和装配质量 5.2.1机床的操作指示形象化符号应符合GB/T31672015的规定。 5.2.2机床进给导轨与其相配件的接触面,应符合GB/T25373一2010的规定。
2
JB/T12412-—2015
5.2.3磨头橡胶轮应与装在其轴上的其他旋转件(如带轮等)一起进行动平衡,平衡品质等级不得低于GB9239.1一2006规定的G1.0级要求。 5.2.4横梁,立柱,旋转工作台等重要零,部件,应做消除应力处理。 5.2.5各进给滑动导轨副、回转运动副应采用相应的耐磨措施。 5.2.6各导轨副的运动应勾速,平稳,不应出现爬行,卡死等现象。 5.2.7横梁的悬伸垂直度应≤2mm/m 5.2.8横梁的水平侧摆度(磨头工作状态)应≤1.0mm/me 5.2.9当横梁处于中间位置时,应保证横梁两端水平高度差≤5mm 5.2.10转台的径向跳动应<1mm,端面跳动应<1.5mmle 5.2.11转台安装后,旋转工作台,其水平度误差应≤3mm/m(转台直径)。 5.2.12转台安装后,工作台与磨头中心的重合度误差应≤5mm。 5.3附件和工具 5.3.1机床应配备能保证基本性能的附件和工具,具体附件和工具由设计根据机床的结构特点规定。 5.3.2根据用户的要求,按协议(或合同)的规定提供特殊附件。
6安全卫生
6.11 磨头处应设防护装置,防护装置打开时,主电源应断开。 6.2# 操作位置应配有紧急停止按钮。 6.3砂带断裂时,磨头电动机和进给电动机应停止工作。 6.4转台应设有防护装置。 6.5机械、电气行程终端应有可靠的极限保护措施。 6.6升降移动部件应有防坠落装置。 6.7机床磨削易燃易爆的材质工件时,应采取相应措施。 6.8机床运转时,不应有不正常的尖叫声和不规则的冲击声。在空运转条件下,机床的噪声声压级不应超过85dB(A)。测量方法应符合GB/T167692008的规定。 6.9电气系统应符合GB5226.1—2008的规定。 6.10汽动系统应符合GB/T7932--2003的规定。 6.11机床的安全防护还应符合GB15760--2004的规定。
7机床试验方法
7.1温度和温升试验
磨头在无负荷状态下进行空运转试验,高速运转不少于1h。当轴承达到稳定温度时,在靠近轴承的外壳处测量,其温度不应超过轴承使用温度。 7.2空运转功率试验 7.2.1磨头(安装砂带)空运转功率不应大于磨头电动机指标的60% 7.2.2驱动机构电动机空运转功率不应大于额定功率的80% 7.3机床功能试验 7.3.1磨头应进行正、反转操作试验,还应进行不少于10次的进给、抬起操作试验,动作应灵活、可
3
JB/T12412—2015
靠、准确,砂带不应跑偏。 7.3.2转台应进行低、中、高速的正、反转运转试验,动作应灵活、可靠。 7.3.3小立柱、横梁应分别进行低、中、高速全行程的移动试验,动作应灵活、可靠,不应有爬行、 震动现象。 7.3.4砂带线速度及工件旋转速度的调速范围应符合设计要求,其实测值相对设计值的误差应不超出 ±5%
注:工件旋转速度选择低、中、高速进行考核。 7.3.5对机床的各种指示灯、控制按钮等进行试验,动作应灵活可靠。 7.3.6对机床的气动,润滑、冷却系统进行试验,动作应灵活。可靠。 7.4机床空运转试验 7.4.1连续空运转试验应在7.3试验之后,精度检验之前进行。 7.4.2机床在全部功能下模拟工作状态做不磨削连续空运转试验,包括机床所有功能和全部工作范围,连续空运转时间应不少于2h 7.4.3整机连续空运转过程中不应发生故障;如出现异常或故障,在查明原因进行调整或排除后,应重新开始试验。 7.5机床负荷试验(抽查)
磨头电动机达到最大功率试验。试验条件如下: a)试件:精度检验标准中用于工作精度检验的试件,或应符合技术协议要求的工件: b)工件旋转速度:高速或中速: c)压力调节:均匀地调节磨削压力,使电动机达到额定功率或设计规定的最大功率。 试验时,机床应正常运转。
7.6磨削压力 7.6.1在加工时,磨头对工件的接触压力须满足工艺要求。 7.6.2磨削压力的调整误差为工艺要求的土10%。
8检验规则
8.1检验分类
检验分为出厂检验和型式检验。 8.2出厂检验 8.2.1每台机床应经检验合格后方能出广 8.2.2出厂时应对本标准规定的5.15.2.15.2.6~5.2.96.1~6.5、6.8、7.17.37.6项目进行检验 8.2.3工作精度的试验规范由设计规定。 8.2.4工作精度检验应一次交验合格。 8.3型式检验 8.3.1有下列情况之一时,应进行型式检验
a)新产品投产: b)工艺或结构发生改变
4