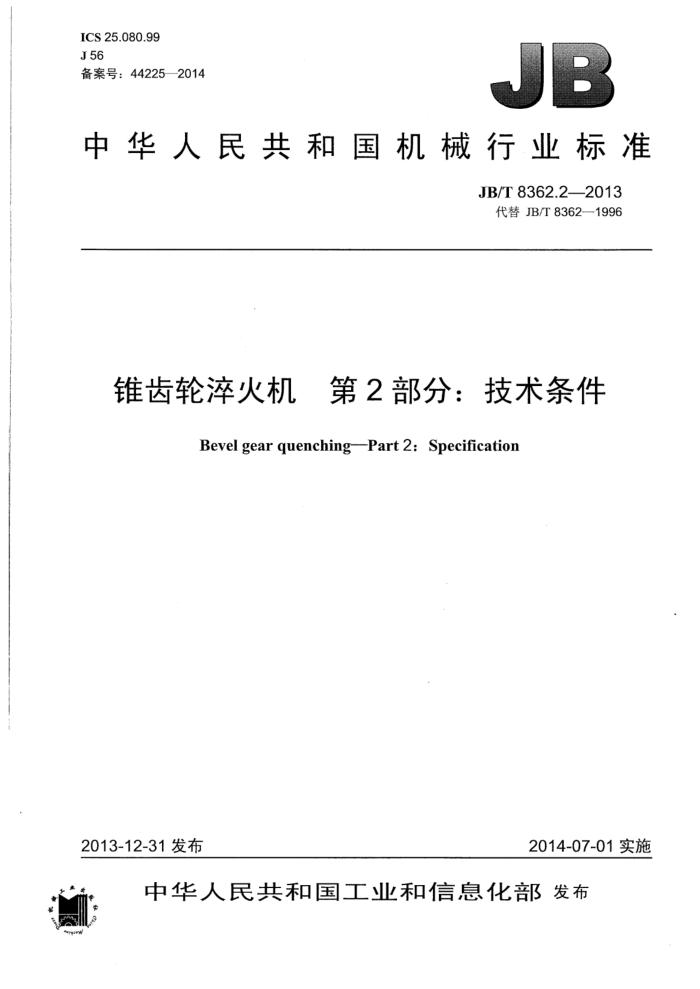
ICS25.080.99 J56 备案号:44225—2014
中华人民共和国机械行业标准
JB/T8362.22013
代替JB/T8362—1996
锥齿轮萍火机第2部分:技术条件
Bevel gear quenching--Part 2: Specification
2014-07-01实施
2013-12-31发布
中华人民共和国工业和信息化部发布
JB/T8362.2-2013
目 次
前言 1范围.. 2
1
规范性引用文件 3 技术要求 3.1 一般要求... 3.2 附件和工具. 3.3布局和外观. 3.4电气系统 3.5 液压、润滑和冷却系统 3.6 安全防护 3.7 加工和装配质量. 4检验与验收
4.1 概述. 4.2 一般要求. 4.3 外观检验. 4.4 附件和工具的检验.. 4.5 参数检验(抽查) 4.6 机床的空运转试验.. 4.7 机床的负荷试验 4.8 机床的精度检验. 4.9 其他 5 包装. 表1 错位量及贴合缝隙值表2 空运转时间表3 负荷试验参数. 表4 重复定位精度
.......
Ⅱ
JB/T 8362.2--2013
前言
JB/T8362《锥齿轮淬火机》分为以下两个部分:
第1部分:精度检验;第2部分:技术条件。
本部分为JB/T8362的第2部分。 本部分按照GB/T1.1-2009给出的规则起草。 本部分代替JB/T8362—1996《锥齿轮淬火机技术条件》,与JB/T8362-1996相比主要技术变化如
下:
引用了最新版的相关标准(见第2章,1996年版的第2章);增加了“布局和外观”(见3.3); -增加了“电气系统”(见3.4); -增加了“液压、润滑和冷却系统”(见3.5);增加了“包装”(见第5章)。
本部分由中国机械工业联合会提出。 本部分由全国金属切削机床标准化技术委员会(SAC/TC22)归口。 本部分起草单位:天津第一机床总厂、重庆机床(集团)有限责任公司、青海第二机床制造有限责
任公司。
本部分主要起草人:柴宝连、程良范、刘德全、喻可斌、李毅、颜芳。 本部分所代替标准的历次版本发布情况为:
JBn/T8362-1986.JB/T83621996.
JB/T8362.2—2013
锥齿轮淬火机第2部分:技术条件
1范围
JB/T8362的本部分规定了锥齿轮淬火机设计、制造、检验与验收的要求。 本部分适用于最大工件直径320mm1250mm锥齿轮淬火机(以下简称“机床”)。
2 规范性引用文件
下列文件对于本文件的应用是必不可少的。凡是注日期的引用文件,仅注日期的版本适用于本文件凡是不注日期的引用文件,其最新版本(包括所有的修改单)适用于本文件。
GB5226.12008机械电气安全机械电气设备第1部分:通用技术条件 GB/T 6576-2002 机床润滑系统 GB/T 9061—2006 金属切削机床通用技术条件 GB15760—2004 金属切削机床安全防护通用技术条件 GB/T16769-—2008 金属切削机床噪声声压级测量方法 GB/T23570-2009 金属切削机床焊接件通用技术条件 GB/T23572-2009 金属切削机床氵 液压系统通用技术条件 GB/T25372—2010 金属切削机床 精度分级 GB/T25373—2010 金属切削机床 装配通用技术条件 GB/T25374-2010 金属切削机床 清洁度的测量方法 GB/T25376—2010 金属切削机床 机械加工件通用技术条件 JB/T 3997—2011 金属切削机床灰铸铁件技术条件 JB/T8356.1—1996 机床包装技术条件 JB/T8356.2—1996 机床包装箱 JB/T8362.1—2013 锥齿轮淬火机 第1部分:精度检验
3技术要求
3.1一般要求
本部分是对GB/T9061—2008、GB/T23570——2009、GB/T25373-2010、GB/T25376—2010等标准的具体化和补充,机床的设计与制造除应符合本部分的规定外,还应符合上述标准中未经本部分具体化的其他技术要求。 3.2附件和工具 3.2.1应随行供应安装机床用的机床垫铁、地脚螺栓各一套。 3.2.2扩大机床性能的特殊附件,可根据用户要求按协议供应。 3.3布局和外观 3.3.1 机床应布局合理、造型美观、色彩和谐,符合人类工效学原则并便于调整及维修。
1
JB/T8362.2—2013
3.3.2 机床外观表面,不应有未规定的凸起、凹陷、粗糙不平和其他损伤。 3.3.37 机床的防护罩及防护装置应表面平整、匀称,不应翘曲、凹陷。 3.3.4 机床外露零件表面不应有磕碰、锈蚀,螺钉、铆钉、销子端部不应有扭伤、锤伤等缺陷。 3.3.5 金属手轮轮缘和操纵手柄表面应涂层防锈。电镀件、发蓝件、发黑件色调应一致,防护层不应有褪色、脱落现象。 3.3.6机床涂漆颜色及光泽应均匀一致、涂漆层应平整,涂漆表面不应有起泡及脱落等缺陷。机床可拆卸的装配结合面的接缝处,在涂漆以后,应切开,切开时不应扯破边缘。 3.3.7机床的各种信息标志及标牌应在机床明显位置平整固定,清晰耐久,不歪斜。 3.3.8机床电气、液压、润滑及冷却等的管道的外露部分,应布置紧凑、排列整齐,必要时应用管夹固定,软管不应扭曲,折叠及断裂。 3.3.9装入沉孔的螺钉不应突出于零件表面,其头部与沉孔之间不应有明显的偏心,固定销一般应略突出于零件表面。螺栓尾端应略突出于螺母端面。外露轴端应突出于包容件的端面,突出值约为倒棱值。 内孔表面与壳体凸缘间的壁厚应均匀对称,其凸缘壁厚之差不应大于实际最大壁厚的25%。 3.3.10机床零部件外露结合面的边缘应整齐匀称,不应有明显的错位,门、盖与机床的结合面应贴合。 错位量及贴合缝隙值不应大于表1的规定。
表1错位量及贴合缝隙值
单位为毫米
结合面边缘及门、盖边长尺寸
≤500 1.5 1 1 1
>500~1250
>1250 3 1.5 2 2
错位量错位不匀称量贴合缝隙值缝隙不均匀值
2 1 1.5 1.5
注1:当结合面边缘及门、盖边长尺寸的长、宽不一致时,可按长边尺寸确定允许值。 注2:错位不匀称量指外露结合面边缘同边或对应边最大错位量与最小错位量之差值。 注3:缝隙不均匀值指门、盖间对开缝或其相对机床本体间最大缝隙值与最小缝隙之差值。
3.4电气系统
机床的电气系统应符合GB5226.1--2008的规定。 3.5液压、润滑和冷却系统 3.5.1机床的液压系统应符合GB/T23572—2009的规定。 3.5.2机床的润滑系统应符合GB/T6576—2002的规定。 3.5.3机床的冷却系统应保证冷却充分、可靠。 3.5.4机床的液压、润滑、冷却系统及其他部位均不应漏(渗)油、漏(渗)水。 3.6安全防护 3.6.1操作手轮、手柄离地面的高度按GB157602004中的“仅调整时使用”的规定考核。 3.6.2观察读数的测量装置,其读数机构的安装高度均按“不经常使用”的读数机构的要求考核。 3.6.3机床上应有防止冷却液飞溅的防护装置,各移动部件的导轨副容易被尘屑磨损的部位应有防护装置。 3.6.4工作台(下压模)前进或后退运动,应有限位和防止碰撞的防护装置。 3.6.5机床下列部位或动作应有安全联锁装置:
a)运动部件间的动作顺序,多泵系统中泵的开动先后次序,均应有安全联锁装置;
2
JB/T8362.2-2013
b)当系统压力不正常或发生故障时应发出警告信号或设急停按钮; c)使用蓄能器的液压系统,应有释放或切断蓄能器中液体压力的装置; d)工件未夹紧,机床的工作循环不能起动。
3.7加工和装配质量1) 3.7.1机械加工件、焊接件应符合图样、工艺文件及GB/T25376--2010、GB/T23570—2009等的有关规定。机床的装配应符合GB/T25373—-2010的规定。 3.7.2,机床灰铸铁件应符合JB/T3997—2011的规定。 3.7.3床身、工作台、工作台支承座、上液压缸缸体、加压液压缸缸体及下盖等重要铸件,应在粗加工后进行时效处理。采用焊接的机床床身应在焊接后进行时效处理。 3.7.4机床床身与工作台之间的导轨副或滑杆及套组成的滑移副应采取耐磨措施。上压模动时定位用的偏心轮,上油缸活塞杆及上下平面凸轮等重要零件,应采取耐磨措施,并符合材质及热处理有关标准的规定。 3.7.5工作台与工作台支承座之间结合面、前立柱与床身之间的结合面、前立柱与液压缸壳体之间的结合面等重要固定结合面,其制造及验收应符合GB/T25376—2010和GB/T25373-—2010的规定。 3.7.6机床各移动部件的导轨副为移置导轨,其制造及验收应符合GB/T253762010和GB/T25373- 2010的规定。 3.7.7机床清洁度按GB/T25374-2010规定的方法进行,一般用目测、手感法检查,不得有脏物。液压和润滑油箱的清洁度用重量法检测,在机床运行30min后,立即从循环润滑油箱(或油池)中的油液中部取油样,一般不少于200mL,油中脏物含量不得超过150mg/L。
4检验与验收
4.1概述 4.1.1每台机床应在制造厂经检验合格后出厂。特殊情况下经用户同意可在机床使用处进行检验。当在机床使用处验收机床时,其验收的项目由用户与制造厂商定。 4.1.2机床检验分为型式试验和出厂检验。 4.1.2.1属于下列形式之一时,应进行型式试验:
a)新产品试制、定型鉴定; b)机床结构、性能较基型有重大改动。
4.1.2.2机床出厂检验一般包括以下内容:
a)外观检验; b)附件和工具检验; c)参数检验(抽查); d)机床的空运转试验(含抽查项); e)机床的负荷试验(含抽查项); f)机床的精度检验; g)其他。
4.2一般要求 4.2.1本部分是对GB/T9061—2008、GB/T23570--2009、GB/T25373—2010、GB/T25376—2010等
1)本章中所提及的重要铸件、主要零件及结合面应视产品的具体结构而定。
3
JB/T8362.2-2013
标准的具体化和补充。按本部分检验与验收机床时,应同时对上述标准中未经本部分具体化的其余有关验收项目进行检验。 4.2.2,验收机床时,按GB/T25372一2010规定的V级精度机床的要求检验。 4.2.3检验与验收前,应将机床安置在适当的基础上,按照制造商的使用说明书调平机床,并应符合 JB/T8362.1-2013规定的安装要求。 4.2.4检验过程中,不应调整影响机床精度和性能的机构和零件。用地脚螺栓紧固的机床,在检验过程中不应重新调整安装水平。否则,应复检调整后受到影响的有关项目。 4.2.5检验原则上是在制造完毕的成品上进行,特殊情况下可按制造商的使用说明书拆卸某些零,部件。 4.2.6机床由于结构上的限制或不具备规定的测试工具时,可用与标准有等同效果的方法代替。 4.3外观检验
按3.3评定及检验机床的布局和外观质量。 4.4附件和工具的检验
按3.2检验随行供应的附件和工具是否符合规定。 4.5参数检验(抽查)
按设计文件检验机床的参数及机床与工夹量具、附件等连接部位的型式和尺寸。 4.6机床的空运转试验 4.6.1动作试验
机床的动作试验包括工作台前进、压模下降、工作台后退、压模上升,以上动作各做10次,动作应准确、无故障。机床工作台有点进(退)动作时,还应考核工作台的点进(退)动作。 4.6.2安全防护
按3.6的要求检验机床的安全防护是否符合规定。 4.6.3噪声检验
按GB/T167692008的规定测量机床的空运转噪声,其噪声声压级不应超过83dBA)。机床运转时,不应有异常的尖叫声、冲击声。 4.6.4工作循环试验
工作循环试验应按表2的规定进行(可不喷冷却液)试验时机床各机构均应工作正常。
表2空运转时间
中中 30~60
长最小 10~20
喷油时间喷油量循环次数
短最大 10~20
4.6.5电气系统的检验
机床电气系统应符合GB5226.1-2008等有关标准的规定,其功能应可靠、稳定,满足机床使用性能的要求。 4
JB/T8362.2---2013
4.6.6液压、冷却和润滑系统的检验
液压、冷却和润滑系统应符合3.5的规定。 4.7:机床的负荷试验 4.7.1 本系列机床应进行负荷试验,推荐的试验参数见表3。 4.7.2 负荷试验应连续进行10次。
表3负荷试验参数
冷却条件
机床最大工件直径
加压压力Pa
加压方式
脉动频率
外压环 内压环 扩张器 外压环 内压环 扩张器 次/min 冷却 喷油时间 喷油量
分段 min L/min 第一段 30
mm
1130 780 1130 1130 780 1130
≤500 4×106 3×106 1.6x106
27 第二段 40
第三段 40 第一段 30 第二段 50 第三段 50
脉动 脉动 固定
>500~ 800
5.5×106 4x106 2×106
18
4.8 机床的精度检验 4.8.1 机床的几何精度检验应符合JB/T8362.1一2013的规定。 4.8.2 本系列机床一般不做工作精度检验,当用户需要时可在协议中说明。 4.8.3 机床工作台进入工作位置的重复定位精度应连续测量7次,误差以测量数值的最大和最小读数的代数差值计,允差见表4。
表4重复定位精度
单位为毫米
最大工件直径 >320~800
>800 0.050
≤320 0.025
0.040
4.9其他
可按订货合同中技术要求的有关内容进行。
5包装
5.1机床在包装前,应按相关规定进行防锈处理。 5.2出厂的机床包装箱内,应提供一套随行技术文件。 5.3机床的包装应符合JB/T8356.1—1996和JB/T8356.2—1996有关规定。
5