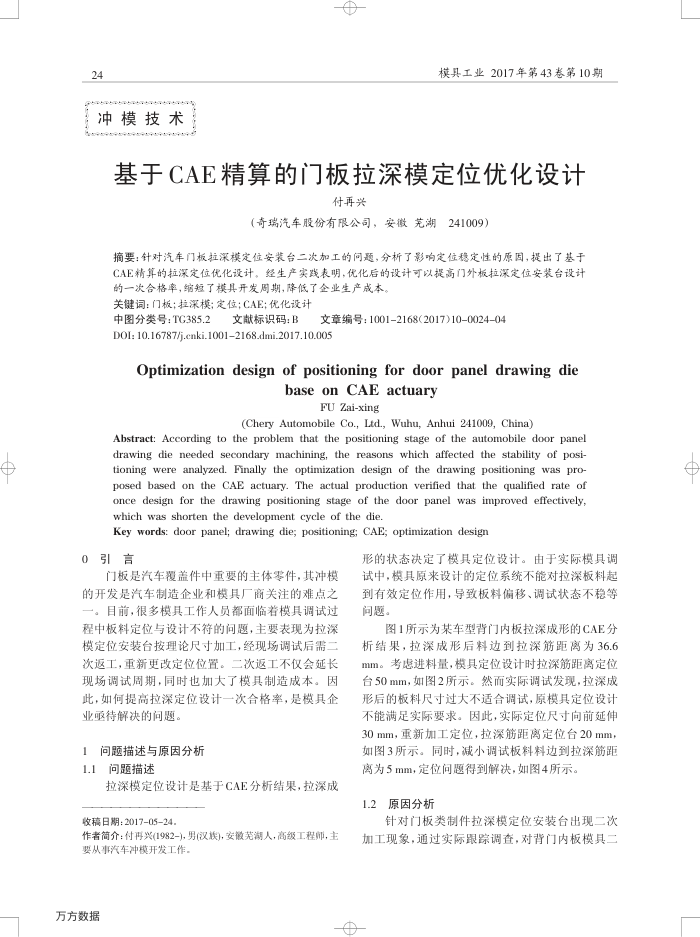
24
冲模技术
模具工业2017年第43卷第10期
基于CAE精算的门板拉深模定位优化设计
付再兴
(奇瑞汽车股份有限公司,安徽芜湖241009)
摘要:针对汽车门板拉深模定位安装台二次加工的问题,分析了影响定位稳定性的原固,提出了基于 CAE精算的拉深定位优化设计。经生产实践表明,优化后的设计可以提高门外板拉深定位安装台设计
的一次合格率,缩短了模具开发周期,降低了企业生产成本。关键词:门板;拉深模;定位;CAE;优化设计
中图分类号:TG385.2
文献标识码:B
文章编号:10012168(2017)10002404
D0I: 10.16787/j.cnki.10012168.dmi.2017.10.005
Optimizationdesignofpositioningfordoorpaneldrawingdie
baseonCAEactuary
FU Zai-xing
(Chery Automobile Co., Ltd., Wuhu, Anhui 241009, China)
Abstract: According to the problem that the positioning stage of the automobile door panel drawing die needed secondary machining, the reasons which affected the stability of posi tioning were analyzed. Finally the optimization design of the drawing positioning was pro-posed based on the CAE actuary. The actual production verified that the qualified rate of once design for the drawing positioning stage of the door panel was improved effectively which was shorten the development cycle of the die.
Key words: door panel; drawing die; positioning; CAE; optimization design
0引言
门板是汽车覆盖件中重要的主体零件,其冲模的开发是汽车制造企业和模具厂商关注的难点之。目前,很多模具工作人员都面临着模具调试过程中板料定位与设计不符的问题,主要表现为拉深模定位安装台按理论尺寸加工,经现场调试后需次返工,重新更改定位位置。二次返工不仅会延长现场调试周期,同时也加大了模具制造成本。因此,如何提高拉深定位设计一次合格率,是模具企业重待解决的问题。
1问题描述与原因分析 1.1问题描述
拉深模定位设计是基于CAE分析结果,拉深成收稿日期:2017-05-24
作者简介:付再兴(1982-),男(汉族),安散芜湖人,高级工程师,主要从事汽车冲模开发工作。
万方数据
形的状态决定了模具定位设计。由于实际模具调试中,模具原来设计的定位系统不能对拉深板料起到有效定位作用,导致板料偏移、调试状态不稳等问题。
图1所示为某车型背门内板拉深成形的CAE分
析结果,拉深成形后料边到拉深筋距离为36.6 mm。考虑进料量,模具定位设计时拉深筋距离定位台50mm,如图2所示。然而实际调试发现,拉深成形后的板料尺寸过大不适合调试,原模具定位设计不能满足实际要求。因此,实际定位尺寸向前延伸 30mm,重新加工定位,拉深筋距离定位台20mm,如图3所示。同时,减小调试板料料边到拉深筋距
离为5mm,定位问题得到解决,如图4所示。 1.2原因分析
针对门板类制件拉深模定位安装台出现二次加工现象,通过实际跟踪调查,对背门内板模具二