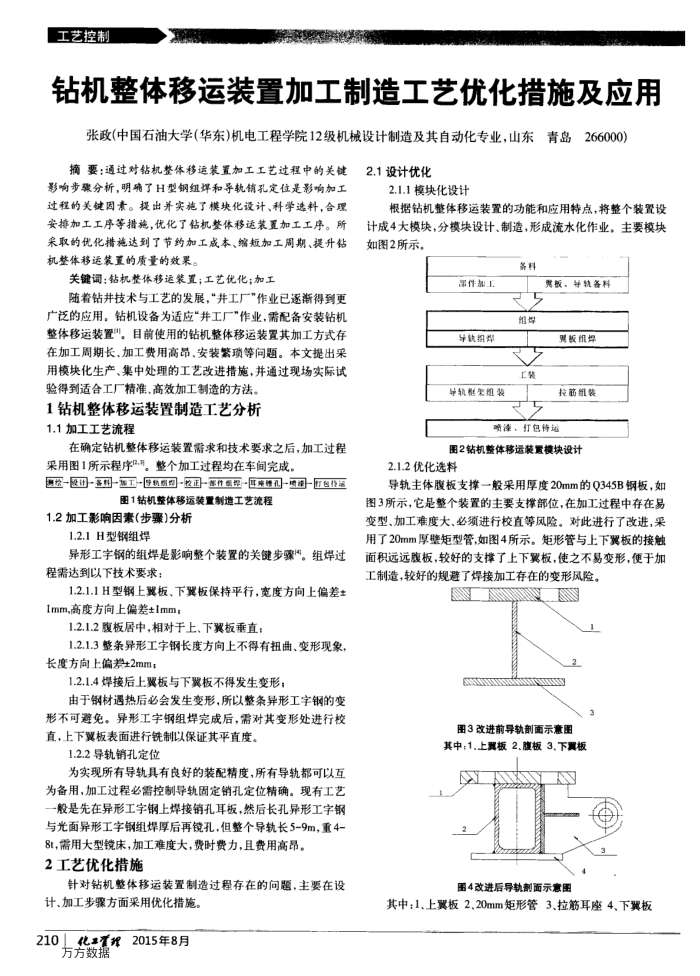
工艺控制
钻机整体移运装置加工制造工艺优化措施及应用张政(中国石油大学(华东)机电工程学院12级机械设计制造及其自动化专业,山东青岛266000)
摘要:通过对钻机整体移造装置加工工艺过程中的关键影响步聚分析,明确了H型钢组焊和导轨销孔定位是影响加工过程的关键因素。提出并实施了模块化设计、科学选料,合理安排加工工序等措施,优化了钻机整体移运某置加工工序。所采取的优化措施达到了节约加工成本、缩短加工周期、提升钻机整体移运装的质量的效果。
关键调:钻机整体移运装置:工艺优化加工
随着钻井技术与工艺的发展,“并工厂"作业已逐浙得到更广泛的应用。钻机设备为适应“井工厂”作业,需配备安装钻机整体移运装置"。目前使用的钻机整体移运装置其加工方式存在加工周期长,加工费用高昂、安装等项等间题。本文提出采用模块化生产、集中处理的工艺改进措施,并通过现场实际试
验得到适合工厂精准、高效加工制造的方法。 1钻机整体移运装置制造工艺分析 1.1加工工艺流程
在确定钻机整体移运装置需求和技术要求之后,加工过程果用图1所示程序,整个加工过程均在车间完成。
经-区-善利-加工-9热期图-轻正-件能经-率维月-随动-红包特道
图1钻机整体移运装置制造工艺流程
1.2加工影响因素(步骤)分析
1.2.1H型钢组焊
异形工字钢的组焊是影响整个装置的关键步骤。组焊过程需达到以下技术要求:
1.2.1.1H型钢上翼板,下翼板保持平行,宽度方向上偏差 Imm,高度方向上偏差+Imm;
1.2.1.2腹板居中,相对于上、下翼板垂直:
1.2.1.3整条异形工字钢长度方向上不得有扭曲、变形现象,长度方向上偏差+2mm;
1.2.1.4焊接后上翼板与下翼板不得发生变形
由于钢材遇热后必会发生变形,所以整条异形工字钢的变形不可避免。异形工字钢组焊完成后,需对其变形处进行校直,上下翼板表面进行铣制以保证其平直度。
1.2.2导轨销孔定位
为实现所有导轨具有良好的装配精度,所有导轨都可以互为备用,加工过程必需控制导轨固定销孔定位精确。现有工艺一般是先在异形工字钢上焊接销孔耳板,然后长孔异形工字钢与光面异形工字钢组焊厚后再镜孔,但整个导轨长5-9m,重4
8t,需用大型镜床,加工难度大,费时费力,且费用高昂。 2工艺优化措施
针对钻机整体移运装置制造过程存在的问鹭.主要在设
计、加工步骤方面采用优化措施 210!化置理
22015年8月
方方数据
2.1设计优化
2.1.1模块化设计
根据钻机整体移运装置的功能和应用特点,将整个装置设计成4大模块,分模块设计、制造,形成流水化作业。主要模块如图2所示。
各料
部件加工导软组翠导轨耗象组装
组焊工装
翼板、导轨各料粥板组焊挖蔽组装
喷漆、打包待
图2钻机整体移运装置模块设计
2.1.2优化选料
导轨主体股腹板支撑一般采用厚度20mm的Q345B钢板,如图3所示,它是整个装置的主要支撑部位,在加工过程中存在易变型、加工难度大、必须进行校直等风险。对此进行了改进,采用了20mm厚壁矩型管,如图4所示。矩形管与上下翼板的接触面积远远腹板,较好的支撑了上下翼板,使之不易变形,便于加工制造,较好的规避了焊接加工存在的变形风险。
图3改进前导轨剖面示意图其中:1.上翼板2.腹板3.下翼板
图4改进后导轨剖面示意图
其中:1.上翼板2.20mm矩形管3.拉筋耳座4、下翼板