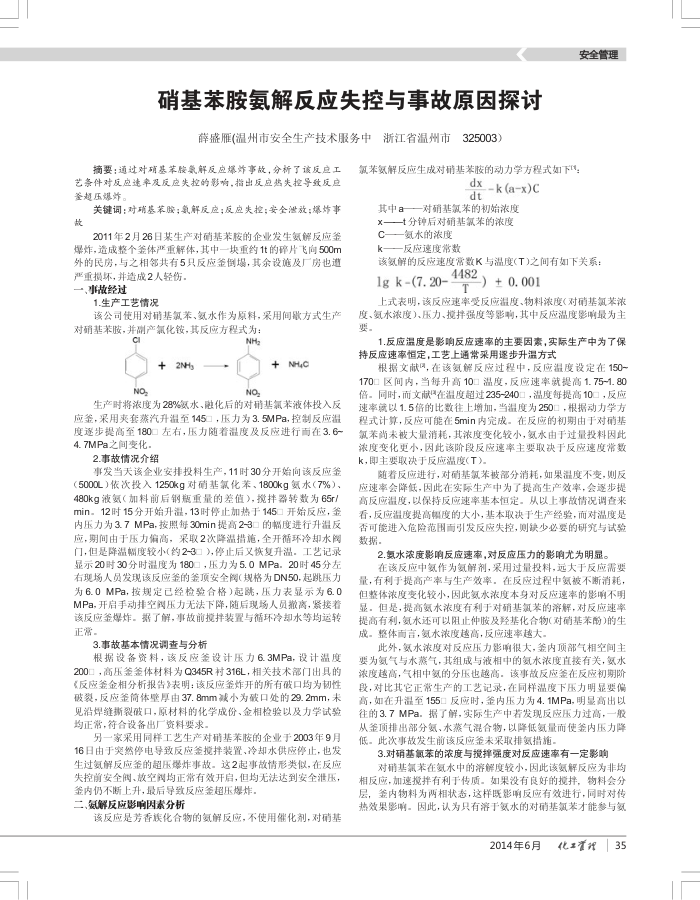
硝基苯胺氨解反应失控与事故原因探讨
薛盛雁(温州市安全生产技术服务中
摘要:通过对硝基萃胺氯解反应爆炸事故,分析了该反应工艺条件对反应速率及反应失拉的影响,指出反应热失控导致反应签超压爆炸,
关键调:对瑞基苯胺;氢解及应;及应失控;安全泄放;爆炸事故
2011年2月26日某生产对硝基苯胺的企业发生氨解反应釜爆炸,造成整个釜体严重解体,其中一块重约1t的辞片飞向500m 外的民房,与之相邻共有5只反应釜倒堤,其余设施及厂房也道
严重损坏,并造成2人轻伤,一、事故经过
1.生产工艺情况
该公司使用对硝基氯苯、氨水作为原料,采用间歌方式生产对硝基苯胺,并副产氯化铵,其反应方程式为:
NH2
2N +
NO,
NO
+NHC
生产时将浓度为28%氨水、融化后的对确基氯苯液体投入反应签,采用爽套蒸汽升温至145,压力为3.5MPa,控制反应温度逐步提高至180左右,压力随着温度及反应进行面在3.6~ 4.7MPa之间变化。
2.事故情况介绍
事发当天该企业安排投料生产,11时30分开始向该反应釜(5000L)依次投入1250kg对硝基氯化苯1800kg氨水(7%), 480kg液氨(加料前后钢瓶重量的差值),搅拌器转数为65r/ min12时15分开始升温,13时停止加热于145开始反应,签内压力为3.7MPa,按照每30min提高2-3的幅度进行升温反应,期间由于压力俏高,采取2次降温措施,全开循环冷却水阀门,但是降温幅度较小(约2-3),停止后又恢复升温,工艺记录显示20时30分时温度为180,压力为5.0MPa.20时45分左右现场人员发现该反应釜的釜项安全(规格为DN50.起跳压力为6.0MPa,按规定已经检验合格)起跳,压力表显示为6.0 MPa,开启手动排空阅压力无法下降,随后现场人员撤离,紧接着该反应釜爆炸。据了解,事故前搅拌装置与循环冷却水等均运转正常。
3.事故基本情况调查与分析
根据设备资料,该反应签设计压力6.3MPa,设计温度 200,高压签签体材料为Q345R村316L,相关技术部门出具的《反应签金相分析报告3表明:该反应釜炸开的所有破口均为韧性破裂,反应釜简体壁厚由37.8mm减小为破口处的29.2mm,未见沿焊缝撕裂破口,原材料的化学成份、金相检验以及力学试验均正常,符合设备出厂资料要求
另一家采用同样工艺生产对硝基苯胺的企业于2003年9月 16日由于突然停电导致反应签搅拌装置、冷却水供应停止,也发生过氨解反应釜的超压媒炸事故-这2起事故情形类似,在反应失控前安全阀、散空阅均正常有效开启,但均无法达到安全泄压,
签内仍不断上升,最后导致反应釜超压爆炸,二、氨解反应影响因素分析
该反应是芳香族化合物的氨解反应,不使用催化剂,对硝基
浙江省温州市
325003)
安全管理
氯苯氨解反应生成对确其苯胺的动力学方程式如下1,
dx -k (ax)c 3p
一对硝基氯苯的初始浓度
其中a
—t分钟后对硝基氯苯的浓度
C——氨水的浓度 k——反应速度常数
该氨解的反应速度常数K与温度(T)之间有如下关系:
4482
1g k (7. 20
±0.001
上式表明,该反应速率受反应温度、物料浓度(对硝基氨苯浓度、氨水浓度)、压力、搅择强度等影响,其中反应温度影响最为主要
1.反应温度是影响反应速率的主要因素,实际生产中为了保持反应速事恒定,工艺上通常采用遥步升温方式
根据文献口,在该氨解反应过程中,反应温度设定在150~ 170区间内,当每升高10温度,反应速率就提高1.75~1.80 倍。同时,而文献"在温度超过235-240,温度每提高10,反应速率就以1.5倍的比数往上增加,当温度为250口,根据动力学方程式计算,反应可能在5min内完成。在反应的初期由于对硝基氯苯尚未被大量消耗,其浓度变化较小,氨水由于过量投料因此浓度变化更小,因此该阶段反应速率主要取决于反应速度常数 k,即主要取决于反应温度(T)。
随着反应进行,对硝基氯苯被部分消耗,如果温度不变,则反应速率会降低,固此在实际生产中为了提高生产效率,会逐步提高反应温度,以保持反应速率基本恒定。从以上事故情况调查来看,反应温度提高幅度的大小,基本取决于生产经验,而对温度是否可能进入危险范围而引发反应失控,则缺少必要的研究与试验数据
2.氨水浓度影响反应速事,对反应压力的影响尤为明显。在该反应中氨作为氨解剂,采用过量投料,远大于反应需要
量,有利于提高产率与生产效率,在反应过程中氨被不断消耗但整体浓度变化较小,固此氨水浓度本身对反应速率的影响不明显,但是,提高氨水浓度有利于对硝基氧苯的溶释,对反应速率提高有利,氨水还可以阻止仲胺及羟基化合物(对硝基苯酚)的生成。整体面言,氨水浓度越高,反应速率越大。
此外,氮水浓度对反应压力影响很大,釜内项部气相空间主要为氨气与水蒸气,其组成与液相中的氨水浓度直接有关,氨水浓度越高,气相中氨的分压也越高,该事故反应釜在反应初期阶段,对比其它正常生产的工艺记录,在同样温度下压力明显要偏高,如在升温至155口反应时,釜内压力为4.1MPa,明显高出以往的3.7MPa.据了解,实际生产中若发现反应压力过高,一般从釜项排出部分氨、水蒸气混合物,以降低氨量而使釜内压力降低。此次事故发生前该反应签未采取排氨措施。
3.对硝基氯苯的浓度与搅择强度对反应速率有一定影响
对硝基氯苯在氨水中的溶解度较小,因此该氨解反应为非均相反应,加速搅拌有利于传质。如果没有良好的搅拌,物料会分层,釜内物料为内相状态,这样既影明反应有效进行,同时对传热效果影明。因此,认为只有溶于氨水的对硝基氧苯才能参与氨
2014年6月
化置理
35