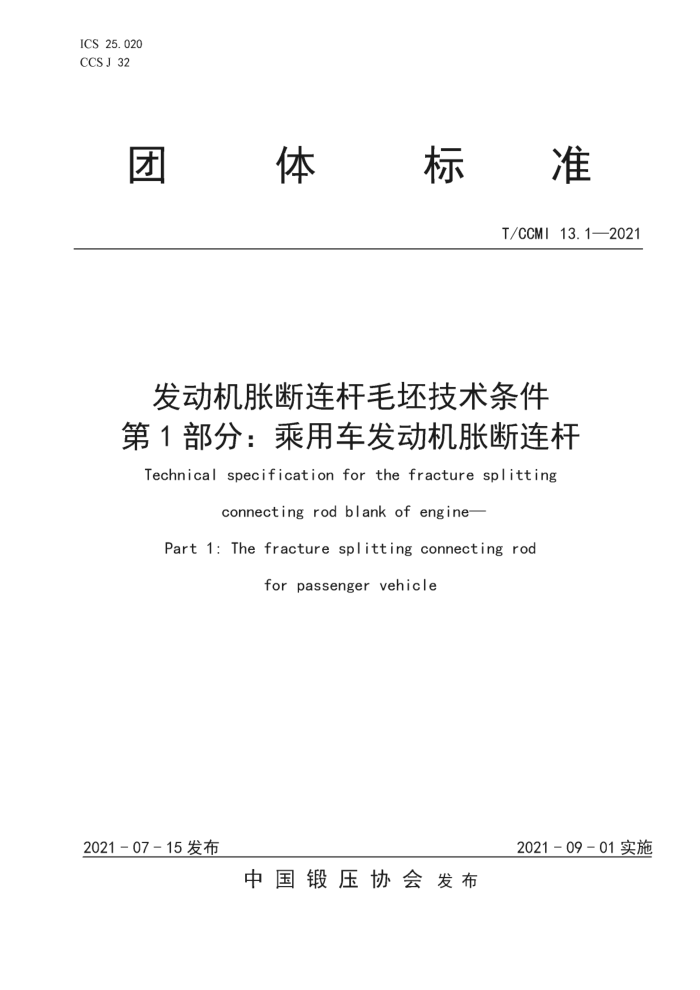
T/CCMI13.1-2021
目次
前言
II
范围规范性引用文件
1
2
3 术语和定义
2
技术要求 5 检验方法,
4
5
检验规则. 7 判定与复检 8标识、包装、运输和贮存附录A(资料性) 发动机连
6
8
WOSS IWOO
9
金相组织图
11
图1 取样位置示意图图2 阿曼试片测试装置图3 内应力检测示意图图 A.1 C70S6显微组织图A.2 C70S6显微组织图A.3 70MnVS4显微组织图A.4 70MnVS4显微组织图A.5 46MnVS5显微组织图A.6 46MnVS5显微组织图A.7 36MnVS4显微组织图A.8 36MnVS4显微组织(500倍)
2
12 12 13 13
表1 发动机连杆毛坏化学成分(熔炼分析)表2非金属夹杂物(级)表3发动机连杆毛坏金相组织表4发动机连杆毛坏硬度值,表5发动机连杆毛坏强度和塑性. 表6发动机连杆毛坏重量公差,表7发动机连杆检验项目、检验比例及试验方法
-
1
T/CCMI13.1-2021
前言
本文件按照GB/T1.1-2020《标准化工作导则第1部分:标准化文件的结构和起草规则》给出的规则起草。
本文件是T/CCMI13《发动机胀断连杆毛坏技术条件》的第1部分。 请注意本文件的某些内容可能涉及专利。本文件的发布机构不承担识别专利的责任。 本文件由中国锻压协会发动机连杆委员会、白城中一精锻股份有限公司提出。 本文件由中国锻压协会归口。 本文件起草单位:白城中一精锻股份有限公司、北京科技大学、南营市精强连杆有限公司、浙江跃
进机械有限公司、张家港市环鑫精密锻造有限公司、重庆江东汽车零部件有限责任公司、石家庄钢铁有限责任公司、江阴兴澄特种钢铁有限公司、建龙北满特殊钢有限责任公司、抚顺特殊钢有限公司。
本文件主要起草人:唐兰晶、廖劲松、邓晓明、张朝磊、冯书华、骆春阳、穆天柱、汪义高、郝彦英、张磊、刘广磊、马群。
本文件为首次发布。
II
T/CCMI 13.1-2021
发动机胀断连杆毛坏技术条件第1部分:乘用车发动机胀断连杆
1范围
本文件规定了乘用车发动机胀断连杆毛坏用术语和定义、技术要求、检验方法、检验规则、判定与复检、标识、包装、运输和贮存等。
本文件适用于乘用车发动机(专指汽油发动机)胀断连杆毛坏。
2规范性引用文件
2
下列文件中的内容通过文中的规范性引用而构成本文件必不可少的条款。其中,注日期的引用文件,仅该日期对应的版本适用于本文件:不注日期的引用文件,其最新版本(包括所有的修改单)适用于本文件。
GB/T 222 钢的成品化学成分允许偏差 GB/T223 钢铁及合金化学分析方法 GB/T 224 钢的脱碳层深度测定法 GB/T 226 钢的低倍组织及缺陷酸蚀检验法 GB/T228.1 金属材料拉伸试验第1部分:室温试验方法 GB/T 231.1 金属材料布氏硬度试验第1部分:试验方法 GB/T702-2017 热轧钢棒尺寸、外形、重量及允许偏差 GB/T1979 结构钢低倍组织缺陷评级图 GB/T 2828.1 计数抽样检验程序第1部分:按接收质量限(AQL)检索的逐批检验抽样计 GB/T 3077 合金结构钢 GB/T 4162 锻轧钢棒超声检测方法 GB/T 4336 碳素钢和中低合金钢多元素含量测定 火花放电原子发射光谱法(常规法) GB/T 4879 防锈包装 GB/T 6394 金属平均晶粒度测定方法 GB/T 7704 无损检测X射线应力测定方法 GB/T10561-2005 钢中非金属夹杂物含量的测定标准评级图显微检验法 GB/T12339 防护用包装材料 GB/T12362 钢质模锻件公差及机械加工余量 GB/T13298 金属显微组织检验方法 GB/T 14188 气相防锈包装材料选用通则 GB/T19532 包装材料气相防锈塑料薄膜 GB/T 20123 钢铁总碳硫含量的测定高频感应炉燃烧后红外吸收法(常规方法) GB/T20124 钢铁氮含量的测定惰性气体熔融热导法(常规方法) GB/T30512 汽车禁用物质要求 BB/T 0049 包装用矿物干燥剂
1
T/CCMI13.12021
JB/T6721.2 内燃机连杆第2部分:磁粉检测 JB/T 8354.1 抛喷丸清理及强化用金属磨料 第1部分:钢丝切丸 JB/T8354.2 抛喷丸清理及强化用金属磨料 第2部分:高碳铸钢丸 JB/T10174-2000钢铁零件强化喷丸的质量检验方法 QC/T941 汽车材料中汞的检测方法 QC/T942 汽车材料中六价铬的检测方法 QC/T943 汽车材料中铅、镉的检测方法 QC/T944 汽车材料中多溴联苯(PBBs)和多溴二苯醛(PBDEs)的检测方法
3术语和定义
下列术语和定义适用于本文件。
3. 1
胀断连杆 Ffractured connecting rod 利用特种钢材的裂解特性,通过连杆大头孔内预制应力槽获得裂解扩展源,使用特定方法控制裂解
痕迹的扩展方向,使连杆体与连杆盖脆性断裂分离,加工组装后获得的连杆,称胀断连杆或裂解连杆。 3. 2
表面覆盖率 surfaceco OFCCM
表面缺陷深度 defect dept 表面缺陷深度是指连杆表面
the surfa 麻点、 雅价的 际深度。
?
> 是部位上,测得弹痕占据的面积与要求强化喷
3. 3
PSSS
rate E 是以在被
受喷零件表面上呈现压坑丸的面积之间的比值,用百分
C
盖率用喷丸时间来计算。
超过100%的
L
[来源:JB/T10174-2000
0
4技术要求
4.1连杆材料 4.1. 1 化学成分
5
连杆的材料牌号和化学成分(熔炼务析)应符台表1的规定。
表1 发动机连杆毛坏化学成分(熔炼分析)
化学成分(质量分数)%
材料牌号
Cr
Mo
Ni
Mn
A1
Nb
C 0. 67 0. 15 0. 45
Si
P
S 0.060 0.10
V
N
≤ 0. 03 ≤ 0.012
≤ 0.045
C70S6
~
~
1
0.070 0.20 0.06 0.20 0. 04 0. 03 0.016 0.060 0.10 ≤ ≤ 0.10 ≤ 0.010
0. 73 0. 25 0. 65 0. 69 0. 15 0.80
≤
~
70MnVS4
~
~
0. 045 ~
A
A
0.070 0.20 0.06 0.20 0. 15 0. 03 0.016 0.040 0.10 ≤ ≤ 0.10 M 0.014 0.015
0. 73 0. 30 0. 90 0. 42 0. 40 0.90
M
46MnVS5 ~
~
0. 045 ~
~
0.08 0. 20 ~ 0. 03
~
0.022 0. 045
0. 48 0. 80 1. 30
0.070 0.30
0.20
2
T/CCMI13.1-2021
表1 发动机连杆毛坏化学成分(熔炼分析) (续)
材料牌号
化学成分 (质量分数)%
Si
Mn
Cr Mo
Ni
Nb
C
P
S
A1
N
V
低S: 0. 030 ~ 0. 10
0. 20 ~
≤ 0.015
0. 34 0. 60 0. 95 ≤ 0.045
M
≤
~
36MnVS4 ~
~
~
~ 0.020
0. 42 0.75 1. 05 0. 045 高S: 0. 25 0. 06 0. 20 0.35 0. 03
0.060
0.085
注1:C70、S70CVS1材料要求参照C70S6。 注2:38MnVS4、S36CVS2材料要求参照36MnVS4。 注3:46MnVS6材料要求参照46MnVS5。 注4:N元素允许偏差土0.002,S元素允许偏差土0.005,其它化学成份的允许偏差应符合GB/T222的规定
4.1.2非金属夹杂物及低倍组织
钢材的非金属夹杂物应按GB/T10561一2005的A法进行检验:夹杂物的判定应按GB/T10561一2005 附录A进行评级,结果应符合表2中的要求。钢材的横截面酸浸低倍试片上不应有肉眼可见的缩孔、气泡、裂纹、夹杂、翻皮及白点等缺陷,酸浸低倍组织按GB/T1979评级,其一般疏松、中心疏松和偏析均不应大于3级。
2非金属夹杂物 (级)
表2
B ≤2.0 ≤2.0
C ≤1. 0 ≤1.0
D ≤1. 0 ≤1.0
粗系细系
≤4.0 ≤3.0
4.1.3 3晶粒度
晶粒度按GB/T6394评级,应不粗于5级, 4.1.4 超声波检验
原材料进行超声波检验,按GB/T4162进行检验,缺陷分级应为A级以上。 4.1.5 5尺寸、外形、重量
尺寸、外形、重量按GB/T702中有关规定执行,尺寸精度、弯曲度按GB/T702一2017的1组规定执
行。 4.1.6其它
脱碳层、试验方法、表面质量、检验规则、验收、包装、标志、质量证明书等按GB/T3077中有关规定执行。
3
T/CCMI 13.1-2021 4. 2 连杆宏观组织
连杆流线方向应连续,金属晶粒流动应遵循锻造轮廓,沿着连杆中心线,并与连杆外形相符,不应有紊乱、扭曲、折叠、回流和间断现象。 4. 3 金相组织及脱碳层 4.3.1 连杆毛坏的基体组织应为均匀的珠光体和少量铁素体,晶粒度按GB/T6394评级,金相组织、 晶粒度和铁素体含量要求见表3。
表3 发动机连杆毛坏金相组织组织
牌号 C70S6 70MnVS4 46MnVS5 36MnVS4
铁素体含量不大于10% 不大于10% 不大于25% 不大于35%
晶粒度 5~8级 5~8级 5~8级 6~9级
铁素体+珠光体铁素体+珠光体铁素体+珠光体铁素体+珠光体
4.3.2 连杆毛坏表面不准许有完全脱碳, 部分脱碳层深度应不大于0.15mm。 4.4力学性能 4.4.1 连杆毛坏的硬度要求应符合表4的规定,同一连杆硬度差应不大于35HB。
表4 发动机连杆毛坏硬度值
牌号硬度值(HB)
C70S6 260~320
70MnVS4 310~370
46MnVS5 285~345
36MnVS4 285~345
4.4.2 连杆毛坏强度和塑性应符合表5规定,
表5 发动机连杆毛坏强度和塑性
屈服强度 Re1/Rpo. 2 (MPa) 不小于550 不小于650 不小于750 不小于750
抗拉强度 R (MPa) 900~1080 1000~1200 1000~1200 1000~1200
断后伸长率 A (%) 不小于10 不小于10 不小于8 不小于8
断面收缩率 Z (%) 20~40 20~40 25~45 30~50
牌号 C70S6 70MnVS4 46MnVS5 36MnVS4
4. 5 尺寸
连杆毛坏未注尺寸公差按GB/T12362中的精密级执行。 4.6 重量
胀断连杆毛坏重量应符合产品图样的规定,重量允许公差组别应符合表6规定。
4
T/CCMI13.1-2021
表6发动机连杆毛坏重量公差
组别 I 组 II 组 II组
重量公差 ± 1. 5% ±2. 0% ±2. 5%
4.7喷丸和内应力
4.7.1连杆毛坏应进行表面强化处理;推荐采用符合JB/T8354.1标准要求的钢丝切丸或JB/T8354.2 标准要求的高碳铸钢丸,其直径宜在0.8mm1.2mm范围内选择,硬度宜在HRC40~HRC48范围内选择。 4.7.2连杆毛坏喷丸强度应控制在0.3A~0.5A之间,表面残余压应力应不小于350MPa;表面覆盖率应达到200%,喷丸时间是其获得100%覆盖率所需时间的2倍。 4.7.3内应力用胀断位置切开后变形量(胀断位置切并前后直径差的最大值)来表示,应不大于 0.06mmc 4.8探伤
连杆毛坏应进行100%的荧光磁粉探伤。探伤后的连杆毛坏应进行退磁,退磁后连杆毛坏的剩余磁
场强度应不大于2×10T(2Gs)。 4.9表面质量 4.9.1连杆毛坏非加工表面:表面应光洁;不应有裂纹、折叠、结疤、折痕、氧化皮残留、锈迹及因金属未充满锻模而产生的缺陷;杆身部位不准许有切边拉伤。 4.9.2连杆毛坏待加工表面:若实际尺寸等于基本尺寸时,其表面缺陷深度为单边加工余量之半:若实际尺寸大于或小于基本尺寸时,其表面缺陷深度为单边加工余量之半加或减单边实际偏差值。对内表面尺寸取相反值。 4.10修复 4.10.1 连杆工字梁筋部圆角处的任何缺陷均不准许修复,其它部位表面缺陷允许修复,经修复后的痕迹应沿金属纤维轮廓方向并且应圆滑过渡,修复后的连杆应经过喷丸处理。 4.10.2客户对连杆的修复有特殊要求的,按客户要求执行。 4.11 禁用物质
连杆毛坏禁用物质应符合GB/T30512标准规定。
5 检验方法
5.1材料化学分析
连杆材料的化学分析方法按GB/T223、GB/T4336、GB/T20123及GB/T20124的规定。 5.2宏观组织
按GB/T226中的规定腐蚀后应采用目视或低倍放大镜检查。 5.3金相组织及脱碳层
5
T/CCMI13.1-2021
目次
前言
II
范围规范性引用文件
1
2
3 术语和定义
2
技术要求 5 检验方法,
4
5
检验规则. 7 判定与复检 8标识、包装、运输和贮存附录A(资料性) 发动机连
6
8
WOSS IWOO
9
金相组织图
11
图1 取样位置示意图图2 阿曼试片测试装置图3 内应力检测示意图图 A.1 C70S6显微组织图A.2 C70S6显微组织图A.3 70MnVS4显微组织图A.4 70MnVS4显微组织图A.5 46MnVS5显微组织图A.6 46MnVS5显微组织图A.7 36MnVS4显微组织图A.8 36MnVS4显微组织(500倍)
2
12 12 13 13
表1 发动机连杆毛坏化学成分(熔炼分析)表2非金属夹杂物(级)表3发动机连杆毛坏金相组织表4发动机连杆毛坏硬度值,表5发动机连杆毛坏强度和塑性. 表6发动机连杆毛坏重量公差,表7发动机连杆检验项目、检验比例及试验方法
-
1
T/CCMI13.1-2021
前言
本文件按照GB/T1.1-2020《标准化工作导则第1部分:标准化文件的结构和起草规则》给出的规则起草。
本文件是T/CCMI13《发动机胀断连杆毛坏技术条件》的第1部分。 请注意本文件的某些内容可能涉及专利。本文件的发布机构不承担识别专利的责任。 本文件由中国锻压协会发动机连杆委员会、白城中一精锻股份有限公司提出。 本文件由中国锻压协会归口。 本文件起草单位:白城中一精锻股份有限公司、北京科技大学、南营市精强连杆有限公司、浙江跃
进机械有限公司、张家港市环鑫精密锻造有限公司、重庆江东汽车零部件有限责任公司、石家庄钢铁有限责任公司、江阴兴澄特种钢铁有限公司、建龙北满特殊钢有限责任公司、抚顺特殊钢有限公司。
本文件主要起草人:唐兰晶、廖劲松、邓晓明、张朝磊、冯书华、骆春阳、穆天柱、汪义高、郝彦英、张磊、刘广磊、马群。
本文件为首次发布。
II
T/CCMI 13.1-2021
发动机胀断连杆毛坏技术条件第1部分:乘用车发动机胀断连杆
1范围
本文件规定了乘用车发动机胀断连杆毛坏用术语和定义、技术要求、检验方法、检验规则、判定与复检、标识、包装、运输和贮存等。
本文件适用于乘用车发动机(专指汽油发动机)胀断连杆毛坏。
2规范性引用文件
2
下列文件中的内容通过文中的规范性引用而构成本文件必不可少的条款。其中,注日期的引用文件,仅该日期对应的版本适用于本文件:不注日期的引用文件,其最新版本(包括所有的修改单)适用于本文件。
GB/T 222 钢的成品化学成分允许偏差 GB/T223 钢铁及合金化学分析方法 GB/T 224 钢的脱碳层深度测定法 GB/T 226 钢的低倍组织及缺陷酸蚀检验法 GB/T228.1 金属材料拉伸试验第1部分:室温试验方法 GB/T 231.1 金属材料布氏硬度试验第1部分:试验方法 GB/T702-2017 热轧钢棒尺寸、外形、重量及允许偏差 GB/T1979 结构钢低倍组织缺陷评级图 GB/T 2828.1 计数抽样检验程序第1部分:按接收质量限(AQL)检索的逐批检验抽样计 GB/T 3077 合金结构钢 GB/T 4162 锻轧钢棒超声检测方法 GB/T 4336 碳素钢和中低合金钢多元素含量测定 火花放电原子发射光谱法(常规法) GB/T 4879 防锈包装 GB/T 6394 金属平均晶粒度测定方法 GB/T 7704 无损检测X射线应力测定方法 GB/T10561-2005 钢中非金属夹杂物含量的测定标准评级图显微检验法 GB/T12339 防护用包装材料 GB/T12362 钢质模锻件公差及机械加工余量 GB/T13298 金属显微组织检验方法 GB/T 14188 气相防锈包装材料选用通则 GB/T19532 包装材料气相防锈塑料薄膜 GB/T 20123 钢铁总碳硫含量的测定高频感应炉燃烧后红外吸收法(常规方法) GB/T20124 钢铁氮含量的测定惰性气体熔融热导法(常规方法) GB/T30512 汽车禁用物质要求 BB/T 0049 包装用矿物干燥剂
1
T/CCMI13.12021
JB/T6721.2 内燃机连杆第2部分:磁粉检测 JB/T 8354.1 抛喷丸清理及强化用金属磨料 第1部分:钢丝切丸 JB/T8354.2 抛喷丸清理及强化用金属磨料 第2部分:高碳铸钢丸 JB/T10174-2000钢铁零件强化喷丸的质量检验方法 QC/T941 汽车材料中汞的检测方法 QC/T942 汽车材料中六价铬的检测方法 QC/T943 汽车材料中铅、镉的检测方法 QC/T944 汽车材料中多溴联苯(PBBs)和多溴二苯醛(PBDEs)的检测方法
3术语和定义
下列术语和定义适用于本文件。
3. 1
胀断连杆 Ffractured connecting rod 利用特种钢材的裂解特性,通过连杆大头孔内预制应力槽获得裂解扩展源,使用特定方法控制裂解
痕迹的扩展方向,使连杆体与连杆盖脆性断裂分离,加工组装后获得的连杆,称胀断连杆或裂解连杆。 3. 2
表面覆盖率 surfaceco OFCCM
表面缺陷深度 defect dept 表面缺陷深度是指连杆表面
the surfa 麻点、 雅价的 际深度。
?
> 是部位上,测得弹痕占据的面积与要求强化喷
3. 3
PSSS
rate E 是以在被
受喷零件表面上呈现压坑丸的面积之间的比值,用百分
C
盖率用喷丸时间来计算。
超过100%的
L
[来源:JB/T10174-2000
0
4技术要求
4.1连杆材料 4.1. 1 化学成分
5
连杆的材料牌号和化学成分(熔炼务析)应符台表1的规定。
表1 发动机连杆毛坏化学成分(熔炼分析)
化学成分(质量分数)%
材料牌号
Cr
Mo
Ni
Mn
A1
Nb
C 0. 67 0. 15 0. 45
Si
P
S 0.060 0.10
V
N
≤ 0. 03 ≤ 0.012
≤ 0.045
C70S6
~
~
1
0.070 0.20 0.06 0.20 0. 04 0. 03 0.016 0.060 0.10 ≤ ≤ 0.10 ≤ 0.010
0. 73 0. 25 0. 65 0. 69 0. 15 0.80
≤
~
70MnVS4
~
~
0. 045 ~
A
A
0.070 0.20 0.06 0.20 0. 15 0. 03 0.016 0.040 0.10 ≤ ≤ 0.10 M 0.014 0.015
0. 73 0. 30 0. 90 0. 42 0. 40 0.90
M
46MnVS5 ~
~
0. 045 ~
~
0.08 0. 20 ~ 0. 03
~
0.022 0. 045
0. 48 0. 80 1. 30
0.070 0.30
0.20
2
T/CCMI13.1-2021
表1 发动机连杆毛坏化学成分(熔炼分析) (续)
材料牌号
化学成分 (质量分数)%
Si
Mn
Cr Mo
Ni
Nb
C
P
S
A1
N
V
低S: 0. 030 ~ 0. 10
0. 20 ~
≤ 0.015
0. 34 0. 60 0. 95 ≤ 0.045
M
≤
~
36MnVS4 ~
~
~
~ 0.020
0. 42 0.75 1. 05 0. 045 高S: 0. 25 0. 06 0. 20 0.35 0. 03
0.060
0.085
注1:C70、S70CVS1材料要求参照C70S6。 注2:38MnVS4、S36CVS2材料要求参照36MnVS4。 注3:46MnVS6材料要求参照46MnVS5。 注4:N元素允许偏差土0.002,S元素允许偏差土0.005,其它化学成份的允许偏差应符合GB/T222的规定
4.1.2非金属夹杂物及低倍组织
钢材的非金属夹杂物应按GB/T10561一2005的A法进行检验:夹杂物的判定应按GB/T10561一2005 附录A进行评级,结果应符合表2中的要求。钢材的横截面酸浸低倍试片上不应有肉眼可见的缩孔、气泡、裂纹、夹杂、翻皮及白点等缺陷,酸浸低倍组织按GB/T1979评级,其一般疏松、中心疏松和偏析均不应大于3级。
2非金属夹杂物 (级)
表2
B ≤2.0 ≤2.0
C ≤1. 0 ≤1.0
D ≤1. 0 ≤1.0
粗系细系
≤4.0 ≤3.0
4.1.3 3晶粒度
晶粒度按GB/T6394评级,应不粗于5级, 4.1.4 超声波检验
原材料进行超声波检验,按GB/T4162进行检验,缺陷分级应为A级以上。 4.1.5 5尺寸、外形、重量
尺寸、外形、重量按GB/T702中有关规定执行,尺寸精度、弯曲度按GB/T702一2017的1组规定执
行。 4.1.6其它
脱碳层、试验方法、表面质量、检验规则、验收、包装、标志、质量证明书等按GB/T3077中有关规定执行。
3
T/CCMI 13.1-2021 4. 2 连杆宏观组织
连杆流线方向应连续,金属晶粒流动应遵循锻造轮廓,沿着连杆中心线,并与连杆外形相符,不应有紊乱、扭曲、折叠、回流和间断现象。 4. 3 金相组织及脱碳层 4.3.1 连杆毛坏的基体组织应为均匀的珠光体和少量铁素体,晶粒度按GB/T6394评级,金相组织、 晶粒度和铁素体含量要求见表3。
表3 发动机连杆毛坏金相组织组织
牌号 C70S6 70MnVS4 46MnVS5 36MnVS4
铁素体含量不大于10% 不大于10% 不大于25% 不大于35%
晶粒度 5~8级 5~8级 5~8级 6~9级
铁素体+珠光体铁素体+珠光体铁素体+珠光体铁素体+珠光体
4.3.2 连杆毛坏表面不准许有完全脱碳, 部分脱碳层深度应不大于0.15mm。 4.4力学性能 4.4.1 连杆毛坏的硬度要求应符合表4的规定,同一连杆硬度差应不大于35HB。
表4 发动机连杆毛坏硬度值
牌号硬度值(HB)
C70S6 260~320
70MnVS4 310~370
46MnVS5 285~345
36MnVS4 285~345
4.4.2 连杆毛坏强度和塑性应符合表5规定,
表5 发动机连杆毛坏强度和塑性
屈服强度 Re1/Rpo. 2 (MPa) 不小于550 不小于650 不小于750 不小于750
抗拉强度 R (MPa) 900~1080 1000~1200 1000~1200 1000~1200
断后伸长率 A (%) 不小于10 不小于10 不小于8 不小于8
断面收缩率 Z (%) 20~40 20~40 25~45 30~50
牌号 C70S6 70MnVS4 46MnVS5 36MnVS4
4. 5 尺寸
连杆毛坏未注尺寸公差按GB/T12362中的精密级执行。 4.6 重量
胀断连杆毛坏重量应符合产品图样的规定,重量允许公差组别应符合表6规定。
4
T/CCMI13.1-2021
表6发动机连杆毛坏重量公差
组别 I 组 II 组 II组
重量公差 ± 1. 5% ±2. 0% ±2. 5%
4.7喷丸和内应力
4.7.1连杆毛坏应进行表面强化处理;推荐采用符合JB/T8354.1标准要求的钢丝切丸或JB/T8354.2 标准要求的高碳铸钢丸,其直径宜在0.8mm1.2mm范围内选择,硬度宜在HRC40~HRC48范围内选择。 4.7.2连杆毛坏喷丸强度应控制在0.3A~0.5A之间,表面残余压应力应不小于350MPa;表面覆盖率应达到200%,喷丸时间是其获得100%覆盖率所需时间的2倍。 4.7.3内应力用胀断位置切开后变形量(胀断位置切并前后直径差的最大值)来表示,应不大于 0.06mmc 4.8探伤
连杆毛坏应进行100%的荧光磁粉探伤。探伤后的连杆毛坏应进行退磁,退磁后连杆毛坏的剩余磁
场强度应不大于2×10T(2Gs)。 4.9表面质量 4.9.1连杆毛坏非加工表面:表面应光洁;不应有裂纹、折叠、结疤、折痕、氧化皮残留、锈迹及因金属未充满锻模而产生的缺陷;杆身部位不准许有切边拉伤。 4.9.2连杆毛坏待加工表面:若实际尺寸等于基本尺寸时,其表面缺陷深度为单边加工余量之半:若实际尺寸大于或小于基本尺寸时,其表面缺陷深度为单边加工余量之半加或减单边实际偏差值。对内表面尺寸取相反值。 4.10修复 4.10.1 连杆工字梁筋部圆角处的任何缺陷均不准许修复,其它部位表面缺陷允许修复,经修复后的痕迹应沿金属纤维轮廓方向并且应圆滑过渡,修复后的连杆应经过喷丸处理。 4.10.2客户对连杆的修复有特殊要求的,按客户要求执行。 4.11 禁用物质
连杆毛坏禁用物质应符合GB/T30512标准规定。
5 检验方法
5.1材料化学分析
连杆材料的化学分析方法按GB/T223、GB/T4336、GB/T20123及GB/T20124的规定。 5.2宏观组织
按GB/T226中的规定腐蚀后应采用目视或低倍放大镜检查。 5.3金相组织及脱碳层
5