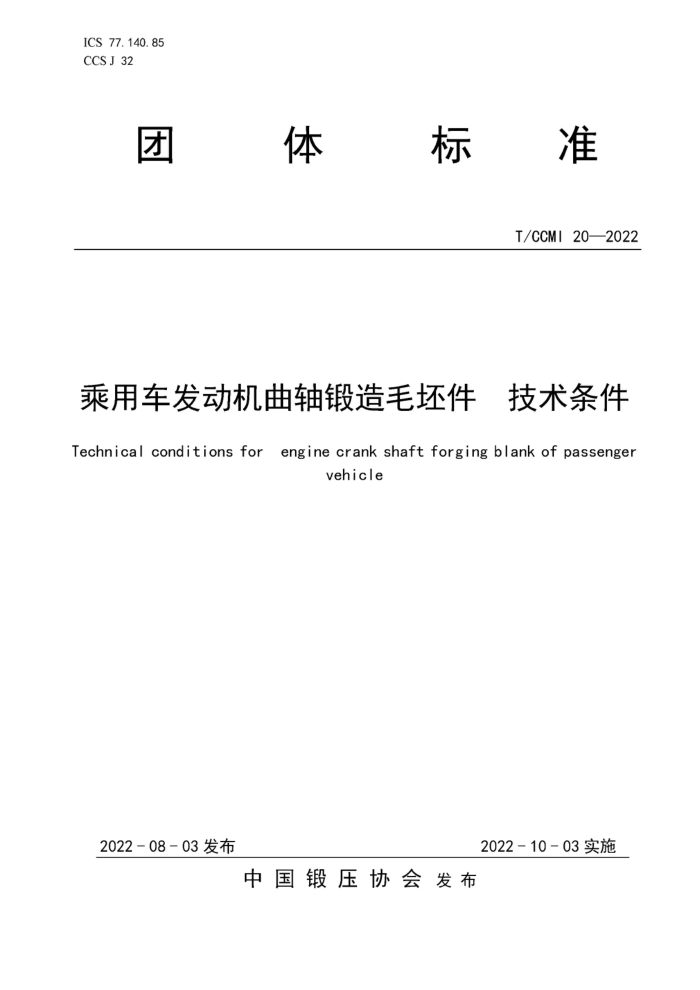
ICS 77.140.85 CCS J 32
体标准
团
T/CCMI 20—2022
乘用车发动机曲轴锻造毛坏件 技术条件 Technical conditions for engine crank shaft forging blank of passenger
vehicle
2022-08-03发布
2022-10-03实施
中国锻压协会发布
T/CCMI 202022
目次
前言范围
II
1
规范性引用文件 3术语和定义
2
2
技术要求, 5试验方法. 6 检验规则
4.
6
标志、包装、运输和贮存附录A(规范性) 乘用车发动机曲轴锻件各部位名称图解,
7
图A.1乘用车发动机曲轴锻件各部位名称,
表1非金属夹杂物级别、 表2酸浸低倍组织级别. 表3锻件热处理后力学性能和硬度推荐参数. 表4原材料入厂检验项目、取样数量、取样部位和试验方法表5锻件检验项目、取样数量及试验方法.
T/CCM1 20-2022
前言
本文件按照GB/T1.1一2020《标准化工作导则第1部分:标准化文件的结构和起草规则》的规定起草。
请注意本文件的某些内容可能涉及专利。本文件的发布机构不承担识别专利的责任。 本文件由重庆大江杰信锻造有限公司提出。 本文件由中国锻压协会归口。 本文件起草单位:重庆大江杰信锻造有限公司、桂林福达股份有限公司、辽宁五一八内燃机配件有
限公司、建龙北满特殊钢有限责任公司、西宁特殊钢股份有限公司、石家庄钢铁有限责任公司、一汽锻造(吉林)有限公司、重庆庆铃锻造有限公司、四川内江金鸿曲轴有限公司、浙江龙虎锻造有限公司。
本文件主要起草人:董旭刚、潘成海、黄斌、焉永才、陈列、王海龙、郝彦英、蔡宏伟、李丹、邓昭东、罗立辉、彭添、孙国峰、刘广磊、张振明、岳镇、陈瑞龙、陈建中。
本文件为首次发布。
II
T/CCMI 20-2022
乘用车发动机曲轴锻造毛坏件 技术条件
1范围
本文件规定了乘用车发动机曲轴锻造毛坏件(以下简称“锻件”)的技术要求、试验方法、检验规则、
标志、包装、运输和贮存。
本文件适用于重量不大于40kg的钢质锻件。 本文件适用于在热模锻压力机、电动螺旋压力机等锻压设备上生产的乘用车发动机曲轴锻件,采用
摩擦压力机、模锻锤等设备生产的亦可参照使用。
规范性引用文件
2
下列文件中的内容通过文中的规范性引用而构成本文件必不可少的条款。其中,注日期的引用文件,仅该日期版本适用于本文件;不注日期的引用文件,其最新版本(包括所有的修改单)适用于本文件。
GB/T 222 GB/T223(所有部分)钢铁及合金化学分析方法
钢的成品化学成分允许偏差
钢的脱碳层深度测定法
GB/T 224 GB/T 225 钢淬透性的末端淬火试验方法(Jominy试验) GB/T 226 钢的低倍组织及缺陷酸蚀检验法 GB/T228.1 金属材料拉伸试验第1部分:室温试验方法 GB/T 229 金属材料夏比摆锤冲击试验方法 GB/T231.1 金属材料布氏硬度试验第一部分:试验方法 GB/T 702 热轧钢棒尺寸、外形、重量及允许偏差 GB/T 1979 结构钢低倍组织缺陷评级图 GB/T 2975 钢及钢产品力学性能试验取样位置及试样制备 GB/T 30772015 合金结构钢 GB/T 4162-2008 锻轧钢棒超声检测方法 GB/T 4336 碳素钢和中低合金钢多元素含量的测定火花放电原子发射光谱法(常规法) GB/T5216-2014 保证淬透性结构钢 GB/T 6394-2017 金属平均晶粒度测定方法 GB/T 8541 锻压术语 GB/T10561-2005 钢中非金属夹杂物含量的测定标准评级图显微检验法 GB/T12361-2016 钢质模锻件通用技术条件 GB/T12362-2016 钢质模锻件公差及机械加工余量 GB/T13298 金属显微组织检验方法 GB/T13299-1991 钢的显微组织评定方法 GB/T13320-2007 钢质模锻件金相组织评级图及评定方法 GB/T15712-2016 非调质机械结构钢 GB/T19055 汽车发动机可靠性试验方法 GB/T 20066 钢和铁化学成分测定用试样的取样和制样方法
1
T/CCMI20-2022
GB/T30512 汽车禁用物质要求 JB/T 6729 内燃机曲轴、凸轮轴磁粉检测 JB/T12662 内燃机曲轴扭转疲劳试验方法 QC/T 637 汽车发动机曲轴弯曲疲劳试验方法
3术语和定义
GB/T8541界定的以及下列术语和定义适用于本文件。
3. 1
熔炼炉号 steel-smeltingfurnacenumber 某熔炼炉在一年内所炼的某 炉钢水的编号。
3. 2
热处理炉次在同一热处理炉内用同一工艺规范- 次或连续处理的同一种锻件为一热处理炉次。 [来源:GB/T1236]-2016,3.2]
treatmentfurnacenumber
heat
3. 3
S
生产批 manufacture batch 按同一工艺规范,在锻造过程中连续生产出的全部锻件为一生产批。 [来源:GB/12361-2016,3.3]
P
3.4
乘用车 passenger vehicle 在其设计和技术特性上主要用于载运乘客及其随身行李或临时物品的汽车,包括驾驶员座位在内最
多不超过9个座位。其也可以牵引一辆挂车。
4技术要求
4.1总则 4.1.1锻件应按需方要求的产品图样和技术文件制造,曲轴锻件各部位名称图解见附录A。 4.1.2锻件用原材料(以下简称“原材料”)加热时宜采用中频感应加热方式,加热时应不准许过烧。 原材料加热温度低于工艺温度上限的甩料件可重复加热三次,加热三次后仍甩料,直接报废;原材料加热温度高于工艺温度上限的直接报废。 4.1.3锻件热处理一般包括:正火、调质、控制冷却。调质钢锻件重复火次数不超过二次,回火次数不限。非调质钢锻件应采用控制冷却处理,客户指定正火处理除外。 4.2原材料 4.2.1原材料化学成分应符合GB/T3077-2015、GB/T5216-2014、GB/T15712-2016的规定或由供需双方协商确定。 4.2.2原材料化学成分允许偏差应符合GB/T222的规定,或由供需双方协商确定。 4.2.3原材料冶炼方法采用电炉冶炼或转炉冶炼并经炉外精炼,以热轧状态或退火状态交货,轧制压缩比不小于6。 4.2.4原材料外形、尺寸、重量及允许偏差,应符合GB/T702的规定,或由供需双方协商确定。
S
2
T/CCMI 202022
4.2.5原材料非金属夹杂物含量按GB/T10561-2005中5.2.1规定的A法进行检验,非金属夹杂物评级应符合表1规定。如需方有不同级别要求或有硫(S)含量要求的,其合格级别由供需双方协商确定。
表1非金属夹杂物级别
单位为级 Ds
B
C
A
D
非金属夹杂物调质钢非调质钢 4.2.6 原材料酸浸低倍组织级别按GB/T T1979的规定评定, 应符合表2的规定。 钢材的横截面酸浸低倍组织试片上或淬火断口试片 上不应有目视可见的缩孔、气泡、裂纹、夹杂、翻皮、 白点及晶界裂纹。
粗系 细系
细系
粗系
细系
粗系
细系
粗系
不大于
2. 0 2. 0 2. 0 1.0 1. 0 3. 0
1. 0 1. 0 1. 0
2.0 3. 0
1. 5 /
2.0
2. 0
1. 0
1.0
1. 0
C
C 表2 酸浸低倍组织级别 L 中心疏松
单位为级
般点状偏析
边缘点状偏析不准许
锭型偏析 ≤2.0
般疏松 ≤2.0
92.0
4.2.7原材料晶粒度按GB/T6394-2017的规定检验奥氏体晶粒度,级别不应粗于5级,晶粒度不均匀
R
级差不应大于3级。 4.2.8原材料脱碳层按GB/224的规定检验,其单边总脱碳层深度(铁素体+过渡区)推荐不宜大于钢材直径的0.8%,或由供需双方协商确定。 4.2.9原材料硬度按GB 231 1的规定检验,在钢材R/2位置测定,硬度不应大于280HBW,或由供
R
需双方协商确定。 4.2.10 原材料带状组织按GB/T1 13299-1991中5.3和附图3的规定评定,带状组织不应大于2.0级。 4.2.11 原材料淬透性按GB/T225的规定进行测定,应符合GB/T5216-2014规定,或由供需双方协商确定。 4.2.12原材料逐支进行超声波探伤检测,应符合GB/T4162-2008中8.2的表4质量等级中A等级(① 2.0mm平底孔)规定,或由供需双方协商确定。 4.2.13原材料禁用物质要求符合GB/T30512规定。 4.2.14确保原材料质量稳定性,应固化钢厂及钢材生产工艺流程。如需方有特殊要求,由供需双方协商确定。 4.2.15未尽事宜按GB/T3077-2015、GB/T5216-2014和GB/T15712-2016规定执行,或由供需双方协商确定。 4.3锻件 4.3.1锻件形状、尺寸及精度 4.3.1.1锻件的形状、尺寸按产品图样执行,锻件主轴径厚度尺寸推荐作为控制锻件厚度尺寸的重要特性;锻件尺寸公差宜按GB/T12362-2016的3.2中表2精密级选取,或由供需双方协商确定。 4.3.1.2锻件拔模斜度1°~3°,推荐1.5°,或由供需双方协商确定。 4.3.1.3锻件重量不大于25kg时,锻件错差不应大于0.8mm;锻件重量大于25kg时,锻件错差不应大于 1.2mm;或由供需双方协商确定。 4.3.1.4锻件直线度不应大于0.75mm/500mm,或由供需双方协商确定。
3
T/CCMI 20-2022 4.3.2锻件表面质量 4.3.2.1锻件基准面上不应有毛刺等影响定位精度的缺陷。锻件其他部位毛刺、飞边的残余高度:锻件重量不大于25kg时,非加工面不应大于0.8mm,加工面不应大于1.2mm;锻件重量大于25kg时,非加工面不应大于1.2mm,加工面不应大于1.5mm;或由供需双方协商确定。 4.3.2.2锻件表面不应有折叠、裂纹、分层等影响强度的缺陷,不应用压整和补焊的方法消除此类缺陷。 4.3.2.3锻件非加工表面上的凹坑、麻点、碰伤等缺陷深度不应大于厚度公差的1/3。 4.3.2.4锻件表面上的折叠、裂纹等缺陷应打磨清除,打磨部位应圆滑过渡,打磨宽度不应小于打磨深度的6倍,打磨长度应在两端超出缺陷长度3mm以上,非加工面打磨深度不得大于厚度公差的1/3,加工面上打磨深度不应大于毛坏实际加工余量的1/2,打磨后应进行探伤和抛丸处理。不应采用压整和焊补的方法消除锻件缺陷。 4.3.2.5锻件表面总脱碳层深度不应大于0.5mm,或由供需双方协商确定。 4.3.2.6锻件应采用直径≤1.2mm的钢丝切断丸或铸钢丸进行抛丸处理,抛丸覆盖率100%。 4.3.2.7锻件抛丸后应100%磁粉探伤,探伤后应进行退磁处理,剩磁量不应大于5Gs。 4.3.3锻造流线
锻造流线应与锻件外轮廓相符,呈纤维状分布,不应出现流线不顺、涡流和穿流的情况。锻造流线试样应沿每个曲拐的主轴颈和连杆颈中心连线方向制取。 4.3.4金相组织 4.3.4.1正火处理的锻件,晶粒度不应粗于GB/T6394-2017中规定的5级,同支产品的晶粒度不均匀级差不应大于3级,金相组织为珠光体+铁素体。 4.3.4.2调质处理的锻件,晶粒度不应粗于GB/T6394-2017中规定的5级,同支产品的晶粒度不均级差不应大于3级,金相组织应符合GB/T13320-2007中6.3规定的1级~4级。 4.3.4.3非调质钢锻件经控制冷却处理后,晶粒度不应粗于GB/T6394-2017中规定的3级,金相组织为珠光体+铁素体,允许有少量贝氏体。 4.3.5力学性能和硬度
常用锻件热处理后力学性能和硬度推荐参数见表3。
表3锻件热处理后力学性能和硬度推荐参数
屈服强度 断后伸长率 断面收缩率 冲击功 Ra2 MPa
硬度 HBW 250~310
抗拉强度 R MPa ≥820 ≥850 ≥850 ≥820
牌号 40Cr 40CrNiMoA 调质 42CrMo
热处理调质
4% ≥12 ≥12 ≥12 ≥12 ≥12 ≥12 ≥10 ≥10 ≥8
2% ≥45 ≥45 ≥45 ≥45 ≥25 ≥25 ≥20
ku2 J * ≥63 260~310 ≥63 260~310 ≥40 240~300
≥620 ≥680 ≥680 ≥630 ≥580 ≥450 ≥450 / ≥440
调质调质控冷 800~1000 控冷
37CrS4 38MnVS6 C38N2 49MnVS3 48MnV S45CVS
245~298 222~266 226~280 207~277 229~285
7 /
750~950 780~950 ≥698 ≥735
控冷控冷控冷
≥20
4
ICS 77.140.85 CCS J 32
体标准
团
T/CCMI 20—2022
乘用车发动机曲轴锻造毛坏件 技术条件 Technical conditions for engine crank shaft forging blank of passenger
vehicle
2022-08-03发布
2022-10-03实施
中国锻压协会发布
T/CCMI 202022
目次
前言范围
II
1
规范性引用文件 3术语和定义
2
2
技术要求, 5试验方法. 6 检验规则
4.
6
标志、包装、运输和贮存附录A(规范性) 乘用车发动机曲轴锻件各部位名称图解,
7
图A.1乘用车发动机曲轴锻件各部位名称,
表1非金属夹杂物级别、 表2酸浸低倍组织级别. 表3锻件热处理后力学性能和硬度推荐参数. 表4原材料入厂检验项目、取样数量、取样部位和试验方法表5锻件检验项目、取样数量及试验方法.
T/CCM1 20-2022
前言
本文件按照GB/T1.1一2020《标准化工作导则第1部分:标准化文件的结构和起草规则》的规定起草。
请注意本文件的某些内容可能涉及专利。本文件的发布机构不承担识别专利的责任。 本文件由重庆大江杰信锻造有限公司提出。 本文件由中国锻压协会归口。 本文件起草单位:重庆大江杰信锻造有限公司、桂林福达股份有限公司、辽宁五一八内燃机配件有
限公司、建龙北满特殊钢有限责任公司、西宁特殊钢股份有限公司、石家庄钢铁有限责任公司、一汽锻造(吉林)有限公司、重庆庆铃锻造有限公司、四川内江金鸿曲轴有限公司、浙江龙虎锻造有限公司。
本文件主要起草人:董旭刚、潘成海、黄斌、焉永才、陈列、王海龙、郝彦英、蔡宏伟、李丹、邓昭东、罗立辉、彭添、孙国峰、刘广磊、张振明、岳镇、陈瑞龙、陈建中。
本文件为首次发布。
II
T/CCMI 20-2022
乘用车发动机曲轴锻造毛坏件 技术条件
1范围
本文件规定了乘用车发动机曲轴锻造毛坏件(以下简称“锻件”)的技术要求、试验方法、检验规则、
标志、包装、运输和贮存。
本文件适用于重量不大于40kg的钢质锻件。 本文件适用于在热模锻压力机、电动螺旋压力机等锻压设备上生产的乘用车发动机曲轴锻件,采用
摩擦压力机、模锻锤等设备生产的亦可参照使用。
规范性引用文件
2
下列文件中的内容通过文中的规范性引用而构成本文件必不可少的条款。其中,注日期的引用文件,仅该日期版本适用于本文件;不注日期的引用文件,其最新版本(包括所有的修改单)适用于本文件。
GB/T 222 GB/T223(所有部分)钢铁及合金化学分析方法
钢的成品化学成分允许偏差
钢的脱碳层深度测定法
GB/T 224 GB/T 225 钢淬透性的末端淬火试验方法(Jominy试验) GB/T 226 钢的低倍组织及缺陷酸蚀检验法 GB/T228.1 金属材料拉伸试验第1部分:室温试验方法 GB/T 229 金属材料夏比摆锤冲击试验方法 GB/T231.1 金属材料布氏硬度试验第一部分:试验方法 GB/T 702 热轧钢棒尺寸、外形、重量及允许偏差 GB/T 1979 结构钢低倍组织缺陷评级图 GB/T 2975 钢及钢产品力学性能试验取样位置及试样制备 GB/T 30772015 合金结构钢 GB/T 4162-2008 锻轧钢棒超声检测方法 GB/T 4336 碳素钢和中低合金钢多元素含量的测定火花放电原子发射光谱法(常规法) GB/T5216-2014 保证淬透性结构钢 GB/T 6394-2017 金属平均晶粒度测定方法 GB/T 8541 锻压术语 GB/T10561-2005 钢中非金属夹杂物含量的测定标准评级图显微检验法 GB/T12361-2016 钢质模锻件通用技术条件 GB/T12362-2016 钢质模锻件公差及机械加工余量 GB/T13298 金属显微组织检验方法 GB/T13299-1991 钢的显微组织评定方法 GB/T13320-2007 钢质模锻件金相组织评级图及评定方法 GB/T15712-2016 非调质机械结构钢 GB/T19055 汽车发动机可靠性试验方法 GB/T 20066 钢和铁化学成分测定用试样的取样和制样方法
1
T/CCMI20-2022
GB/T30512 汽车禁用物质要求 JB/T 6729 内燃机曲轴、凸轮轴磁粉检测 JB/T12662 内燃机曲轴扭转疲劳试验方法 QC/T 637 汽车发动机曲轴弯曲疲劳试验方法
3术语和定义
GB/T8541界定的以及下列术语和定义适用于本文件。
3. 1
熔炼炉号 steel-smeltingfurnacenumber 某熔炼炉在一年内所炼的某 炉钢水的编号。
3. 2
热处理炉次在同一热处理炉内用同一工艺规范- 次或连续处理的同一种锻件为一热处理炉次。 [来源:GB/T1236]-2016,3.2]
treatmentfurnacenumber
heat
3. 3
S
生产批 manufacture batch 按同一工艺规范,在锻造过程中连续生产出的全部锻件为一生产批。 [来源:GB/12361-2016,3.3]
P
3.4
乘用车 passenger vehicle 在其设计和技术特性上主要用于载运乘客及其随身行李或临时物品的汽车,包括驾驶员座位在内最
多不超过9个座位。其也可以牵引一辆挂车。
4技术要求
4.1总则 4.1.1锻件应按需方要求的产品图样和技术文件制造,曲轴锻件各部位名称图解见附录A。 4.1.2锻件用原材料(以下简称“原材料”)加热时宜采用中频感应加热方式,加热时应不准许过烧。 原材料加热温度低于工艺温度上限的甩料件可重复加热三次,加热三次后仍甩料,直接报废;原材料加热温度高于工艺温度上限的直接报废。 4.1.3锻件热处理一般包括:正火、调质、控制冷却。调质钢锻件重复火次数不超过二次,回火次数不限。非调质钢锻件应采用控制冷却处理,客户指定正火处理除外。 4.2原材料 4.2.1原材料化学成分应符合GB/T3077-2015、GB/T5216-2014、GB/T15712-2016的规定或由供需双方协商确定。 4.2.2原材料化学成分允许偏差应符合GB/T222的规定,或由供需双方协商确定。 4.2.3原材料冶炼方法采用电炉冶炼或转炉冶炼并经炉外精炼,以热轧状态或退火状态交货,轧制压缩比不小于6。 4.2.4原材料外形、尺寸、重量及允许偏差,应符合GB/T702的规定,或由供需双方协商确定。
S
2
T/CCMI 202022
4.2.5原材料非金属夹杂物含量按GB/T10561-2005中5.2.1规定的A法进行检验,非金属夹杂物评级应符合表1规定。如需方有不同级别要求或有硫(S)含量要求的,其合格级别由供需双方协商确定。
表1非金属夹杂物级别
单位为级 Ds
B
C
A
D
非金属夹杂物调质钢非调质钢 4.2.6 原材料酸浸低倍组织级别按GB/T T1979的规定评定, 应符合表2的规定。 钢材的横截面酸浸低倍组织试片上或淬火断口试片 上不应有目视可见的缩孔、气泡、裂纹、夹杂、翻皮、 白点及晶界裂纹。
粗系 细系
细系
粗系
细系
粗系
细系
粗系
不大于
2. 0 2. 0 2. 0 1.0 1. 0 3. 0
1. 0 1. 0 1. 0
2.0 3. 0
1. 5 /
2.0
2. 0
1. 0
1.0
1. 0
C
C 表2 酸浸低倍组织级别 L 中心疏松
单位为级
般点状偏析
边缘点状偏析不准许
锭型偏析 ≤2.0
般疏松 ≤2.0
92.0
4.2.7原材料晶粒度按GB/T6394-2017的规定检验奥氏体晶粒度,级别不应粗于5级,晶粒度不均匀
R
级差不应大于3级。 4.2.8原材料脱碳层按GB/224的规定检验,其单边总脱碳层深度(铁素体+过渡区)推荐不宜大于钢材直径的0.8%,或由供需双方协商确定。 4.2.9原材料硬度按GB 231 1的规定检验,在钢材R/2位置测定,硬度不应大于280HBW,或由供
R
需双方协商确定。 4.2.10 原材料带状组织按GB/T1 13299-1991中5.3和附图3的规定评定,带状组织不应大于2.0级。 4.2.11 原材料淬透性按GB/T225的规定进行测定,应符合GB/T5216-2014规定,或由供需双方协商确定。 4.2.12原材料逐支进行超声波探伤检测,应符合GB/T4162-2008中8.2的表4质量等级中A等级(① 2.0mm平底孔)规定,或由供需双方协商确定。 4.2.13原材料禁用物质要求符合GB/T30512规定。 4.2.14确保原材料质量稳定性,应固化钢厂及钢材生产工艺流程。如需方有特殊要求,由供需双方协商确定。 4.2.15未尽事宜按GB/T3077-2015、GB/T5216-2014和GB/T15712-2016规定执行,或由供需双方协商确定。 4.3锻件 4.3.1锻件形状、尺寸及精度 4.3.1.1锻件的形状、尺寸按产品图样执行,锻件主轴径厚度尺寸推荐作为控制锻件厚度尺寸的重要特性;锻件尺寸公差宜按GB/T12362-2016的3.2中表2精密级选取,或由供需双方协商确定。 4.3.1.2锻件拔模斜度1°~3°,推荐1.5°,或由供需双方协商确定。 4.3.1.3锻件重量不大于25kg时,锻件错差不应大于0.8mm;锻件重量大于25kg时,锻件错差不应大于 1.2mm;或由供需双方协商确定。 4.3.1.4锻件直线度不应大于0.75mm/500mm,或由供需双方协商确定。
3
T/CCMI 20-2022 4.3.2锻件表面质量 4.3.2.1锻件基准面上不应有毛刺等影响定位精度的缺陷。锻件其他部位毛刺、飞边的残余高度:锻件重量不大于25kg时,非加工面不应大于0.8mm,加工面不应大于1.2mm;锻件重量大于25kg时,非加工面不应大于1.2mm,加工面不应大于1.5mm;或由供需双方协商确定。 4.3.2.2锻件表面不应有折叠、裂纹、分层等影响强度的缺陷,不应用压整和补焊的方法消除此类缺陷。 4.3.2.3锻件非加工表面上的凹坑、麻点、碰伤等缺陷深度不应大于厚度公差的1/3。 4.3.2.4锻件表面上的折叠、裂纹等缺陷应打磨清除,打磨部位应圆滑过渡,打磨宽度不应小于打磨深度的6倍,打磨长度应在两端超出缺陷长度3mm以上,非加工面打磨深度不得大于厚度公差的1/3,加工面上打磨深度不应大于毛坏实际加工余量的1/2,打磨后应进行探伤和抛丸处理。不应采用压整和焊补的方法消除锻件缺陷。 4.3.2.5锻件表面总脱碳层深度不应大于0.5mm,或由供需双方协商确定。 4.3.2.6锻件应采用直径≤1.2mm的钢丝切断丸或铸钢丸进行抛丸处理,抛丸覆盖率100%。 4.3.2.7锻件抛丸后应100%磁粉探伤,探伤后应进行退磁处理,剩磁量不应大于5Gs。 4.3.3锻造流线
锻造流线应与锻件外轮廓相符,呈纤维状分布,不应出现流线不顺、涡流和穿流的情况。锻造流线试样应沿每个曲拐的主轴颈和连杆颈中心连线方向制取。 4.3.4金相组织 4.3.4.1正火处理的锻件,晶粒度不应粗于GB/T6394-2017中规定的5级,同支产品的晶粒度不均匀级差不应大于3级,金相组织为珠光体+铁素体。 4.3.4.2调质处理的锻件,晶粒度不应粗于GB/T6394-2017中规定的5级,同支产品的晶粒度不均级差不应大于3级,金相组织应符合GB/T13320-2007中6.3规定的1级~4级。 4.3.4.3非调质钢锻件经控制冷却处理后,晶粒度不应粗于GB/T6394-2017中规定的3级,金相组织为珠光体+铁素体,允许有少量贝氏体。 4.3.5力学性能和硬度
常用锻件热处理后力学性能和硬度推荐参数见表3。
表3锻件热处理后力学性能和硬度推荐参数
屈服强度 断后伸长率 断面收缩率 冲击功 Ra2 MPa
硬度 HBW 250~310
抗拉强度 R MPa ≥820 ≥850 ≥850 ≥820
牌号 40Cr 40CrNiMoA 调质 42CrMo
热处理调质
4% ≥12 ≥12 ≥12 ≥12 ≥12 ≥12 ≥10 ≥10 ≥8
2% ≥45 ≥45 ≥45 ≥45 ≥25 ≥25 ≥20
ku2 J * ≥63 260~310 ≥63 260~310 ≥40 240~300
≥620 ≥680 ≥680 ≥630 ≥580 ≥450 ≥450 / ≥440
调质调质控冷 800~1000 控冷
37CrS4 38MnVS6 C38N2 49MnVS3 48MnV S45CVS
245~298 222~266 226~280 207~277 229~285
7 /
750~950 780~950 ≥698 ≥735
控冷控冷控冷
≥20
4