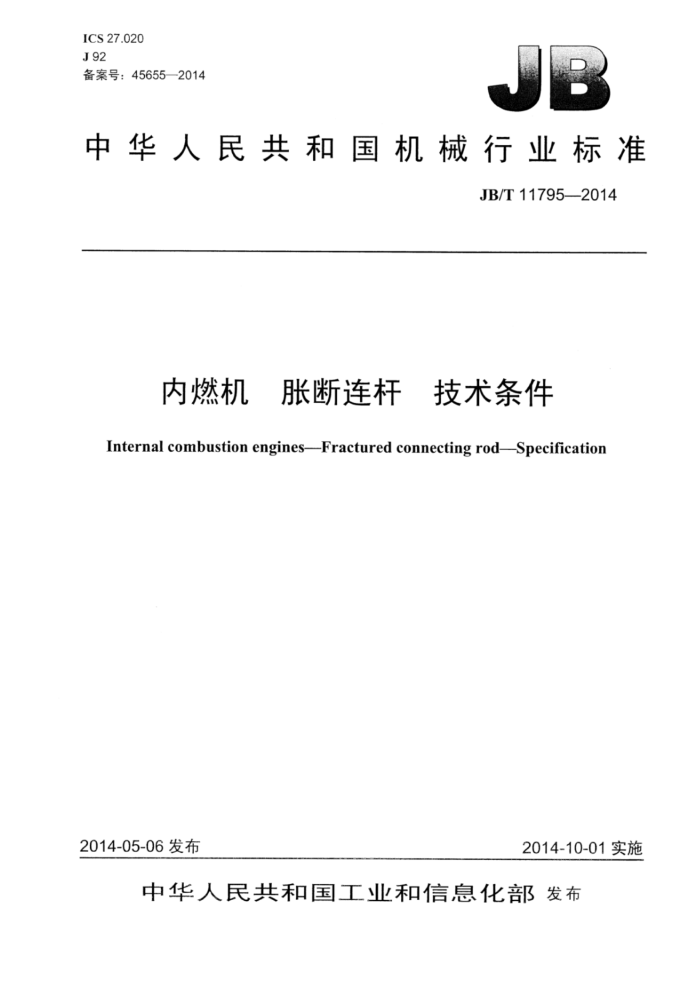
ICS 27.020 J92 备案号:45655—2014
中华人民共和国机械行业标准
JB/T11795—2014
内燃机 胀断连杆 技术条件 Internal combustion engines--Fractured connecting rodSpecification
2014-10-01实施
2014-05-06发布
中华人民共和国工业和信息化部发布
JB/T117952014
目 次
前言
.I
范围. 2 规范性引用文件 3术语和定义
4 技术要求 5 检验方法 6 检验规则 7标志、包装、运输和贮存附录A(资料性附录)牌号对照表
3
.8
.......I....
..10
JB/T11795—2014
前言
本标准按照GB/T1.1一2009给出的规则起草。 本标准由中国机械工业联合会提出。 本标准由全国内燃机标准化技术委员会(SAC/TC177)归口。 本标准起草单位:云南西仪工业股份有限公司、天润曲轴股份有限公司、承德苏垦银河连杆股份有
限公司、上海内燃机研究所、潍柴动力股份有限公司、常州远东连杆集团有限公司。
本标准主要起草人:邓伟、丛建臣、赵明好、朱海青、王建平、邱建平、冀会平、孙军、张勇、林国华、葛全慧、陈兰兰、杨建辉、沈红节。
本标准为首次发布。
II
JB/T11795—2014
内燃机胀断连杆技术条件
1范围
本标准规定了往复式内燃机胀断连杆(包括连杆体、连杆盖和连杆衬套)的术语和定义、技术要求、 检验方法、检验规则及标志、包装、运输和贮存
本标准适用于气缸直径不大于200mm的往复式内燃机用胀断连杆(以下简称胀断连杆)。
2规范性引用文件
下列文件对于本文件的应用是必不可少的。凡是注日期的引用文件,仅注日期的版本适用于本文件。 凡是不注日期的引用文件,其最新版本(包括所有的修改单)适用于本文件。
GB/T222 钢的成品化学成分充许偏差 GB/T223.5钢铁酸溶硅和全硅含量的测定还原型硅钼酸盐分光光度法 GB/T223.12 钢铁及合金化学分析方法碳酸钠分离-二苯碳酰二肼光度法测定铬量 GB/T223.14钢铁及合金化学分析方法钼试剂萃取光度法测定钒含量 GB/T223.26 钢铁及合金钼含量的测定硫氰酸盐分光光度法 GB/T223.37 钢铁及合金化学分析方法蒸馏分离-靛酚蓝光度法测定氮量 GB/T223.53 钢铁及合金化学分析方法火焰原子吸收分光光度法测定铜量 GB/T223.54 钢铁及合金化学分析方法火焰原子吸收分光光度法测定镍量 GB/T223.58 钢铁及合金化学分析方法亚砷酸钠-亚硝酸钠滴定法测定锰量 GB/T223.59 钢铁及合金磷含量的测定铋磷蓝分光光度法和锦磷钼蓝分光光度法 GB/T223.60 钢铁及合金化学分析方法高氯酸脱水重量法测定硅含量 GB/T223.61 钢铁及合金化学分析方法磷钼酸铵容量法测定磷量 GB/T223.62 钢铁及合金化学分析方法乙酸丁酯萃取光度法测定磷量 GB/T223.63 钢铁及合金化学分析方法高碘酸钠(钾)光度法测定锰量 GB/T223.64 钢铁及合金锰含量的测定火焰原子吸收光谱法 GB/T223.67 钢铁及合金硫含量的测定次甲基蓝分光光度法 GB/T223.68 钢铁及合金化学分析方法管式炉内燃烧后碘酸钾滴定法测定硫含量 GB/T223.69 钢铁及合金碳含量的测定管式炉内燃烧后气体容量法 GB/T223.71 钢铁及合金化学分析方法管式炉内燃烧后重量法测定碳含量 GB/T223.72 钢铁及合金硫含量的测定重量法 GB/T223.76 钢铁及合金化学分析方法火焰原子吸收光谱法测定钒量 GB/T 223.79 钢铁多元素含量的测定X-射线荧光光谱法(常规法) GB/T223.81 钢铁及合金总铝和总硼含量的测定微波消解-电感耦合等离子体质谱法 GB/T223.85 钢铁及合金硫含量的测定感应炉燃烧后红外吸收法 GB/T223.86 钢铁及合金总碳含量的测定感应炉燃烧后红外吸收法 GB/T224钢的脱碳层深度测定法 GB/T228.1 金属材料主 拉伸试验第1部分:室温试验方法 GB/T231.1 金属材料布氏硬度试验第1部分:试验方法
1
JB/T117952014
GB/T1184一1996形状和位置公差未注公差值 GB/T1800.1 产品几何技术规范(GPS)极限与配合:第1部分:公差、偏差和配合的基础 GB/T1958 产品几何量技术规范(GPS)形状和位置公差检测规定 GB/T2828.1 计数抽样检验程序第1部分:按接收质量限(AQL)检索的逐批检验抽样计划 GB/T3075 金属材料疲劳试验轴向力控制方法 GB/T3821 中小功率内燃机清洁度测定方法 GB/T4336 碳素钢和中低合金钢火花源原子发射光谱分析方法(常规法) GB/T6394 金属平均晶粒度测定方法 GB/T12362 2003 钢质模锻件公差及机械加工余量 GB/T24176 金属材料疲劳试验数据统计方案与分析方法 JB/T6721.2 内燃机连杆第2部分:磁粉检测 JB/T7292.1 内燃机衬套连杆衬套技术条件 JB/T7293.2 内燃机螺栓与螺母第2部分:连杆螺栓技术条件 JB/T9764 内燃机卷制连杆衬套技术条件
3术语和定义
下列术语和定义适用于本文件。
3.1
胀断连杆 fractured connecting rod 利用特种钢材的裂解特性,通过连杆大头孔内的预制应力槽获得裂解扩展源,使用特定方法控制裂
解痕迹的扩展方向,使连杆体与连杆盖脆性断裂分离,加工组装后获得的连杆,也称裂解连杆或胀断裂解连杆。 3.2
胀断断口宽度fractured zone 分别以胀断连杆外表面断口痕迹的波峰最高点与波谷最低点为基准,且平行于与胀断连杆大小孔中
心连线成α(0<α≤90°)角的连杆外表面区域,如图1所示。
A4 W
大大
A
说明:
一胀断断口与大小孔中心连线的夹角: W 一胀断断口宽度
图 1
2
JB/T117952014
等缺陷:采用辊锻制坏时其纤维方向应沿连杆中心线,并与外形相符,不得有紊乱、间断等现象。 4.6金相组织 4.6.1胀断连杆体和连杆盖的基体组织应为均匀的珠光体和少量铁素体,铁素体应沿晶界断续分布,不允许出现连续网状铁素体,铁素体含量不大于10%;奥氏体晶粒度按GB/T6394评级,不低于4级。 4.6.2胀断连杆体和连杆盖允许在表面有轻微的脱碳现象。表面总脱碳层深度应不大于0.25mm,完全脱碳层深度应不大于0.1mm。 4.7 表面粗糙度
胀断连杆各主要加工表面粗糙度Ra值应符合表3的规定。
表3
单位为微米
部位胀断连杆衬套孔胀断连杆大头孔
表面粗糙度Ra
≤0.63 ≤0.8 ≤1.25 ≤0.63 ≤1.6 ≤3.2
加衬套不加衬套
胀断连杆小头孔
胀断连杆大头两端面
螺栓孔支撑面
4.8 3尺寸公差
胀断连杆各主要加工部位尺寸公差的公差等级应不低于表4的规定。
表4
位置胀断连杆衬套孔胀断连杆大头孔胀断连杆小头孔
公差等级
IT6 IT6 IT7 IT8
胀断连杆大小头孔中心距
公差等级按GB/T1800.1的规定。
4.9形状和位置公差 4.9.1胀断连杆小头孔及胀断连杆衬套孔轴线对胀断连杆大头孔轴线的平行度按GB/T1184一1996中下列公差等级制造:
a)在大、小头孔轴线所决定的平面的垂直方向上的平行度公差不低于6级; b)在大、小头孔轴线所决定的平面的平行方向上的平行度公差不低于7级。
4.9.2胀断连杆下列各加工部位的形状和位置公差按GB/T1184一1996中下列公差等级制造:
a)胀断连杆衬套孔的圆柱度公差不低于6级; b)胀断连杆大头孔的圆柱度公差不低于6级; c)胀断连杆小头孔的圆柱度公差不低于7级; d胀断连杆大头两端面对胀断连杆大头孔轴线的垂直度公差不低于8级。
4
JB/T11795—2014
4.10表面质量 4.10.1胀断连杆的表面不允许有毛刺、磕碰伤痕及锈蚀等缺陷。 4.10.2胀断连杆非加工表面应光洁,不允许有裂纹、折叠、折痕、结疤、氧化皮等缺陷。杆身部位不允许有切边拉伤,分模面飞边高度应不大于0.5mm。允许有总数不多于2个,直径不大于5mm 深度公差为厚度尺寸公差三分之一的凹坑,但位置不得在同一横截面上。胀断连杆表面缺陷允许在尺寸公差范围内修整,经修整的部位应圆滑过渡,打磨宽度不小于深度的6倍,长度应在两端超出缺陷长度3mm以上,其深度应符合GB/T12362一2003的要求。 4.10.3胀断连杆毛坏不允许有因金属锻造未充满而产生的缺陷,不允许焊补。 4.10.4胀断连杆毛坏应经喷丸或其他表面强化处理。 4.11断口质量 4.11.1胀断断面应为脆性断裂面,不允许有明显的纤维状塑性断裂区域。 4.11.2·胀断断面经清渣处理后,不允许有松动的金属颗粒。 4.11.3胀断断口宽度W不大于4mm,且偏移向胀断连杆体或胀断连杆盖均不大于2mm。 4.11.4沿胀断断口痕迹不允许出现长度超过2mm的次级裂纹、螺栓孔内壁不允许有任何形式的裂纹。 4.11.5胀断结合面区域a×b小于或等于35mm×20mm时,沿胀断断口痕迹允许出现不多于两处,且长度不大于5mm、宽度不大于2mm的胀断掉渣;胀断结合面区域a×b大于35mm×20mm时,沿胀断断口痕迹允许出现不多于两处,且长度不大于12mm、宽度不大于3mm的胀断掉渣。沿胀断断口痕迹出现两处胀断掉渣时,不允许位于同一侧,胀断掉渣不允许出现在大孔内壁及连杆机加工平面位置。 4.11.6在胀断断面不允许出现高度大于2mm的台阶。 4.11.7大孔内壁胀断断口位置如残留应力槽,其深度不大于0.2mm。 4.12装配要求
装配后胀断连杆体与连杆盖错移量不大于0.05mm 4.13质量及质量配组
胀断连杆质量及质量分组、整台内燃机上同一组胀断连杆的质量差,应符合产品图样的规定 4.14缺陷磁痕
胀断连杆经磁粉检测出的缺陷磁痕允许极限值应符合JB/T6721.2的规定。 4.15清洁度
胀断连杆未拆解状态下的清洁度限值应符合产品图样或技术文件的规定。产品图样或技术文件没有规定的,每支胀断连杆清洗下来的杂质质量不大于6mg,最大颗粒长度不大于1mm。 4.16疲劳寿命
胀断连杆在循环基数10°次(长期服役)下,失效概率应小于万分之五。
5检验方法
5.1化学分析
胀断连杆材料的化学分析方法按GB/T223或GB/T4336的规定。仲裁时,按GB/T223的规定。
5