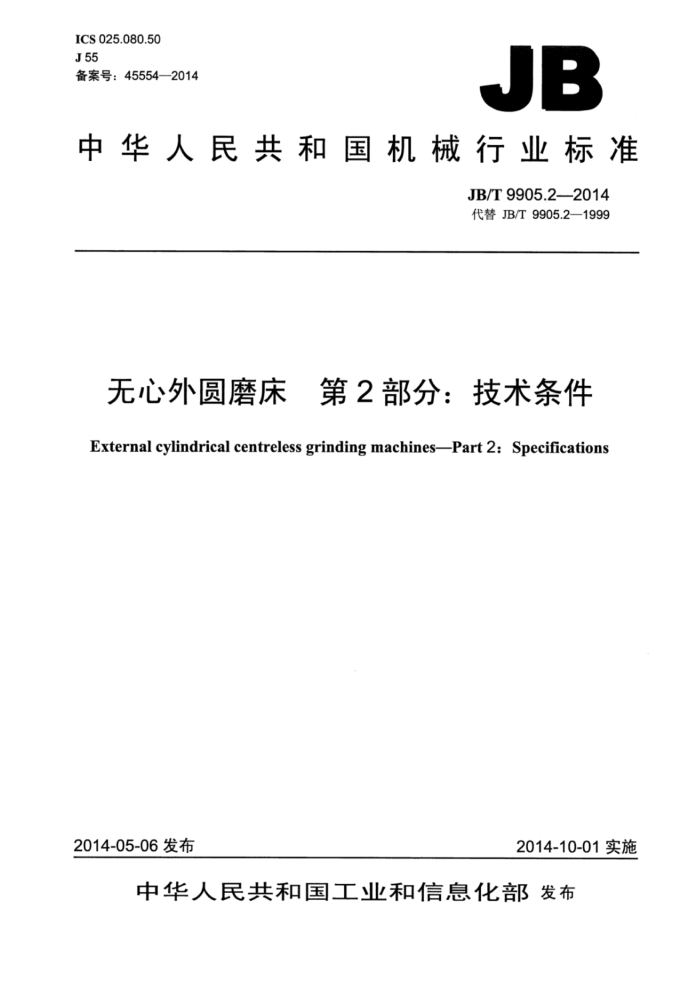
ICS025.080.50 J55 备案号:45554—2014
JB
中华人民共和国机械行业标准
JB/T9905.2—2014 代替JB/T9905.2—1999
无心外圆磨床 第2部分:技术条件
External cylindrical centreless grinding machinesPart 2: Specifications
2014-10-01实施
2014-05-06发布
中华人民共和国工业和信息化部发布
JB/T9905.2—2014
目 次
前言.. 1 范围 2 规范性引用文件 3 一般要求.
U
附件与工具.. 安全卫生..
X
5
6 加工和装配质量
机床空运转试验. 7.1 温度和温升试验. 7.2 主运动和进给运动的检验, 7.3 空运转功率试验 7.4机床的功能试验.. 7.5机床的连续空运转试验 7.6其他.. 8机床负荷试验(抽查) 9机床精度检验 10直线坐标最小设定单位试验.
-
.
10.1试验方法 10.2 误差的计算方法, 10.3 允差... 10.4 检验工具
JB/T9905.2—2014
前言
JB/T9905《无心外圆磨床》分为三个部分:
-第1部分:型式与参数;第2部分:技术条件; -第3部分:高精度机床精度检验。
本部分为JB/T9905的第2部分。 本部分按照GB/T1.1——2009给出的规则起草。 本部分代替JB/T9905.2—1999《无心外圆磨床技术条件》,与JB/T9905.2—1999相比主要技术变
化如下:
-增加机床精度等级的说明(见3.2);增加了机床噪声的考核要求(见5.3);增加了采用滚动轴承对砂轮架部件内部的清洁度考核要求(见6.9);一增加了数控磨床的数控考核要求(见第7章、第10章);增加了机床的连续空运转试验(见7.5):修改了“规范性引用文件”(见第2章,1999年版的第2章》:一“附件与工具”内容改为“由设计根据机床结构特点进行选择”(见第4章,1999年版的第4章);将手轮、手柄操纵力移至“安全卫生”章节,并进行了量化(见5.4,1999年版的6.7)。
本部分由中国机械工业联合会提出。 本部分由全国金属切削机床标准化技术委员会(SAC/TC22)归口。 本部分起草单位:无锡机床股份有限公司。 本部分主要起草人:夏红、顾越苏、张宏兵、吕洪明。 本部分所代替标准的历次版本发布情况为:
-JB/T2860—1981、JB/T2860—1987; -JB/T9905.21999.
II
JB/T9905.2—2014
无心外圆磨床第2部分:技术条件
1范围
JB/T9905的本部分规定了一般用途的无心外圆磨床的制造与验收的要求。 本部分适用于最大磨削直径20mm~400mm,砂轮宽度100mm~600mm的一般用途的普通级和
高精度级的无心外圆磨床(以下简称机床)。
2规范性引用文件
下列文件对于本文件的应用是必不可少的。凡是注日期的引用文件,仅注日期的版本适用于本文件。凡是不注日期的引用文件,其最新版本(包括所有的修改单)适用于本文件。
GB/T4681-2007 无心外圆磨床精度检验 GB5226.1—2008 机械电气安全 机械电气设备第1部分:通用技术条件 GB/T9061—2006 金属切削机床 通用技术条件 GB15760—2004 金属切削机床安全防护通用技术条件 GB/T16769—2008 金属切削机床噪声声压级测量方法 GB/T23572—2009 金属切削机床液压系统通用技术条件 GB/T25372—2010 金属切削机床 精度分级 GB/T25373—2010 金属切削机床 装配通用技术条件 GB/T25374—2010 金属切削机床清洁度的测量方法 GB/T25376-2010 金属切削机床机械加工件通用技术条件 JB40292000磨床砂轮防护罩安全防护技术要求 JB/T9905.3-2014无心外圆磨床第3部分:高精度机床精度检验
3一般要求
3.1本部分是对GB/T9061—2006、GB/T25373-2010、GB/T25376—2010等的具体化和补充。按本部分验收机床时,应同时对上述标准中未经本部分具体化的其余有关验收项目进行检验。 3.2按GB/T25372--2010的规定,普通级机床为IV级精度机床,高精度级机床为I级精度机床。
4附件与工具
4.1机床应配备能保证基本性能的附件和工具,由设计根据机床的结构特点进行选择。 4.2根据用户要求,按协议(或合同)的规定提供特殊附件。
5安全卫生
5.1 砂轮主轴的起动系统中应设置可靠的联锁保护装置。 5.2砂轮等危险部件应设置专用安全防护罩,砂轮防护罩还应符合JB4029一2000的规定。
1
JB/T9905.2—2014
5.3机床运转时不应有非正常的尖叫声和冲击声。在空运转条件下,机床的噪声声压级普通级不应超过83dB(A),高精度级不应超过75dB(A)。机床噪声的测量方法按GB/T16769—2008的规定。 5.4手轮、手柄操纵力在行程范围内应均匀,其操纵力不宜大于表1的规定,主进给手轮按“经常用” 手轮的要求考核;调整手轮按“不经常用”手轮的要求考核。
表1 >2~5 60 80
机床重量t 经常用N 不经常用N
≤2 40 60
>5~10 80 120
>10 100 160
5.5按本部分验收机床时,应同时对GB5226.1--2008、GB15760—2004、GB/T23572—2009中未经本部分具体化的其余有关验收项目进行检验。
6加工和装配质量
6.1下列重要铸件应在粗加工后进行时效处理。高精度级机床还应在半精加工后进行第二次时效处理:
a)床身: b)砂轮架; c)转体; d)托架座; e)进给滑板: f)固定体。
6.2机床两砂轮修整器的纵向移动导轨副应采用耐磨措施。 6.3机床横向主进给导轨与其相配件、修整器往复运动导轨与其相配件的接触面,按GB/T25373一2010 “静压、滑(滚)动导轨”的要求考核。 6.4下列结合面应按GB/T25373一2010“特别重要固定结合面”的要求考核:
a)托架下平面与其相配件的结合面: b)两修整器底座与其相配件的结合面: c)双支承支座的结合面: d)转体与固定体的结合面; e)回转板与床身的结合面或固定体与拖板的结合面; f)砂轮架壳体与床身的结合面。
6.5导轮传动系统中的蜗轮副,应在空运转后按设计规定抽检其接触斑点和侧隙。 6.6 5导轮主轴与内锥滑动轴承孔的接触指标普通级不少于80%,高精度级不少于85%,且应靠近大端。 6.7 主进给手轮的反向空程量不应超过表2的规定。
表2
普通级
精度等级机床重量t 空程量I 注:其他有刻度值的手轮、手把,根据使用的需要由设计规定。
高精度级
≤10 1/10
>10 1/4
≤10 1/20
>10 1/10
6.8砂轮主轴传动电动机应连同带轮进行动平衡并校正。校正后剩余不平衡量引起振动的双振幅值不应大于表3的规定。
2
JB/T9905.22014
表3 机床重量 t <5 >5 《5 >5
振动双振幅值
机床精度等级
μm 6 8 4 6
普通级
高精度级
6.9按GB/T25374一2010的规定检验砂轮架部件内部的清洁度。采用滑动轴承时,清洁度按重量法检验,其杂质、污物不应超过200mg,采用滚动轴承时,清洁度按目测法或手感法检验(抽查)。
7机床空运转试验
7.1温度和温升试验
砂轮、导轮主轴(带砂轮和导轮)按设计规定进行空运转试验,从最低速度起依次运转至最高速度或设计规定的最高速度,在最高速度运转足够的时间(不少于1h),使主轴轴承达到稳定温度。在主轴轴承外壳处检验滑动轴承的温度和温升,其温度不应超过55℃,温升不应超过25℃。在靠近主轴滚动轴承的外壳处检验轴承的温度和温升,其温度不应超过65℃,温升不应超过35℃。在床身油池(或独立油箱油池)中测量油液温度和温升应符合GB/T23572一2009的规定。 7.2主运动和进给运动的检验 7.2.1有级变速传动的各级主轴转速的实际偏差,不宜超过标牌指示值的土5%(不包括主电动机转速误差);无级变速传动的主轴转速的实际偏差,不宜超过标牌指示值的土10%。 7.2.2对机床直线坐标上的运动部件分别以低,中、高进给速度进行空运转试验,运动部件移动时应平稳、灵活、可靠,无明显爬行和振动现象。 7.3空运转功率试验
砂轮架电动机的空运转功率不应大于砂轮架电动机空运转功率指标的115% 注1:选择装配质量较好的10套砂轮架,测量其电动机空运转功率,其平均值作为砂轮架电动机空运转功率指标
(测量及检验时均扣除电动机空载功率)。
注2:在砂轮架电动机的空运转功率指标尚未确定时,砂轮架电动机的空运转功率可按不超过电动机额定功率的
25%考核,也可以由设计规定
7.4机床的功能试验 7.4.1对机床的各种指示灯、冷却液润滑装置等控制按钮进行试验,动作应灵活、可靠。 7.4.2对机床的移动、定位等功能逐一进行试验,其功能应可靠,动作应灵活正确。 7.5机床的连续空运转试验
在7.1~7.4试验之后,几何精度检验之前,模拟工作状态按主要加工功能在内的程序操作机床做不切削的连续空运转试验。
机床的连续空运转试验时间应不少于表4的规定。 连续空运转试验过程中不应发生故障。若出现异常或故障,在查明原因进行调整或排除后,应重新开
始试验。试验时,自动循环应包括所有功能和全部工作范围,各次自动循环之间的休止时间不应大于1min。
3
JB/T9905.22014
表4
单位为小时
机床控制形式机械控制电、液控制
连续运转时间
4 8 36 48
联动轴数<3 联动轴数≥3
数字控制
7.6其他 7.6.1 主进给精度检验
主进给按最小标称进给量,每次进给和连续10次进给误差不应超过表5的规定。
表5 导轨结构滚动或静压滑动滚动或静压滑动
允差 80% 100% 16% 20%
检验项目
每次进给
10次进给
误差按式(1)和式(2)计算:
an-b]
S每次
(1)
X100%
1
Zan -10b
010次
X100%
***** (2)
10b
式中:
S每次 每次进给误差; S10次 -10次进给误差;
每次实际进给量,单位为微米(um);最小标称进给量,单位为微米(um)。
an b
7.6.2静压试验
试验应符合下列规定: a)若机床主进给导轨为静压导轨,静压导轨的浮起量在规定的测量点内测量,应不大于0.015mm,
其四角浮起的不均匀性应不大于0.005mm,应连续试验5次。 机床静压建立后应能拖动其负载,拖动力不应大于表6的规定(按设计规定或用户要求)。
表6
拖动力N
机床重量t
120 200
≤5 >5
→
JB/T9905.2—2014
检验方法:在负载的后端装一个测力器(或弹簧秤),在与负载水平运动相平行的平面内拉动负载。
b)若机床的砂轮轴轴承为静压轴承,在静压建立后用手转动主轴,油腔压力波动应不大于
0.05MPa。空转时,薄膜反馈节流器静压轴承的压力比B应符合表7的规定。
表7
轴承形式径向轴承推力轴承
压力比β 1.7~2.6 1.9~2.9
7.6.3砂轮修整器低速移动平稳性试验
普通级机床,砂轮修整器移动速度不大于0.03m/min时,应无爬行。高精度级机床,砂轮修整器移动速度不大于0.006m/min时,应无爬行。
检验方法如下:在砂轮或导轮全宽范围内用百分表检查,百分表指针应均匀连续转动。
机床负荷试验(抽查)
8
本机床仅做砂轮电动机达到设计规定的最大功率试验,用磨削法试验。高精度级机床不做此项试验。 试验条件如下: a)试件按设计规定: b)纵向送进速度按设计规定: c)进给量每次0.10mm,逐步递增至电动机达到设计规定的最大功率。
9 机床精度检验
9.1普通级机床的精度检验按GB/T4681一2007进行。高精度级机床的精度检验按JB/T9905.3一2014 的规定进行。 9.2GB/T4681—2007和JB/T9905.3--2014中的几何精度G1、G3和工作精度M1M2应在机床达到稳定温度后进行。 9.3工作精度检验时,试件表面粗糙度Ra上限值及试件表面波纹度,平均波幅Wz最大充许值,应符合表8的规定。
表8 Ra ≤0.32 ≤0.16
单位为微米
Wz 1.6~2.5 0.4~0.6
机床精度等级
普通级高精度级
10 直线坐标最小设定单位试验
10.1试验方法
先以快速使直线坐标上的运动部件向正(或负)方向移动一定距离,停止后,向同方向给出数个最
5