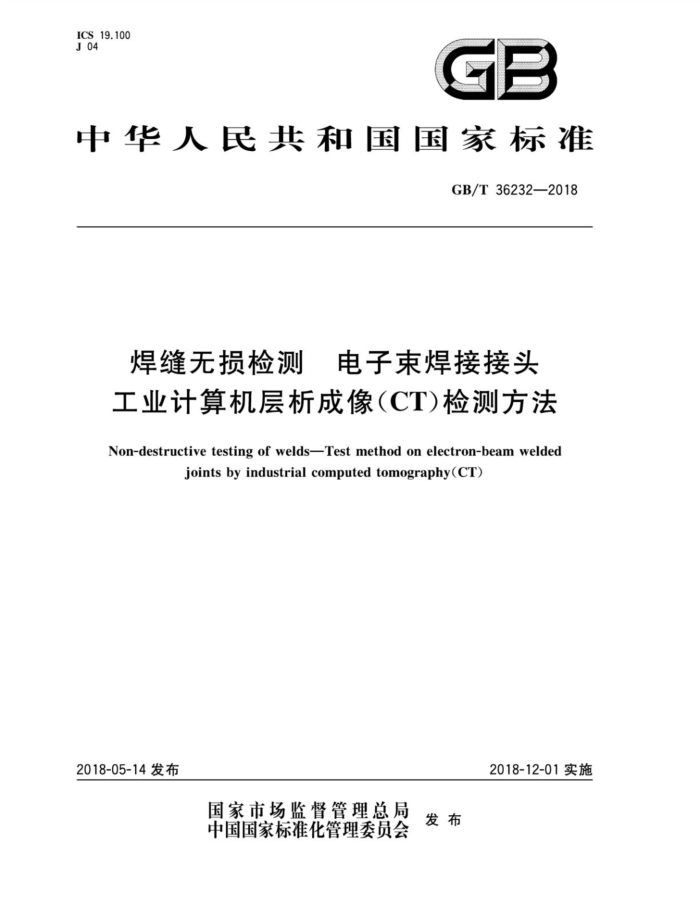
ICS 19.100 J 04
GB
中华人民共和国国家标准
GB/T36232—2018
焊缝无损检测 电子束焊接接头工业计算机层析成像(CT)检测方法
Non-destructivetesting ofwelds-Testmethod onelectron-beamwelded
joints by industrial computed tomography(CT)
2018-05-14发布
2018-12-01实施
国家市场监督管理总局中国国家标准化管理委员会
发布
GB/T36232—2018
目 次
前言引言 1 范围 2 规范性引用文件 3 术语和定义
IV
检测人员 5 环境条件 6 检测系统对比试样 8 检测准备 9 检测程序 10 结果说明· 11 检测报告附录A(资料性附录) 气孔类对比试样的制作附录B(资料性附录) 裂纹类对比试样的制作附录C(资料性附录) 端接焊缝间隙对比试样的制作附录D(资料性附录) 电子束焊缝内部缺欠的CT图片示例
4
.
GB/T 36232—2018
前言
本标准按照GB/T1.1一2009给出的规则起草。 本标准由全国焊接标准化技术委员会(SAC/TC55)提出并归口。 本标准起草单位:中国兵器科学研究院宁波分院、北京控制工程研究所、洛阳LYC轴承有限公司、
宁波出人境检验检疫局、中国兵器工业标准化研究所、上海材料研究所。
本标准主要起草人:倪培君、张维国、曹玉玲、郭智敏、徐向群、乔日东、陈翠丽、齐子诚、李红伟王晓艳、郑颖、左欣、曹国洲、王琳、翟莲娜。
I
GB/T36232—2018
引言
电子束焊接为一种利用电子束作为热源的焊接工艺,在航空、航天、兵器、汽车、机械等各个行业取得了广泛应用。工业CT用于电子束焊缝质量的无损检测已有二十多年历史,在保证电子束焊接件质量及可靠性方面发挥了重要作用。本标准是在总结多年电子束焊缝工业CT检测实践经验的基础上制定的。
V
GB/T36232—2018
焊缝无损检测电子束焊接接头工业计算机层析成像(CT)检测方法
1范围
本标准规定了用工业计算机层析成像(CT)检测电子束焊接接头的术语和定义、人员、环境条件、检
测系统、对比试样、检测准备、检测程序、结果说明、检测报告等要求。
本标准适用于电子束焊接接头内部缺欠的定性、定量及定位检测。
2规范性引用文件
2
下列文件对于本文件的应用是必不可少的。凡是注日期的引用文件,仅注日期的版本适用于本文
件。凡是不注日期的引用文件,其最新版本(包括所有的修改单)适用于本文件。
GB/T3375 焊接术语 GB/T 9445 无损检测 人员资格鉴定与认证 GB18871 电离辐射防护与辐射源安全基本标准 GB/T22085.1 电子束及激光焊接接头缺欠质量分级指南第1部分:钢 GB/T22085.2 电子束及激光焊接接头缺欠质量分级指南第2部分:铝及铝合金 GB/T29034 无损检测 工业计算机层析成像(CT)指南 GB/T29070 无损检测 工业计算机层析成像(CT)检测通用要求 GB/T34365 无损检测 术语工业计算机层析成像((CT)检测 GBZ 98 3放射工作人员健康要求 GBZ 117 工业X射线探伤放射防护要求
3术语和定义
3
GB/T3375、GB/T34365GB/T22085.1、GB/T22085.2、GB/T29034界定的术语和定义适用于本文件。
4检测人员
4.1从事电子束焊接件焊缝工业CT检测的人员应按照GB/T9445有关规定接受培训、考核,并取得相应的技术资格证书,各级检测人员应从事与自已资格等级相对应的技术工作。 4.2从事电子束焊接件焊缝工业CT检测的人员健康应符合GBZ98标准,并应经过电离辐射防护知识培训,取得资格证书。 4.3从事工业CT检测的人员在工作时应佩戴个人剂量计,个人剂量计应定期送当地有关部门进行检测,检测人员的吸收剂量值应符合GB18871的有关规定。 4.4从事电子束焊接件焊缝工业CT检测的人员应熟悉电子束焊接工艺、接头形式、缺欠类型等相关知识。
1
GB/T 36232—2018
5 5环境条件
5.1 检测室防护条件应符合GBZ117、GB18871的相关规定。 5.2 检测室温湿度应满足检测设备和检测产品相应要求,并配备温湿度监测装置。 5.3其他环境条件应符合GB/T29070相关规定。
6 检测系统
6.1系统组成
工业CT检测系统由射线源、探测器、机械扫描装置、计算机等子系统组成。射线源为X射线源(含电子加速器),射线源的能量(穿透能力)应满足试样的材料和尺寸要求。探测器系统可以使用面阵探测器,也可以使用线阵探测器;使用线阵探测器时,应装有前、后准直器,且后准直器宽度可以调节。 6.2系统性能要求 6.2.1检测电子束焊接接头质量的工业CT系统,空间分辨率在10%调制度时的要求如下:
a) 直径小于50mm钢件,空间分辨率应不低于2lp/mm; b) 直径为50mm100mm钢件,空间分辨率应不低于1.5lp/mm; c) 直径大于100mm钢件,空间分辨率应不低于1lp/mm。
6.2.2 对比度分辨率优于0.5%。 6.2.3 系统应配备相关的尺寸测量软件,系统的尺寸测量精度应满足实际产品的检测要求。 6.3 系统性能核查
系统的性能应按照GB/T29070的要求进行定期核查,并记录核查结果。
7对比试样
7.1 对比试样的材料、尺寸及射线衰减特性应与试样相同或相近。 7.2对比试样的具体制作可在实际产品上加工,也可参考附录A、附录B、附录C制作。 7.3 对比试样上的人工缺欠尺寸需进行标定。
8检测准备
8.1 试样分析 8.1.1检测前,应对试样进行整体结构分析,包括试样的形状、组成材料、大致结构、检测部位最大穿透厚度及重量。 8.1.2检测部位最大穿透厚度可以通过实际测量和计算得到。最大穿透厚度可以通过图1箭头所示进行测量或计算。
2
GB/T36232—2018
图1穿透厚度的确定
8.2射线控制 8.2.1 射线能量应保证穿透试样的最大穿透厚度。 8.2.2在射线能量和强度允许的条件下,选用小焦点,以提高空间分辨率。 8.2.3对于线阵探测器,调节准直器狭缝的宽度和形状,减少散射线。 8.2.4采用滤波片减小射束硬化伪像。 8.3 扫描参数的确定 8.3.1 焊接件摆放位置
扫描时焊接件宜放在射束宽度(BW)最小的位置,即最佳放大倍数位置,最佳放大倍数M的计算见式(1):
M=1+()
...(1)
式中: d—单个探测器元的尺寸的数值,单位为毫米(mm); a 射线源焦点尺寸的数值,单位为毫米(mm)。 当机械系统无法使用最佳放大倍数时,M应选择在保证机械安全及其他工艺参数允许条件下的最
接近值。 8.3.2 采样点数和采样幅数要求
采样点数和采样幅数的设置应满足6.2.1的空间分辨率要求。 8.3.3积分时间要求
积分时间的设置应满足6.2.2的对比度分辨率要求。 8.3.4线阵探测器方式下切片参数的确定 8.3.4.1切片厚度宜不大于焊缝验收允许最大缺欠尺寸。 8.3.4.2切片数量应根据焊缝实际情况确定,相邻切片应完全连接,以保证覆盖焊缝需检测区域。对于对接焊缝根据焊缝实际宽度确定切片数量,对于端接焊缝根据焊接工艺要求或最小熔深要求确定,最少切片数量的确定如图2所示。
3
GB/T36232—2018
切片位置
切片位置
最小熔深
切片厚度
切片厚度
图2 2最少切片数量的确定
8.3.4.3 3切片位置宜采用DR图像上定位或直接测量确定。 8.4E 图像的重建、显示和处理 8.4.1图像重建
选用合适的数据滤波和图像重建方法。重建范围应大于焊缝部位最大尺寸。重建的CT图像应保
证图像像素尺寸小于要求检出最小缺欠尺寸的二分之一。 8.4.2图像显示
根据需要,选取灰度、彩色、放大或二维、三维等图像显示方式,通过窗宽/窗位的调整,使得图像便
于观察。 8.4.3图像处理
在不丢失图像缺欠信息条件下,可采用合适的图像处理方法进行图像处理,改善对比度和清晰度 8.5其他 8.5.1检测前,应针对焊接件编制检测工艺卡,工艺卡中一般应包括以下内容:工艺卡编号、产品名称、 编号、材料牌号、检测方法、检测标准、设备型号、检测技术参数、检测部位示意图等。 8.5.2检测前,应按检测系统说明书的要求对检测系统进行标定。 8.5.3 使用对比试样对比的方法验证检测工艺是否正确、检测系统是否稳定。
9 检测程序
9.1 将试样放置在转台上,使被检对接焊缝与转台平面水平,端接焊缝与转台平面垂直。 9.2 通过DR扫描图像或技术图纸等相关技术文件,确定焊缝位置,明确切片的起始位置。 9.31 使用与对比试样相同的检测条件对试样焊缝进行全覆盖检测,获取满足质量检测要求图像。伪像不能影响缺欠的识别和尺寸测量。
10 结果说明 10.1 缺欠定性 10.1.1 根据CT图像细节特征的像素灰度值、形状、尺寸等情况对图像进行分析,部分典型缺欠的CT 4
ICS 19.100 J 04
GB
中华人民共和国国家标准
GB/T36232—2018
焊缝无损检测 电子束焊接接头工业计算机层析成像(CT)检测方法
Non-destructivetesting ofwelds-Testmethod onelectron-beamwelded
joints by industrial computed tomography(CT)
2018-05-14发布
2018-12-01实施
国家市场监督管理总局中国国家标准化管理委员会
发布
GB/T36232—2018
目 次
前言引言 1 范围 2 规范性引用文件 3 术语和定义
IV
检测人员 5 环境条件 6 检测系统对比试样 8 检测准备 9 检测程序 10 结果说明· 11 检测报告附录A(资料性附录) 气孔类对比试样的制作附录B(资料性附录) 裂纹类对比试样的制作附录C(资料性附录) 端接焊缝间隙对比试样的制作附录D(资料性附录) 电子束焊缝内部缺欠的CT图片示例
4
.
GB/T 36232—2018
前言
本标准按照GB/T1.1一2009给出的规则起草。 本标准由全国焊接标准化技术委员会(SAC/TC55)提出并归口。 本标准起草单位:中国兵器科学研究院宁波分院、北京控制工程研究所、洛阳LYC轴承有限公司、
宁波出人境检验检疫局、中国兵器工业标准化研究所、上海材料研究所。
本标准主要起草人:倪培君、张维国、曹玉玲、郭智敏、徐向群、乔日东、陈翠丽、齐子诚、李红伟王晓艳、郑颖、左欣、曹国洲、王琳、翟莲娜。
I
GB/T36232—2018
引言
电子束焊接为一种利用电子束作为热源的焊接工艺,在航空、航天、兵器、汽车、机械等各个行业取得了广泛应用。工业CT用于电子束焊缝质量的无损检测已有二十多年历史,在保证电子束焊接件质量及可靠性方面发挥了重要作用。本标准是在总结多年电子束焊缝工业CT检测实践经验的基础上制定的。
V
GB/T36232—2018
焊缝无损检测电子束焊接接头工业计算机层析成像(CT)检测方法
1范围
本标准规定了用工业计算机层析成像(CT)检测电子束焊接接头的术语和定义、人员、环境条件、检
测系统、对比试样、检测准备、检测程序、结果说明、检测报告等要求。
本标准适用于电子束焊接接头内部缺欠的定性、定量及定位检测。
2规范性引用文件
2
下列文件对于本文件的应用是必不可少的。凡是注日期的引用文件,仅注日期的版本适用于本文
件。凡是不注日期的引用文件,其最新版本(包括所有的修改单)适用于本文件。
GB/T3375 焊接术语 GB/T 9445 无损检测 人员资格鉴定与认证 GB18871 电离辐射防护与辐射源安全基本标准 GB/T22085.1 电子束及激光焊接接头缺欠质量分级指南第1部分:钢 GB/T22085.2 电子束及激光焊接接头缺欠质量分级指南第2部分:铝及铝合金 GB/T29034 无损检测 工业计算机层析成像(CT)指南 GB/T29070 无损检测 工业计算机层析成像(CT)检测通用要求 GB/T34365 无损检测 术语工业计算机层析成像((CT)检测 GBZ 98 3放射工作人员健康要求 GBZ 117 工业X射线探伤放射防护要求
3术语和定义
3
GB/T3375、GB/T34365GB/T22085.1、GB/T22085.2、GB/T29034界定的术语和定义适用于本文件。
4检测人员
4.1从事电子束焊接件焊缝工业CT检测的人员应按照GB/T9445有关规定接受培训、考核,并取得相应的技术资格证书,各级检测人员应从事与自已资格等级相对应的技术工作。 4.2从事电子束焊接件焊缝工业CT检测的人员健康应符合GBZ98标准,并应经过电离辐射防护知识培训,取得资格证书。 4.3从事工业CT检测的人员在工作时应佩戴个人剂量计,个人剂量计应定期送当地有关部门进行检测,检测人员的吸收剂量值应符合GB18871的有关规定。 4.4从事电子束焊接件焊缝工业CT检测的人员应熟悉电子束焊接工艺、接头形式、缺欠类型等相关知识。
1
GB/T 36232—2018
5 5环境条件
5.1 检测室防护条件应符合GBZ117、GB18871的相关规定。 5.2 检测室温湿度应满足检测设备和检测产品相应要求,并配备温湿度监测装置。 5.3其他环境条件应符合GB/T29070相关规定。
6 检测系统
6.1系统组成
工业CT检测系统由射线源、探测器、机械扫描装置、计算机等子系统组成。射线源为X射线源(含电子加速器),射线源的能量(穿透能力)应满足试样的材料和尺寸要求。探测器系统可以使用面阵探测器,也可以使用线阵探测器;使用线阵探测器时,应装有前、后准直器,且后准直器宽度可以调节。 6.2系统性能要求 6.2.1检测电子束焊接接头质量的工业CT系统,空间分辨率在10%调制度时的要求如下:
a) 直径小于50mm钢件,空间分辨率应不低于2lp/mm; b) 直径为50mm100mm钢件,空间分辨率应不低于1.5lp/mm; c) 直径大于100mm钢件,空间分辨率应不低于1lp/mm。
6.2.2 对比度分辨率优于0.5%。 6.2.3 系统应配备相关的尺寸测量软件,系统的尺寸测量精度应满足实际产品的检测要求。 6.3 系统性能核查
系统的性能应按照GB/T29070的要求进行定期核查,并记录核查结果。
7对比试样
7.1 对比试样的材料、尺寸及射线衰减特性应与试样相同或相近。 7.2对比试样的具体制作可在实际产品上加工,也可参考附录A、附录B、附录C制作。 7.3 对比试样上的人工缺欠尺寸需进行标定。
8检测准备
8.1 试样分析 8.1.1检测前,应对试样进行整体结构分析,包括试样的形状、组成材料、大致结构、检测部位最大穿透厚度及重量。 8.1.2检测部位最大穿透厚度可以通过实际测量和计算得到。最大穿透厚度可以通过图1箭头所示进行测量或计算。
2
GB/T36232—2018
图1穿透厚度的确定
8.2射线控制 8.2.1 射线能量应保证穿透试样的最大穿透厚度。 8.2.2在射线能量和强度允许的条件下,选用小焦点,以提高空间分辨率。 8.2.3对于线阵探测器,调节准直器狭缝的宽度和形状,减少散射线。 8.2.4采用滤波片减小射束硬化伪像。 8.3 扫描参数的确定 8.3.1 焊接件摆放位置
扫描时焊接件宜放在射束宽度(BW)最小的位置,即最佳放大倍数位置,最佳放大倍数M的计算见式(1):
M=1+()
...(1)
式中: d—单个探测器元的尺寸的数值,单位为毫米(mm); a 射线源焦点尺寸的数值,单位为毫米(mm)。 当机械系统无法使用最佳放大倍数时,M应选择在保证机械安全及其他工艺参数允许条件下的最
接近值。 8.3.2 采样点数和采样幅数要求
采样点数和采样幅数的设置应满足6.2.1的空间分辨率要求。 8.3.3积分时间要求
积分时间的设置应满足6.2.2的对比度分辨率要求。 8.3.4线阵探测器方式下切片参数的确定 8.3.4.1切片厚度宜不大于焊缝验收允许最大缺欠尺寸。 8.3.4.2切片数量应根据焊缝实际情况确定,相邻切片应完全连接,以保证覆盖焊缝需检测区域。对于对接焊缝根据焊缝实际宽度确定切片数量,对于端接焊缝根据焊接工艺要求或最小熔深要求确定,最少切片数量的确定如图2所示。
3
GB/T36232—2018
切片位置
切片位置
最小熔深
切片厚度
切片厚度
图2 2最少切片数量的确定
8.3.4.3 3切片位置宜采用DR图像上定位或直接测量确定。 8.4E 图像的重建、显示和处理 8.4.1图像重建
选用合适的数据滤波和图像重建方法。重建范围应大于焊缝部位最大尺寸。重建的CT图像应保
证图像像素尺寸小于要求检出最小缺欠尺寸的二分之一。 8.4.2图像显示
根据需要,选取灰度、彩色、放大或二维、三维等图像显示方式,通过窗宽/窗位的调整,使得图像便
于观察。 8.4.3图像处理
在不丢失图像缺欠信息条件下,可采用合适的图像处理方法进行图像处理,改善对比度和清晰度 8.5其他 8.5.1检测前,应针对焊接件编制检测工艺卡,工艺卡中一般应包括以下内容:工艺卡编号、产品名称、 编号、材料牌号、检测方法、检测标准、设备型号、检测技术参数、检测部位示意图等。 8.5.2检测前,应按检测系统说明书的要求对检测系统进行标定。 8.5.3 使用对比试样对比的方法验证检测工艺是否正确、检测系统是否稳定。
9 检测程序
9.1 将试样放置在转台上,使被检对接焊缝与转台平面水平,端接焊缝与转台平面垂直。 9.2 通过DR扫描图像或技术图纸等相关技术文件,确定焊缝位置,明确切片的起始位置。 9.31 使用与对比试样相同的检测条件对试样焊缝进行全覆盖检测,获取满足质量检测要求图像。伪像不能影响缺欠的识别和尺寸测量。
10 结果说明 10.1 缺欠定性 10.1.1 根据CT图像细节特征的像素灰度值、形状、尺寸等情况对图像进行分析,部分典型缺欠的CT 4