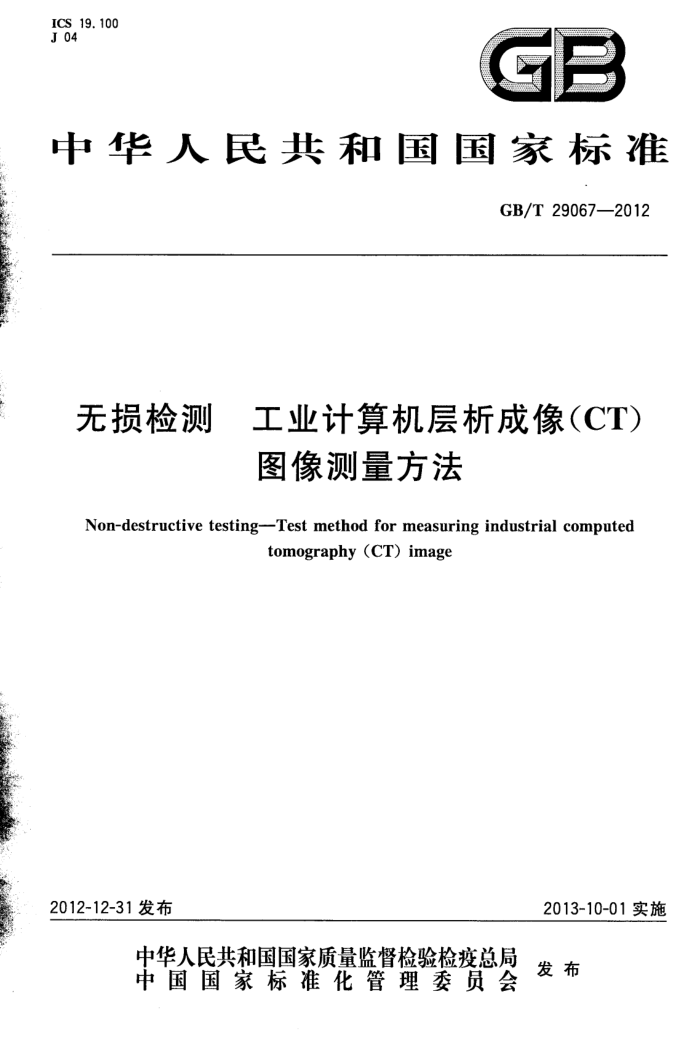
ICS 19. 100 J 04
GB
中华人民共和国国家标准
GB/T 29067—2012
无损检测 工业计算机层析成像(CT)
图像测量方法
Non-destructive testing--Test method for measuring industrial computed
tomography (CT) image
2013-10-01实施
2012-12-31发布
中华人民共和国国家质量监督检验检疫总局
中国国家标准化管理委员会 发布
GB/T 29067—2012
前言
本标准按照GB/T1.1一2009给出的规则起草。 本标准由全国无损检测标准化技术委员会(SAC/TC56)提出并归口。 本标准起草单位:重庆真测科技股份有限公司、重庆大学ICT研究中心、上海泰司检测科技有限公
司、中国石油集团济柴动力总厂、齐齐哈尔轨道交通装备有限责任公司、上海航天动力技术研究所。
本标准主要起草人:曾理、王珏、李树生、蔡玉芳、沈宽、邹永宁、王福全、段黎明、杨蓉、高金生、俞翔、 沈伟民。
一
GB/T29067—2012
无损检测工业计算机层析成像(CT)
图像测量方法
1 范围
本标准规定了用于无损检测的工业计算机层析成像(CT)系统图像密度测量校准和尺寸测量校准
的方法,以及从CT图像测量被测物体物质密度和尺寸的方法。
本标准适用于测量被测物体内部各部分的密度(包括由不同材料组成的被测物体内部各部分的密度)及被测物体内外结构(特别是封闭内腔)的几何尺寸。
.2·规范性引用文件
下列文件对于本文件的应用是必不可少的。凡是注日期的引用文件,仅注日期的版本适用于本文件。凡是不注日期的引用文件,其最新版本(包括所有的修改单)适用于本文件。
GB/T12604.2无损检测术语射线照相检测
3术语和定义
GB/T12604.2界定的术语和定义适用于本文件。
4应用基础
4.1.检测设备要求
要求具备相关的检测设备(包括工业CT设备及相关图像处理软件),并要求客户和供应商在相关方面达成一致。 4.2避免图像伪影对密度测量的影响
密度测量方法要求:CT密度的变化反映被测物体密度的真实变化而不是图像伪影。由于探测器响应不一致、射线散射、射线硬化等原因,CT图像可能呈现出一定程度的伪影,且伪影往往被误认为是密度变化。为确保该密度测量方法的有效性,工业CT设备制造商应对射线投影数据进行校正,以尽量减少CT图像伪影。在实际检测中,用户应该尽量避开受伪影影响的区域进行密度测量。 4.3避免图像伪影对尺寸测量的影响
尺寸测量方法要求:被测物体的被测区域对应的CT图像应具有比较陡峭的边缘。由于探测器响应不一致、射线散射、射线硬化等原因,CT图像可能呈现出一定程度的伪影,加之被测物体的直线型边缘可能会造成条状伪影。为确保该尺寸测量方法的有效性,工业CT设备制造商应对射线投影数据进行校正,以尽量减少CT图像伪影。在实际检测中,用户应该尽量避开受伪影影响的区域进行尺寸测量。
1
GB/T29067-—2012
5标准试件的制作
5.1密度标准试件的制作 5.1.1若客户与供应商之间没有其他的协议,密度标准试件组应由多个不同密度的圆柱形密度标准试件组成,在基体上沿圆周均匀分布,如图1所示。
森辉
基体
截面A—A
图1密度标准试件组
5.1.2密度标准试件组的材料密度应涵盖被测物体材料密度范围,且每个标准试件的密度已知。每个标准试件应材质均匀,各个标准试件的尺寸规格应相同。 5.1.3密度标准试件高度应为CT切片厚度的3倍以上。 5.1.4密度标准试件圆柱直径应该确保每个标准试件CT切片图像的像素个数不少于100。 5.2尺寸标准试件的制作 5.2.1尺寸标准试件宜选择与被测物体材料一致的试块,也可选用标准量块。 5.2.2尺寸标准试件的偏差应小于被测物体的测量偏差要求至少一个数量级,例如被测物体的测量偏差要求小于0.1mm,则标准试件尺寸的偏差应小于0.01mm。 5.2.3尺寸标准试件的形状应为长方体。设系统的空间分辨力为K(单位为LP/mm),尺寸标准试件
的最长边的长度应大于 50×2xk mm,且对应 CT 图像的最长边宜具有 50 个或以上的像素,以减少测量的系统误差。 6校准与测量 6.1标准试件和被测物体的检测工艺要求 6.1.1将标准试件或被测物体安置在CT系统转台上,使得试件中心轴垂直于扫描基准平面。 域到转轴的距离近似相同。
6.1.2标准试件应尽量安置在转台上与被测物体的待测区域大致相同的位置,或与被测物体的待测区
2
GB/T29067—2012
6.1.3标准试件扫描切片位置应大致选择在标准试件的中间位置,被测物体扫描切片位置根据需要而定。 6.1.4标准试件与被测物体应采用相同的工艺参数(包括射线源参数、扫描参数、重建参数等)及图像数据处理方法。 6.2密度测量校准 6.2.1密度测量校准时宜将扫描参数、重建参数调整至系统密度分辨力最优的参数设置下。 6.2.2在CT图像上的每个密度标准试件中心部位分别选圆形区域(每个圆形区域像素数宜多于 50个,但不大于整个标准试件区域的2/3),测得该区域内每一点的CT密度f(工,y),计算该区域的平均CT密度f。 6.2.3选取密度标准试件组中一个密度标准试件作为密度测量校准的基准标准试件。根据基准标准试件指定区域的平均CT密度f。和CT系统设定的比例系数k(根据CT系统总体参数确定,一般为 1000~5000),对每个密度标准试件指定区域的平均CT密度于按式(1)进行归一化处理,获得该区域内的平均CT数:
-{-xk
.(1)
fo
式中: f一密度标准试件指定区域的平均CT密度; —密度标准试件指定区域的平均CT数; f。-基准标准试件指定区域的平均CT密度; k—CT系统设定的比例系数。
6.2.4利用各个密度标准试件指定区域的平均CT数和该标准试件已知的密度p,采用多项式拟合校准平均CT数与物质密度p之间的关系式:p=f(),推荐采用三次多项式拟合。 6.3被测物体的密度测量 6.3.1选取与密度校准时采用的同一基准标准试件,将基准标准试件放在被测物体的待测区域附近与被测物体同时进行CT扫描;或将基准标准试件单独放在(与被测物体的待测区域)同一扫描位置,采用与被测物体扫描时相同的工艺参数,对密度标准试件单独进行扫描。 6.3.2从基准标准试件的CT图像中,获取指定区域(指定区域内像素数宜多于50个且不大于整个标准试件区域的2/3)的平均CT密度f。。 6.3.3从被测物体的CT图像中,获取待测区域(区域内像素数宜多于50个)的平均CT密度于。按式 (2)进行归一化得到被测物体的待测区域的平均CT数。
i-{xk
..(2)
fo
式中:于—被测物体的待测区域的平均CT密度; i被测物体的待测区域的平均CT数; f。一基准标准试件的指定区域的平均CT密度; k一一CT系统设定的比例系数(与密度测量校准时相同)。
6.3.4根据被测物体的待测区域的平均CT数和已校准的函数关系p=f(π),求得该区域平均物质密度p。 6.3.5重复测量同一均匀材质不同区域至少5次,以5次测得密度的平均值作为此材质的密度值,并计算密度测量的标准偏差。
3
GB/T290672012
6.4尺寸测量校准 6.4.1尺寸标准试件校准时应将扫描参数、重建参数调整至系统空间分辨力最优的参数设置下。 6.4.2测试时,宜使尺寸标准试件对射线的衰减系数与实际被测物体接近,必要时可采用射线衰减补偿。 6.4.3如图2所示,设定尺寸标准试件1为校准测量的标准试件,尺寸标准试件2为测试测量误差的标准试件。在CT图像上尺寸标准试件1短边中心处,沿长边方向画一条直线。将直线所经过点的CT 数绘制在坐标图上则形成该标准试件的CT数曲线。由于尺寸标准试件和空气的密度相差很大,因此该曲线会形成一个边缘陡峭的波峰,其理想曲线如图3所示。 6.4.4由于噪声的干扰,标准试件的CT数曲线往往不能形成理想曲线。因此,建议沿长边方向画5 条平行直线,将5条直线所经过点的CT数绘制在坐标图上,并进行最小二乘拟合,以获得近似的理想 CT数曲线。 6.4.5在该波峰高度约一半的位置定位一测量直线P,该直线与CT数曲线相交于A、B两点,在坐标系中找出A、B点对应的横坐标值,由两者差的绝对值可得到尺寸标准试件1的图像长度D(单位:像素)。 6.4.6 根据标准试件1的图像长度D(单位:像素)、图像矩阵的宽度W(单位:像素)、CT系统扫描视场成像直径V(单位:毫米),由式(3)计算出标准试件1的CT几何长度测量值L(单位:毫米):
L=D× V
(3)
W
6.4.7比较标准试件1的几何长度测量值L与实际长度值之间的差异,如果测量值大于实际值则将测量直线P向上移动直至两者相等,反之则将直线P向下移动。记录此时测量直线P所处位置的CT 数μP。
尺寸标件1
尺寸标件2
图2尺寸标准试件组CT示意图
4
GB/T29067—2012
CT数
像素个数
RC
RA
图3图2中标准试件1直线位置的理想CT数曲线图
6.4.8计算曲线上低密度物质对应CT数的均值u,即图3中RA和RC所指曲线段的CT数平均值;计算曲线上高密度位置对应CT数的均值H,即图3中RB所指曲线段的CT数平均值;计算测量直线 P在CT数曲线陡坡上的相对位置比例Cp,Cp由式(4)计算得到:
Cp
(4)
μHμL
6.4.9在图像上尺寸标准试件2短边中心处,沿长边方向画一条直线。将该直线所经过各个点的CT 值绘制在坐标图上则形成类似图3的CT数曲线。同样在该曲线上定位一直线Q,调整Q的位置使得 Q所处位置的CT数等于μQ,Q通过式(5)得到:
μQ =μL+Cp×(μH-μL)
..(5)
则直线Q与CT数曲线相交两点之间横坐标差的绝对值,即为本次测量的尺寸标准试件2的CT 图像长度(单位:像素)。 6.4.10重复测量3次,依次计算出标准试件2的图像长度D1,D2,D3。由式(6)计算取三者的平均值作为尺寸标准试件2的CT图像像素长度测量值D(单位:像素),并计算标准偏差。
D = (D: + D, + D,)
.(6)
3
6.4.11依据式(3)计算出标准试件2的几何长度测量值L。由标准试件2的CT几何长度测量值与其实际长度之差的绝对值,得到标件2的CT长度L测量误差的绝对值:α一IL测量值一L实际值I。 6.4.12由于该方法是基于图像中物质CT数曲线,因此在测量线上需消除或避开图像伪影。 6.4.13为了克服本测量方法中由于人工划线带来的测量结果的不稳定性,图像处理系统可以采用软件自动测量尺寸标准试件两条平行短边的距离,代替手动测量平均值。 6.5被测物体的人工尺寸测量 6.5.1测量被测物体时,建议将被测物体与其密度相近的尺寸标准试件一起做CT扫描或采用相同的工艺参数扫描。 6.5.2采用和前述尺寸标准试件校准时测量标准试件2尺寸类似的步骤和方法,测量被测物体尺寸。 先测量标准试件的长度,确定标准试件测量线的相对位置比例Cp。然后测量被测物体待测区域的长
5
GB/T29067—2012
度,根据Cp的值调整被测物体测量线的位置。计算被测物体测量线与CT数曲线相交两点的横坐标差的绝对值,然后根据CT视场直径求出两点的实际长度。 6.5.3由于被测物体待测区域周围的材料密度可能不一致,导致上述CT数曲线左右高度可能不一致。此时可根据测量线的相对位置比例Cp,分别在CT数曲线的左右陡边中确定相交点,并计算两点的横坐标之差。 6.5.4由于CT系统的固有特性和空间分辨力的限制,CT图像边缘存在扩散现象。该测量方法可有效地克服CT图像边缘扩散对测量精度的影响,但要求被测物体待测区域的长度应大于边缘扩散带宽的5倍以上。 6.6被测物体的自动尺寸测 6.6.1对管道(包括被测物体内腔及内部管道)壁厚的自动测量,可用图像处理软件自动提取内外壁边缘点并跟踪,自动计算内壁上各点到外壁的最短距离,从而得到壁厚变化曲线,最大、最小和平均壁厚等几何参数。 6.6.2对于已知CAD模型的被测物体,可采用(二维或三维)CAD模型和CT图像的尺寸比对自动测量技术,自动计算并直观显示被测物体的尺寸误差,以便于改进制造工艺。包括自动配准(根据CT视场直径缩放CT图像或CAD图形,CT图像边缘提取,CT图像边缘与CAD图形线的平移旋转配准)和自动尺寸误差测量(计算CT图像边缘点到最近的CAD图形线的距离,并用不同的颜色或灰度显示被测物体边缘点的误差大小)等。
7精度和偏差
7.1密度测量的精度
由密度测量最大误差除以系统密度测量量程,可得到系统密度测量(相对于量程的)精度(引用误差)。密度测量精度与系统密度分辨力等因素有关。有实例显示:若系统密度分辨力达到干分之三,且 CT图像无明显伪影,CT系统密度测量精度可达到1%左右。 7.2人工尺寸测量的偏差
具体偏差和系统分辨力等因素有关。设系统的空间分辨力为K(单位为LP/mm),则CT系统尺寸测量偏差可小于1/(2×K)mm。系统的空间分辨力越高,CT尺寸测量偏差越小。人工划线结合CT 数曲线自动定位的尺寸测量方法,可有效地消除数字图像按像素采样和CT图像边缘扩散带来的误差,使得测量偏差可小于个像素代表的实际长度。 7.3自动尺寸测量的偏差
自动尺寸测量(包括壁厚自动测量、CAD图形和CT图像的尺寸比对自动测量)效率高、测量结果稳定。自动尺寸测量的偏差取决于边缘点的定位偏差等因素,而CT图像存在的像素采样误差和边缘扩护散影响了边缘点的定位偏差。自动尺于测量的偏差般大于或等于一个像素代表的实际长度,采用亚像素的边缘点定位方法可减少边缘定位偏差和自动尺寸测量偏差。
8报告
报告应包括重建参数、显示参数,相关图像和测量数据。其中密度测量部分至少要包括指定材料的密度测量值,尺寸测量部分至少要包括指定位置(标示于CT图像上)的尺寸测量值。客户和供应商可协商其他需要包括的参数和数据。 6