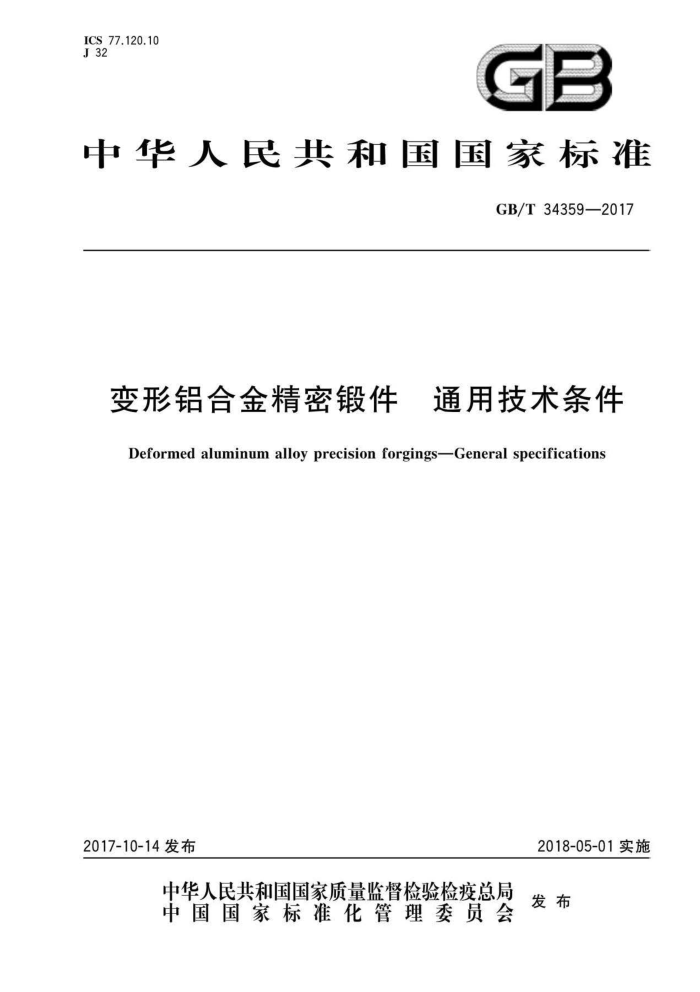
ICS 77.120.10 J32
GB
中华人民共和国国家标准
GB/T34359—2017
变形铝合金精密锻件 通用技术条件
Deformed aluminum alloy precision forgingsGeneral specifications
2017-10-14发布
2018-05-01实施
中华人民共和国国家质量监督检验检疫总局中国国家标准化管理委员会
发布
GB/T34359—2017
前言
本标准按照GB/T1.1一2009给出的规则起草。 本标准由全国锻压标准化技术委员会(SAC/TC74)提出并归口。 本标准起草单位:芜湖禾田汽车工业有限公司、北京机电研究所、湖北三环锻造有限公司、贵州安大
航空锻造有限责任公司、江苏太平洋精锻科技股份有限公司、江苏龙城精锻有限公司、宁波蜗牛锻造有限公司。
本标准主要起草人:潘琦俊、潘海斌、魏巍、金红、胡柏丽、张运军、王斌、夏汉关、庄晓伟、魏百江、 吴忠林、包其华、黎诚、赵迎军、晏洋、王战兵、蒋容华、王晓飞、陶立平、郑俊涛、陈文敬、周林。
-
GB/T34359—2017
变形铝合金精密锻件 通用技术条件
1范围
本标准规定了变形铝合金精密锻件(以下简称“锻件”)的分类、技术要求、试验方法、检验规则和标识、质量合格证书、包装、运输和储存。
本标准适用于质量小于15kg的变形铝合金热模锻件。
规范性引用文件
2
下列文件对于本文件的应用是必不可少的。凡是注日期的引用文件,仅注日期的版本适用于本文件。凡是不注日期的引用文件,其最新版本(包括所有的修改单)适用于本文件。
GB/T231.1金属材料布氏硬度试验第1部分:试验方法 GB/T2828(所有部分)计数抽样检验程序 GB/T2829 周期检验计数抽样程序及表(适用于对过程稳定性的检验) GB/T3191 铝及铝合金挤压棒材 GB/T3199 铝及铝合金加工产品包装、标志、运输、贮存 GB/T3246.1 变形铝及铝合金制品组织检验方法第1部分:显微组织检验方法 GB/T3246.2一2012变形铝及铝合金制品组织检验方法第2部分:低倍组织检验方法 GB/T6519 变形铝、镁合金产品超声波检验方法 GB/T6892 一般工业用铝及铝合金挤压型材 GB/T7999 铝及铝合金光电直读发射光谱分析方法 GB/T8541 锻压术语 GB/T8545—2012铝及铝合金模锻件的尺寸偏差及加工余量 GB/T9452 热处理炉有效加热区测定方法 GB/T10125 人造气氛腐蚀试验盐雾试验 GB/T11346 铝合金铸件X射线照相检验针孔(圆形)分级 GB/T12363 锻件功能分类 GB/T16475 变形铝及铝合金状态代号 GB/T16865 变形铝、镁及其合金加工制品拉伸试验用试样及方法 GB/T17432 变形铝及铝合金化学成分分析取样方法 GB/T18851(所有部分)无损检测渗透检测 GB/T20975(所有部分)铝及铝合金化学分析方法
3术语和定义
GB/T8541界定的术语和定义适用于本文件。
4分类
4.1锻件根据GB/T12363分类,分为I、Ⅱ、Ⅱ、IV四类
1
GB/T34359—2017
锻件类别在产品图中标明。
4.2
5技术要求
5.1 原材料
5.1.1锻件选用铝合金材料的化学成分宜符合GB/T3190的规定,一般要求宜符合GB/T3191的规定,也可由供需双方协商确定。 5.1.2 挤压棒材、型材、可锻铸棒宜进行均化处理。 5.1.3 挤压棒材、型材、可锻铸棒的表面质量不应有超出表1规定的缺陷。
表1原材料质量要求
缺陷 判 定 处数
L<300mm 合格
L>300mm~500mm L>500mm~800mm L>800mm~1000mm
序号
不合格 2
合格 不合格 2
不合格 1
合格 1
不合格 1
合格 0
0 碰磕缺陷:宽度不大于1.2mm,长度不大于2mm,高度或深度不大于.0.15mm。 合格
不合格 1
合格 0
不合格 1
合格 1
不合格 2
合格 2
不合格 3
0 拉伤缺陷:宽度不大于1.2mm,长度不大于50mm,高度或深度不大于0.10mm。
2
表面:除控制材料流痕外,不应有气泡、缩孔和麻点存在。弯曲、扭曲程度应符合GB/T6892的规定。 内部:气孔、针孔、夹杂、夹渣、疏松、偏析、裂纹等冶金缺陷通常不作破坏性检查,挤压前铸锭的质量控制应按照GB/T11346的规定进行。
5.1.4 挤压棒材或型材不应有成层和缩尾存在,粗晶环深度要求应符合GB/T3191规定。 5.1.5 氧化膜缺陷的起算长度大于0.3mm,0.3mm~1.0mm长度的氧化膜缺陷点数不大于2点,不应存在大于1mm的氧化膜缺陷。 5.1.6按供需双方确定的检验项目进行检验和复验。 5.2工艺 5.2.1 “下料设备可采用圆盘锯、高速带锯等。 5.2.2 锻前加热设备(包括模具加热炉)应选用相应的加热设备并符合GB/T9452的规定。铝锻坏、工模具加热炉的技术要求见表2。
表2 铝锻坏、工模具加热炉技术要求控温 记录表指示精度 记录纸刻度 炉子检测
仪表检定周期
有效加热区保温精度
加热炉类别
周期月 6 12
精度 ℃ ±5 ±10
(不低于)
(不大于) ℃/mm
℃ ±5
℃ 0.5 0.5
月 6 12
铝锻坏加热炉工模具加热炉 ±25
6 10
测试点数应按GB/T9452规定。
2
GB/T34359—2017
5.2.3锻造设备的选择应根据生产工艺要求和企业实际情况确定。 5.2.4锻件飞边切断处的毛刺宜通过振动光饰予以清除。 5.2.5锻件表面可用抛丸、喷砂等方法清理,可用钝化、阳极氧化等表面处理方式。 5.3热处理 5.3.1 锻件热处理状态及代号按GB/T16475规定。 5.3.2 固溶和时效热处理之间的时间间隔一般不超过24h。 5.3.3淬火加热炉和时效强化加热炉炉温的均匀性不超过士5℃。 5.3.4加热设备的周期校验应符合GB/T9452规定。 5.3.5 热处理一般要求可参照YS/T591。 5.4锻件质量 5.4.1表面质量 5.4.1.1 表面不应有缺料、起皮、气泡、毛刺,可有轻微的碰伤、划伤、压坑、擦伤等缺陷。 5.4.1.2 2锻造成形后,如表面有裂纹,应予以清除。裂纹位于待加工处,其打磨深度应保证留有三分之一的名义加工余量;裂纹位于非加工处,其打磨深度不应超过该处尺寸偏差的三分之二。 5.4.1.3清除裂纹的痕迹要求:清除裂纹处与其周边应圆弧过渡,修痕的宽深比不小于6。 5.4.2力学性能
锻件力学性能应符合需方要求,锻件硬度通常采用布氏试验方法检测。未规定硬度范围时可按 YS/T591的规定执行。取样及检验位置应在图样中标明。 5.4.3显微组织
不应有过烧存在。 5.4.4低倍组织 5.4.4.1 流线方向应符合产品图样的规定,不应有穿流和严重涡流。 5.4.4.2 不应有自视可见的裂纹、气孔、折叠、偏析和夹杂物等缺陷。 5.4.4.3 :表面粗晶层深度不大于3mm。在分模线处,粗晶层深度不大于8mm,宽度不大于7mm。 5.4.4.4晶粒度应不低于GB/T3246.2—2012中四级分级标准。 5.5盐雾腐蚀性能
耐中性盐雾腐蚀性能时间大于240h,试验后划线处的单边腐蚀延伸不超过2mm。 5.6 6尺寸偏差
锻件的尺寸偏差应符合GB/T8545一2012中A级规定。
6试验方法 6.1化学成分
化学成分分析取样按GB/T17432规定,试验方法可采用GB/T7999或GB/T20975,仲裁分析方法应符合GB/T20975的规定。
3
GB/T34359—2017
6.2 表面质量
表面质量可在自然散射光下目视检验。
6.3 力学性能
室温拉伸力学性能试验方法应符合GB/T16865的规定。布氏硬度试验方法应符合GB/T231.1
的规定。 6.4显微组织
显微组织检验方法应符合GB/T3246.1的规定。
6.5 低倍组织
低倍组织检验方法应符合GB/T3246.2的规定。
6.6 盐雾试验
盐雾试验方法应符合GB/T10125的规定。 6.7 ,尺寸偏差
锻件的尺寸及外形应用相应精度的量具或专用工具进行测量。
6.8无损检测
超声波检验方法应符合GB/T6519的规定。荧光渗透检验方法应符合GB/T18851的规定 6.9 特殊检验项目
当锻件需要增加特殊检验项目而又没有相应国家标准或行业标准时,可采用企业标准,并在技术协议中注明。
7检验规则 7.1检查和验收 7.1.1 锻件交付检验由供方根据图纸、技术协议及相关标准进行,出具质量合格证书, 7.1.2 需方根据供方的质量合格证书和相关文件,按GB/T2828、GB/T2829进行抽查验收。 7.2组批
锻件应成批提交验收,每批应由同一牌号、同一生产批和同一热处理炉次的产品组成。 7.3 计量
锻件应按产品数量计量。 7.4检验项目和数量
各类锻件成品出厂前的检验项目和取样数量应符合表3规定。
4
GB/T34359—2017
表3 各类锻件的检验项目和取样数量
锻件类别化学成分 每批抽取至少3件 每批抽取至少3件
IV
1
ⅡI
Ⅲ
每批抽取至少1件
每批抽取至少1件
100% 每批抽取至少3件抽检或100%
100% 每批抽取至少3件抽检或100%
100% 每批抽取至少1件抽检或100%
100% 每批抽取至少1件
表面质量盐雾试验尺寸偏差布氏硬度力学性能显微组织低倍组织无损检测抽检方法按GB/T2828、GB/T2829执行。 特殊项目检测由供需双方共同确定。
抽检抽检
抽检每批抽取至少3件每批抽取至少3件每批抽取至少3件
抽检每批抽取至少3件每批抽取至少3件每批抽取至少3件
抽检每批抽取至少1件每批抽取至少1件每批抽取至少1件每批抽取不少于10件 每批抽取不少于3件
每批抽取至少1件每批抽取至少1件每批抽取至少1件
100%
100%
标识、质量合格证书、包装、运输和储存
8
8.1 标识
锻件应做标识,标识的内容、位置等由供需双方协商确定。 8.2 质量合格证书
锻件质量合格证书应包括以下内容: a) 供方名称或代号; b) 锻件名称、数量、生产日期、出厂日期; c) 锻件材料牌号、化学成分、力学性能; d) 熔炼炉号、热处理炉次; e) 对特殊要求进行补充检验的结论; f) 质量检验及合格标记。 超出上述内容,由供需双方协商确定。
8.3 包装、运输和储存 8.3.1 包装 8.3.1.1 锻件的包装应符合GB/T3199的规定 8.3.1.2 宜单件隔离包装。 8.3.1.3 包装箱应有放置不应上下颠倒的标志以及锻件名称或代号、重量、件数等标识。 8.3.1.4 不应与钢铁类产品或零件混装。 8.3.1.5 应有防水措施。 8.3.2 运输和储存
.
锻件的运输和储存应符合GB/T3199的规定。
5
GB/T34359—2017
参考文 献
[1] GB/T3190 变形铝及铝合金化学成分 [2] YS/T591 变形铝及铝合金热处理
D