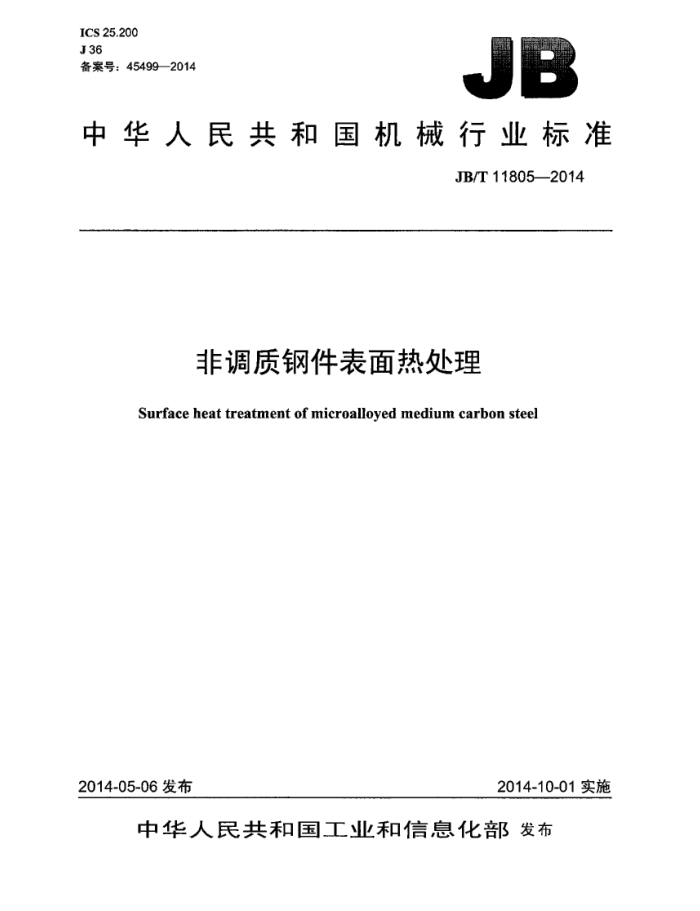
ICS 25.200 J36 备案号:45499—2014
B
中华人民共和国机械行业标准
JB/T11805—2014
非调质钢件表面热处理
Surface heat treatment of microalloyed medium carbon steel
2014-05-06发布
2014-10-01实施
中华人民共和国工业和信息化部发布
JB/T11805—2014
目 次
前言. 1 范围. 2 规范性引用文件. 3 术语和定义 A
.11 .1 .1 .1 .1 .2 .3 .4 .5 .7 .8 .8 .8 .2 .3 .3 .4 .5 .5 .6 .6 .6 .7 .7
.
**
非调质钢件的表面热处理工艺 5 待处理工件,
..
.
.. .
6 感应淬火回火
气体渗氮. 8 气体氮碳共渗 9 离子渗氮, 10 检测设备. 11 产品报告单. 12 安全、卫生要求表1 待处理工件的原始状态表2 感应率火件表面硬度(洛氏)允许偏差范围,表3 感应淬火件表面硬度(维氏)允许偏差范围表4 有效硬化层深度允许偏差范围,表 5 气体渗氮件表面硬度允许偏差范围表6 气体渗氮层深度允许偏差范围表 7 气体氮碳共渗件表面硬度允许偏差范围,表8 气体氮碳共渗层深度表9 气体氮碳共渗层深度允许偏差范围,表10 离子渗氮件表面硬度允许偏差范围表11 离子渗氮层深度允许偏差范围
7
*
FEI
1
JB/T118052014
前 言
本标准按照GB/T1.1一2009给出的规则起草。 本标准由中国机械工业联合会提出。 本标准由全国热处理标准化技术委员会(SAC/TC75)归口。 本标准起草单位:上海市机械制造工艺研究所有限公司、北京机电研究所、辽宁五一八内燃机配件
有限公司、天润曲轴股份有限公司。
本标准主要起草人:蔡红、叶俭、任颂赞、吕东显、孙海涛、姜全会、丛建臣、王开远、邵诗波、 谷韶刚、陈德华、卢军、李光瑾。
本标准为首次发布。
II
JB/T11805—2014
非调质钢件表面热处理
1范围
本标准规定了非调质钢件表面热处理质量控制、安全卫生的基本要求。 本标准适用于非调质钢件的表面感应淬火、气体渗氮、气体氮碳共渗及离子渗氮工艺,
2规范性引用文件
下列文件对于本文件的应用是必不可少的。凡是注日期的引用文件,仅注日期的版本适用于本文件。 凡是不注日期的引用文件,其最新版本(包括所有的修改单)适用于本文件。
GB/T5617 钢的感应淬火或火焰淬火后有效硬化层深度的测定 GB/T7232 金属热处理工艺术语 GB/T11354 钢铁零件渗氮层深度测定和金相组织检验 GB/T 15712 非调质机械结构钢 GB/T15735 金属热处理生产过程安全、卫生要求 GB/T15822.1 无损检测磁粉检测第1部分:总则 GB/T 18177 钢件的气体渗氮 GB/T22560 钢铁件的气体氮碳共渗 JB/T6050 钢铁热处理零件硬度检验通则 JB/T6956 钢铁件的离子渗氮 JB/T9201 钢铁件的感应淬火回火 JB/T9204 钢件感应火金相检验 JB/T9218 无损检测渗透检测
3术语和定义
GB/T7232界定的以及下列术语和定义适用于本文件。
3.1
非调质钢 microalloyedmediumcarbonsteels 不进行调质热处理,通过微合金化、控制轧制(锻制)和控制冷却等强韧化方法,达到或接近调质
钢力学性能的一类优质或特殊质量的结构钢。
4非调质钢件的表面热处理工艺
4.1感应淬火
利用感应电流通过工件所产生的热量,使工件表层、局部加热并快速冷却的淬火。感应淬火工艺适用于含碳量≥0.30%的非调质钢件。
1
JB/T11805—2014
4.2气体渗氮
在可提供活性氮原子的气体中进行渗氮的热处理工艺。非调质钢件气体渗氮工艺温度一般<600℃C。 对贝氏体型非调质钢件的气体渗氮,应考虑基体韧度下降的影响。 4.3气体氮碳共渗
在气体介质中,使工件表层同时渗入氮和碳,并以渗氮为主的热处理工艺。非调质钢件气体氮碳共渗工艺温度一般为600℃。对贝氏体型非调质钢件的气体氮碳共渗,应考虑基体韧度下降的影响。 4.4离子渗氨
在低于1×10’Pa(通常是10Pa~10~Pa)的渗氮气氛中,利用工件(阴极)和阳极之间产生的辉光放电进行渗氮的热处理工艺。非调质钢件离子渗氮工艺温度一般<600℃。对贝氏体型非调质钢件的离子渗氮,应考虑基体韧度下降的影响。
5待处理工件
5.1常用材料
GB/T15712中及其他相关牌号的铁素体-珠光体型和贝氏体型非调质钢件。 5.2待处理工件的原始状态
根据表1规定的项目记录待处理工件的原始状态,并予以保存。
表1待处理工件的原始状态
项 目
备 注
待处理工件的试验数据
工件种类化学成分’ 炼钢炉号力学性能试验数据“ 硬度试验数据金相组织检验记录“
晶粒度、脱碳层、非金属夹杂物、微观及宏观组织
待处理工件的制造方法
锻造轧制机械加工
有无预先热处理
正火表面加工品质及矫正精度”
切(磨)削方法及其条件有光矫正 “对表面热处理无妨碍时可省略。
2
JB/T11805--2014
6感应淬火回火
6.1预处理要求
感应火回火工艺前的工件一般为锻造或轧制状态,但不允许有晶粒粗大现象,晶粒度一般应控制在5级以上,否则应进行正火处理以细化晶粒。 6.2感应淬火回火处理工艺
感应淬火回火处理工艺应符合JB/T9201的规定。可根据.T.件形状、材料牌号、设备条件和试验结果,确定加热工艺参数和冷却工艺参数。工件应在淬火后及时回火,回火温度的选择应使工件达到规定的技术要求,也可采用自回火的方法。 6.3品质要求及检验 6.3.1外观 6.3.1.1感应淬火回火后工件的表面不应有裂纹、烧伤及影响使用的伤痕等缺陷。 6.3.1.2外观检验采用目测或低倍放大镜观察,必要时可根据GB/T15822.1、JB/T9218规定的方法进行检验。 6.3.2表面硬度
感应火回火件的表面硬度应按JB/T6050或其他技术上约定的硬度检验方法进行检验,表面硬度偏差应符合表2或表3的规定。
表2感应淬火件表面硬度(洛氏)允许偏差范围
单件 >50~60 ≤4.5 ≤5.5
同批件 >50~60 ≤5.5 ≤6.5
工件类型表面硬度HRC
≤50 5 ≤6
>60 ≤4 5
≤50 ≤6 7
>60 5 M6
硬度允许 重要件HRC 偏差范围 一般件HRC
注1:单件的表面硬度允许偏差指的是在同样淬火回火或萍火条件下,在形状、尺寸相同的部位所测得的偏差。 注2:同批件是对用同一批待处理工件在同一操作条件下处理得到的工件的总称。 注3:具体硬化部位的表面硬度允许偏差范围可由委托方与受托方协商确定。
表3感应淬火件表面硬度(维氏)允许偏差范围
单件
工件类型表面硬度HV
同批件
≤500 ≤55 ≤75
>500 ≤85 ≤105
≤500 ≤75 ≤95
>500 》105 ≤125
硬度允许偏差范围注1:单件的表面硬度允许偏差指的是在同样淬火回火或火条件下,在形状、尺寸相同的部位所测得的偏差。 注2:同批件是对用同一批待处理工件在同一操作条件下处理得到的工件的总称注3:具体硬化部位的表面硬度允许偏差范围可由委托方与受托方协商确定。
重要件HV 一般件HV
6.3.3有效硬化层深度
有效硬化层深度的检验应按GB/5617或委托方与受托方协商的规定执行。工件有效硬化层深度偏差应符合表4的规定。
3
JB/T11805-2014
表4有效硬化层深度允许偏差范围
单位为毫米
允许偏差范围
有效硬化层深度
单件 ≤0.2 ≤0.4 ≤0.6 ≤0.8 ≤1.0
同批件 ≤0.4 ≤0.6 ≤0.8 ≤1.0 ≤1.5
≤1.5 >1.5~2.5 >2.5~3.5 >3.5~5.0 >5.0
注1:单件的有效硬化层深度允许偏差指的是在同样淬火回火或萍火条件下,在形状、尺寸相同的部位所测得的偏差。 注2:同批件是对用同一批待处理工件在同一操作条件下处理得到的工件的总称。 注3:具体硬化部位的允许偏差范围可由委托方与受托方协商确定。
6.3.4金相组织
金相组织的检验应符合JB/T9204的规定,验收标准应由委托方与受托方协商确定。 6.3.5畸变
工件的畸变应不影响后续的机械加工及使用。具体的允许畸变量应当由委托方与受托方协商确定。 6.3.6 6检验方式
可采用与工件材料相同、状态相同的随炉试样进行检验。若要在工件上检验,具体要求应当由委托方与受托方协商确定。
7 气体渗氨
7.1 预处理要求
气体渗氮前的工件一般为锻造或轧制状态,但不允许有晶粒粗大现象,晶粒度一般应控制在5级以上,否则应进行正火处理以细化晶粒。 7.2气体渗氮处理工艺
气体渗氮处理工艺应符合GB/T18177的规定。在渗氮层深度相同的条件下,非调质钢件的气体渗氮时问可适当缩短。 7.3品质要求及检验 7.3.1外观 7.3.1.1外观检验采用目测。表面不应有裂纹、剥落及肉眼可见的疏松等缺陷;在硬度、渗氮层深度和脆性等各项均合格的前提下,渗氮件表面允许存在氧化色。 7.3.1.2对裂纹等缺陷也可采用磁粉或渗透检测等方法进行检验,检验方法应符合GB/T15822.1、JB/T 9218的规定。 7.3.2表面硬度
气体渗氮件的表面硬度应按JB/T6050或其他技术上约定的硬度检验方法进行检验,表面硬度偏差应符合表5的规定。 4
JB/T11805--2014
表5 5气体渗氮件表面硬度允许偏差范围
单件
同批件
工件类型表面硬度HV
>600 ≤60
≤600 ≤70
>600 ≤100
≤600 ≤45
硬度允许偏差范围HV 注1:同批件是指用相同钢材、经相同预备热处理,并在同一炉次进行渗氮处理后的一组工件。 注2:局部渗氨件的测定位置距渗氨边界的距离应不小于渗层深度值。 注3:具体硬化部位的表面硬度允许偏差范围可由委托方与受托方协商确定。
7.3.3 渗氨层深度
气体渗氮层深度的检验应符合GB/T11354的规定。渗氮件应达到工艺要求的渗氮层深度,其深度偏差应符合表6的规定。
单位为毫米
表6 气体渗氮层深度允许偏差范围
允许偏差范围
渗氮层深度
同批件 ≤0.10 ≤0.15 ≤0.20
单件 ≤0.05 ≤0.10 ≤0.15
<0.3 ≥0.3~0.6 >0.6
注1:同批件是指用相同钢材、经相同预备热处理,并在间一炉次进行渗氮处理后的一组工件。 注2:局部渗氮件的测定位置距渗氮边界的距离应不小于渗层深度值的2倍。 注3:具体硬化部位的渗氮层深度允许偏差范围可由委托方与受托方协商确定,
7.3.4 金相组织
金相组织的检验应符合GB/T11354的规定,验收标准应由委托方与受托方协商确定。 7.3.5畸变
工件的畸变应不影响后续的机械加工及使用。具体的允许畸变量应当由委托方与受托方协商确定。 7.3.6 6检验方式
可采用与工件材料相同、状态相同的随炉试样进行检验。若要在工件上检验,具体要求应当由委托与受托方协商确定。
8气体氮碳共渗
8.1预处理要求
气体氮碳共渗前的工件一般为锻造或轧制状态,但不允许有晶粒粗大现象,晶粒度一般应控制在5 级以上,否则应进行正火处理以细化晶粒。 8.2气体氮碳共渗处理工艺
气体氮碳共渗工艺应符合GB/T22560的规定。常用的气体氮碳共渗温度为520~570℃。
5
ICS 25.200 J36 备案号:45499—2014
B
中华人民共和国机械行业标准
JB/T11805—2014
非调质钢件表面热处理
Surface heat treatment of microalloyed medium carbon steel
2014-05-06发布
2014-10-01实施
中华人民共和国工业和信息化部发布
JB/T11805—2014
目 次
前言. 1 范围. 2 规范性引用文件. 3 术语和定义 A
.11 .1 .1 .1 .1 .2 .3 .4 .5 .7 .8 .8 .8 .2 .3 .3 .4 .5 .5 .6 .6 .6 .7 .7
.
**
非调质钢件的表面热处理工艺 5 待处理工件,
..
.
.. .
6 感应淬火回火
气体渗氮. 8 气体氮碳共渗 9 离子渗氮, 10 检测设备. 11 产品报告单. 12 安全、卫生要求表1 待处理工件的原始状态表2 感应率火件表面硬度(洛氏)允许偏差范围,表3 感应淬火件表面硬度(维氏)允许偏差范围表4 有效硬化层深度允许偏差范围,表 5 气体渗氮件表面硬度允许偏差范围表6 气体渗氮层深度允许偏差范围表 7 气体氮碳共渗件表面硬度允许偏差范围,表8 气体氮碳共渗层深度表9 气体氮碳共渗层深度允许偏差范围,表10 离子渗氮件表面硬度允许偏差范围表11 离子渗氮层深度允许偏差范围
7
*
FEI
1
JB/T118052014
前 言
本标准按照GB/T1.1一2009给出的规则起草。 本标准由中国机械工业联合会提出。 本标准由全国热处理标准化技术委员会(SAC/TC75)归口。 本标准起草单位:上海市机械制造工艺研究所有限公司、北京机电研究所、辽宁五一八内燃机配件
有限公司、天润曲轴股份有限公司。
本标准主要起草人:蔡红、叶俭、任颂赞、吕东显、孙海涛、姜全会、丛建臣、王开远、邵诗波、 谷韶刚、陈德华、卢军、李光瑾。
本标准为首次发布。
II
JB/T11805—2014
非调质钢件表面热处理
1范围
本标准规定了非调质钢件表面热处理质量控制、安全卫生的基本要求。 本标准适用于非调质钢件的表面感应淬火、气体渗氮、气体氮碳共渗及离子渗氮工艺,
2规范性引用文件
下列文件对于本文件的应用是必不可少的。凡是注日期的引用文件,仅注日期的版本适用于本文件。 凡是不注日期的引用文件,其最新版本(包括所有的修改单)适用于本文件。
GB/T5617 钢的感应淬火或火焰淬火后有效硬化层深度的测定 GB/T7232 金属热处理工艺术语 GB/T11354 钢铁零件渗氮层深度测定和金相组织检验 GB/T 15712 非调质机械结构钢 GB/T15735 金属热处理生产过程安全、卫生要求 GB/T15822.1 无损检测磁粉检测第1部分:总则 GB/T 18177 钢件的气体渗氮 GB/T22560 钢铁件的气体氮碳共渗 JB/T6050 钢铁热处理零件硬度检验通则 JB/T6956 钢铁件的离子渗氮 JB/T9201 钢铁件的感应淬火回火 JB/T9204 钢件感应火金相检验 JB/T9218 无损检测渗透检测
3术语和定义
GB/T7232界定的以及下列术语和定义适用于本文件。
3.1
非调质钢 microalloyedmediumcarbonsteels 不进行调质热处理,通过微合金化、控制轧制(锻制)和控制冷却等强韧化方法,达到或接近调质
钢力学性能的一类优质或特殊质量的结构钢。
4非调质钢件的表面热处理工艺
4.1感应淬火
利用感应电流通过工件所产生的热量,使工件表层、局部加热并快速冷却的淬火。感应淬火工艺适用于含碳量≥0.30%的非调质钢件。
1
JB/T11805—2014
4.2气体渗氮
在可提供活性氮原子的气体中进行渗氮的热处理工艺。非调质钢件气体渗氮工艺温度一般<600℃C。 对贝氏体型非调质钢件的气体渗氮,应考虑基体韧度下降的影响。 4.3气体氮碳共渗
在气体介质中,使工件表层同时渗入氮和碳,并以渗氮为主的热处理工艺。非调质钢件气体氮碳共渗工艺温度一般为600℃。对贝氏体型非调质钢件的气体氮碳共渗,应考虑基体韧度下降的影响。 4.4离子渗氨
在低于1×10’Pa(通常是10Pa~10~Pa)的渗氮气氛中,利用工件(阴极)和阳极之间产生的辉光放电进行渗氮的热处理工艺。非调质钢件离子渗氮工艺温度一般<600℃。对贝氏体型非调质钢件的离子渗氮,应考虑基体韧度下降的影响。
5待处理工件
5.1常用材料
GB/T15712中及其他相关牌号的铁素体-珠光体型和贝氏体型非调质钢件。 5.2待处理工件的原始状态
根据表1规定的项目记录待处理工件的原始状态,并予以保存。
表1待处理工件的原始状态
项 目
备 注
待处理工件的试验数据
工件种类化学成分’ 炼钢炉号力学性能试验数据“ 硬度试验数据金相组织检验记录“
晶粒度、脱碳层、非金属夹杂物、微观及宏观组织
待处理工件的制造方法
锻造轧制机械加工
有无预先热处理
正火表面加工品质及矫正精度”
切(磨)削方法及其条件有光矫正 “对表面热处理无妨碍时可省略。
2
JB/T11805--2014
6感应淬火回火
6.1预处理要求
感应火回火工艺前的工件一般为锻造或轧制状态,但不允许有晶粒粗大现象,晶粒度一般应控制在5级以上,否则应进行正火处理以细化晶粒。 6.2感应淬火回火处理工艺
感应淬火回火处理工艺应符合JB/T9201的规定。可根据.T.件形状、材料牌号、设备条件和试验结果,确定加热工艺参数和冷却工艺参数。工件应在淬火后及时回火,回火温度的选择应使工件达到规定的技术要求,也可采用自回火的方法。 6.3品质要求及检验 6.3.1外观 6.3.1.1感应淬火回火后工件的表面不应有裂纹、烧伤及影响使用的伤痕等缺陷。 6.3.1.2外观检验采用目测或低倍放大镜观察,必要时可根据GB/T15822.1、JB/T9218规定的方法进行检验。 6.3.2表面硬度
感应火回火件的表面硬度应按JB/T6050或其他技术上约定的硬度检验方法进行检验,表面硬度偏差应符合表2或表3的规定。
表2感应淬火件表面硬度(洛氏)允许偏差范围
单件 >50~60 ≤4.5 ≤5.5
同批件 >50~60 ≤5.5 ≤6.5
工件类型表面硬度HRC
≤50 5 ≤6
>60 ≤4 5
≤50 ≤6 7
>60 5 M6
硬度允许 重要件HRC 偏差范围 一般件HRC
注1:单件的表面硬度允许偏差指的是在同样淬火回火或萍火条件下,在形状、尺寸相同的部位所测得的偏差。 注2:同批件是对用同一批待处理工件在同一操作条件下处理得到的工件的总称。 注3:具体硬化部位的表面硬度允许偏差范围可由委托方与受托方协商确定。
表3感应淬火件表面硬度(维氏)允许偏差范围
单件
工件类型表面硬度HV
同批件
≤500 ≤55 ≤75
>500 ≤85 ≤105
≤500 ≤75 ≤95
>500 》105 ≤125
硬度允许偏差范围注1:单件的表面硬度允许偏差指的是在同样淬火回火或火条件下,在形状、尺寸相同的部位所测得的偏差。 注2:同批件是对用同一批待处理工件在同一操作条件下处理得到的工件的总称注3:具体硬化部位的表面硬度允许偏差范围可由委托方与受托方协商确定。
重要件HV 一般件HV
6.3.3有效硬化层深度
有效硬化层深度的检验应按GB/5617或委托方与受托方协商的规定执行。工件有效硬化层深度偏差应符合表4的规定。
3
JB/T11805-2014
表4有效硬化层深度允许偏差范围
单位为毫米
允许偏差范围
有效硬化层深度
单件 ≤0.2 ≤0.4 ≤0.6 ≤0.8 ≤1.0
同批件 ≤0.4 ≤0.6 ≤0.8 ≤1.0 ≤1.5
≤1.5 >1.5~2.5 >2.5~3.5 >3.5~5.0 >5.0
注1:单件的有效硬化层深度允许偏差指的是在同样淬火回火或萍火条件下,在形状、尺寸相同的部位所测得的偏差。 注2:同批件是对用同一批待处理工件在同一操作条件下处理得到的工件的总称。 注3:具体硬化部位的允许偏差范围可由委托方与受托方协商确定。
6.3.4金相组织
金相组织的检验应符合JB/T9204的规定,验收标准应由委托方与受托方协商确定。 6.3.5畸变
工件的畸变应不影响后续的机械加工及使用。具体的允许畸变量应当由委托方与受托方协商确定。 6.3.6 6检验方式
可采用与工件材料相同、状态相同的随炉试样进行检验。若要在工件上检验,具体要求应当由委托方与受托方协商确定。
7 气体渗氨
7.1 预处理要求
气体渗氮前的工件一般为锻造或轧制状态,但不允许有晶粒粗大现象,晶粒度一般应控制在5级以上,否则应进行正火处理以细化晶粒。 7.2气体渗氮处理工艺
气体渗氮处理工艺应符合GB/T18177的规定。在渗氮层深度相同的条件下,非调质钢件的气体渗氮时问可适当缩短。 7.3品质要求及检验 7.3.1外观 7.3.1.1外观检验采用目测。表面不应有裂纹、剥落及肉眼可见的疏松等缺陷;在硬度、渗氮层深度和脆性等各项均合格的前提下,渗氮件表面允许存在氧化色。 7.3.1.2对裂纹等缺陷也可采用磁粉或渗透检测等方法进行检验,检验方法应符合GB/T15822.1、JB/T 9218的规定。 7.3.2表面硬度
气体渗氮件的表面硬度应按JB/T6050或其他技术上约定的硬度检验方法进行检验,表面硬度偏差应符合表5的规定。 4
JB/T11805--2014
表5 5气体渗氮件表面硬度允许偏差范围
单件
同批件
工件类型表面硬度HV
>600 ≤60
≤600 ≤70
>600 ≤100
≤600 ≤45
硬度允许偏差范围HV 注1:同批件是指用相同钢材、经相同预备热处理,并在同一炉次进行渗氮处理后的一组工件。 注2:局部渗氨件的测定位置距渗氨边界的距离应不小于渗层深度值。 注3:具体硬化部位的表面硬度允许偏差范围可由委托方与受托方协商确定。
7.3.3 渗氨层深度
气体渗氮层深度的检验应符合GB/T11354的规定。渗氮件应达到工艺要求的渗氮层深度,其深度偏差应符合表6的规定。
单位为毫米
表6 气体渗氮层深度允许偏差范围
允许偏差范围
渗氮层深度
同批件 ≤0.10 ≤0.15 ≤0.20
单件 ≤0.05 ≤0.10 ≤0.15
<0.3 ≥0.3~0.6 >0.6
注1:同批件是指用相同钢材、经相同预备热处理,并在间一炉次进行渗氮处理后的一组工件。 注2:局部渗氮件的测定位置距渗氮边界的距离应不小于渗层深度值的2倍。 注3:具体硬化部位的渗氮层深度允许偏差范围可由委托方与受托方协商确定,
7.3.4 金相组织
金相组织的检验应符合GB/T11354的规定,验收标准应由委托方与受托方协商确定。 7.3.5畸变
工件的畸变应不影响后续的机械加工及使用。具体的允许畸变量应当由委托方与受托方协商确定。 7.3.6 6检验方式
可采用与工件材料相同、状态相同的随炉试样进行检验。若要在工件上检验,具体要求应当由委托与受托方协商确定。
8气体氮碳共渗
8.1预处理要求
气体氮碳共渗前的工件一般为锻造或轧制状态,但不允许有晶粒粗大现象,晶粒度一般应控制在5 级以上,否则应进行正火处理以细化晶粒。 8.2气体氮碳共渗处理工艺
气体氮碳共渗工艺应符合GB/T22560的规定。常用的气体氮碳共渗温度为520~570℃。
5