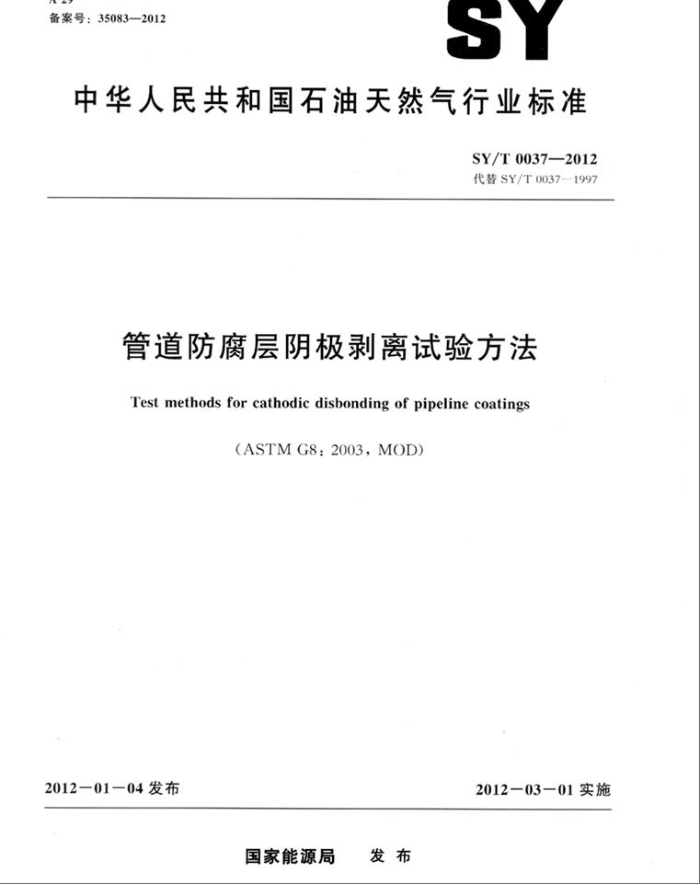
SY
备案号:35083—2012
中华人民共和国石油天然气行业标准
SY/T00372012 代替SY/T0037-—1997
管道防腐层阴极剥离试验方法
Test methods for cathodic disbonding of pipeline coatings
(ASTMG8:2003.MOD)
2012一01一04发布
2012-03—01实施
国家能源局 发布
SY/T0037—2012
目 次
前言
-
范围 2 规范性引用文件 3 概述
1
试剂和材料 n 仪器和设备 6 试件
-
2
试件准备方法A的步骤
5
9 方法B的步骤 10 试验报告 11 精度与偏差附录A(资料性附录) 管道防腐层阴极剩离试验的数据表
…下一页
SY/T00372012
前言
本标准按照GB/T1.1-2009《标准化工作导则 第1部分:标准的结构和编写》给出的规则起草。
本标准代替SY/T0037一1997《管道防腾层阴极剥离试验方法》。与SY/T0037—1997相比:除编辑性修改外,主要技术变化如下:
修改广前育:增加了ASTMG8:1996(2003确认)中1.2的内容(见第1章,1997年版的第1章);标题“引用标准”改为“规范性引用文件”,引人GB/T1.1的导语,增加了相关的引用标准(见第2章,1997年版的第2章): - 将“钻头直径应大于防腐层厚度的三倍,且不得小于6mm”修改为“钻头直径应大于防脚层厚度的三倍,且不得小于6.4mm”(见6.2,1997年版的7.2):将.....但没没面积不应小于2.3×10mm,条件许可时,以9.3×10mm的面积最为适宜改为“...*-但浸没面积不应小于23227mm,以92900mm的面积最为适宜”(见6.5. 1997年版的7.4);
一合并了1997年版的第3章和第4章,并删除了1997年版的3.5;
工修改了人为缺陷孔的位置(见图3和图4,1997年版的图2和图4);
修改了电位值,将*-1.45V~-1.55V(CSE)”改为”-1.38V~-1.48V(饱和甘秉电极)”(见5.1.2和8.2,1997年版的6.1和9.2):将1997年版的公式(1)移到了11.3中(见11.3,1997年版第11章): “精密度”改为“精度与偏差”(见第11章,1997年版第12章): 1997年版的附录A(标准的附录)改为附录A(资料性的附录)(见附录A,1997年版的附录A)。
本标准是以美国材料试验学会ASTMG8:1996(2003确认)《管道防层阴极刹离性能试验方法》为基础形成的标准,与ASTMG8:1996(2003确认)的一致性程度为修改。
本标准由中国石油管道学院负责解释。在执行过程中,请各单位结合工程实践,认真总结经验。 注意积累资料,如发现本标准有需要修改和补充之处。请将意见和建议寄到中国石油管道学院(地址:廊坊市爱民西道90号,邮编:065000)。
本标准由石油工程建设专业标准化委员会提出并归口。 本标准起草单位:中国石油管道学院、 本标准参编单位:中国石油管道科技研究中心,本标准主要起草人:李桂芝、王营、苏丽珍、王德增、成昱辉、陈建忠
SY/T0037—2012
管道防腐层阴极剥离试验方法
1范围
1.1本标准规定了测定管道防魔层阴极离性能的加速试验方法。 1.2本标准适用于施加阴极保护的埋地管道绝缘外防腐层阴极剥离对比性能的测定 1.3本标准可用于室温下检验浸泡溶液中的防胸层,若试件不能放入溶液,可采用SY/T0094。 1.4本标准包括方法A和方法B两种试验方法,可自由选择,但应在试验报告中注明。
2规范性引用文件
下列文件对于本文件的应用是必不可少的,凡是注日期的引用文件,仅注日期的版本适用于本文件。凡是不注日期的引用文件:其最新版本(包括所有的修改单)适用于本文件
SY/T0066 钢管防腐层厚度的无损测量方法(磁性法)(SY/T0066一1999,ASTMG12: 1992.MOD)
SY/T0094 管道防腐层阴极刹离试验方法(粘结电解槽法)(SY/T0094—1999ASTMG19X) ASTMG95:1992.MOD)
3概述
3.1意义和用途 3.1.1在管道的运输和数设过程中,儿乎不可避免地会损坏防腐层。管道埋地后,由于土填电解质的作用,管道防腐层在破损处就有可能受到蚀。正常的土壤电位以及施加的阴极保护电位,都会使防腐层在漏点处产生剥离。本试验方法提供了一种使防腐层产生加速剥离的条件,用来测定防腐层的抗阴极刺离性能, 3.1.2试验结果可通过直观检查或通过监测试件的电流来得出,通常这两种方法之问没有相关性,但两种方法都很重要。传统直观检查方法是由观测到的相对黏结能力的差异,来评价防腐层和金属表面的有效黏结强度。受电应力的影响,漏点范明会扩展到试件防胸层与金属表面有效黏结的边缘而停止,与监测结果有关的慢设包括:
a)采用剥离技术,对未浸泡的新制作对比孔处的防腾层进行松脱或剥离,该处的附着力代表测
量时最大的附着力或黏结力。而在浸泡区域的检测孔上,使用同样的刺离技术,提供了一种比较防腾层抗剩离性能的方法:
b)在没泡区域防腐层的检测孔上,任何相对黏结力较小的区域都是由电应力引起的,而不是
由于涂激工艺所造成的。抗阴极剥离能力是在比较的基础上得出的理想性能,但在这个试验里,刹离本身不一定就是一项不利的指标。由于目前通用的所有绝缘类型的防腐层都在某种程度上发生剩离,因此,这项试验的优点就在于提供了将一种防腐层与另一种防腐层相互比较的手段:黏结强度对某些防腐层的固有特性米说,比其他性能更重要,而两种不同的防胸层即使具有相同的刺离,也不意味着他们丧失了相同的防腐能力
c) 试验电路中的电流密度值是判断防腐层刺离强度的相对指标。而这种试验的电流密度值通常
1
SY/T0037—2012
要比土壤环境中阴极保护所需要的大得多。
3.2方法概述
3.2.1本标准的两种方法中,试件浸人高导电的碱性电解液中,防腾层受到电应力的作用,电应力可通过镁阳极或强制电流装置面获得。在开始测试前,防腐层应钻人为缺陷孔。 3.2.2在方法A里,用镁阳极提供试件与阳极间的电位差,且在试验期间无需电参数监控。在试验周期结束后,其试验结果用直观检查方法确定。 3.2.3在方法B里,镁阳极或强制电流装置均可使用。但应测量电路中的电流及电位,并在试验周期结束时直观检查试件。 3.2.4无论使用哪种方法,其直观检查都是通过比较试件浸泡区域人为缺陷孔和未浸没区域的新制作的对比孔处防腐层的松脱和剥离程度来实现的。
4试剂和材料
4.1电解液:用自米水加人质量分数各为1%的工业纯无水氟化钠、无水硫酸钠、无水碳酸钠配制而成,且必须现用现配。 4.2试件的端头密封材料:可采用沥青制品、石蜡、环氧树脂或其他材料,包括模铸的合成橡胶或塑料瑙帽。 4.3试验槽盖板:可用胶合板或塑料板制作,盖板上应留有供试件、阳极等穿过的孔,穿过试件顶部孔的木制销钉应将试件悬挂在槽盖上。
5 仪器和设备
5.1 方法A和方法B共用的仪器和设备 5.1.1 试验槽:用不导电材料制作的非金属槽或内村为不导电材料的金属槽。楷的尺寸应满足以下要求:
a) 试件应在槽内垂直悬挂,其下端与植底的距离应不小于25mm。 b) 试件之间、试件与阳极及槽壁之间以及参比电极与阳极之间的距离应不小于38mm。 e) 按a),b)和6.5的要求确定试验精的容积,且情的高度应能使试件的测试段浸人电解
液中。 如果按照方法B,使用电监控,可将参比电极放置在槽内任何位置,它与试件、与阳极的距离应
不小于38mm。 5.1.2镁阳极:由镁合金制成,在按4.1配制的电解液中,其电位应-1.38V~-1.48V(饱和甘汞电极)之间。阳极表面积不得小于全部试件浸没面积的1/3,镁阳极的端头应伸出试验槽盖板。 5.1.33 连接线:线芯标称截面不小于2mm的绝缘铜导线。 5. 1.4 钻孔和直观检查的工具:钻孔用普通钻头,直径按6.2的规定:直观检套用带安全柄的尖刀。 5.1.5 直流电压表:测量相对于参比电极的电位,内阻大于10Ma,量程0.01V~5V。 5.1.63 参比电极:铜/硫酸铜(饱和)电极,直径不宜超过19mm,其相对于标准氢电极的电位为 -0.316V.也可使用饱和甘汞电极,但必须将观测到的读数加上-0.072V,以换算成相对于铜/硫酸铜(饱和)电极的数值。
注:在本标准中规定:以标准氢电极作为阴极、以给定电极作为阳极组成原电池,此电池的电动势为给定电极的
电极电位,按此规定,钢/硫酸钢(饱和)电极和饱和甘求电极相对于标准氢电极的电位均为负值。
5.1.7 磁性测厚仪:测量范围为1um~20mm,精度为量程的±2%。 2
SY/T0037—2012
5.1.8水银温度计:量程为0℃100℃,最小分度值为1℃,浸没深度76mm。 5.1.9平面求积仪:精确度为0.5%
5.2方法B中增加的仪器和设备
5.2.1 直流电压表:内阻大于10M0,分辨率10xV。 5.2.2 标准电阻:1Q土0.012,功率不小于1W。 5.2.3 兆欧表:额定输出电压小于1000V,量程为0M~2000MQ, 5.2.4 金属电极:可采用不锈钢电极 5.2.56 黄铜接线柱:接线柱的直径不应小于6mm。 5.2.6 零阻电流表:该表应能测出10A以下的直流电流。 5.2.7 直流稳压电源:可提供试件和参比电极之间实测到的恒定在(3+0.01)V的电压。 5.2.8 辅助阳极:应采用低消耗率的金属阳极,用密封的绝缘铜导线连接,或将阳极上端伸出槽盖外。 5.2.9变阻器:1000,25W的绕线电位器,用于如图6所示的多个试件的检测、
6试件
6.1试件应取可代表工业生产情况的防离管,其中一端应封堵或使用端帽加以密封。 6.2每个试件上应钻一个或三个人为缺陷孔,推存采用三个孔。图1标明了试件的推荐尺寸,单孔试件应将孔钻在没没段的中间:如钻三个孔,孔的方位应各相差120°,中孔钻在没没段的中间,另外两个孔分别位于距离浸没线和试件底端1/4处。每个孔要钻到使维部完全进入钢管壁,且维部边缘与钢管外表面齐平。钻头直径应大于防腐层厚度的三倍,且不得小于6.4mm。管壁不得钻透。对于小口径的试件,可先用一个标准60的钻头开钻,最后用平头钻头来完成 6.3伸出试验槽盖板的管端可用穿过上端孔的销钉支撑,并连有单独的导线供电测用。所有连接接点应采用锡焊、铜焊或螺栓牢固连接,并用绝缘材料保护和密封。
注:在制作人为缺陷孔之前,请参看7.1的要求, 6.4如有露出液面的管段,要有合适的支撑,并连有单独的导线用于电测。所有连接点用锡或钢焊牢,或者将导线拴接到管端上,伸出槽外的管端包括支架和导线连接的伸出端。均用绝缘防腐材料保护和密封 6.5从试件端部密封边缘到浸没线之间的面积为测试面积,端部密封区域不应视作测试面积。试件可选用适当直径和长度的防腐管,但浸没面积不应小于23227mm,以92900mm的面积最为适宜。
7试件准备
7.1在制作人为缺陷孔之前,应按下列做法检验防腐层的连续性和端密封的有效性。 7.1.1把试件与金属电极浸没于电解液中,将兆欧表的一端与试件连接,另一端接到金属电极上,测出试件的表观电阻,然后将兆欧表的接头对调再测一次,并记录测试结果。 7.1.2将试件与兆欧表断开,没没15min,然后按7.1.1的要求再测试件的表观电阻, 7.1.3若试件15min后的表观电阻明品减小,则表明防腐层或端部密封有漏点,如漏点在防腐层上,则试件应报废:如漏点在端部密封处,则应修补。修补完毕再按7.1.1和7.1.2的要求重新测试。 7.1.4浸没15min后的最低电阻值不宜小于1000M0,如表观电阻在浸没15min前后的测试中均保持小于1000MQ的稳定值,可以认为防虞层不存在裂缝或缺陷,试件仍可使用。试验报告中应列出
3
SY/T0037—2012
8方法A的步骤
8.1按图2所示将试件与阳极浸入电解液中并连接起来,中间缺陷孔或单个缺陷孔应背向阳极。在试验槽上标明浸没线的位置,每天加水保持液位。电解液的温度应保持在21℃~25℃之间 8.2在试验开始和结束前,应测量试件和参比电极之间的电位测试时采用图2所示的临时接线,其电位值应在-1.38V~=1.48V(饱和甘汞电极)之间。参比电极仅在测量时浸人电解液中。
销钉
连接线
栓接的接线片
真流电压表
翁时接线
参比电极
浸没线
试验槽盖板
预密封的阳极导线人为缺陷孔镁阳极试验精电解液
格福
店
试件的密封遇头
图2 用镁阳极时方法A的测试装置
8.3:试验周期应为30d,也可为60d或90d 8.4当试验周期结束时,应立即做以下测试:
a) 取出试件并用温水轻轻地冲洗浸没区,直观检查试件在浸没区是否出现新的涌点以及所有漏
点(包括人为缺陷孔)边缘防腐层的松脱情况,记录防腐层的状况,如颜色、气泡、裂纹、 附着物等。
b) 采用图1推荐的位置并按6.2中人为缺陷孔的钻孔方法,在没没线以上未没没的防层上,
距试验盖板和浸没线约1/2处钻一个新的对比孔。 以对比孔和人为缺陷孔为原点,按图3在孔周围的防随层上用锋利的小刀做一个径向45的横向切口,要注意确保防腐层被完全切透到钢管表面。
)
d) 用刀尖尝试着挑起对比孔和人为缺陷孔处的防痴层,以对比孔处防腐层的黏结程度为参考,
将那些比对比孔更易挑起或剥离的防腐层面积定为剥离面积。 e) 将半透明坐标纸罩在人为缺陷孔上面出挑起区域的轮席,用平面求积仪或用计算坐标纸上方
格数的方法得出人为缺陷孔的挑起而积。用同样方法求得对比孔的挑起面积,两者之差即为刹离面积。
9方法B的步骤
9.1除按8.18.3的要求进行试验外,还应按以下要求进行试验。
s