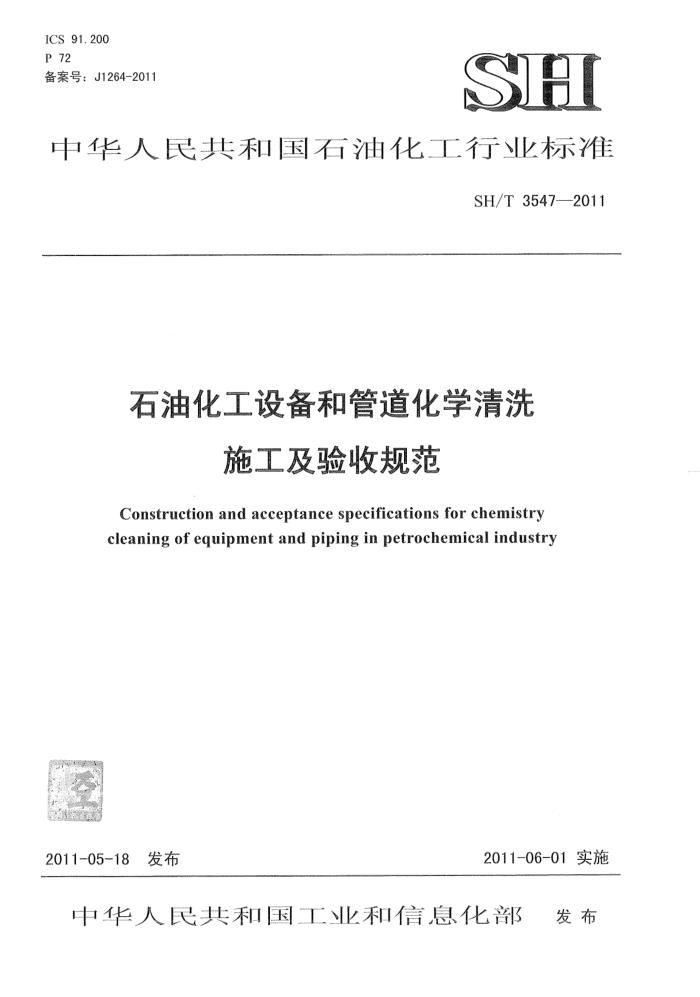
ICS 91.200 P 72 备案号:J1264-2011
SH
中华人民共和国石油化工行业标准
SH/T 3547—2011
石油化工设备和管道化学清洗
施工及验收规范
Construction and acceptance specifications for chemistry cleaning of equipment and piping in petrochemical industry
2011-05-18发布
2011-06-01实施
中华人民共和国工业和信息化部 发布
SH/T35472011
目 次
前言
范围 2 规范性引用文件 3 术语和定义 4 总则· 5 施工准备 5. 1 材料机具准备 5. 2 技术准备 5.3 作业条件.
1
化学清洗方法·· 6. 1 ·般要求· 6.2 循环清洗 6.3 浸泡清洗:
6
化学清洗质量标准 8 安全技术要求 8.1 一般规定 8.2 酸碱作业 8.3.脱脂作业 9交工技术文件:附录A(资料性附录)化学药剂特性及常用的清洗配方附录B(规范性附录)化学清洗的基本程序附录C(资料性附录)化学清洗操作流程附录D(规范性附录)腐蚀率、腐蚀量及除垢率的测定.. 附录E(资料性附录)化学清洗中的测试方法附录F(规范性附录)钝化膜的检验用词说明附:条文说明
T
电
10
20
2
23
SH/T 3547--2011
前言
根据国家发展和改革委员会办公厅《2007年行业标准修订、制定计划》(发改办工业[2007] 1415号)的要求,规范编制组经广泛调查研究,认真总结实践经验,参考有关国际标准和国外先进标准,并在广泛征求意见的基础上,制定本规范。
本规范共分9章和6个附录。 本规范的主要技术内容是:施工准备;化学清洗方法;化学清洗质量标准;安全技术要求。 本规范由中国石油化工集团公司负责管理,由中国石油化工集团公司施工技术淄博站负责日常
管理,由中国石化集团第十建设公司负责具体技术内容的解释。执行过程中如有意见和建议,请寄送日常管理单位和主编单位。
本规范日常管理单位:中国石油化工集团公司施工技术淄博站
通讯地址:山东省淄博市临淄区建设路29号邮政编码:255438 电 话:0533-6295840 传 真:0533-7501126
本规范主编单位:中国石化集团第十建设公司
通讯地址:淄博市临淄区建设路29号邮政编码:255438
本规范参编单位:蓝星环境工程有限公司本规范主要起草人员:杜宗岚 赵喜平 张学发 焦永涛 陈淑芬 张继军 伊祖良本规范主要审查人员:赵珍祥 葛春玉 张发有 汪庆华 单承家 张桂红 蔡隆展 束志军
徐明才 林明良 许锋雪 陈绍福 凌敏华
本规范为首次发布。
III
SH/T3547-2011
石油化工设备和管道化学清洗施工及验收规范
1范围
本规范规定了石油化工设备和管道化学清洗的技术和质量要求及试验方法。 本规范适用于石油化工新建、改建、扩建工程的设备和管道系统的化学清洗。检修工程设备和管
道的化学清洗可参照使用。 2规范性引用文件
下列文件中的条款通过本规范引用而成为本规范的条款。凡是注明日期的引用文件,其后所有的修改单(不包括勘误的内容)或修改版均不适用于本规范,然而,鼓励根据本规范达成协议的各方研究是否可使用这些文件的最新版本。凡是不注明日期的引用文件,其最新版本适用于本规范。
GB8978污水综合排放的标准 GB50484,石油化工建设工程施工安全技术规范 HG/T3523冷却水化学处理标准腐蚀试片技术条件 HG20202 脱脂工程施工及验收规范 SH/T3503 石油化工建设工程项目交工技术文件规定 SH/T3543石油化工建设工程项自过程技术文件规定
3术语和定义 3.1
化学清洗chemistrycleaning 采用化学药剂及其水溶液除去被清洗设备和管道表面污物、氧化物、腐蚀产物等,达到表面清洁
的方法。 3.2
循环清洗cyclecleaning 通过循环泵将清洗液注入清洗设备和管道进行循环,达到系统清洁的方法。
3. 3
浸泡清洗immersingcleaning 将被清洗件放置在盛有清洗液的容器内或将清洗液注入清洗件内沉浸,达到表面清洁的方法。
3. 4
腐蚀率corrosionrate 化学药剂及其水溶液与被清洗设备和管道的金属接触时金属被腐蚀的相对速率。
3. 5
除垢率 removingdirtystuffrate 被清洗的垢量与清洗前原有垢量之比的百分数。
3.6
洗净率cleaningrate 清洗表面经化学清洗后除掉污垢的面积与清洗前原污垢覆盖面积之比的百分数。
4总则
SH/T 3547—-2011
4.1 石油化工设备和管道化学清洗宜采用循环清洗,也可采用浸泡清洗。 4.2 清洗前,对循环泵、管道、所用容器等进行试水检查应无泄露。 4.3 铝制设备、管道的清洗应采用中性或专用清洗剂。 4.4 计量器具应检定合格并在有效期内。接触化学清洗液的计量具应满足耐腐蚀要求。 4.5清洗作业的安全技术要求除应符合本规范外,尚应符合GB50484的要求。 4.6 化学清洗除应符合本规范外尚应符合设备、管道相关技术条件或国家现行标准的要求。 5施工准备 5.1 材料机具准备 5.1.1 用于化学清洗的临时连接材料,应根据清洗系统的操作压力、操作温度和清洗剂的腐蚀性要求选用。 5.1.2 用于盛放清洗液的容器宜采用不锈钢或其他耐腐蚀制品。 5.1.3 采用循环清洗时,应选用耐腐蚀泵,流量和扬程应满足清洗要求,循环泵最大流量按公式(1)核算。
C Q 最大循环流量,m/h;
Q=3600·FmaxV
(1)
U
式中
O
各循环组件中最大的流通截面积,m 选用的最大循环流速,m/s,宜取0.2m/s~0.5m/s
Fm
5.1.4 化学药剂性能指标应符合相应产品标准并在有效期内。药剂及其溶液应专库、分类存,并应设置警示标识。 5.1.6 化学清洗应采用工业用水、脱盐水等清洁水。用于清洗奥氏体不锈钢的水中氯离子含量不得大于50mg/L 5.2技术准备 5.2.1 编制化学清洗施工技术方案,确定清洗程序及验收标准。化学清洗施工技术方案宜包括以下内容:
a) 编制依据 b) 清洗范围; c) 清洗方法及质量要求; d)清洗系统的设计; e) 清洗配方及化学药品用量:
A
监测、分析、记录; g) 残液处理及排放 h) 人员、设备及工机具; i) 安全技术要求。 施工技术方案批准后,应进行技术交底。
f)
5.2.2 5.3作业条件 5.3.1化学清洗作业场地,应根据设备、管道安装进度和施工平面布置要求确定,清洗现场的道路应平整、畅通。 5.3.21 化学清洗需要的水、汽、 排污管线应已连通。 5.3.3 配备必要的通信设施,夜间作业应有照明。 5.3.4 清洗作业区应设置警戒线及警示标志。 5.3.5 采用循环清洗的设备、管道,应在安装、试压完毕后进行,对不宜进行化学清洗的工艺设备、
2
SH/T3547—2011
仪器、仪表应进行隔离或保护,隔离的阀门应挂牌标识 5.3.6·采用浸泡清洗的管道,应合理分段。 5.3.7清洗作业过程应保证清洗电源不得中断。
S
6.化学清洗方法 6.1一般要求 6.1.1化学清洗主要包括系统水冲洗、脱脂、酸洗、漂洗、钝化和保护等 步骤。化学清洗过程的脱脂作业应按HG20202的规定进行, 6.1.2化学清洗的设备、管道压力试验合格后,应进行工序交接:并填写工序交接记录。 6.1.3 化学药剂应根据清洗设备、管道的材质及清洗要求选用,常用化学药剂特性及清洗配方参见附录 A。 6.1.4清洗液升温可采用蒸汽加热法或电加热法 6.1.5 亿学清洗各工序应连续进行,合格后进行封闭或充氮保护 6.1.6 洗合格的系统,不得进行切割或开孔作业。丸已进行封闭或充氮保护的清洗系统 未经允许不得改变封闭或充氮保护状态。 6. 2 循环清洗 6.2.1 循环清洗的基本程序见附录B,操作流程参见附录C 6.2. 2根据清洗流程图,检查清洗系统应符合下列要求:
m 刀 O
循环泵的流量应符合本规范5.1.3条的要求,循环泵及其他转动机械应试运 转无异 常,循环泉入口或清洗箱出口应装滤网,滤网孔径应小于5mm:放空及排凝点的位置正确,清洗系统内的清洗液应充满、与系统内壁应接触 并保持起够的流
2
T < D N
临时接管的布置合理,必要时加设支架进行支撑固定: D 清洗箱的标高及液位应满足清洗泵的吸入高度。
6.2.3水冲洗应符合下列要求:
清洗系统内的压力宜为0.2MPa-1.0MPa: 检查清洗系统应无泄漏情况:冲洗至进出水质基本一致: d加热系统应满足温升要求:
射难以形成回路的盲端,应加装DN15~DN20的临时排放阀 f) 循环液的进液管和回液管应有足够的截面积以保证清洗液的流量, 且各回路的流速应均匀。
6.2.4 配方配制脱脂液进行脱脂清洗,操作温度、清洗时间应满是要求
脱脂后,用清洁水将脱脂液置换至出水呈中性或弱碱性(pH7 一pH9)。置换出的脱脂液应经处
6.2.5 理后,达标排放。 6.2.6水冲洗后按配方配制酸洗液进行循环酸洗,操作温度、酸时间应满足要求。在酸洗过程中,应安装监视管段或指示岸。监视管段和指示片的测定见附录D。在酸洗过程中,每0.5h检测一次酸浓度及铁离子浓度或其他主要金属浓度,一次酸洗时间不应超过2h。酸洗液浓度的测定参见附录E。
6.2.7酸洗过程中,液体流速控制在0.2m/s-0.5m/s,流体压劳不应超过设计压力。 6.2.8酸洗液中铁离子趋子稳定、酸浓度趋于稳定时再循环Th酸洗结束,取出监视管段或指示片,称重后按附录D的规定计算腐蚀率。 6.2.9.酸洗结束后,酸洗液应中和达标排放。酸洗液排净后,系统注入清洁水,对系统进行水冲洗至弱酸性,pH值为4~4.5。
3
SH/T 3547—2011
6.2.10 水冲洗结束后,按配方配置漂洗液,进行1h~2h漂洗。 6.2.11漂洗结束后,在清洗系统中加入碱性药剂中和,启动泵循环,在循环回路末端取样测试系统内pH值宜为9~9.5。 6.2.12中和结束后,在中和液中加入钝化剂,循环钝化液生成防锈膜,操作温度和钝化时间应满足要求。 6.2.13钝化结束后,钝化液中和达标排放。进行系统吹扫,至清洗系统残液排净。清洗系统吹扫、 干燥应使用脱油脱水的洁净压缩空气或工业氮气。 6.2.14拆除临时设施,复位安装并检查确认。 6.2.15复位后,应及时封闭。当采用氮封保护时,氮气压力宜为0.07MPa~0.1MPa。 6.3·浸泡清洗 6.3.1小型零部件、管段及管件宜采用浸泡清洗。 6.3.2清洗容器和储槽满足清洗件的使用要求,且应设置安全防护设施。各零部件在溶液中应每0.5h 翻动一次,并按程序及时进行倒槽。 6.3.3清洗过程控制,其清洗时间和控制条件参见本规范附录A。 6.3.4'清洗结束后,废液中和达标排放。 7化学清洗质量标准 7.1被清洗设备和管道表面应清洁,无浮锈,无金属粗晶析出的过酸洗现象,并有完整的钝化膜。对含铜材质的清洗系统应无镀铜现象。 7.2碳钢材质的钝化膜质量,可用酸性硫酸铜点滴液检验,检验方法见附录F。点滴液由蓝色变为红色的时间不小于5s为合格。 7.3奥氏体不锈钢材质的钝化膜质量,可用酸性铁氰化钾点滴液检验,检验方法见附录F。点滴液覆盖面内10min内出现的蓝色小点不多于8点为合格。 7.4首次使用的配方,清洗施工前应进行验证。清洗系统设备、管道的腐蚀率和腐蚀量应不大于表1 的数值。
表1腐蚀率及腐蚀量指标
腐蚀率 g/ (m*h)
腐蚀量 g/m2 72 24 24 24 24
材料类别碳钢类不锈钢类紫铜铜合金铝及铝合金
6 2 2 2 2
7.5清洗质量符合下列要求之为合格:
a)对于清洗后的金属表面,目测无残垢: b)对于用除垢率或洗净率检验的,应符合表2的要求; c)若用数点法确认洗净率时,100cm的被清洗表面上直径为5mm10mm的残留垢点三次取样
平均应小于1个,或直径为5mm以下的残留垢点三次取样平均应小于3个为合格。
4
SH/T 3547-2011
表2,除垢率和洗净率指标
单位:%
污垢类型碳酸盐垢
除垢率 90 85 95 95 85
洗净率 95 80 95 95 80
硫酸盐垢、硅酸盐垢
锈垢油垢其他垢
7.6忌油清洗系统脱脂后,应进行含油量测定。含油量符合下列任意一项要求为合格:
a)用波长320nm~380nm的紫外光检查被清洗系统金属表面,应无油脂荧光;
用清洁干燥的白色滤纸擦拭清洗系统金属表面,滤纸应无油脂痕迹;
b)
c) 用无油蒸汽吹洗清洗系统金属表面,取其冷凝液,放入一粒直径小于等于1mm的纯樟脑(萘),
樟脑粒应不停旋转。
8安全技术要求 8.1般规定 8.1.1、化学清洗人员应参加化学清洗施工技术交底和熟悉学习化学清洗安全操作规程,了解化学药品性能、特点、使用方法、保管方法。 8.1.2化学清洗作业人员应根据清洗要求,佩戴防护眼镜、防毒面具,穿戴耐酸碱的工作服、工作帽和橡皮手套等专用劳动保护用品。 8.1.3化学清洗应统一指挥,未经现场指挥人员允许,不得擅自进行操作。 8.1.4 化学清洗时不得在清洗系统上进行其他工作。 8.1.5清洗作业区应设置警戒线并设置醒目的警示标志。 8.1.6 化学清洗作业场所应有冲洗水源和救治用品。 8.1.7 清洗过程中应有专职监护人员,并应每半小时巡检一次清洗系统。 8.1.8 未经处理的酸、碱液及其他有害废液不得排放。化学清洗废液的排放应符合GB8978的规定,污水综合排放指标和最高允许排放浓度见表3。
表3污水综合排放指标
单位:mg/L
最高容许排放浓度
序号
有害物质或项目名称
新扩改(二级标准)
现 有(二级标准)
三级标准
1 2
pH值悬浮物化学需氧量(重铬酸钾法)氟化物
6~9 200 150
6~9 250
6~9 400
3
200
500 20(用氟离子计测定)
4
10 20
15 40
5
油
100
5