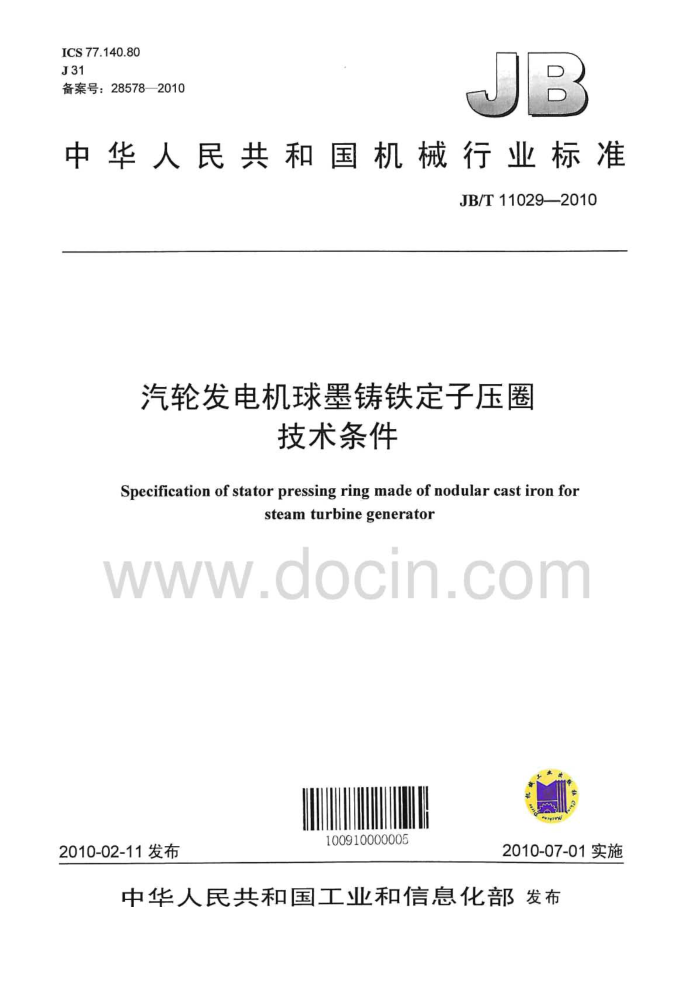
ICS77.140.80 J31 备案号:28578—2010
中华人民共和国机械行业标准
JB/T11029—2010
汽轮发电机球墨铸铁定子压圈
技术条件
Specification of stator pressing ring made of nodular cast iron for
steam turbine generator
www.aocin.com
100910000005
2010-02-11发布
2010-07-01实施
中华人民共和国工业和信息化部发布
JB/T110292010
目 次
前言 1 范围 2 规范性引用文件订货要求
1
3
4制造工艺 4.1铸造.. 4.2热处理。 4.3补焊.. 5技术要求 5.1 化学成分 5.2 力学性能 5.3 金相组织 5.4 无损检测 5.5 表面质量 5.6 尺寸公差 6’试验方法和检验规则 6.1 化学分析 6.2 力学性能试验 6.3 金相检验 6.4 无损检测. 6.5 表面质量检验 6.6 尺寸检查 6.7 复试 7验收及质量证明书 7.1验收 7.2 质量证明书 8标志和包装 8.1标志 8.2 包装附录A(规范性附录)汽轮发电机球墨铸铁压圈超声检测程序 A.1 适用范围 A.2 通则 A.3 检验时期及表面质量要求 A.4 检测方法 A.5 应该记录的信息 A.6 验收 A.7 超声检测报告表1 压圈铸件化学成分,表2 压圈铸件的力学性能,
一
中
福
F0E1
I
JB/T11029—2010
前 言
本标准的附录A为规范性附录。 本标准由中国机械工业联合会提出。 本标准由机械工业大型铸锻件标准化技术委员会归口。 本标准起草单位:哈尔滨大电机研究所。 本标准主要起草人:李文君。 本标准为首次发布。
www.docin.com
II
JB/T110292010
汽轮发电机球墨铸铁定子压圈技术条件
1范围
本标准规定了汽轮发电机球墨铸铁压圈的订货要求、制造工艺、技术要求、试验方法和检验规则、 验收及质量证明书等。
本标准适用于汽轮发电机球墨铸铁压圈的订货、制造、检验和验收。 2规范性引用文件
下列文件中的条款通过本标准的引用而成为本标准的条款。凡是注日期的引用文件,其随后所有的修改单(不包括勘误的内容)或修订版均不适用于本标准,然而,根据本标准达成协议的各方也可研究是否使用这些文件的最新版本。凡是不注日期的引用文件,其最新版本适用于本标准。
GB/T222钢的成品化学成分允许偏差 GB/T223(所有部分)钢铁及合金化学分析方法 GB/T231.1金属材料布氏硬度试验第1部分:试验方法(GB/T231.1—2009,ISO6506-1:
2005,MOD)
GB/T1348球墨铸铁件(GB/T1348—2009,ISO1083:2004,MOD) GB/T6060.1表面粗糙度比较样块铸造表面(GB/T6060.1—1997,eqVISO2632-3:1979) GB/T9441球墨铸铁金相检验(GB/T9441—2009,ISO945-1:2008,MOD) GB/T20066钢和铁化学成分测定用试样的取样和制样方法(GB/T200662006,ISO14284:
1996,IDT)
ASTME8金属材料拉伸试验的试验方法 ASTME709磁粉检验标准
.docin.com
3订货要求 3.11 供方应有完善的质量保证体系,原则上应具有生产过类似材料、相近尺寸的铸件的业绩。 3.2需方应在订货合同或技术协议书中说明采用的标准、材料牌号、铸件强度级别、供需双方明确的相应技术要求和检验项目以及本标准要求之外的检验项目。 3.3需方应向供方提供标明力学性能试验取样位置的粗加工图样,必要时还应提供精加工尺寸。 3.4需方要求参加现场检验的项目应在合同中注明。 4制造工艺 4.1铸造
EE
压圈铸件铸造时不允许使用内冷铁。若需采用芯撑和铸造工艺孔,在制造开始前应取得需方的书面认可,否则不允许使用。 4.2热处理
每个铸件都应充分地进行去除应力处理。去除应力处理可以采用铸件在铸模中缓慢冷却的方法进行。为了保证要求的加工公差,铸件应在铸模中冷却足够长的时间以达到去除应力的效果。如有必要,可采用铁素体化热处理,以满足力学性能或金相检验的要求并保证在随后的加工过程中不会产生超差变形。 4.3补焊
1
JB/T11029—2010
没有征得需方的同意,不允许对铸件进行任何形式的补焊。 5技术要求 5.1化学成分 5.1.1供方应按熔炼炉号逐炉取样进行熔炼分析,熔炼分析的结果应满足表1的规定。除碳、硫之外其他元素的含量作为工艺配料供参考,但所确定的铸件的化学成分应满足力学性能要求。
表1压圈铸件化学成分(质量分数)
(%) Ren 0.02~0.04
P 0.07
S ≤0.02
Mg 0.03~0.06
Mn ≤0.3
Si 2.5-3.0
C ≥2.5
5.1.2应对压圈铸件进行成品化学成分分析,分析结果应符合表 :规定 成品分析的允许偏差应符合 GB/T222的规定。 5.2力学性能
压圈铸件的力学性能应待合表2规定。
表2压圈铸件的力学性能
Rpuz MPa m 250 276
4 (9%) > 15.0 18.0
R MPa
硬度 HBW" 130~180 140~200
材料牌号
二
400 414
QT400-15 60-40-18 任意两点间的布氏硬度偏差值不得超过40HBW。
5.3金相组织 5.3.1每个铸件都应进行金相组织检验,金相组织的检验结果应为铁素体+球状石墨。 5.3.2铸件组织的球化级别应不低于四级 5.4无损检测 5.4.1超声检测
com
在加工螺钉孔之前,每个铸件都应按照附录A的要求进行超声检测和验收。 5.4.2磁粉检测
铸件的磁粉检测的质量等级应符合检测图样或技术协议的要求 a)线性缺陷一一在任意150mm×150mm的区域内缺陷显示不得超过六个,且单个缺陷的尺寸不
得大于10mm。小于1.6mm的任何缺陷均可忽略不计。若相的两个或多个缺陷呈纵向排列,且它们之间的距离小于最小缺陷的长度,则可以把这些缺陷看作是一个缺陷。
b)非线性缺陷一一在任意150mm×150mm的区域内缺陷显示不得超过九个,且单个缺陷的尺寸
不得大于16mm。最大尺寸小于3.2mm的任何缺陷均可忽略不计。若相邻的两个或多个缺陷之间的距离小于最小缺陷的最大尺寸时,则可以把这些缺陷看作是一个缺陷。
5.5表面质量 5.5.1所有的铸件都应进行外观检查。铸件表面不得有粘砂并且应保证光滑。铸件在加工前和加工后均不得有硬质点以及裂纹、冷隔、砂眼、气孔、缩孔和明显的疏松等有害缺陷。 5.5.2铸件的横浇道、冒口、飞边和附铸试块及退火氧化皮均应去掉。 5.5.3每个加工后的铸件应进行适当的清理并去除油污。 5.6尺寸公差
每个铸件的尺寸公差都应满足订货图样或技术协议的要求。
2
JB/T11029—2010
6试验方法和检验规则 6.1化学分析 6.1.1压圈铸件化学分析的取样应按GB/T20066规定的方法进行。化学成分分析应按GB/T223规定的方法进行。 6.1.2当需方需要进行成品化学成分分析时,可以在供方提供的附铸试块上取样进行。 6.2力学性能试验 6.2.1材料牌号为QT400-15的铸件,力学性能试验按GB/T1348规定的方法进行。材料牌号为60-40-18 的铸件,力学性能试验按ASTME8规定的方法进行 如需方同意出可按照GB/T1348的规定执行。 6.2.2拉伸试样为直径@12.5mm 标斯somm的标准形拉伸试样: 取自干型砂模中铸出的25.4mm 厚的基尔试块。 6.2.3硬度试验
硬度试验按GB/T231.1规定的方法进行。 在铸件平整的表面上任取两点进行布氏硬度检验。 6.3金相检验
铸件金相组织的检验方法应按照GB/T9441的规进行。试样取自从附铸试块上加工的拉伸试样的夹头部位。
铸件的金相检验报告中应包括 00倍金相组织照片。首次提供的铸件还需提供套料试样的金相照片,套料试样的金相照片仅供参考, 不作为验收依据。 6.4无损检测 6.4.1每个铸件在加工螺钉孔之前都应进行超声检测,超声检测应按附录A的规定进行。 6.4.2每个铸件在精加工后都应进行磁粉检测,碰粉检测应按ASTME709 的规定进行。 6.5表面质量检验
铸件表面粗糙度的检测应按GB/T6060.1的规定执行。 6.6尺寸检查
铸件的尺寸检查应由检查人员按订货图样和技术协议采用相应的量规检查。 6.7复试
若力学性能试验结果不合格·充许在同一附铸试块上取双倍试样进行复试。如果复试结果均符合表 1的规定,则判为合格,其中只要有一个试验结果不合格:则应判为不合格或由供需双方协商处理。 7 验收及质量证明书 7.1验收
需方有权选择铸件的某些试验项目进行验收,在验收或检验中,发现铸件不符合本标准和订货合同中规定的补充技术要求条款时,需方应及时通知供方,双方办商解决 7.2质量证明书
供方应向需方提供质量证明书,质量证明书应包含下列内容: a)订货合同号: b)铸件图号及名称: c)标准号和材料牌号: d)供方的铸件识别号及供方名称: e)熔炼炉号: f)化学成分分析结果; g)力学性能试验结果; h)金相检验结果(包括100倍金相组织照片): i)无损检测报告;
3
JB/T11029—2010
j)尺寸检验记录; k)订货合同中规定的补充项目的检验结果。
8标志和包装 8.1标志
每个加工完的铸件都应在图样规定的位置用不小于6mm的钢字打上标志(或铸上字母和数字)。 标志应包含以下内容:
a)合同号、图号、木模号: b)供方名称; c)供方的铸件识别号; d)熔炼炉号。
8.2包装 8.2.1每个铸件均应涂醇酸树脂漆,但螺钉孔不应涂漆。 8.2.2铸件应以适当的形式进行包装,以免在发运过程中受损或遗失。 8.2.3每次发运的铸件的外包装上都应清楚地标明订货合同号、供方名称和材料牌号。
www.docin.com
JB/T110292010
附录A (规范性附录)
汽轮发电机球墨铸铁压圈超声检测程序
A.1适用范围
本程序规定了球墨铸铁定子压圈超声检测的纵波扫查步骤。 A.2通则 A.2.1按本程序进行检测的人员应至少具备NDT超声波I级以上资格。 A.2.2应对检测中所用的探头进行测试。超声检测的垂直线性小于信号高度土5%或满屏土2%为合格。 A.3检验时期及表面质量要求 A.3.1应在试件表面机械加工完成后进行检测。其表面粗糙度Ra值应达到6.3μm的要求。 A.3.2试件表面的毛刺、机械加工痕迹、污垢或其他影响结果判定的杂质应清理干净。 A.4检测方法 A.4.1耦合剂应采用SAE20以下的机油。 A.4.2检测频率应由担任检测的责任工程师评定超声波指示区域之后确定。 A.4.3试件表面应采用1MHz,晶片直径为20mm~25mm的单晶纵波探头扫查。晶片外可以使用尼龙保护膜。 A.4.4检测时应进行连续扫查。探头每次移动的幅度应不超过探头宽度或直径的3/4。 A.4.5底面反射回波应作为参考波。参考底波的振幅应调整并保持100%。这一灵敏度能够检测出每一厚度的缺陷区域。 A.5应该记录的信息 A.5.1当底波降低75%以下的位置时应在表面做出标记。 A.5.2每一个底波降低75%以下的位置需要记录以下信息: A.5.2.1底波损失的百分比和线形长度。 A.5.2.2缺陷的半径位置。 A.5.2.3相对固定标记(如压圈编号等)的周长位置(距参照点的位置)。 A.5.3对于底波有损失的位置,应在报告中记录其最大的振幅和距探测面深度,在可能情况下还应记录该指示距表面的深度。 A.6验收
一
提供的定子压圈在下列情况下应接收。 a)底波降低75%以下的缺陷在任意方向上不超过50.8mm,即没有线形长度时; b)底波降低75%以下的无线形长度的缺陷不超过两点时; c)如果定子压圈不满足验收标准,生产厂应向订货方提供完整的标明缺陷位置和数量的质量报告,
能否使用由订货方决定。
5