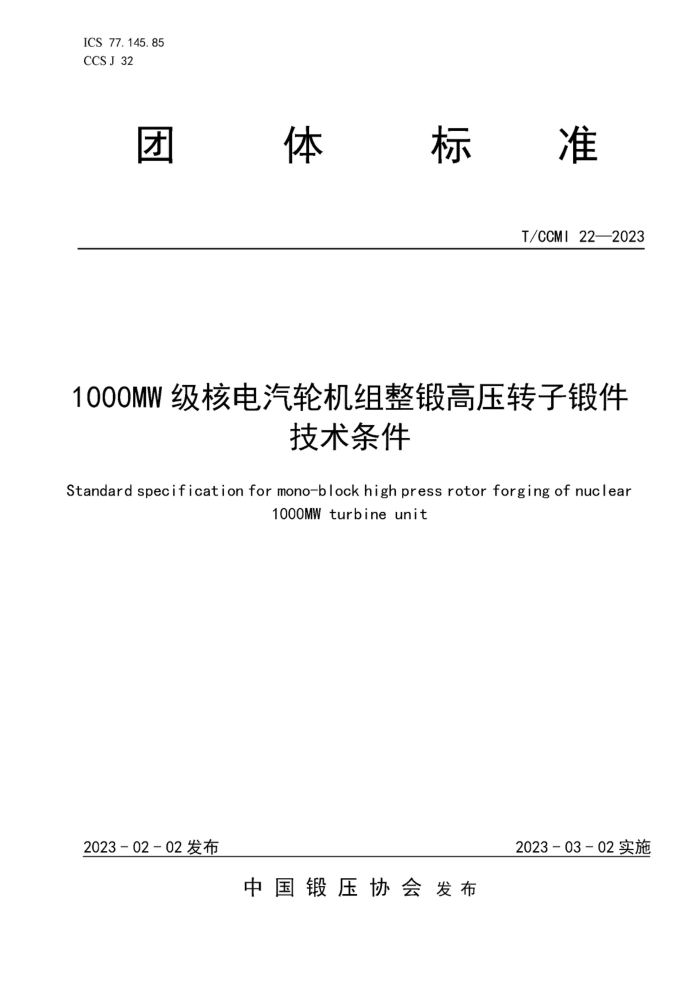
T/CCMI 222023
目次
前言范围,
II
1 2 规范性引用文件 3 术语和定义
制造工艺 5 技术要求. 6 试验方法.
4
检验规则质量证明书、标志和包装,
7
8
图1 力学性能取样和硬度检测推荐位置,
表1熔炼分析. 表2成品分析. 表3气体含量分析表4 锻件的力学性能
1
T/CCMI22-2023
前言
本文件按照GB/T1.1-2020《标准化工作导则 可第1部分:标准化文件的结构和起草规则》的规定起
草。
请注意本文件的某些内容可能涉及专利。本文件的发布机构不承担识别这些专利。 本文件由中国锻压协会提出并归口。 本文件起草单位:中国第一重型机械股份公司、哈尔滨汽轮机厂有限责任公司、上海电气电站设备
有限公司。
本文件主要起草人:张金珠、张国利、牛广斌、曹志远、张建国、芮守泰、季雪、于秀平、彭亚敏、 赵义瀚、陈纪伟、宫金鑫。
本文件为首次发布。
II
T/CCMI 22-2023
1000MW级核电汽轮机组整锻高压转子锻件 技术条件
1范围
本文件规定了1000MW级核电常规岛汽轮机组用30Cr2Ni4MoV合金钢整锻高压转子锻件的制造工艺、 技术要求、试验方法、检验规则、质量证明书、标志和包装。
本文件适用于1000MW级核电常规岛汽轮机组用30Cr2Ni4MoV合金钢整锻高压转子锻件的采购和验
收。
规范性引用文件
2
下列文件中的内容通过文中的规范性引用而构成本文件必不可少的条款。其中,注日期的引用文件,仅该日期对应的版本适用于本文件;不注日期的引用文件,其最新版本(包括所有的修改单)适用于本文件。
GB/T223(适用部分) 钢铁及合金化学分析方法 GB/T228.1金属材料拉伸试验第1部分:室温试验方法 GB/T229 金属材料夏比摆锤冲击试验方法 GB/T 231.1 金属材料布氏硬度试验第1部分:试验方法 GB/T 6394 金属平均晶粒度测定法 GB/T10561-2005钢中非金属夹杂物含量的测定-标准评级图显微检验法 GB/T 8541 锻压术语 JB/T 8467 锻钢件超声检测 JB/T 8468 锻钢件磁粉检测 JB/T 8888 环芯法测量汽轮机、汽轮发电机转子锻件残余应力的试验方法 JB/T9021 汽轮机主轴和转子锻件的热稳定性试验方法
3 术语和定义
GB/T8541界定的以及下列术语和定义适用于本文件。
3. 1
1000MW级核电汽轮机组 nuclear 1000MWturbineunit 单机容量1000MW的核反应堆发电站,以核燃料在核反应堆中发生裂变产生热量来加热水使之变成蒸
汽,蒸汽通过管路进入汽轮机,推动汽轮发电机发电。 3. 2
整锻高压转子 mono-block highpress rotor 汽轮机组高压缸内工作的整体锻造结构转子。
4制造工艺
1
T/CCMI 22-2023 4.1总则
本条规定了锻件的冶炼、锻造、热处理和机械加工的相关要求。 4.2冶炼
锻件用钢采用电炉冶炼,钢液真空浇铸钢锭时,采用真空碳脱氧,未经需方同意不得采用其它终脱氧方法。 4.3锻造 4.3.1锻件应在有足够能力的锻压机上锻造成形,以确保锻件整个截面充分锻透。 4.3.2钢锭的顶部和底部应有足够的切除量,以确保锻件无缩孔、疏松、严重的偏析和其他有害缺陷。 4.3.3锻造比要求大于3.5。 4.4热处理 4.4.1 预备热处理
IWO
C
锻件的预备热处理应为正火加回火,或者其他有利于组织均匀化和晶粒细化的热处理方式。
0 S
4.4. 2 性能热处理 4.4.2.1 性能热处理为率火加回火。性能热处理推荐温度830℃~860℃,保温足够长的时间使锻件完全奥氏体化,然后水冷或喷水冷。待内部组织完全转变后,应进行回火处理,保温足够长的时间并控制
好冷却速率,以使残余应力达到最小值。 4.4.2.2锻件的性能热处理宜在垂直状态下进行,锻件回火时圆周和整个长度上的冷却速度尽可能均
S D
匀一致。 4.4.3 去应力处理
去应力热处理宜在垂直状态下进行,去应力推荐温度为低于调质回火温度15℃~50℃。保温
4.4.3.1 足够时间,以确保锻件内部温度均匀,缓慢冷却。 4.4.3.2 对于残余应力合格的锻件,且回火炉温的控制冷却速度不超过10℃/h,锻件可不进行去应力热处理,若锻件残余应力检测超过规定值,应进行去应力热处理。 4.5机械加工 4.5.1 在性能热处理前,锻件的全部表面应进行第一次机加工。 4.5.2在性能热处理之后、超声波检测前锻件应进行第二次机加工 4.5.3在各项性能检验和超声检测合格后,锻件应按需方订货图样规定的尺寸、公差以及粗糙度要求进行加工。
5技术要求
5.1化学成分 5.1.1 供方应对每炉钢水进行熔炼分析,多炉合浇时的权重分析结果应符合表1的规定。 5. 1.2 供方应对每个锻件进行成品分析,成品分析结果应符合表2的规定。 5.1.3 每个锻件应分析气体元素含量,分析结果应满足表3的规定。
2
T/CCM1 22-2023
表1 熔炼分析
单位:质量分数% 质量分数 0.30~0.60 0. 07~0. 15 ≤0.15 ≤0.010 ≤0.015 ≤0.012 ≤0.0015
元素 c Si Mn P s Cr Ni
元素 Mo > Cu Al As Sn Sb
质量分数 ≤0. 35 ≤0.10 0.20~0. 40 ≤0. 007 ≤0. 003 1.50~2. 00 3. 25 ~3. 75
M C L 质量分数 O
表2 成品分析
单位:质量分数% 质量分数
元素 c si Mn P s Cr Ni
元素 Mo > cu A1 As Sn Sb
0.28~0. 62 0. 06~0.16 0.17 ≤0.012 ≤0.020 ≤0.014 ≤0.0017
≤0.37
S ≤0.12 S 0. 17~0. 43 山
≤0. 009
? P ≤0.009 S 1. 45~2. 05 D 3.18~3.82
表3 气体含量分析
ON 4
单位:ppm
H ≤1.5
0 ≤35
N ≤70
J
5. 2 力学性能
如果没有其他规定, 锻件力学性能应符合表4的规定。径向试样屈服强度最大值和最小值之差应不大于55MPa。
表4 锻件的力学性能
抗拉强度R。 屈服强度R,a.2 断面收缩率Z 断后伸长率A 冲击吸收能量KV2 韧脆转变温度FATTso
MPa ≥725 注:V型缺口冲击试验为 一组三个试样, 三个试样的试验结果的算术平均值不应低于规定值, 其中只允许有 有一个试
MPa ≥620
% ≥50
J ≥68
℃ ≤4
% ≥17
J-
样的试验结果低于规定值,但不应低于规定值的70%。
5. 3 硬度均匀性
3
T/CCMI 22-2023
锻件应在性能热处理后检查硬度的均匀性,硬度的绝对值供参考。在同一圆周上各点间的硬度差不应超过30HBW,在同一母线上的硬度差不应超过40HBW。 5.4金相检验 5.4.1锻件的平均晶粒度应不粗于3.0级。 5.4.2锻件的A、B、C、D夹杂物均不应超过2.5级。Ds类型夹杂物是否检测应按需方要求执行。 5.5残余应力
锻件的残余应力不应超过屈服下限值的8%。若残余应力不合格,锻件可进行去应力处理,并重新测定残余应力和硬度。 5.6尺寸、公差和表面粗糙度
锻件尺寸、公差和表面粗糙度应符合双方确认的订货图样的要求。 5.7表面质量
锻件不应有裂纹、缩孔、折叠以及其它有害缺陷。 5.8无损检测 5.8.1超声波检测
在完成粗加工和性能热处理后,应对转子锻件的外圆表面进行超声波检测。超声波检测结果应符合以下规定:
a)当量直径小于Φ1.6mm的单个分散缺陷不计,但杂波高度应低于当量直径Φ1.6mm幅度的50% 注:单个分散缺陷是指相邻两缺陷之间的距离大于其中较大缺陷当量直径10倍的缺陷。 b)不允许当量直径Φ1.6m以上的单个缺陷和当量直径Φ1.Omm以上的密集缺陷 c) 不应有游动缺陷信号和连续缺陷信号; d) 供方应向需方提供用2MHz5MHz探头在锻件最大直径处两端和中间三处测得的材料衰减数
据: e) 超过上述要求的缺陷应报告需方,由供需双方进行复验和协商,但锻件是否可用由需方决定。
5.8.2磁粉检测 5.8.2.1在交货态,供方应对锻件轴身与轴颈的过渡圆角处、两轴颈外圆进行磁粉检测,磁粉检测结果应符合以下规定:记录所有长度大于1.0mm的缺陷显示大小(长,宽,形状)及位置;不允许1.5mm 以上的显示。 5.8.2.2锻件在精加工后,由需方对外圆表面进行磁粉检验,供方对检验结果负责。 5.9热稳定性
锻件在交货态进行热稳定性试验。
6试验方法
6.1化学成分分析 6.1.1化学成分分析应按GB/T223规定的方法或能保证分析质量的其他分析方法执行。 6.1.2应对每炉(每包)钢液测定其化学成分,多炉合浇时应报告权重平均分析结果。 4
T/CCMI 222023
目次
前言范围,
II
1 2 规范性引用文件 3 术语和定义
制造工艺 5 技术要求. 6 试验方法.
4
检验规则质量证明书、标志和包装,
7
8
图1 力学性能取样和硬度检测推荐位置,
表1熔炼分析. 表2成品分析. 表3气体含量分析表4 锻件的力学性能
1
T/CCMI22-2023
前言
本文件按照GB/T1.1-2020《标准化工作导则 可第1部分:标准化文件的结构和起草规则》的规定起
草。
请注意本文件的某些内容可能涉及专利。本文件的发布机构不承担识别这些专利。 本文件由中国锻压协会提出并归口。 本文件起草单位:中国第一重型机械股份公司、哈尔滨汽轮机厂有限责任公司、上海电气电站设备
有限公司。
本文件主要起草人:张金珠、张国利、牛广斌、曹志远、张建国、芮守泰、季雪、于秀平、彭亚敏、 赵义瀚、陈纪伟、宫金鑫。
本文件为首次发布。
II
T/CCMI 22-2023
1000MW级核电汽轮机组整锻高压转子锻件 技术条件
1范围
本文件规定了1000MW级核电常规岛汽轮机组用30Cr2Ni4MoV合金钢整锻高压转子锻件的制造工艺、 技术要求、试验方法、检验规则、质量证明书、标志和包装。
本文件适用于1000MW级核电常规岛汽轮机组用30Cr2Ni4MoV合金钢整锻高压转子锻件的采购和验
收。
规范性引用文件
2
下列文件中的内容通过文中的规范性引用而构成本文件必不可少的条款。其中,注日期的引用文件,仅该日期对应的版本适用于本文件;不注日期的引用文件,其最新版本(包括所有的修改单)适用于本文件。
GB/T223(适用部分) 钢铁及合金化学分析方法 GB/T228.1金属材料拉伸试验第1部分:室温试验方法 GB/T229 金属材料夏比摆锤冲击试验方法 GB/T 231.1 金属材料布氏硬度试验第1部分:试验方法 GB/T 6394 金属平均晶粒度测定法 GB/T10561-2005钢中非金属夹杂物含量的测定-标准评级图显微检验法 GB/T 8541 锻压术语 JB/T 8467 锻钢件超声检测 JB/T 8468 锻钢件磁粉检测 JB/T 8888 环芯法测量汽轮机、汽轮发电机转子锻件残余应力的试验方法 JB/T9021 汽轮机主轴和转子锻件的热稳定性试验方法
3 术语和定义
GB/T8541界定的以及下列术语和定义适用于本文件。
3. 1
1000MW级核电汽轮机组 nuclear 1000MWturbineunit 单机容量1000MW的核反应堆发电站,以核燃料在核反应堆中发生裂变产生热量来加热水使之变成蒸
汽,蒸汽通过管路进入汽轮机,推动汽轮发电机发电。 3. 2
整锻高压转子 mono-block highpress rotor 汽轮机组高压缸内工作的整体锻造结构转子。
4制造工艺
1
T/CCMI 22-2023 4.1总则
本条规定了锻件的冶炼、锻造、热处理和机械加工的相关要求。 4.2冶炼
锻件用钢采用电炉冶炼,钢液真空浇铸钢锭时,采用真空碳脱氧,未经需方同意不得采用其它终脱氧方法。 4.3锻造 4.3.1锻件应在有足够能力的锻压机上锻造成形,以确保锻件整个截面充分锻透。 4.3.2钢锭的顶部和底部应有足够的切除量,以确保锻件无缩孔、疏松、严重的偏析和其他有害缺陷。 4.3.3锻造比要求大于3.5。 4.4热处理 4.4.1 预备热处理
IWO
C
锻件的预备热处理应为正火加回火,或者其他有利于组织均匀化和晶粒细化的热处理方式。
0 S
4.4. 2 性能热处理 4.4.2.1 性能热处理为率火加回火。性能热处理推荐温度830℃~860℃,保温足够长的时间使锻件完全奥氏体化,然后水冷或喷水冷。待内部组织完全转变后,应进行回火处理,保温足够长的时间并控制
好冷却速率,以使残余应力达到最小值。 4.4.2.2锻件的性能热处理宜在垂直状态下进行,锻件回火时圆周和整个长度上的冷却速度尽可能均
S D
匀一致。 4.4.3 去应力处理
去应力热处理宜在垂直状态下进行,去应力推荐温度为低于调质回火温度15℃~50℃。保温
4.4.3.1 足够时间,以确保锻件内部温度均匀,缓慢冷却。 4.4.3.2 对于残余应力合格的锻件,且回火炉温的控制冷却速度不超过10℃/h,锻件可不进行去应力热处理,若锻件残余应力检测超过规定值,应进行去应力热处理。 4.5机械加工 4.5.1 在性能热处理前,锻件的全部表面应进行第一次机加工。 4.5.2在性能热处理之后、超声波检测前锻件应进行第二次机加工 4.5.3在各项性能检验和超声检测合格后,锻件应按需方订货图样规定的尺寸、公差以及粗糙度要求进行加工。
5技术要求
5.1化学成分 5.1.1 供方应对每炉钢水进行熔炼分析,多炉合浇时的权重分析结果应符合表1的规定。 5. 1.2 供方应对每个锻件进行成品分析,成品分析结果应符合表2的规定。 5.1.3 每个锻件应分析气体元素含量,分析结果应满足表3的规定。
2
T/CCM1 22-2023
表1 熔炼分析
单位:质量分数% 质量分数 0.30~0.60 0. 07~0. 15 ≤0.15 ≤0.010 ≤0.015 ≤0.012 ≤0.0015
元素 c Si Mn P s Cr Ni
元素 Mo > Cu Al As Sn Sb
质量分数 ≤0. 35 ≤0.10 0.20~0. 40 ≤0. 007 ≤0. 003 1.50~2. 00 3. 25 ~3. 75
M C L 质量分数 O
表2 成品分析
单位:质量分数% 质量分数
元素 c si Mn P s Cr Ni
元素 Mo > cu A1 As Sn Sb
0.28~0. 62 0. 06~0.16 0.17 ≤0.012 ≤0.020 ≤0.014 ≤0.0017
≤0.37
S ≤0.12 S 0. 17~0. 43 山
≤0. 009
? P ≤0.009 S 1. 45~2. 05 D 3.18~3.82
表3 气体含量分析
ON 4
单位:ppm
H ≤1.5
0 ≤35
N ≤70
J
5. 2 力学性能
如果没有其他规定, 锻件力学性能应符合表4的规定。径向试样屈服强度最大值和最小值之差应不大于55MPa。
表4 锻件的力学性能
抗拉强度R。 屈服强度R,a.2 断面收缩率Z 断后伸长率A 冲击吸收能量KV2 韧脆转变温度FATTso
MPa ≥725 注:V型缺口冲击试验为 一组三个试样, 三个试样的试验结果的算术平均值不应低于规定值, 其中只允许有 有一个试
MPa ≥620
% ≥50
J ≥68
℃ ≤4
% ≥17
J-
样的试验结果低于规定值,但不应低于规定值的70%。
5. 3 硬度均匀性
3
T/CCMI 22-2023
锻件应在性能热处理后检查硬度的均匀性,硬度的绝对值供参考。在同一圆周上各点间的硬度差不应超过30HBW,在同一母线上的硬度差不应超过40HBW。 5.4金相检验 5.4.1锻件的平均晶粒度应不粗于3.0级。 5.4.2锻件的A、B、C、D夹杂物均不应超过2.5级。Ds类型夹杂物是否检测应按需方要求执行。 5.5残余应力
锻件的残余应力不应超过屈服下限值的8%。若残余应力不合格,锻件可进行去应力处理,并重新测定残余应力和硬度。 5.6尺寸、公差和表面粗糙度
锻件尺寸、公差和表面粗糙度应符合双方确认的订货图样的要求。 5.7表面质量
锻件不应有裂纹、缩孔、折叠以及其它有害缺陷。 5.8无损检测 5.8.1超声波检测
在完成粗加工和性能热处理后,应对转子锻件的外圆表面进行超声波检测。超声波检测结果应符合以下规定:
a)当量直径小于Φ1.6mm的单个分散缺陷不计,但杂波高度应低于当量直径Φ1.6mm幅度的50% 注:单个分散缺陷是指相邻两缺陷之间的距离大于其中较大缺陷当量直径10倍的缺陷。 b)不允许当量直径Φ1.6m以上的单个缺陷和当量直径Φ1.Omm以上的密集缺陷 c) 不应有游动缺陷信号和连续缺陷信号; d) 供方应向需方提供用2MHz5MHz探头在锻件最大直径处两端和中间三处测得的材料衰减数
据: e) 超过上述要求的缺陷应报告需方,由供需双方进行复验和协商,但锻件是否可用由需方决定。
5.8.2磁粉检测 5.8.2.1在交货态,供方应对锻件轴身与轴颈的过渡圆角处、两轴颈外圆进行磁粉检测,磁粉检测结果应符合以下规定:记录所有长度大于1.0mm的缺陷显示大小(长,宽,形状)及位置;不允许1.5mm 以上的显示。 5.8.2.2锻件在精加工后,由需方对外圆表面进行磁粉检验,供方对检验结果负责。 5.9热稳定性
锻件在交货态进行热稳定性试验。
6试验方法
6.1化学成分分析 6.1.1化学成分分析应按GB/T223规定的方法或能保证分析质量的其他分析方法执行。 6.1.2应对每炉(每包)钢液测定其化学成分,多炉合浇时应报告权重平均分析结果。 4