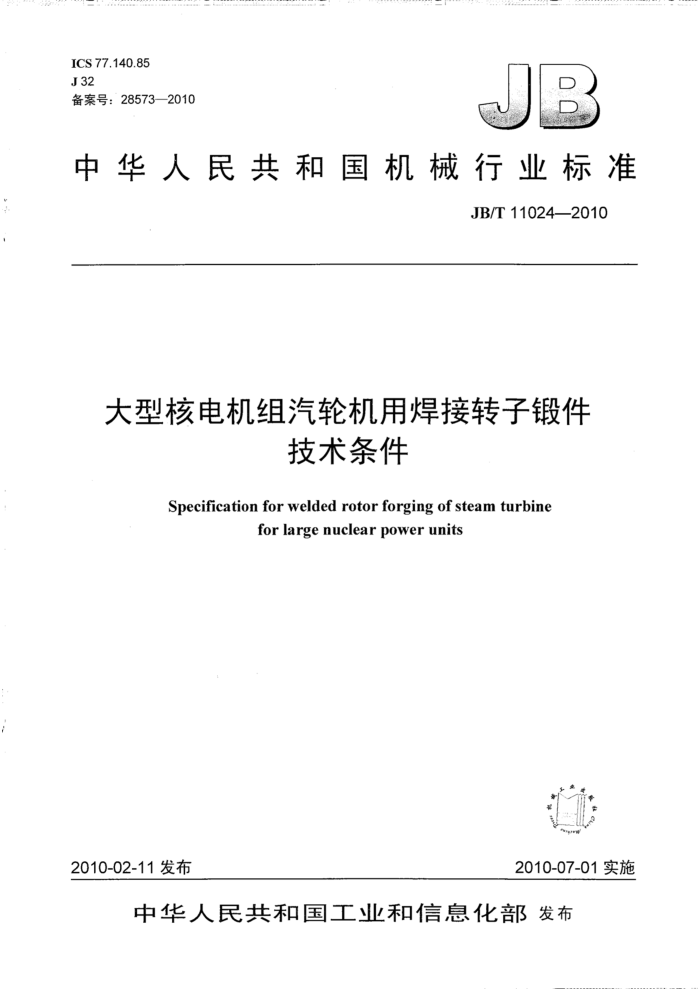
ICS77.140.85 J32 备案号:28573—2010
中华人民共和国机械行业标准
JB/T110242010
大型核电机组汽轮机用焊接转子锻件
技术条件
Specification for welded rotor forging of steam turbine
for large nuclear power units
2010-07-01实施
2010-02-11发布
中华人民共和国工业和信息化部发布
JB/T11024—2010
目 次
前言范围
1
2规范性引用文件
#中电
订货要求. 4. 制造工艺 4.1治炼和铸锭 4.2 锻造.. 4.3 热处理 4.4 机械加工 4.5 焊接, 5·技术要求. 5.1 化学成分 5.2 力学性能. 5.3 硬度, 5.4 无损检测, 5.5 金相组织 5.6 残余应力, 5.7 尺寸和表面粗糙度 6检验规则和试验方法 6.1 化学成分分析 6.2 力学性能检验。 6.3 硬度检验. 6.4 无损检测. 6.5 金相检验 6.6 残余应力测定 6.7 复试 6.8 重新热处理 7 验收及质量证明书 7.1 验收. 7.2 质量证明书。 8标志和包装附录A(规范性附录)超声波扫查部位及扫查方法. A.1超声波扫查部位 A.2 转子轮盘锻件的超声波扫查方法. A.3转子轴端轮盘锻件的超声波扫查方法
3
BE0Ea1
.-
.B..B...E
10i000010000000000 .
1888088F0000000000
JB/T11024—2010
前 言
本标准的附录A为规范性附录。 本标准由中国机械工业联合会提出。 本标准由机械工业大型铸锻件标准化技术委员会归口。 本标准起草单位:东方汽轮机有限公司。 本标准主要起草人:钟杰、杨功显、范华、王化、王仕洋。 本标准为首次发布。
III
JB/T11024--2010
大型核电机组汽轮机用焊接转子锻件扌 技术条件
1.范围
本标准规定了大型核电机组汽轮机用合金钢焊接转子锻件的订货要求、制造工艺、技术要求、检验规则和试验方法、验收及质量证明书等。
本标准适用于大型核电机组汽轮机用的在高应力下工作的、经过粗加工和热处理的焊接转子锻件的订货、制造与检验。 2规范性引用文件
下列文件中的条款通过本标准的引用而成为本标准的条款。凡是注日期的引用文件,其随后所有的修改单(不包括勘误的内容)或修订版均不适用于本标准,然而,鼓励根据本标准达成协议的各方研究是否可使用这些文件的最新版本。凡是不注日期的引用文件,其最新版本适用于本标准。
GB/T223(所有部分)·钢铁及合金化学分析方法 GB/T228金属材料室温拉伸试验方法(GB/T228—2002,eqVISO6892:1998) GB/T 229 金属材料夏比摆锤冲击试验方法(GB/T229—2007,ISO148-1:2006,MOD) GB/T231.1金属材料布氏硬度试验第1部分:试验方法(GB/T231.1-2009,ISO6506-1:
2005,MOD)
GB/T6394 金属平均晶粒度测定法(GB/T6394--2002,ASTME112:1996,MOD) GB/T10561—2005钢中非金属夹杂物含量的测定标准评级图显微检验法(ISO4967:1998,
IDT)
JB/T8468锻钢件磁粉检验方法 JB/T8888环芯法测量汽轮机、汽轮发电机转子锻件·残余应力的试验方法 ASTMA370钢制品的力学性能试验方法和定义
3订货要求 3.1供方应有完善的质量保证体系,原则上应具有生产过类似材料、相近尺寸的锻件的业绩。 3.2供方应编制制造计划和制造过程监控的质量检验计划。如需方要求首件认证,应按供需双方协议执行。 3.3需方应在订货合同或技术协议书中说明采用的标准、材料牌号、锻件强度级别、供需双方明确的相应技术要求和检验项目以及本标准要求之外的检验项目。 3.4需方应向供方提供标明力学性能试验取样位置的粗加工图样,必要时还应提供精加工尺寸。 3.5需方要求参加现场检验的项目应在合同中注明。 4制造工艺 4.1冶炼和铸锭 4.1.1锻件用钢应采用电炉冶炼、钢包精炼、真空碳脱氧工艺,也可以采用电渣重熔工艺。经需方同意,也可采用保证质量的其他方法冶炼。 4.1.2钢水在浇铸过程中应进行真空处理,以去除有害气体,特别是氢。在真空处理过程中,真空系统的能力必须太到在开浇后的2min内就能将初始增高的压强降至较低值,通常应低于133Pa。 4.2锻造
JB/T1102420.10
4.2.1‘钢锭上部和下部均应有足够的切除量,以确保成品锻件无缩孔、疏松、严重的偏析和其他有害缺陷。 4.2.2采用的锻造方法必须尽可能使整个锻件得到均匀的组织结构。锻压机应有足够的能力,以使锻件的整个截面锻透。 4.2.3.钢锭可采用镦粗或直接锻成锻件的方法。锻造比应不小于3.5。 4.3热处理 4.3.1锻后热处理
锻后热处理为正火和回火,随后空冷或炉冷。 4.3.2性能热处理
锻件粗加工后进行淬火加回火的性能热处理。回火冷却速度不应大于25℃/h。 4.3.3去除应力处理
锻件在性能热处理及随后的粗加工以后,应在低于最终回火温度15℃~50℃的范围内去除应力。 锻件应在此温度下保持足够长的时间以保证热透,并以适当的方式和冷却速度进行冷却以保证残余应力合格。对于残余应力合格的锻件,经需方同意也可以不进行去除应力处理。 4.4机械加工 4.4.1.粗加工
锻件全部表面均应进行粗加工。在进行正式超声检测前,不允许对锻件进行叶轮间的切槽和加工。 调质前不允许从锻件本体切取试料。 4.4.2精加工
锻件全部表面均应进行精加工。锻件的精加工尺寸精度和表面粗糙度应符合订货图样的规定。 4.5·焊接
锻件毛坏不允许焊接。 5技术要求 5.1化学成分 5.1.1:供方应对每炉钢水进行熔炼分析,分析结果应符合表1的规定。 5.1.2供方应对每个锻件进行成品分析,分析结果应符合表1的规定,但允许有表2规定的偏差。 5.1.3每个锻件均应进行气体含量分析,分析结果应符合表3的规定。当采用电渣重熔钢锭时,气体含量的要求可由供需双方另行协商规定。 5.2力学性能
锻件的常规力学性能应符合表4的规定。
表1化学成分(质量分数)
(%)
Al Sn Sb As
材料牌号 C Mn Sia P s Cr Ni Mo
Cu
0.18~ 0.25~ 0.10~ M. M 1.20~ 0.90~ 0.50~ N V ≤ N 0.25 0.80 0.40 0.012 0.012 2.00 1.10 0.80 0.05 0.15 0.010 0.015 0.0015 0.020 10.20~ 0.40~ 10.10~ .1 ≤ 1.50~
V
20Cr2NiMo
2.80~ 0.40~ N
N
V
V
M
:
22Cr2Ni3MoV
0.25 0.80 0.40 0.012 0.012 2.00 3.20 0.60 0.110 0.15 0.010 0.015 0.0015 0.020
V 0.17~ M 1.50~ 3.25~ 10.20~ 0.05~
U
V
25Cr2Ni4MoV
0.25 0.35 0.37 0.012 0.0122.00 4.00 0.50 0.15 0.15 0.010 0.0150.001510.020
a‘采用真空碳脱氧时,硅含量应不大于0.10%。 b.Sb为目标值。
2
JB/T11024—2010
表2化学成分(质量分数)的允许偏差
(%) Sb
材料牌号 20Cr2NiMo 22Cr2Ni3MoV 25Cr2Ni4MoV+0.03+0.03
Mn Si P s Cr Ni Mo
C
V
Cu
Al
Sn
AS
±0.03
+0.02
±0.02±0.03
±0.02
±0.02+0.005+0.005 ±0.05
+0.02+0.002+0.002+0.0002+0.005
±0.10
±0.01
表3 气体含量(体积分数)
(%)
02 ≤35X 10-4
H2 ≤1.5 X 104
N2 ≤70×10-
注:当采用电渣重熔钢锭时,供需双方另行协商。
表4力学性能
Rm MPa 735~880 800~950
Rpo.2 MPa ≥635 ≥680
Akva J ≥50 ≥100
A4 (%) ≥15 ≥14
FATTso ℃ ≤20 ≤-30
材料牌号
20Cr2NiMo 22Cr2Ni3MoV 25Cr2Ni4MoV 冲击试验温度为0℃。试验要求值为三个试样的平均值。允许其中一个试样的值最低不得低于规定值的70%。
5.3 硬度
在性能热处理以后应检查锻件硬度的均匀性,硬度的绝对值供参考。在同一圆周上各点间的硬度差不应超过30HBW。 5.4无损检测 5.4.1一般要求
锻件不得有裂纹、白点、缩孔、折叠、过度的偏析以及超过允许值的夹杂和疏松。 5.4.2磁粉检测
锻件的所有表面在精加工以后应进行磁粉检测,供方应保证检测结果符合以下要求: a)不允许有长度超过1.5mm的任何缺陷显示; b)同一母线上的两个缺陷之间的距离小于其中较小缺陷长度时,按一个连续缺陷处理; c)转子最终检查时,除了轴承部位之外,在其他部位发现有大于1.5mm的缺陷显示时,允许进行
局部打磨和抛光,抛光的深度不应超过1.5mm,并应与周围表面圆滑过渡。
5.4.3超声检测 5.4.3.1·锻件的超声检测结果应符合表5的要求。 5.4.3.2当量直径在Φ0.5mm以下的单个分散的缺陷信号不计,但杂波高度应低于当量直径Φ0.5mm 缺陷幅度的50%。 5.4.3.3不允许存在裂纹性质的缺陷。 5.4.3.4·缺陷区的底波损失不允许大于20%。 5.4.3.5 当需方认为锻件不能验收时,应由供需双方进行协商,但锻件是否合格应由需方决定。
JB/T 11024—2010
表5锻件的超声检测要求
单个缺陷的最大
成组缺陷的最大
密集缺陷的最大
应记录的缺陷的
当量尺寸 mm 0.5 1.0 1.6 2.0
当量尺寸 mm 0.7 1.5 2.0 3.0
区 域
当量尺寸 mm 0.5 1.0 1.6
当量尺寸 mm 1.0 2.0 3.0 5.0
s区 C区 0区 i区注1:单个缺陷信号为在任何方向上,缺陷信号之间的最近距离大于40mm的缺陷显示。 注2:成组缺陷信号为两个相邻缺陷信号之间的距离小于40mm,但在边长为50mm的立方体内只含有五个以下
1.6
的缺陷信号显示。
注3:密集缺陷信号为边长为50mm的立方体内含有五个或五个以上的缺陷信号显示。 注4:连续缺陷信号为某个测距上的缺陷当量不小于技术条件规定值,其反射幅度的波动范围在探头持续移动30mm
或30mm以上区间内不大于2dB的缺陷信号显示。 注5:游动缺陷信号为在技术条件规定灵敏度下,当探头在被移动部位移动时,信号前沿位置的游动距离相当于25mm
或25mm以上工件厚度的缺陷信号。
5.5金相组织 5.5.1晶粒度
锻件每一检查部位上的晶粒度均不得粗于4.0级。 5.5.2纯净度
锻件每一检查部位上的任一类型的夹杂物级别均不得超过3.0级。 5.6残余应力
锻件应测定残余应力。残余应力值不得超过49MPa。如果锻件的残余应力超过49MPa,则应按4.3.3 的规定进行补充去应力回火,并重新测定残余应力和硬度值。 5.7尺寸和表面粗糙度
加工后的锻件应符合锻件图样规定的尺寸、公差和表面粗糙度要求。锻件表面粗糙度除符合锻件图样要求外,还应满足本标准规定的无损检测要求。 6·检验规则和试验方法 6.1化学成分分析 6.1.1化学成分分析应按GB/T223规定的方法或能保证分析质量的其他方法进行。 6.1.2如果熔炼分析试样不符合要求或无法进行熔炼分析时,允许用成品分析代替熔炼分析,但是,当从锻件上取样进行化学成分分析时,其分析结果应符合成品分析要求。 6.1.3成品分析试样可取自锻件本体延长部分,也可取自力学性能试样。 6.1.4·气体分析试样应在切向试样上切取。 6.2力学性能检验 6.2.1拉伸试验应按GB/T228或ASTMA370规定的方法进行,冲击试验应按GB/T229规定的方法进行。 6.2.2·转子的力学性能试样应按需方订货图和取样图规定的部位和数量切取: 6.3硬度检验
硬度试验应按GB/T231.1规定的方法进行。在每个轴类锻件两端及中间部位的外圆表面每隔90°各测一点(共12点)。在每个轮盘锻件的外圆表面每隔90°各测一点(共四点)。
JB/T11024-2010
6.4无损检测 6.4.1·磁粉检测 6.4.1.1锻件外表面的磁粉检测应按JB/T8468的规定进行。 6.4.2超声检测 6.4.2.1锻件外表面的超声检测可由供方参照本标准的相关要求编制超声检测工艺,并报需方认可后实施。 6.4.2.2.锻件的超声波扫查部位分区及相应的超声波扫查方法,应按附录A的要求执行。在锻件本体部位选择S、A、0、1(见图A.1)四个部位中的无缺陷的部位,用2MHz~2.5MHz和4MHz两种频率范围中的各一个频率的探头,分别测量材料的衰减数据,并向需方报告测试结果。 6.4.2.3,锻件至少应进行两次超声检测,第一次检测在调质前进行,第二次检测在调质后进行。检测位置为所有表面。两次检测结果均应提供给需方。 6.5金相检验 6.5.1晶粒度检验应在转子轴身取切向试样,并按ASTME112:1996的规定进行。 6.5.2夹杂物检验应在转子轴身取切向试样,并按GB/T10561一2005中附录A评级图1进行评定。 6.6残余应力测定 6.6.1可采用切环法或环芯电阻应变法测定残余应力。 6.6.2采用切环法测量残余应力时,可在轴身一端切取25mm×25mm的圆环,用测量该环在切割前后平均变形量的方法来计算残余应力,计算公式为:
(1)
=ES/D
式中: Of 残余应力,单位为MPa; E一一材料的弹性模量,单位为MPa; s一直径增加的代数值,单位为mm; D一切割前环的外径,单位为mm。
6.6.3采用环芯电阻应变法测定残余应力时,应按JB/T8888的规定进行 .6.7'复试 6.7.1如果力学性能试验中某一组试验结果不合格,可在锻件上与原试样相邻部位取双倍试样进行复试。拉伸试验的双倍试样的复试结果以及初试、复试三个试样的试验结果的平均值均应满足规定要求:冲击试验的双倍试样和所有试验结果的平均值均应满足规定要求。 6.7.2力学性能检验结果如因白点和裂纹不合格的,不得复试。 6.8重新热处理 6.8.1如果锻件力学性能复试仍不合格,且试样的强度高而塑性、韧性或FATT达不到要求时,应将试样放入原位置与锻件一起重新回火,再按6.2~6.6的规定重新进行检验。 6.8.2,如果力学性能检验结果表明锻件不能进行重新回火,则允许对锻件重新进行调质热处理,重新调质热处理后,应再按6.2~6.6的规定进行检验。 6.8.3未经需方同意,不包括回火在内的重新热处理次数不允许超过两次。 7.验收及质量证明书 7.1·验收 7.1.1供方应向需方验收人员提供必要的条件,以便需方验收人员进行现场检验工作。 7.1.2需方有权选择锻件的某些试验项目进行验收试验,在验收或在以后的加工或试验中发现锻件不符合本标准和订货合同中规定的技术要求时,需方应及时通知供方,由双方协商解决。 7.2质量证明书