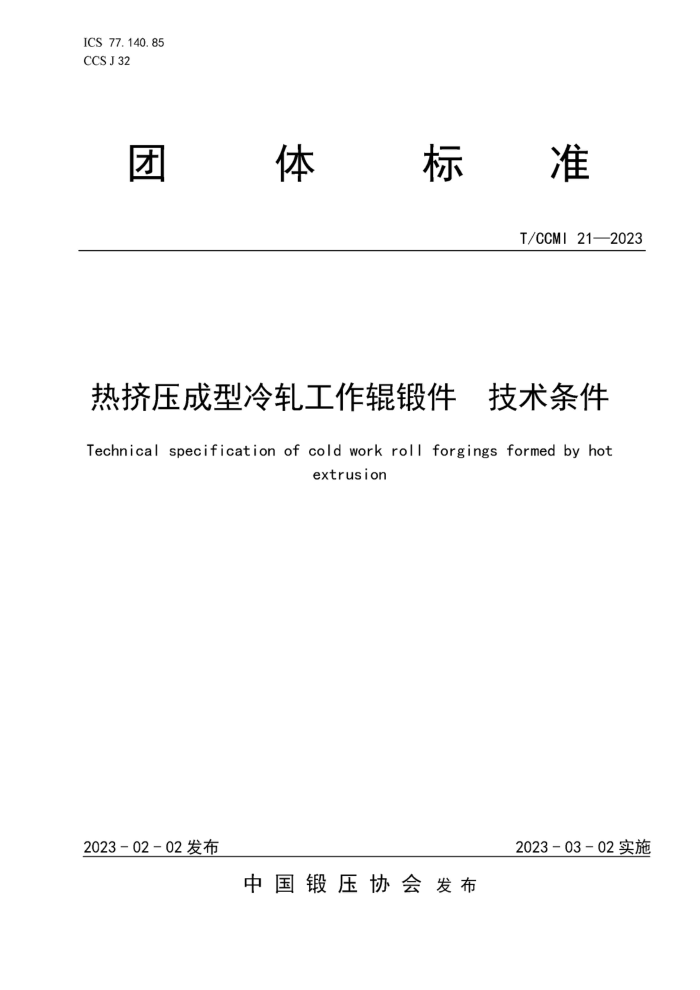
T/CCMI 212023
目次
前言范围,
II
1
规范性引用文件:术语和定义,
2
3
制造技术要求试验方法, 6 检验规则,
4
5
b
标志、清洁、包装和储运
图1热挤压成型冷轧工作辊锻件公称尺寸. 图2连铸圆坏取样示意图...... 图3 模铸坏或电渣锭化学成分偏析分析取样示意图,
表1热挤压成型冷轧工作辊锻件用钢及化学成分表2热挤压成型冷轧工作辊锻件机械加工余量及公差
T/CCMI 212023
前言
本文件按照GB/T1.1-2020《标准化工作导则第1部分:标准化文件的结构和起草规则》的规定起
草。
请注意本文件的某些内容可能涉及专利。本文件的发布机构不承担识别这些专利。 本文件由中国锻压协会提出并归口。 本文件起草单位:中国第一重型机械股份公司、一重集团常州市华冶轧辊股份有限公司、河北宏润
核装备股份有限公司。
本标准主要起草人:牛广斌、刘凯泉、张国利、时立佳、张金珠、葛浩斌、刘春海。 本文件为首次发布。
II
T/CCMI21-2023
热挤压成型冷轧工作锻件 技术条件
1范围
本文件规定了热挤压成型冷轧工作辊锻件的术语和定义、制造要求、试验方法、检测规则、标志、 包装、运输及储运。
本文件适用于连铸坏或模铸坏预制等棒坏,采用热挤压成型工艺生产辊身直径不大于700mm的冷轧工作辊锻件毛坏(以下简称:冷轧辊)。
2规范性引用文件
2
下列中的内容通过文中的规范性引用而构成本文件必不可少的条款。其中,注日期的引用文件,仅
该日期对应的版本适用于本文件;不注日期的引用文件,其最新版本(包括所有的修改单)适用于本文件。
GB/T223(所有部分) 钢铁及合金化学分析方法 GB/T226钢的低倍组织及缺陷酸蚀检验法 GB/T 1299 合金工具钢 GB/T 8541 锻压术语 GB/T13313 轧辊肖氏、里氏硬度试验方法 GB/T 13314 锻钢冷轧工作辊通用技术条件 GB/T15546 冶金轧辊术语 GB/T 15547 锻钢冷轧辊辊坏
3术语和定义
GB/T8541和GB/T15546界定的以及下列术语和定义适用本文件,
3. 1
热挤压成型冷轧工作辊锻件coldworkrollforgingsformedbyhotextrusion 采用热挤压成型工艺方式在大型水压(油)机、挤压模锻压力机等设备上利用专用挤压模具获得的
冷轧工作辊锻件。 3. 2
机械加工余量 machiningallowance 机械加工过程中,为改变工件尺寸和形状切除的金属厚度。本文件中机械加工余量由基础余量组成。
3. 3
尺寸公差dimensionaltolerance 描述冷轧工作辊锻件实际尺寸与设计公称尺寸偏差的最大允许范围。
1
T/CCMI21-2023
3. 4
冷轧工作辊公称尺寸nominaldimensionalofcoldworkroll 冷轧工作辊零件尺寸加上余量后的尺寸。
4制造技术要求
4.1化学成分
热挤压成型冷轧工作辑锻件用钢的材料牌号及其化学成分见表1。需方有要求可协商。
表1 热挤压成型冷轧工作辑锻件用钢及化学成分
单位为质量分数%
化学成分
牌号
Ni
P
si 5 C
Mn
V
Cu
C
C1 1.30 1.70
Mo
S
0.80~ ≤0.40 0. 80~
≤0.030
9Cr2
≤0.40
0. 95
8Cr2MoV 0.90 Q.15
0.30~ 1.80 0.20
0.05~
0. 40 0. 50 2. 40 0.40 0. 15
0.20~
SS
9Cr2Mo
1.70~ 0.40
≤0.25
≤0.025
Lo.
0.20~ 2.10 0.20~ 0.10~ 0. 35
0.85 0.95
.25 0.45
9Cr2MoV
0.30 0. 20
2.50~ 0.20~ 3.50
9Cr3Mo
S
0. 40
0.78~ 0.40 0.20~ 2.80 0.20~ 0.05~ 1. 10 1.10 0.50 3.20 0. 60 0. 15
≤0.025
9Cr3MoV
0.78~ 0.40 0.20~ 4.80~ 0.20~ 0.10~ ≤0.80 0. 90
≤0.25
8Cr5MoV 注:以上成分仅供参考,或可按需方化学成分要求。
≤0.020
110
0. 50
5.50
0.60
0.20
4. 2 冶炼工艺与方式 4.2. 1 钢锭冶炼工艺可采用“电弧炉/转炉+精炼炉+真空脱气炉”,用模铸其他保护法浇铸或真空浇铸。 4.2.2 连铸坏冶炼和浇铸工艺可采用“电弧炉/转炉+精炼炉+真空脱气炉+连铸”。 4.2.3 也可采用电渣重熔工艺或用户认可的其他冶炼方式。 4.3热挤压成型 4.3.1 采用热挤压模具对坏料热挤压可挤压出棒料,然后采用自由锻拔长工序锻造出成品尺寸:也可热挤压成型出冷轧工作辊成品尺寸。 4.3.2模铸钢锭应先制坏,然后进行热挤压成型锻件:采用模铸钢锭的冒口和尾部应切净且保证锭身两端有足够的切除量。 4.3.3采用连铸坏料可进行热挤压成型,应保证挤压后的锻件两端压余挤压效果不好的部分清除。 4.3.4钢加热应在温度、时间、均匀性上保证坏料具有足够的可塑性,钢加热应避免钢氧化、脱碳、 过热、过烧以及加热温度不均匀等;宜适当控制加热温度、变形温度、变形条件及冷却等工艺参数。 2
T/CCMI 212023
4.3.5热挤压宜选择足够吨位的锻压设备、工装附具及工艺以保证坏料实现挤压,锻件应满足成形尺寸并获得良好的表面状态及均匀的组织结构,应保证锻件中心线与坏料中心线重合;挤压比应大于2.5。 4.3.6挤压前模具应预热,挤压后应快速脱模,应控制挤压后的冷却速度。 4.4热挤压锻件余量及公差
热挤压冷轧工作辊锻件余量及公差应按表2确定,锻件公称尺寸应按图1确定。
5
+0.75a
0.750.
O0
.1.50
图1 热挤压成型冷轧工作辊锻件公称尺寸
表2热挤压成型冷轧工作辊锻件机械加工余量及公差
单位为毫米
零件直径D 321~400 401~500 501~600 601~700 余量a及公差
零件长度L
≤200
201~250
251~320
11 13 15 ts 19.1% 2217 25 43 28 -14
15012500
15 s 19 1 2271 25 13 29 19 31 18 19 ~% 22 7 25 13 29 1 33 1 35 13 22 71 25 -13 29 -19 33-1 37 13 41 -
2501~4000
4001~6500
6501~10000
注:台阶轴按最大直径D及总长查取余量a及公差 4.5 锻后热处理 4.5.1 锻后热处理应保证消除热挤压过程中产生的变形应力。 4.5.2 2锻后冷却方式应采用控冷+退火、正火+球化+高温回火等方式。 4. 6 锻件毛坏质量
冷轧辊锻件粗加工毛坏内部质量及表面质量可参照GB/T13314执行。
5试验方法
5.1化学成分分析方法应按GB/T223规定执行。 5.2成品化学成分偏差应按GB/T15547规定执行,来料应按以下分析方法执行:
3
T/CCMI 21-2023
a) 连铸坏的成分偏析分析:
1)制造商对连铸坏圆坏成分偏析分析; 2) 取样方法:任意一支连铸坏取样,圆坏横截面按图2所示的圆坏取样位置示意均取9点,
化学成分偏析范围应按GB/T15547执行。
O & A 4 0 O A
内弧
侧 弧
侧弧
0
3/4R
1/2R
外弧
图2 连铸圆坏取样示意图
b)7 模铸锭或电渣锭的成分偏析分析:
1)制造商在首件模铸锭或电渣锭成锻件后对成分偏析分析: 2) 应检测冒口端偏析。试样横截面应为图3所示位置取5点。化学成分偏析范围应按GB/T
15547执行。
2t
e
R
2 1
0
图3模铸坏或电渣锭化学成分偏析分析取样示意图
5.3低倍组织检验应按GB/T226规定执行。 5.4网状碳化物检验应按GB/T1299规定执行。 5.5超声波探伤检验应按GB/T13314规定执行。 5. 6 冷轧辊辊身表面裂纹检验应由供需双方协商确定。 4
T/CCMI 212023
目次
前言范围,
II
1
规范性引用文件:术语和定义,
2
3
制造技术要求试验方法, 6 检验规则,
4
5
b
标志、清洁、包装和储运
图1热挤压成型冷轧工作辊锻件公称尺寸. 图2连铸圆坏取样示意图...... 图3 模铸坏或电渣锭化学成分偏析分析取样示意图,
表1热挤压成型冷轧工作辊锻件用钢及化学成分表2热挤压成型冷轧工作辊锻件机械加工余量及公差
T/CCMI 212023
前言
本文件按照GB/T1.1-2020《标准化工作导则第1部分:标准化文件的结构和起草规则》的规定起
草。
请注意本文件的某些内容可能涉及专利。本文件的发布机构不承担识别这些专利。 本文件由中国锻压协会提出并归口。 本文件起草单位:中国第一重型机械股份公司、一重集团常州市华冶轧辊股份有限公司、河北宏润
核装备股份有限公司。
本标准主要起草人:牛广斌、刘凯泉、张国利、时立佳、张金珠、葛浩斌、刘春海。 本文件为首次发布。
II
T/CCMI21-2023
热挤压成型冷轧工作锻件 技术条件
1范围
本文件规定了热挤压成型冷轧工作辊锻件的术语和定义、制造要求、试验方法、检测规则、标志、 包装、运输及储运。
本文件适用于连铸坏或模铸坏预制等棒坏,采用热挤压成型工艺生产辊身直径不大于700mm的冷轧工作辊锻件毛坏(以下简称:冷轧辊)。
2规范性引用文件
2
下列中的内容通过文中的规范性引用而构成本文件必不可少的条款。其中,注日期的引用文件,仅
该日期对应的版本适用于本文件;不注日期的引用文件,其最新版本(包括所有的修改单)适用于本文件。
GB/T223(所有部分) 钢铁及合金化学分析方法 GB/T226钢的低倍组织及缺陷酸蚀检验法 GB/T 1299 合金工具钢 GB/T 8541 锻压术语 GB/T13313 轧辊肖氏、里氏硬度试验方法 GB/T 13314 锻钢冷轧工作辊通用技术条件 GB/T15546 冶金轧辊术语 GB/T 15547 锻钢冷轧辊辊坏
3术语和定义
GB/T8541和GB/T15546界定的以及下列术语和定义适用本文件,
3. 1
热挤压成型冷轧工作辊锻件coldworkrollforgingsformedbyhotextrusion 采用热挤压成型工艺方式在大型水压(油)机、挤压模锻压力机等设备上利用专用挤压模具获得的
冷轧工作辊锻件。 3. 2
机械加工余量 machiningallowance 机械加工过程中,为改变工件尺寸和形状切除的金属厚度。本文件中机械加工余量由基础余量组成。
3. 3
尺寸公差dimensionaltolerance 描述冷轧工作辊锻件实际尺寸与设计公称尺寸偏差的最大允许范围。
1
T/CCMI21-2023
3. 4
冷轧工作辊公称尺寸nominaldimensionalofcoldworkroll 冷轧工作辊零件尺寸加上余量后的尺寸。
4制造技术要求
4.1化学成分
热挤压成型冷轧工作辑锻件用钢的材料牌号及其化学成分见表1。需方有要求可协商。
表1 热挤压成型冷轧工作辑锻件用钢及化学成分
单位为质量分数%
化学成分
牌号
Ni
P
si 5 C
Mn
V
Cu
C
C1 1.30 1.70
Mo
S
0.80~ ≤0.40 0. 80~
≤0.030
9Cr2
≤0.40
0. 95
8Cr2MoV 0.90 Q.15
0.30~ 1.80 0.20
0.05~
0. 40 0. 50 2. 40 0.40 0. 15
0.20~
SS
9Cr2Mo
1.70~ 0.40
≤0.25
≤0.025
Lo.
0.20~ 2.10 0.20~ 0.10~ 0. 35
0.85 0.95
.25 0.45
9Cr2MoV
0.30 0. 20
2.50~ 0.20~ 3.50
9Cr3Mo
S
0. 40
0.78~ 0.40 0.20~ 2.80 0.20~ 0.05~ 1. 10 1.10 0.50 3.20 0. 60 0. 15
≤0.025
9Cr3MoV
0.78~ 0.40 0.20~ 4.80~ 0.20~ 0.10~ ≤0.80 0. 90
≤0.25
8Cr5MoV 注:以上成分仅供参考,或可按需方化学成分要求。
≤0.020
110
0. 50
5.50
0.60
0.20
4. 2 冶炼工艺与方式 4.2. 1 钢锭冶炼工艺可采用“电弧炉/转炉+精炼炉+真空脱气炉”,用模铸其他保护法浇铸或真空浇铸。 4.2.2 连铸坏冶炼和浇铸工艺可采用“电弧炉/转炉+精炼炉+真空脱气炉+连铸”。 4.2.3 也可采用电渣重熔工艺或用户认可的其他冶炼方式。 4.3热挤压成型 4.3.1 采用热挤压模具对坏料热挤压可挤压出棒料,然后采用自由锻拔长工序锻造出成品尺寸:也可热挤压成型出冷轧工作辊成品尺寸。 4.3.2模铸钢锭应先制坏,然后进行热挤压成型锻件:采用模铸钢锭的冒口和尾部应切净且保证锭身两端有足够的切除量。 4.3.3采用连铸坏料可进行热挤压成型,应保证挤压后的锻件两端压余挤压效果不好的部分清除。 4.3.4钢加热应在温度、时间、均匀性上保证坏料具有足够的可塑性,钢加热应避免钢氧化、脱碳、 过热、过烧以及加热温度不均匀等;宜适当控制加热温度、变形温度、变形条件及冷却等工艺参数。 2
T/CCMI 212023
4.3.5热挤压宜选择足够吨位的锻压设备、工装附具及工艺以保证坏料实现挤压,锻件应满足成形尺寸并获得良好的表面状态及均匀的组织结构,应保证锻件中心线与坏料中心线重合;挤压比应大于2.5。 4.3.6挤压前模具应预热,挤压后应快速脱模,应控制挤压后的冷却速度。 4.4热挤压锻件余量及公差
热挤压冷轧工作辊锻件余量及公差应按表2确定,锻件公称尺寸应按图1确定。
5
+0.75a
0.750.
O0
.1.50
图1 热挤压成型冷轧工作辊锻件公称尺寸
表2热挤压成型冷轧工作辊锻件机械加工余量及公差
单位为毫米
零件直径D 321~400 401~500 501~600 601~700 余量a及公差
零件长度L
≤200
201~250
251~320
11 13 15 ts 19.1% 2217 25 43 28 -14
15012500
15 s 19 1 2271 25 13 29 19 31 18 19 ~% 22 7 25 13 29 1 33 1 35 13 22 71 25 -13 29 -19 33-1 37 13 41 -
2501~4000
4001~6500
6501~10000
注:台阶轴按最大直径D及总长查取余量a及公差 4.5 锻后热处理 4.5.1 锻后热处理应保证消除热挤压过程中产生的变形应力。 4.5.2 2锻后冷却方式应采用控冷+退火、正火+球化+高温回火等方式。 4. 6 锻件毛坏质量
冷轧辊锻件粗加工毛坏内部质量及表面质量可参照GB/T13314执行。
5试验方法
5.1化学成分分析方法应按GB/T223规定执行。 5.2成品化学成分偏差应按GB/T15547规定执行,来料应按以下分析方法执行:
3
T/CCMI 21-2023
a) 连铸坏的成分偏析分析:
1)制造商对连铸坏圆坏成分偏析分析; 2) 取样方法:任意一支连铸坏取样,圆坏横截面按图2所示的圆坏取样位置示意均取9点,
化学成分偏析范围应按GB/T15547执行。
O & A 4 0 O A
内弧
侧 弧
侧弧
0
3/4R
1/2R
外弧
图2 连铸圆坏取样示意图
b)7 模铸锭或电渣锭的成分偏析分析:
1)制造商在首件模铸锭或电渣锭成锻件后对成分偏析分析: 2) 应检测冒口端偏析。试样横截面应为图3所示位置取5点。化学成分偏析范围应按GB/T
15547执行。
2t
e
R
2 1
0
图3模铸坏或电渣锭化学成分偏析分析取样示意图
5.3低倍组织检验应按GB/T226规定执行。 5.4网状碳化物检验应按GB/T1299规定执行。 5.5超声波探伤检验应按GB/T13314规定执行。 5. 6 冷轧辊辊身表面裂纹检验应由供需双方协商确定。 4