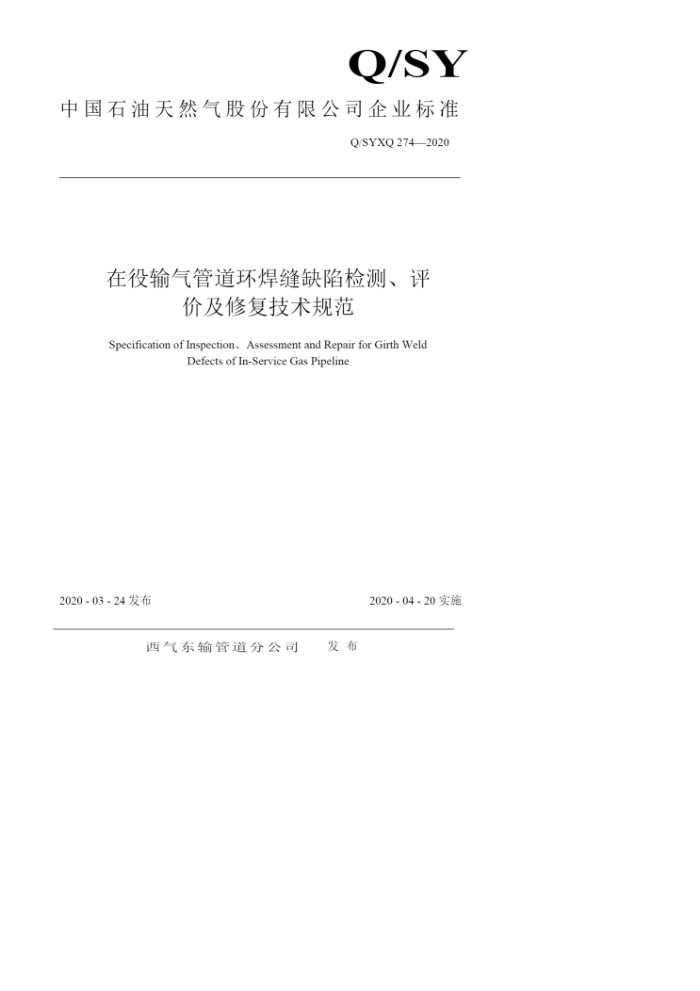
Q/SY
中国石油天然气股份有限公司企业标准
Q/SYXQ2742020
在役输气管道环焊缝缺陷检测、评
价及修复技术规范
Specification of Inspection、Assessment and Repair for Girth Weld
Defects of In-Service Gas Pipeline
2020-04-20实施
2020-03-24发布
西气东输管道分公司 发布
Q/SYXQ274—2020
目 次
前
II
二
1范围 2规范性引用文件 3术语、定义与符号 4资料收集 5环焊缝检测方法 6环焊缝缺陷评价 7评价报告 8管道环焊缝修复附录A(规范性附录)环焊缝缺陷开挖检测数据记录表,附录B(资料性附录)冲击功与CTOD转换关系附录C(资料性附录)环焊缝轴向应力分析附录D(资料性附录)环焊缝残余应力分析,
13
13
16
17
18
. 21
Q/SYXQ 274—2020
前言
本标准微据GB1.1-2009《标准化工作导则第1静分:标准的酷构和编驾》给出的规期起草。 本瑞准由中国石油国气东输标准化委员会提册并妇口。 本标准起章单位:西气东输分公司、中国石油天然气管道料学研究院有限公司、中国石油天然气集团会
司管材新究所
本编准主夏超章人:毛建、李暂、修林亭、丁疆激、顾清林、姜承落、占传恩、黄亮亮、彩区、就型得、 杨平、刘艳华、孙巧飞
I
Q/SYXQ 274—2020
在役输气管道环焊缝缺陷检测、评价及修复技术规范
1范围
本标准规定了在役输气管道环焊缝缺陷检测和表征、缺陷的评价及修复。 本标准适用于钢级X80及以下、管径D1219mm及以下规格在役输气管道环焊缝质量
排查,其它在役输气管道环焊缝缺陷检测、评价、修复可参考本标准执行。
本标准不适用于输气管道场站、阀室环焊缝质量排查。 规范性引用文件
2
下列文件对于本文件的应用是必不可少的。凡是注日期的引用文件,仅所注日期的版本适用于本文件。凡是不注日期的引用文件,其最新版本(包括所有的修改单)适用于本文件。
油气长输管道工程施工及验收规范无损检测残余应力超声临界折射纵波检测方法在用含缺陷压力容器安全评定理地钢质管道管体缺陷修复指南油气输送管道跨越工程设计标准无损检测又射线应力测定方法石油天然气钢质管道无损检测含缺陷油气管造剩余强度评价方法承压设备无损检测第10部分:射时差法超声检测油气储运工程无损检测技术规范第2部分:钢质管道相控阵超声检测
GB 50369 GB 32073 GB/T 19624 GB/T 36701 GB/T 50459 GB/T 7704 SY/T 4109 SY/T 6477 NB/T 47013.10 Q/SY 06317.2
API 579-1/ASME FFS-1 Fitness-For-Service
3术语、定义与符号 3.1术语、定义 3.1.1金属损失型缺陷 metal loss flaw
环焊缝及合环焊缝管体由于金属损失造成的缺陷,包括:离蚀、未焊满、沟槽。 3.1.2裂纹型缺陷crack-likeflaw
一种根部尖锐的面型缺陷,主要参数有裂纹深度和长度,包括:裂纹、未熔合、未焊透、咬边、内凹。 3.1.3缺陷表征 defect characterization
将实际缺陷按规则简化为一个简单几何形状的缺陷,称为缺陷表征或缺陷的规则化。 经表征或规则化的缺陷尺寸称为表征缺陷尺寸。
3
Q/SYXQ 274—2020
3.1. 4 断裂评定 fracture assessment
采用断裂力学的方法,评价含缺陷管道能否排除断裂失效的安全评定。 3.1.5 塑性失效评价plasticcollapseassessment
采用塑性极限分析的方法,评价含缺陷管道能否排除塑性失效的安全评定。 3. 2 符号
a为纹在沿钢管厚方向的尺寸,mm; 管道壁厚;计算环焊缝中因错边引起的弯曲二次应力时,错边两侧的管道壁厚的较大值,mm: 计算环焊缝中因错边引起的弯曲二次应力时,错边两侧的管道壁厚的较小值,mm; 裂纹在沿钢管表面方向的半长,mm; 夏比冲击功,J:钢管外径,mm; 在评定溢度下的材料弹性模量, ,一般取值2.07×10°MPa: 表征理藏精圆裂纹中心偏离壁厚中心的偏心距,mm; 错边量,mm; 跨越管道强度设计系数;瑞和需的总称,无量剩计算由薄膜应力6m引起的裂纹尺寸a方向裂纹尖端处应力强度因子时所用的裂纹构型因子,无量纲:计算由薄膜应力om引起的裂纹尺寸c方向裂纹尖端处应力强度因子时所用的裂纹构型固子,无量纲;给和瑞的总称,无量纳;计算由弯曲应力引起的裂纹尺寸a方向裂纹尖端处应力强度因子时所用的裂纹构型因子,无量纲;计算由弯曲应力og引起的裂纹尺寸c方向裂纹尖端处应力强度因子时所用的裂纹构型因子,无量纲相邻两裂纹间弹塑性干涉效应系数,无量纲;应力强度因子,MPa(mm)"; 一次应力引起的应力强度因子, MPa(mm)2; 二次应力引起的应力强度因子,MPa(mm)"2;施加载荷作用下的应力强度因子与以应力强度因子表示的材料断裂韧度的比值,无量纲;平面缺陷常规评定中考虑了分安全系数后,! 以应力强度因子表的材料断裂韧性,MPa(mm)"2;
a B Bi B2 c Cv D E e 81 F fnt f 蕴 fe f f G Kt KS KP K Kp
4
Q/SYXQ 274—2020
L Lr M n R s so W 5 6 8 1 x 6 Oa Oh Gar dp OaR Gog Om OB Ca: Oa 0; Gr p Wi 2 资料收集
板长的一半,mm 载荷比,指引起一次应力的施加载荷与塑性屈服极限载荷的比值,表示载荷接近于材料塑性屈服极限载荷的程度,无量纲;鼓胀系数,无量纲:应变强化指数,无量纲;管道弯自半径,m;两共面裂纹间的间距,mm; 判断两共面裂纹是否应合并的临界间距,mm 试样宽度的一半,mm; 管道许用拉应力提高系数,无量纲; CTOD值,mm; 均匀延伸率;泊松比,无量纲;以焊缝中心为零点, 沿管道轴向的距离,mm; 应力,MPa; 管道轴向应力,MPa; 管道环向应力,MPa;温差应力,MPa; 内压引起的轴向应力,MPa:弹性敷设引起的轴向应力,MPa; 均布载荷引起的轴向应力,MPa; 薄膜应力,MPa 由应力分布线性化规则得到的弯曲应力,MPa;计算得到的缺陷所能承受的轴向临界应力,MPa; 检测得到的轴向应力,MPa; 屈服强度,MPa 残余应力,MPa; 平面缺陷评定中计算二次应力的塑性修正因子,无量纲;平面缺陷评定中,为计算Kr所涉及的塑性修正因子p时的中间参量,无量纲; Q=0a/0a
4
管道缺陷检测及评价时,应收集以下信息:
4.1
a)管道的基本信息,包 包括但不限于:管道钢级、管 管径、壁厚、设计压力、设计系数等。
5
Q/SYXQ 274—2020
b)进行缺陷检测及评价前应收集环焊缝基本信息,包括但不限于:焊接坡口形式及尺寸、焊接工艺、焊接验收指标、焊口类型(正常口、弯管口、变壁厚口、自由连头口、碰死口、返修口等)。 c)收集环焊缝内检测信息,包括但不限于:内检测环焊缝编号、内检测里程、环焊缝与制管焊缝交点、环焊缝异常特征信息等。 d)记录环焊缝所处环境情况,包括但不限于:当地温差变化、管道坡度、距离弯管距离、弯管角度以及地质运动情况等。
4.2环焊缝数据收集信息参照附件A记录。 环焊缝检测方法
5
5.1 环焊缝缺陷检测方法 5.1.1 环焊缝缺陷检测方法包括:久 外观检测、渗透检测(PT)、 磁粉检测(MT)、 射线检测(RT)、超声波检测(A型脉冲反射法(UT)、相控阵超声检测(PAUT)超声波衍射时差法(TOFD))等,各类缺陷所对应检测方法及工具、设备宜参见表 1。
表1环焊缝缺陷检测方法及工具、设备
缺陷
分类 / 表面气孔内部及埋藏气孔 射线检测、超声波检测
检测方法外观检测外观检测外观检测
检测工具、设备焊接检验尺焊接检验尺
类型余高错边气孔夹渣 表面夹渣
焊接检验尺、深度尺、游标卡尺、刻度尺、半径规、轮廊规等
RT、UT
焊接检验尺、深度尺、游标卡尺、刻度尺、半径规、轮廊规等
外观检测
内部及埋藏夹渣 射线检测、超声波检测
RT、 UT
焊接检验尺、深度尺、游标卡尺、刻度尺、半径规、轮廊规等
金属 外表面金属损失缺陷
外观检测
缺陷 损失咬边裂纹未熔 根部及夹层未熔合 射线检测、超声波检测 RT、UT、PAUT、TOFD 未焊 根部、错变未焊透及 射线检测、超声波检测 RT、UT、PAUT、TOFD
内部金属损失缺陷 射线检测、超声波检测
RT、超声测厚仪焊接检验尺
外咬边内咬边外表面裂纹 渗透检测、磁粉检测、 清洗剂、渗透剂、显像剂、磁轭
外观检测射线检测、超声波检测 RT、UT、PAUT、TOFD 射线检测、超声波检测 探伤仪、RT、UT、PAUT
内部及埋藏裂纹 射线检测、超声波检测 RT、UT、PAUT、TOFD
合透内凹烧穿
中间未焊透
射线检测、超声波检测 RT、UT、PAUT、TOFD 射线检测、超声波检测 RT、UT、PAUT、TOFD
6
Q/SYXQ 274—2020
5.1.2 环焊缝开挖排查,应首先采用外观检测、RT、UT对环焊缝进行检测。发现表面裂纹时,应采用PT、MT、PAUT和TOFD进行复核。当发现根部及埋藏型裂纹,以及严重超标的未熔合、未焊透等裂纹型缺陷时,应采用PAUT和TOFD进行确认和复核。 5.1.3 外观检测
a)环焊缝外观检测比例为100%。 b)外观检测前应去除环焊缝表面防腐层,避免因表面残留物而掩盖表面缺陷。 c)测量并记录环焊缝外观缺陷,外观验收标准应根据施工验收规范或GB50369 执行,包括以下内容:
一焊缝余高:环向长度、高度及起始钟点位置。 一焊缝错边:环向长度、错边量及起始钟点位置。 一焊缝外咬边:环向长度、深度及起始钟点位置。
d)测量并记录外部金属损失缺陷,包括以下内容
一沟槽:轴向长度、环向长度、深度或高度差、底部曲率半径及起始钟点位置。 一未焊满:轴向长度、环向长度、深度、底部曲率半径以及起始钟点位置一腐蚀缺陷:轴向长度、环向长度以、深度以及起始钟点位置。若腐蚀缺陷面积较大,可对腐蚀区域进行网格划分,网格间距宜控制在5-20mm。
5.1.4 渗透检测/磁粉检测
对于环焊缝表面裂纹、外部金属损失缺陷底部裂纹可采用渗透检测或磁粉检测,具体方法参照SY/T4109执行。 b)记录表面裂纹方向、环向长度、轴向长度及起始钟点位置。
a)
5.1.5 射线检测
a) 射线检测宜在目视检测及渗透/磁粉检测之后进行。
环焊缝射线检测应采用双壁透照方式,具体要求参照SY/T4109执行。
b)
c) 记录缺陷类型、缺陷轴向长度、缺陷环向长度以及起始钟点位置 5.1.6超声波检测
超声波检测可采用A型脉冲反射法(UT)、超声相控阵检测(PAUT)、衍
a)
射时差法(TOFD)等方法。 b) A型脉冲反射法应与射线检测配合使用。 c)A型脉冲反射法超声波探伤宜在射线探伤之后进行,对于射线检测以及内检测发现缺陷部位应进行重点检测,具体要求参照SY/T4109执行。 d)超声相控阵检测(PAUT)具体要求参照Q/SY06317.2执行。
7