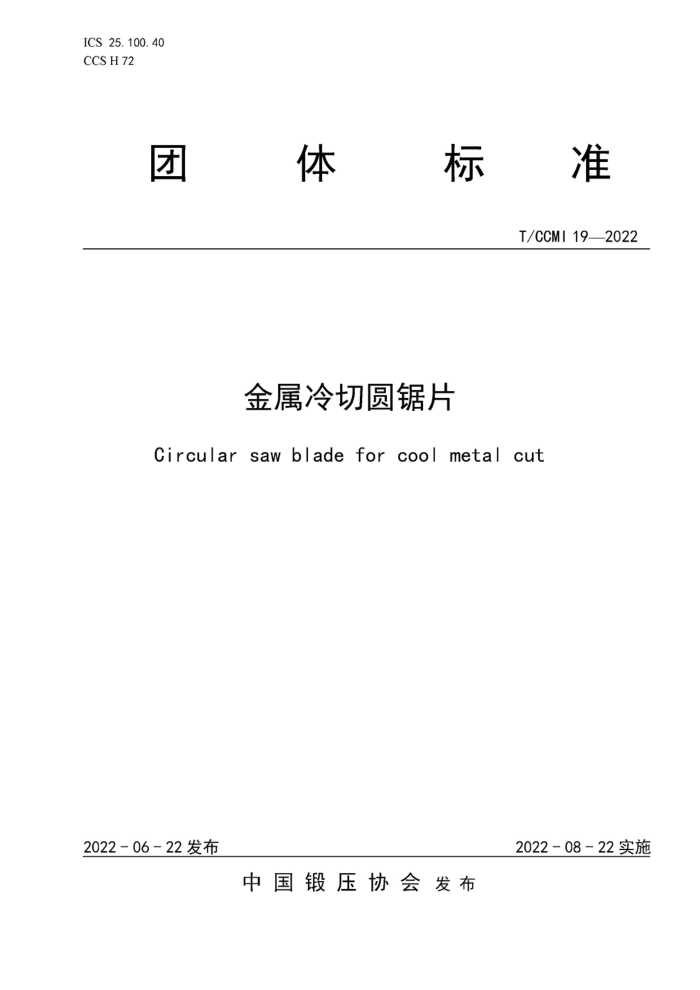
T/CCMI19-2022
目次
前言范围,
II
1
规范性引用文件 3术语和定义
2
结构形式、基本参数、尺寸标记 5 技术要求
4
检验方法,检验规则标识、包装、运输和储存
6
b
7
c
8
X
附录A(资料性) 金属冷切圆锯片使用寿命.
10
图1锯片结构形式图2 锯片齿形和角度图3锯片适张度检测方法,图4 锯片焊接强度检测方法图5 锯片侧刃面技术参数检测方法. 图6 锯片的径向圆跳动检测方法. 图7 锯片平面度检测方法,
表1 锯片基本参数及尺寸. 表2锯片片体加工精度要求表3锯片焊接技术要求. 表4锯片刀刃研磨技术要求表5锯片形状位置公差. 表6出厂检验项目及抽样规则,
T/CCMI192022
前言
本文件按照GB/T1.1-2020《标准化工作导则第1部分:标准化文件的结构和起草规则》的规定起
草。
请注意本文件的某些内容可能涉及专利。本文件的发布机构不承担识别专利的责任。 本文件由杭州博野精密工具有限公司提出。 本文件由中国锻压协会归口。 本文件起草单位:杭州博野精密工具有限公司、浙江至广精密工具有限公司、浙江锐力智能装备有
限公司、昆山耐锐德精密工具有限公司、山东黑旋风锯业有限公司,苏州金凯达机械科技股份有限公司、 苏州小野精密刀具有限公司、浙江精卫特机床有限公司、小林金刚石刀具(杭州)有限公司、凯控自动化设备(天津)有限公司。
本文件主要起草人:张涛、刘占仁、胡龙、宁建峰、应鹏飞、胡汉明、冯浩华、柯晓华、黄雅平、 沈金卫、秦京武、 刘剑涵、杨裕琳、赵志孟、侯路通、禹俊、蒋志超、姜国飞、陈澎军、华玉坤、李志
P O
C
新。
本文件为 首 布
II
T/CCMI 192022
金属冷切圆锯片
1范围
本文件规定了金属冷切圆锯片(简称锯片)的结构形式、基本参数、尺寸标记、技术要求、检验方法、检验规则、标识、包装、运输和储存。
本文件适用于在常温状态下锯切金属棒材、板材、管材、型材,外径在0200mm~0960mm的金属冷切圆锯片。
2规范性引用文件
2
下列文件中的内容通过文中的规范性引用而构成本文件必不可少的条款。其中,注日期的引用文件,仅该日期对应的版本适用于本文件;不注日期的引用文件,其最新版本(包括所有的修改单)适用于本文件。
-
0
GB/T 191 包装储运图示标志(IS0780:1997,MOD)
C
金属材料 洛氏硬度试验 第1部分:试验方法
GB/T 230.1
3术语和定义
义适用于本文件。
下列术语和定
0
3.1冷切 cold cut
A
采用切割过程不产生高温的技术手段和方法,使被切物保持原有材料特性,切割过程温度没有剧烈的升温变化的 J一种切割方法。 通常温升不超过40摄氏度
A
3. 2 适张度 proper tension
S
在锯片片体适当位置局部通过锤击或磁压等机械方式改变锯片固有的应力结构,使锯片片体达到一定的张力度。
4结构形式、基本参数、尺寸标记
4.1锯片结构形式
锯片结构形式应符合图1、齿形和角度应符合图2规定。
1
T/CCMI19-2022
图1 锯片结构形式
±0.
侧刃面视图
前刃面视图
齿顶面视图齿顶面两侧倒角角度;分屑槽宽度;锯齿的侧刃面向心角;一后角;
相邻两个齿之间的间距;一齿顶面两侧倒角长度;相邻两个齿上分屑槽中心间距;锯齿的侧刃面突出量;
a
C b1- 1 Y- 一 一负前角: t :
L
a
Y' 断屑槽前角:
一负刀面宽度;锯齿的侧刃面切向后角
断屑槽圆弧半径;
R
注:齿顶面需开分屑槽,在相邻两齿上按锯片厚度中心交错对称分布。
图2 锯片齿形和角度
4. 2 锯片基本参数
锯片基本参数及尺寸应符合表1规定。
2
T/CCMI19-2022
表1 锯片基本参数及尺寸
外径(D) 锯齿宽度 片体厚度(b) 安装孔 传动孔(d1) 传动孔分布圆
齿数 (Z) 54、60、72 60、80、100
(B) mm 1. 5 2. 0 2. 0 2. 6 2.7 2.7 2. 7 3. 0 3. 4 3. 8 C37 3. 8 F 3. 2 4. 0 O 3.2 4. 0 S 3.2
(d) mm 32 32 32 40 50 50 50 50 80 80 80 80 80
(D1) mm 50 50 63 90 90 90 90 120 160 180 180 180 200
mm 225 250 285 360 425 460 500 560 630 680 750 840 960 注:其它非标规格可根据上表相近规格设计加工 4. 3 锯片标记
mm 1. 25 1. 7 1. 7 2. 25 2. 25 2. 25 2. 25 2.5 :1
mm 9 9 11 11 16 21 21 21 23 23 23 26 26
54、60、80、100、120 60、80、 100, 120、140
60、80、100 60、80、100、 、120、140 60、80、100、120 40、60、80、100 40、60、80、100 40、60、80、100 40、60、80、100
40、 、60、80、100 40、60、80、100
R 要素的含义如下:
锯片标记及标讠
(b) X Z
D X
0
齿数片体厚度锯齿宽度安装孔径外径
?
+ ★ X
Z A
S
示例: 285 X 32 X 2.0 X 1.7 X 72
5 技术要求
5. 1 锯片片体技术要求 5.1.1 锯片片体原材料一般选用8CrV、8CrNi2冷轧钢板或可保证使用性能的其它合金工具钢制造,钢板的硬度HBW不大于240。 5.1.2 锯片片体一般做淬火回火处理,回火后主要组织应为回火屈氏体,热处理后硬度HRC46HRC50。 5. 1.3 锯片片体加工精度要求见表2。
3
T/CCMI19-2022
表2 锯片片体加工精度要求
单位
序号 1 2 3 4 5 6 5. 2 锯片焊接技术要求
技术项目片体厚度片体同片厚度差
技术要求 (0.02,0.015)
≤0. 02 ≤1. 6 H7 (0,0.5) (0, 0.30)
mm um
片体表面粗糙度(Ra)
安装孔直径传动孔直径片体适张度
mm mm
锯片焊接技术要求见表3。
S 技术项目焊接强度(剪切强度)片体焊接热影响区硬度 S
表3 锯片焊接技术要求
序号 1 2 锯片刀刃研磨技术要求
单位 MPa HRC
技术要求 ≥180 40~55
5. 3
S R
锯片刀刃研磨技术要求见表4。
P
表4 锯片刀刃研磨技术要求
3 技术项目研磨面粗糙度(Ra)两侧刃面向心角对称度负刀面宽度一致性
序号 1 2 3 4 3 L5 6 5. 4 锯片形状位置公差
单位 μm mm mm m mm mm mm
技术要求 ≤0.4 ≤0. 02 ≤0. 02 ≤0. 02 ≤0. 04 ≤0. 03 ≤0. 02
两侧刃面突出量对称度两侧刃面切向后角对称度
齿顶面两侧倒角长度对称度
锯齿宽度差
锯片形状位置公差见表5。
表5 锯片形状位置公差
单位为毫米
公差
项目
200≤D<300 300≤D<400 400≤D<500 500≤D<600 600≤D<700 700≤D<960
锯齿顶刃对安装孔轴线的径
0. 03
0. 05
0. 04
向圆跳动片体平面度
0. 02
0. 03
0. 04
0. 06 ≤00.30
0. 08
0. 10
传动孔对安装孔的位置度
4
T/CCMI19-2022
目次
前言范围,
II
1
规范性引用文件 3术语和定义
2
结构形式、基本参数、尺寸标记 5 技术要求
4
检验方法,检验规则标识、包装、运输和储存
6
b
7
c
8
X
附录A(资料性) 金属冷切圆锯片使用寿命.
10
图1锯片结构形式图2 锯片齿形和角度图3锯片适张度检测方法,图4 锯片焊接强度检测方法图5 锯片侧刃面技术参数检测方法. 图6 锯片的径向圆跳动检测方法. 图7 锯片平面度检测方法,
表1 锯片基本参数及尺寸. 表2锯片片体加工精度要求表3锯片焊接技术要求. 表4锯片刀刃研磨技术要求表5锯片形状位置公差. 表6出厂检验项目及抽样规则,
T/CCMI192022
前言
本文件按照GB/T1.1-2020《标准化工作导则第1部分:标准化文件的结构和起草规则》的规定起
草。
请注意本文件的某些内容可能涉及专利。本文件的发布机构不承担识别专利的责任。 本文件由杭州博野精密工具有限公司提出。 本文件由中国锻压协会归口。 本文件起草单位:杭州博野精密工具有限公司、浙江至广精密工具有限公司、浙江锐力智能装备有
限公司、昆山耐锐德精密工具有限公司、山东黑旋风锯业有限公司,苏州金凯达机械科技股份有限公司、 苏州小野精密刀具有限公司、浙江精卫特机床有限公司、小林金刚石刀具(杭州)有限公司、凯控自动化设备(天津)有限公司。
本文件主要起草人:张涛、刘占仁、胡龙、宁建峰、应鹏飞、胡汉明、冯浩华、柯晓华、黄雅平、 沈金卫、秦京武、 刘剑涵、杨裕琳、赵志孟、侯路通、禹俊、蒋志超、姜国飞、陈澎军、华玉坤、李志
P O
C
新。
本文件为 首 布
II
T/CCMI 192022
金属冷切圆锯片
1范围
本文件规定了金属冷切圆锯片(简称锯片)的结构形式、基本参数、尺寸标记、技术要求、检验方法、检验规则、标识、包装、运输和储存。
本文件适用于在常温状态下锯切金属棒材、板材、管材、型材,外径在0200mm~0960mm的金属冷切圆锯片。
2规范性引用文件
2
下列文件中的内容通过文中的规范性引用而构成本文件必不可少的条款。其中,注日期的引用文件,仅该日期对应的版本适用于本文件;不注日期的引用文件,其最新版本(包括所有的修改单)适用于本文件。
-
0
GB/T 191 包装储运图示标志(IS0780:1997,MOD)
C
金属材料 洛氏硬度试验 第1部分:试验方法
GB/T 230.1
3术语和定义
义适用于本文件。
下列术语和定
0
3.1冷切 cold cut
A
采用切割过程不产生高温的技术手段和方法,使被切物保持原有材料特性,切割过程温度没有剧烈的升温变化的 J一种切割方法。 通常温升不超过40摄氏度
A
3. 2 适张度 proper tension
S
在锯片片体适当位置局部通过锤击或磁压等机械方式改变锯片固有的应力结构,使锯片片体达到一定的张力度。
4结构形式、基本参数、尺寸标记
4.1锯片结构形式
锯片结构形式应符合图1、齿形和角度应符合图2规定。
1
T/CCMI19-2022
图1 锯片结构形式
±0.
侧刃面视图
前刃面视图
齿顶面视图齿顶面两侧倒角角度;分屑槽宽度;锯齿的侧刃面向心角;一后角;
相邻两个齿之间的间距;一齿顶面两侧倒角长度;相邻两个齿上分屑槽中心间距;锯齿的侧刃面突出量;
a
C b1- 1 Y- 一 一负前角: t :
L
a
Y' 断屑槽前角:
一负刀面宽度;锯齿的侧刃面切向后角
断屑槽圆弧半径;
R
注:齿顶面需开分屑槽,在相邻两齿上按锯片厚度中心交错对称分布。
图2 锯片齿形和角度
4. 2 锯片基本参数
锯片基本参数及尺寸应符合表1规定。
2
T/CCMI19-2022
表1 锯片基本参数及尺寸
外径(D) 锯齿宽度 片体厚度(b) 安装孔 传动孔(d1) 传动孔分布圆
齿数 (Z) 54、60、72 60、80、100
(B) mm 1. 5 2. 0 2. 0 2. 6 2.7 2.7 2. 7 3. 0 3. 4 3. 8 C37 3. 8 F 3. 2 4. 0 O 3.2 4. 0 S 3.2
(d) mm 32 32 32 40 50 50 50 50 80 80 80 80 80
(D1) mm 50 50 63 90 90 90 90 120 160 180 180 180 200
mm 225 250 285 360 425 460 500 560 630 680 750 840 960 注:其它非标规格可根据上表相近规格设计加工 4. 3 锯片标记
mm 1. 25 1. 7 1. 7 2. 25 2. 25 2. 25 2. 25 2.5 :1
mm 9 9 11 11 16 21 21 21 23 23 23 26 26
54、60、80、100、120 60、80、 100, 120、140
60、80、100 60、80、100、 、120、140 60、80、100、120 40、60、80、100 40、60、80、100 40、60、80、100 40、60、80、100
40、 、60、80、100 40、60、80、100
R 要素的含义如下:
锯片标记及标讠
(b) X Z
D X
0
齿数片体厚度锯齿宽度安装孔径外径
?
+ ★ X
Z A
S
示例: 285 X 32 X 2.0 X 1.7 X 72
5 技术要求
5. 1 锯片片体技术要求 5.1.1 锯片片体原材料一般选用8CrV、8CrNi2冷轧钢板或可保证使用性能的其它合金工具钢制造,钢板的硬度HBW不大于240。 5.1.2 锯片片体一般做淬火回火处理,回火后主要组织应为回火屈氏体,热处理后硬度HRC46HRC50。 5. 1.3 锯片片体加工精度要求见表2。
3
T/CCMI19-2022
表2 锯片片体加工精度要求
单位
序号 1 2 3 4 5 6 5. 2 锯片焊接技术要求
技术项目片体厚度片体同片厚度差
技术要求 (0.02,0.015)
≤0. 02 ≤1. 6 H7 (0,0.5) (0, 0.30)
mm um
片体表面粗糙度(Ra)
安装孔直径传动孔直径片体适张度
mm mm
锯片焊接技术要求见表3。
S 技术项目焊接强度(剪切强度)片体焊接热影响区硬度 S
表3 锯片焊接技术要求
序号 1 2 锯片刀刃研磨技术要求
单位 MPa HRC
技术要求 ≥180 40~55
5. 3
S R
锯片刀刃研磨技术要求见表4。
P
表4 锯片刀刃研磨技术要求
3 技术项目研磨面粗糙度(Ra)两侧刃面向心角对称度负刀面宽度一致性
序号 1 2 3 4 3 L5 6 5. 4 锯片形状位置公差
单位 μm mm mm m mm mm mm
技术要求 ≤0.4 ≤0. 02 ≤0. 02 ≤0. 02 ≤0. 04 ≤0. 03 ≤0. 02
两侧刃面突出量对称度两侧刃面切向后角对称度
齿顶面两侧倒角长度对称度
锯齿宽度差
锯片形状位置公差见表5。
表5 锯片形状位置公差
单位为毫米
公差
项目
200≤D<300 300≤D<400 400≤D<500 500≤D<600 600≤D<700 700≤D<960
锯齿顶刃对安装孔轴线的径
0. 03
0. 05
0. 04
向圆跳动片体平面度
0. 02
0. 03
0. 04
0. 06 ≤00.30
0. 08
0. 10
传动孔对安装孔的位置度
4