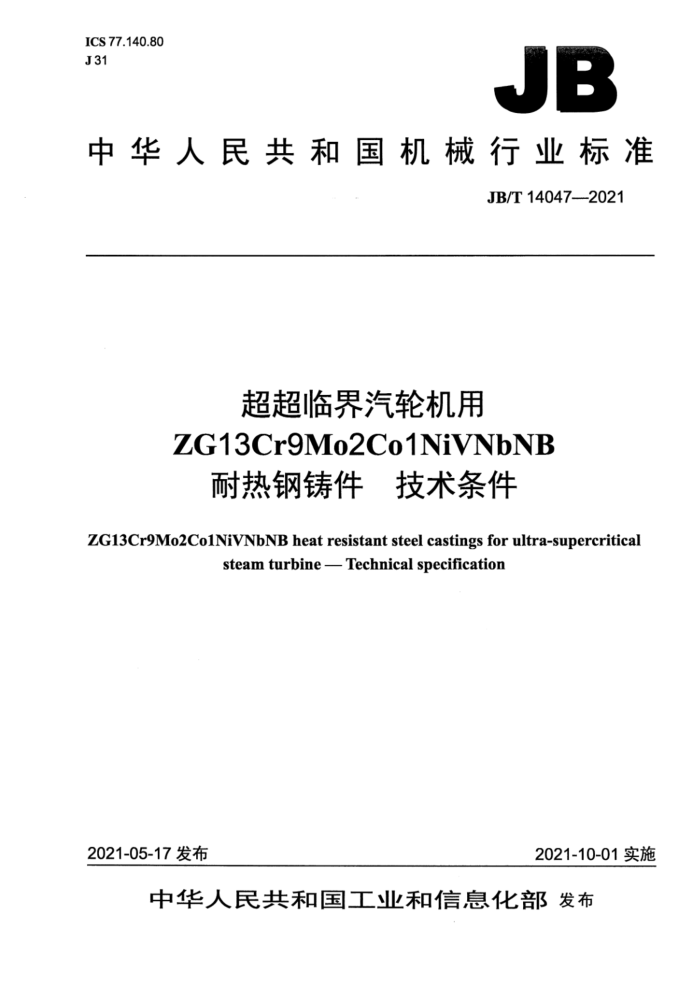
JB
中华人民共和国机械行业标准
JB/T14047--2021
超超临界汽轮机用
ZG13Cr9Mo2Co1NiVNbNB
耐热钢铸件 技术条件
一
ZG13Cr9Mo2Co1NiVNbNB heat resistant steel castings for ultra-supercritical
steam turbineTechnical specification
2021-05-17发布
2021-10-01实施
目 次
前言 1范围.. 2规范性引用文件, 3订货要求.. 4制造工艺. 4.1治炼... 4.2铸造...
4.3 热处理. 4.4 焊接 5技术要求. 5.1 化学成分 5.2 力学性能. 5.3 硬度. 5.4 铸件表面质量. 5.5 无损检测. 5.6 水压试验. 5.7 形状与尺寸公差. 5.8 重量公差. 5.9 工艺评审试验要求. 6检验规则和试验方法 6.1 化学成分分析. 6.2 力学性能试验.. 6.3 无损检测 6.4 水压试验 6.5 工艺评审试验. 6.6 复试和重新热处理 7验收和质量证明书 8标识和包装。
表1化学成分. 表2成品化学成分的允许偏差表3室温力学性能表4铸件粗加工尺寸允许的极限偏差
前言
本标准按照GB/T1.12009给出的规则起草。 本标准由中国机械工业联合会提出。 本标准由全国大型铸锻件标准化技术委员会(SAC/TC506)归口。 本标准起草单位:上海电气电站设备有限公司上海汽轮机厂、二重(德阳)重型装备有限公司、哈
尔滨汽轮机厂有限责任公司。
本标准主要起草人:沈红卫、丁丽锋、刘松锋、许存官、张帆、陈雷、张舒、肖章玉、刘新新、张小伍。
本标准为首次发布。
超超临界汽轮机用ZG13Cr9Mo2Co1NiVNbNB
耐热钢铸件技术条件
1范围
本标准规定了超超临界汽轮机用ZG13Cr9Mo2Co1NiVNbNB耐热钢铸件的订货要求、制造工艺、
技术要求、检验规则和试验方法、验收和质量证明书、标识和包装。
本标准适用于工作温度为630℃的超超临界汽轮机用ZG13Cr9Mo2Co1NiVNbNB耐热钢汽缸、 阀壳等铸件(以下简称铸件)的订货、制造、检验和验收。
2规范性引用文件
下列文件对于本文件的应用是必不可少的。凡是注日期的引用文件,仅注日期的版本适用于本文件。凡是不注日期的引用文件,其最新版本(包括所有的修改单)适用于本文件。
GB/T223(所有部分) 钢铁及合金化学分析方法 GB/T228.1 金属材料拉伸试验第1部分:室温试验方法 GB/T 228.2 金属材料扌 拉伸试验第2部分:高温试验方法 GB/T229 金属材料夏比摆锤冲击试验方法 GB/T231.1 金属材料布氏硬度试验第1部分:试验方法 GB/T2039 金属材料单轴拉伸蠕变试验方法 GB/T5677 铸件射线照相检测 GB/T5678 铸造合金光谱分析取样方法 GB/T6394 金属平均晶粒度测定方法 GB/T6414一2017铸件尺寸公差、几何公差与机械加工余量 GB/T9443铸钢铸铁件渗透检测 GB/T11170 )不锈钢多元素含量的测定火花放电原子发射光谱法(常规法) GB/T11351 铸件重量公差 GB/T13298金属显微组织检验方法 GB/T20066钢和铁化学成分测定用试样的取样和制样方法 JB/T4058-2017汽轮机清洁度 JB/T9629汽轮机承压件水压试验技术条件 JB/T9630.1汽轮机铸钢件磁粉探伤及质量分级方法 JB/T9630.2汽轮机铸钢件超声波探伤及质量分级方法 YB/T4402 2马氏体不锈钢中铁素体含量金相测定法
3订货要求
3.1供方应有完善的质量保证体系,并应具有类似材料、相近尺寸的铸件的生产业绩。
3.3需方提供的铸件订货图样(如粗加工图、无损检测图、组焊图等)与本标准共同构成订货合同的一部分。 3.4铸件应经性能热处理及粗加工后交货,如果图样中有组焊要求,还应按照图样要求完成组焊后交货。
4制造工艺
4.1冶炼
铸件用钢应采用电炉冶炼,并经过二次精炼,如钢包精炼(LF)或真空除气(VD)。经需方同意,也可采用能保证质量的其他冶炼方法。 4.2铸造 4.2.1铸造时应保持铸型的清洁和干燥,未经需方书面许可,不得使用芯撑和内冷铁。 4.2.2附铸试块应附在铸件的主壁厚区域,并保证铸件有足够数量的附铸试块用于供方和需方的试验。 4.3热处理 4.3.1预备热处理
进行性能热处理前,铸件可进行适当的退火热处理。 4.3.2性能热处理
铸件应进行调质热处理,推荐热处理工艺如下: a)淬火温度为1080℃~1130℃,保温时间由铸件的主壁厚确定,铸件快速冷却至300℃以下,保
证所有截面完全发生马氏体转变; b)回火温度为720℃~760℃,保温时间根据铸件的主壁厚确定,铸件在炉冷至300℃后可出炉
空冷。
4.3.3去应力热处理
铸件在粗加工,补焊及焊接后均应进行去应力热处理,去应力热处理温度应不高于铸件的回火温
度。如果粗加工后还需进行焊接,且随后进行焊后热处理,则可以省略粗加工后的去应力热处理。 4.4焊接 4.4.1供方应采用需方规定的焊接标准,规范焊接和补焊的生产过程。 4.4.2焊工应具有资格证书。供方应完成必要的焊接工艺评定,编制焊接工艺规程。 4.4.3允许对铸件中的超标缺陷进行补焊。补焊前应彻底去除不允许的缺陷,绘制补焊区示意图并记录补焊区的位置和尺寸。
5技术要求
5.1化学成分 5.1.1供方应对每炉钢液进行熔炼分析,分析结果应符合表1的规定。
表1化学成分
(质量分数,%)
P ≤0.020 Nb
c 0.10~0.15
Si ≤0.50 Ni 0.10~0.60
s ≤0.010 8.50~10.00 1.40~1.80 N
Cr
Mn ≤1.00 V 0.15~0.25 0.04~0.08 0.015~0.030 0.008~0.015
Mo
Co 0.90~1.30 5.1.2 当需方有要求时,可进行成品分析,成品化学成分允许偏差应符合表2的规定。
B
Al ≤0.02
表2月 成品化学成分的允许偏差
(质量分数,%)
c ±0.01 Co ±0.02
si +0.05 Ni ±0.03
P +0.005 Nb ±0.01
s +0.005 N ± 0.01
Cr ±0.15 B ±0.001
Mo ±0.05 Al +0.01
Mn +0.05 V ±0.03
5.2 力学性能
经最终热处理后铸件室温力学性能应符合表3的规定。
表3 室温力学性能
Rpo.2 MPa ≥490 三个试样试验结果的算术平均值不应低于规定值,其中只允许有一个试样的试验结果低于规定值,但不应低于规定值的70%
Rm MPa ≥630
A % ≥15
z % ≥35
KVaa J ≥27
5.3硬度
如果进行补焊或焊接,在焊后热处理后应对补焊或焊接区域(包括热影响区)进行硬度检验,检验结果应≤350HBW。 5.4铸件表面质量 5.4.1铸件的表面质量应符合图样规定。如果图样未做规定,则铸件的表面粗糙度Ra应达到100um。 5.4.2需做无损检测的铸件加工面的表面粗糙度Ra应达到6.3μm,非加工面的表面粗糙度Ra应达到 12.5 μm 5.4.3应彻底清除铸件表面的裂纹、粘砂、缩孔、冷隔等缺陷,若缺陷清除后壁厚超出尺寸公差的要求,则应进行补焊。 5.4.4铸件非加工面上的浇口、冒口、工艺补贴和铸筋被切除后,应进行精整打磨,使其表面与铸件本体平滑过渡。 5.4.5如果订货图样和订货技术协议中对表面清洁度未做规定,则高中压汽缸内缸、阀壳的内壁应符合JB/T4058—2017中洁-2的要求。 5.5无损检测
可后可采用渗透检测代替。 5.5.3铸件最终去应力处理后,应按照技术要求进行超声检测。 5.5.4需方有要求时,应进行射线照相检测。 5.5.5铸件的补焊区域应按照本体规定的质量要求进行无损检测。 5.6水压试验
如果订货技术协议中有水压试验要求,铸件在交货状态或精加工后应进行水压试验。 5.7形状与尺寸公差 5.7.1铸件的几何形状和尺寸应符合图样的规定。 5.7.2铸件非加工面的尺寸公差应符合图样的规定,如果图样未做明确规定,铸件非加工面的尺寸公差应符合GB/T6414—2017中等级DCTG13的规定。 5.7.3铸件的壁厚公差应符合图样的规定,如果图样未做明确规定,铸件的壁厚公差应符合 GB/T6414一2017中等级DCTG14的规定,且上极限偏差为公差值的60%,下极限偏差为公差值的40%, 5.7.4铸件粗加工面的尺寸公差应符合图样的规定,如果图样未做明确规定,应符合表4的规定。
表4铸件粗加工尺寸充许的极限偏差
单位为毫米
允许的极限偏差
尺寸范围 ≤125 125~600 >600
±0.50 ±0.75 ±1.50
累计尺寸公差总和应不超过总的尺寸公差。
5.7.5铸件的错型值不应超过壁厚的尺寸公差,错型处修整后应平滑过渡。 5.8重量公差
铸件的重量公差应符合GB/T11351的规定。除订货合同中有要求外,铸件的重量偏差不作考核。 5.9工艺评审试验要求
当需方有要求或铸件首件生产或制造工艺发生重大变化时,可增加以下技术要求: a)金相组织:铸件经最终热处理后进行金相检验,显微组织、铁素体和晶粒度应满足需方的
要求; b)高温拉伸性能:铸件经最终热处理后进行高温拉伸试验:试验温度和考核指标由供需双方商定;心)高温持久性能:铸件经最终热处理后进行高温持久试验,试验温度、试验应力和考核指标由供
需双方商定。
6检验规则和试验方法
6.1化学成分分析 6.1.1化学成分分析取样和制样应按照GB/T20066和GB/T5678的规定执行。化学成分分析应按照
重分析结果为准。 6.1.3成品分析用试样应在附铸试块或铸件距离表面6mm以下处取样。 6.2力学性能试验 6.2.1力学性能试样应取自附铸试块,附铸试块的尺寸、数量、位置由供需双方商定。如果铸件受重量、几何结构和壁厚等因素的限制无法附铸试块时,经需方同意,可采用同炉浇注的单铸试块 6.2.2附铸试块应在全部热处理结束后方可取下。试块可在热处理前先切割出适当的缝隙,但不允许完全割断,应保留少许金属与本体连接,以便不采用热割方法就能取下。若采用单铸试块,应随铸件进行全部热处理。 6.2.3经需方同意,因特殊情况需提前取下的附铸试块,应放置到铸件原位置附近进行全部后续热处理。 6.2.4一般每个铸件取1块附铸试块进行试验。 6.2.5拉伸试验应按照GB/T228.1的规定执行,应采用直径为10mm的圆形横截面比例试样。冲击试验应按照GB/T229的规定执行,采用V型缺口标准试样。每个试块取1个拉伸和3个(1组)冲击试样进行试验。 6.2.6如果发现试样有加工缺陷或铸造缺陷,可重新补充试样进行试验。 6.2.7硬度试验应按照GB/T231.1的规定执行。补焊区域应分散抽5处进行硬度试验,若补焊区域少于5处应全部进行硬度试验。铸件所有的结构焊缝都应进行硬度试验。 6.3无损检测 6.3.1 铸件在无损检测之前应按照规定做好表面准备。 6.3.2磁粉检测应按照JB/T9630.1的规定执行,也可由供需双方另行商定。 6.3.3渗透检测应按照GB/T9443的规定执行,也可由供需双方另行商定。 6.3.4超声检测应按照JB/T9630.2的规定执行,也可由供需双方另行商定。 6.3.5射线照相检测应按照GB/T5677的规定执行,也可由供需双方另行商定。 6.4水压试验
铸件的水压试验应按照JB/T9629的规定执行,也可由供需双方另行商定。 6.5工艺评审试验 6.5.1如果需要,铸件材料性能评审试验应从附铸试块上取样进行。 6.5.2显微组织、铁素体和晶粒度检验分别按照GB/T13298、YB/T4402和GB/T6394的规定执行。 6.5.3高温拉伸试验按照GB/T228.2的规定执行。 6.5.4高温持久试验按照GB/T2039的规定执行。 6.6复试和重新热处理 6.6.1当力学性能试验结果不合格时,允许从该附铸试块或铸件的其他附铸试块上取样进行复试。 6.6.2拉伸试验取双倍试样进行复试,如果复试结果均符合表3的规定,判定为合格。否则,相应铸件连同试块应重新进行热处理或由供需双方协商处理。 6.6.3冲击试验取3个试样进行复试,如果初试与复试的6个试样的平均值及复试的3个试样的单个值均符合表3的规定,判定为合格。否则,相应铸件连同试块应重新进行热处理或由供需双方协商处理。