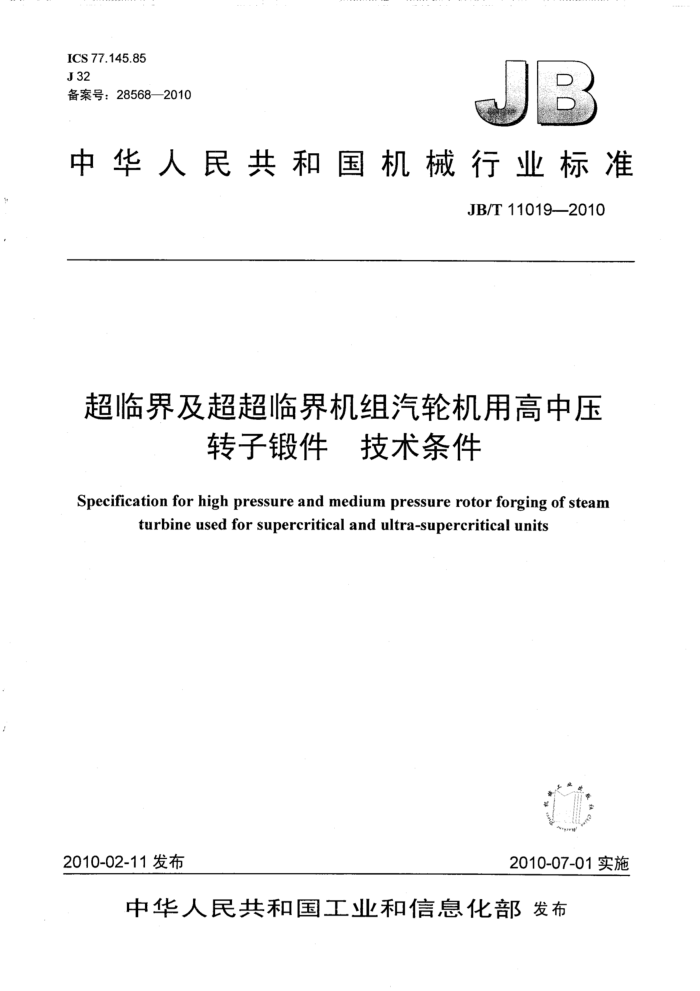
JB/T11019-—2010
目 次
II
前言范围
1 2 3 X
规范性引用文件订货要求制造工艺 4.1 冶炼和铸锭 4.2 锻造. 4.3 热处理. 4.4 机械加工 4.5 焊接 5技术要求 5.1 化学成分 5.2 力学性能, 5.3 硬度 5.4 无损检测 5.5 金相组织 5.6 残余应. 5.7 热稳定性 5.8 尺寸公差和表面粗糙度 6 检验规则和试验方法 6.1 化学成分分析 6.2 力学性能试验 6.3 硬度试验 6.4 无损检测, 6.5 金相检验.. 6.6 残余应力检验, 6.7 热稳定性试验. 6.8 复试, 6.9 重新热处理 7 验收及质量证明书 7.1 验收. 7.2 质量证明书. 8标志和包装发运表1化学成分表2化学成分的允许偏差。 表3气体含量,表 4力学性能表5高温持久强度
.........
中.h.E.E.s.....R中Pt-E
.E-E
EEE
.i..-.-.F......
I
JB/T11019--2010
前: 言
本标准由中国机械工业联合会提出。 本标准由机械工业大型铸锻件标准化技术委员会归口。 本标准起草单位:中国第二重型机械集团公司。 本标准主要起草人:龚惠昌、王月乔、游卫。 本标准为首次发布。
JB/T11019-2010
超临界及超超临界机组汽轮机用高中压转子锻件:技术条件
范围
本标准规定了超临界及超超临界汽轮机组用不锈钢型高中压转子锻件的订货要求、制造工艺、技术要求、检验规则和试验方法、验收及质量证明书等。
本标准适用于超临界及超超临界汽轮机组用不锈钢型高中压转子锻件的订货、制造与检验等。 2规范性引用文件
下列文件中的条款通过本标准的引用而成为本标准的条款。凡是注日期的引用文件,其随后所有的修改单(不包括勘误的内容)或修订版均不适用于本标准,然而,鼓励根据本标准达成协议的各方研究是否可使用这些文件的最新版本。凡是不注日期的引用文件,其最新版本适用于本标准。
GB/T223(所有部分)钢铁及合金化学分析方法 GB/T228 金属材料室温拉伸试验方法(GB/T228--2002,eqvISO6892:1998) GB/T2293 金属材料夏比摆锤冲击试验方法(GB/T229—2007,ISO148-1:2006,MOD) GB/T 231.1金 金属材料布氏硬度试验第1部分:试验方法(GB/T231.1-2009,ISO6506-1:
2005,MOD)
GB/T 2039 金属拉伸蠕变及持久试验方法(GB/T20391997,eqvISO204:1997) GB/T 6394 4金属平均晶粒度测定方法(GB/T6394—2002,ASTME112:1996,MOD) JB/T 8468 锻钢件磁粉检验方法 JB/T8888环芯法测量汽轮机、汽轮发电机转子锻件残余应力的试验方法 JB/T9021汽轮机主轴和转子锻件的热稳定性试验方法 ASTMA370钢制品的力学性能试验方法和定义 ASTME292—2001材料断裂时间的凹口张力试验的标准试验方法
3订货要求 3.1供方应有完善的质量保证体系,原则上应具有生产过类似材料、相近尺寸的转子锻件的业绩。 3.2对于制造的首件产品要有质量评定,评定项目应由供需双方协商决定。 3.3需方应在订货合同或技术协议中写明采用的标准、材料牌号、锻件强度级别、供需双方明确的相应技术要求和检验项目及本标准要求以外的检验项目。 3.4需方应提供包括力学性能试验取样位置的锻件订货图样和转子精加工图样。 3.5需方应在订货合同中注明要求参加现场检验或联合检验的项目。 4制造工艺 4.1冶炼和铸锭 4.1.1锻件用钢应采用电炉冶炼和钢包精炼工艺,也可采用真空碳脱氧工艺或电渣重熔。经需方同意,允许采用保证质量的其他冶治炼方法。 4.1.2锻件用钢锭应采用下注法浇注或真空浇注,也可采用电渣重熔钢锭。如采用下注钢锭,则钢水应至少进行一次真空除气。真空系统必须有足够的能力,保证在开浇后2min之内将真空室的压强降至较低值。 4.1.3当锻件采用电渣重熔钢锭制造时,电渣重熔所使用的电极应由经过真空处理的钢制造。
JB/T110192010
4.1.4当锻件采用非电渣重溶钢锭制造时,则应采用高径比合适的短粗锭型,以将偏析控制在允许的范围以内。 4.2:锻造 4.2.1锻件用钢锭的头部和底部应有足够的切除量,以确保成品锻件无缩孔、疏松、严重的偏析及其他有害缺陷。 4.2.2锻件应在具有足够能力的锻压机上锻造,以使锻件整个截面充分地锻透并得到均匀致密的内部组织。 4.2.3应尽可能保持锻件轴线与钢锭中心线重合。除非订货协议另有规定,钢锭质量较好的一端应为靠近发电机端。 4.2.4'锻件应采用粗十拔长工艺锻造。锻件的轴身总锻比不得小于3.0。对于采用电渣重熔锭或者采用其他特殊锻造方法时,锻造主变形方式可以由供需双方另行确定。 4.3热处理 4.3.1锻后热处理
在锻件完成锻造成形后,应进行锻后热处理。根据锻件材料的不同,锻后热处理应选择等温退火或者正火十回火工艺。当采用正火十回火工艺时,应至少进行一次正火和两次回火,其中第二次回火温度应比第一次回火温度高15℃~60℃。 4.3.2性能热处理
锻件应在垂直状态下进行性能热处理,锻件的性能热处理为淬火十回火处理。 淬火处理应先将锻件均匀加热到淬火温度并经足够长时间的保温,使其组织充分奥氏体化后再采
用喷雾或油冷火。
锻件在淬火处理后应进行二次回火处理,第一次回火处理温度为550℃~590℃,第二次回火处理温度大于等于650℃。在保证力学性能要求的前提下应尽可能提高第二次回火温度;但第二次回火温度不应超过钢的下临界点温度。锻件回火应炉冷到250℃以下后空冷。 4.3.3去除应力处理
锻件应在轴颈表面堆焊后、热稳定性试验前进行去除应力处理。锻件的去除应力处理应在垂直状态下进行,去除应力处理温度应低于性能热处理的第二次回火温度15℃~30°℃。 4.4机械加工 4.4.1在性能热处理前,应对锻件进行第一次粗加工。 4.4.2在性能热处理后、超声检测之前,应对锻件进行第二次粗加工。 4.4.3 锻件应在超声检测合格之后进行第三次粗加工。 4.4.44 锻件在各项性能和无损检测合格后,应按照需方订货图样规定的尺寸和公差要求进行最后加 H: 4.5焊接
转子锻件轴颈表面应按照订货图样要求,采用适宜的材料进行堆焊。堆焊应采用埋弧焊方法。堆焊后应对锻件轴颈表面进行加工。 5技术要求 5.1化学成分 5.1.1供方应对每炉(每包)钢水进行熔炼分析,分析结果应符合表1规定。在检验报告中应提供微量元素Cu、·As、Sb和Sn的含量。多炉合浇时还应报告权重分析结果。 5.1.2:供方应对每个锻件进行成品分析,分析结果应符合表1规定,但允许有表2的偏差。 5.1.3每个锻件均应分析气体含量,分析结果应符合表3的规定。电渣重熔锭制造的锻件气体含量应由双方协商确定。
2
JB/T11019—2010
表1 化学成分(质量分数)
(%)
Mn Si P S Cr Ni Mo V W Nb N Al
材料牌号 12Cr10NiMoWVNbN
C 0.11~ 0.40
M M 10.20- 0.70~ 1.00~ 0.15~ 0.95~ 0.04~ 10.040~ M
4
+
0.13 0.50 0.12 0.012[ 0.008 10.60 0.80 1.10 0.25 1.05 0.07 0.060 0.010 0.10~ N M ≤ ≤ 10.00~ ≤ 1.30- 0.12~
0.03~ 0.03~ ≤ 0.08 .0.07 0.010
13Cr10NiMoVNbN
0.16 1.00 0.10 0.015 0.015 11.00 1.00 1.60 0.22
M ≤ 9.50~ 0.60~ 0.90~ 0.15~ 0.80~ 0.03~ 0.04~ Λ
0.12~ 0.40~ 0.16 0.70 0.10 0.015 0.010 11.50 1.00 1.20 0.25 1.20 0.12. 0.08 0.010 0.13~ 10.40~ t ≤ N 10.00~ 0.40~ 1.15~ 0.15~ 0.25~ 0.04~ 0.03~ 0.16 0.70 0.07 0.015 0.010 11.00 0.70 1.35 0.20 0.40 0.07 0.07 0.010
14Cr10NiMoWVNbN
15Cr10NiMoWVNbN
表2 化学成分 (质量分数) 的允许偏差
(%) Nb
N
Ni Mo
W
Cr
V
Mn
Si
P
S
C
±0.02 +0.04 +0.02 +0.005 +0.005 ±0.05 ±0.06 ±0.02 ±0.01 +0.05 +0.005 +0.005
表3 气体含量(体积分数)
(%)
H2 ≤2.0×10-4 ≤2.0×10-4 ≤1.5×10-4
02 ≤75×10-4 ≤75×10-4 ≤35×10-4
材料牌号 12 Cr10NiMoWVNbN 13Cr10NiMoVNbN 14Cr10NiMoWVNbN 15Cr10NiMoWVNbN
5.2力学性能 5.2.1锻件的力学性能应符合表4的规定。锻件本体径向的屈服强度和抗拉强度的最大与最小值之差应不大于40MPa。
表4力学性能
项目 取样位置 12Cr10NiMoWVNbN13Cr10NiMoVNbNa14Cr10NiMoWVNbN 15Cr10NiMoWVNbN
≥655 (Rpo.02) ≥655 (Rp0.02)
≥685 (Rp0.02)
轴端纵向
Rpo.2 本体径向
≥670(所有)
≥685
≥700 ≥700
MPa Rm MPa A (%) 本体径向 z
芯棒纵向轴端纵向本体径向轴端纵向
≥830 ≥830 ≥17 ≥15 ≥40 ≥35 ≥14
≥880 ≥880 ≥17 ≥15 ≥40 ≥35 ≥20
≥830(所有)
≤1000
≥16(所有)
≥13
轴端纵向
≥45(所有) ≥20(所有)
≥35 ≥30 ≥30 结果供参考结果供参考
(%) 本体径向 Akv 本体径向
芯棒径向
J
FATTs0 本体径向 ℃
≤80
≤80
≤80(所有)
芯棒径向本体径向
上平台能
≥81
T
a该材料试样未规定取样位置和方向。
3
JB/T11019—2010
5.2.2锻件应进行高温持久强度试验,首件产品高温持久强度试验结果应达到表5的要求,正常生产时的高温持久强度试验条件应从表5中选择,原则上每件产品选择一种温度和载荷进行试验,并应达到表5中相应的要求。
表5高温持久强度
试验温度 应力 ℃
试验要求
材料牌号
MPa 230 断裂时间≥500h1)试样位置为中心孔径向 264 断裂时间≥100h 12)断口不得在V型缺口上 363 1)断裂时间≥100h 314 2》首件产品试验采用ASTME292:2001中的联合持久试样,试
600 600 538 566 593 521
12Cr10NiMo WVNbN
13Cr10NiMoVNbN
样位置为本体径向
265 206 3)断口不得在V型缺口上
1)断裂时间≥100h
14Cr11Mo WNiVNbN
≥216 2)试样位置为本体径向
630
3)断口不得在V型缺口上 1)断裂时间≥100h 2)试样位置为本体径向 3)断口不得在V型缺口上
575 600 625 650
308 264 215 171
15Cr10NiMoWVNbN
5.3硬度
在性能热处理后应按交货图样指定的位置检查锻件硬度的均匀性。在圆周方向四等分点进行硬度分布检查,在同一圆周上各点间的硬度差应不超过30HBW,在同一母线上的硬度差应不超过40HBW。 硬度的绝对值供参考。 5.4无损检测 5.4.1一般要求
锻件应无裂纹、白点、缩孔、折叠、过度的偏析以及超过规定的夹杂和疏松, 5.4.2磁粉检测
在锻件的外圆表面完成精加工以后,应对轴承部位表面和两轴身外端面及过渡区进行磁粉检测。磁粉检测由需方进行,供方应保证检测结果符合以下要求:
a)转子锻件的外圆表面不允许有大于1.5mm的任何缺陷显示; b)同一条母线上的两个缺陷之间的距离小于其中较大缺陷长度的五倍时,按一个连续缺陷处理。
5.4.3超声检测
锻件应进行超声检测,检验方法和验收标准应满足供需双方商定的标准或技术协议的规定。 5.5金相组织 5.5.1锻件的平均晶粒度不应粗于2.0级。 5.5.2锻件的A、B、C、D四种类型的夹杂物均不应超过3.0级。 5.6残余应力
锻件应进行残余应力测定,残余应力要求应在双方商定的技术协议中另行规定。如果残余应力超过规定,锻件应进行补充去除应力处理,并且重新测定残余应力和硬度值。 5.7热稳定性
热稳定性试验结果应符合JB/T9021的规定,供方应对试验结果负责。 5.8尺寸公差和表面粗糙度
加工后的锻件应符合订货图样规定的尺寸、公差和表面粗糙度要求。
+
JB/T11019—2010
6检验规则和试验方法 6.1化学成分分析 6.1.1化学成分分析应按GB/T223规定的方法或能保证分析质量的其他方法进行。 6.1.2:可于每炉(每包)钢水浇注时取样测定钢水的化学成分。当无法进行熔炼分析时,允许用成品分析代替熔炼分析,但从锻件上取样进行分析的分析结果应符合成品分析要求。 6.1.3'成品分析试样可取自锻件本体延长部分,或取自径向试样。 6.1.4气体分析用试样应在径向试棒上切取。 6.2·力学性能试验 6.2.1拉伸试验应按GB/T228或ASTMA370规定的方法进行。 6.2.2冲击试验应按GB/T229规定的方法进行,冲击试样槽口方向应与转子的轴线平行 6.2.3.锻件轴端与本体试样的取样数量、试样位置及试验项目的选择应按需方订货图样和取样图样的规定进行。 6.2.4,高温持久强度试验应按GB/T2039的规定进行。 6.3硬度试验
硬度试验应按GB/T231.1规定的方法和订货图样的规定进行,当订货图样没有规定时,应在每个锻件的两轴颈及轴身部位的外圆表面每隔90°的位置各测一点(共12点)。 6.4无损检测 6.4.1锻件的磁粉检测应按JB/T8468的规定进行。 6.4.2锻件的超声检验规则和试验方法应按供需双方商定的标准或技术协议的规定进行。 6.5金相检验
晶粒度检验应按GB/T6394的规定进行。晶粒度检验的试样为取自轴身电机端的径向试样。 6.6残余应力检验 6.6.1:应采用切环法或环芯电阻应变法测定锻件的残余应力。 6.6.2采用切环法测定残余应力时,在轴身一端切取25mm×25mm的圆环,用测量该圆环切割前后平均变形量的方法来计算残余应力,计算公式为:
Q=ES/ D.
(1
式中: α—残余应力,单位为MPa; E—材料的弹性模量单位为MPa; 直径增量的代数值,单位为mm; D一切割前圆环的外径,单位为mm。
6.6.3采用环芯电阻应变法测定残余应力时,应在订货图样要求的部位按JB/T8888的规定进行,测量位置应符合订货图样规定。 6.7热稳定性试验
热稳定性试验应按JB/T9021规定的方法进行。 6.8复试 6.8.1如果力学性能检验中某一试验结果不合格,可在锻件上与原试样相邻部位取双倍试样进行复试。 拉伸试验的两个试样的复试结果及初试、复试三个试验结果的平均值应满足表4规定要求。冲击试验取双倍试样进行复试,所有试验结果的平均值应满足表4规定要求。 6.8.2如因白点和裂纹造成力学性能检验结果不合格者,不得复试。 6.9·重新热处理 6.9.1如果锻件力学性能复试仍不合格,且试样的强度高而塑性、韧性或FATT达不到要求时,锻件应重新进行回火,回火后应按6.2的规定进行检验。