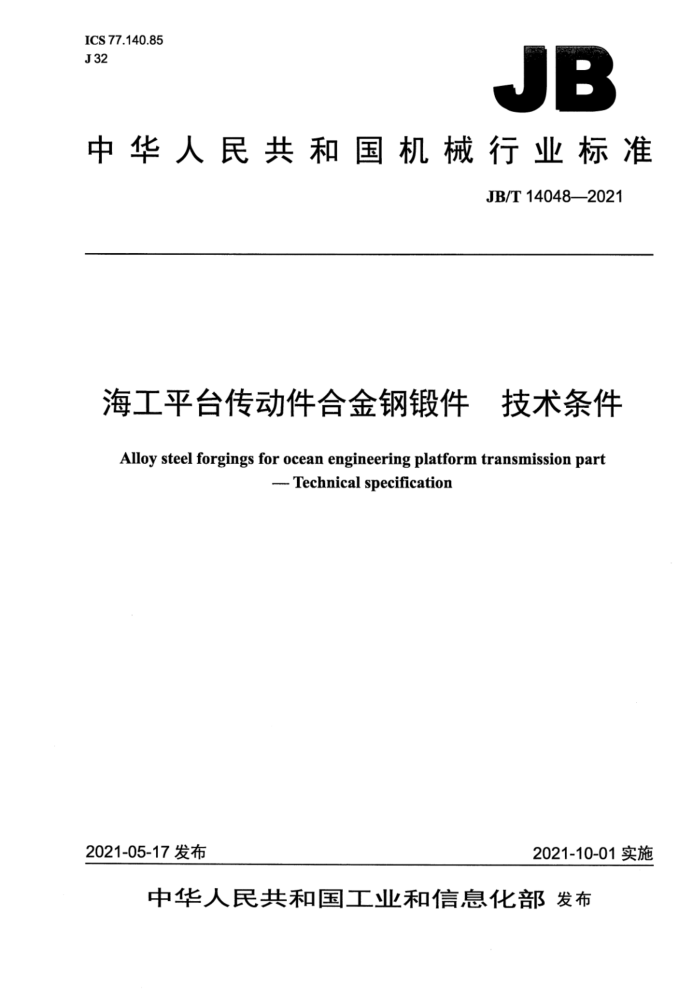
JB
中华人民共和国机械行业标准
JB/T14048—2021
海工平台传动件合金钢锻件 技术条件 Alloy steel forgings for ocean engineering platform transmission part
--- Technical specification
2021-10-01实施
2021-05-17发布
中华人民共和国
机械行业标准
海工平台传动件合金钢锻件 技术条件
JB/T14048--2021
*
机械工业出版社出版发行北京市百万庄大街22号
邮政编码:100037
*
210mm×297mm·1印张·27千字 2021年10月第1版第1次印刷
定价:18.00元
*
书号:15111·16159 网址:http://www.cmpbook.com 编辑部电话:(010)88379399 直销中心电话:(010)88379399
封面无防伪标均为盗版
目 次
前言 1范围.. 2规范性引用文件 3订货要求, 4制造工艺
I
4.1 总则. 4.2 冶炼和浇注. 4.3 锻造. 4.4 热处理 4.5 去应力处理. 4.6 机械加工 4.7 焊接.. 5技术要求 5.1 化学成分 5.2 力学性能. 5.3 硬度和硬度均匀性, 5.4 金相组织.. 5.5 无损检测 5.6 尺寸和表面粗糙度. 6检验规则和试验方法. 6.1 组批规则. 6.2 化学成分分析.. 6.3 力学性能试验. 6.4 硬度检验 6.5 金相检验.. 6.6 无损检测 6.7 表面粗糙度评定 6.8 复试. 6.9 重新热处理. 7验收和质量证明书 8标识和包装.
10
图1锻件取样位置和取样方向图2成品齿轮、齿轮轴锻件取样位置和取样方向. 图3饼形、齿轮类锻件取样位置和取样方向.. 图4齿圈锻件取样位置和取样方向
A
表1 化学成分表2 成品化学成分允许偏差表3 力学性能. 表4抗拉强度允许差值表5 硬度允许差值. 表6 锻件的低倍组织缺陷级别表7 锻件的非金属夹杂物级别
电860606电电电电电电86835电3
i8iiia BBaiiaii8iaa
tii.
E电EEEE
.5
EE.EO.
L8556E66E08585E5电8E888E881EEEEEE88E081 8185E138E5E5E868888338E9135E888808889315268E88858233 手业业业
5
前言
本标准按照GB/T1.1一2009给出的规则起草。 本标准由中国机械工业联合会提出。 本标准由全国大型铸锻件标准化技术委员会(SAC/TC506)归口。 本标准起草单位:太原重工股份有限公司。 本标准主要起草人:宋国旺、郭金玲、耿家栋、邱成国、刘炎。 本标准为首次发布。
海工平台传动件合金钢锻件技术条件
1范围
本标准规定了海工平台升降机构、锁紧机构中传动件合金钢锻件的订货要求,制造工艺、技术要求、检验规则和试验方法、验收和质量证明书、标识和包装。
本标准适用于海工平台升降机构和锁紧机构中传动件合金钢锻件(以下简称锻件)的订货、制造和检验。
2规范性引用文件
下列文件对于本文件的应用是必不可少的。凡是注日期的引用文件,仅注日期的版本适用于本文件。凡是不注日期的引用文件,其最新版本(包括所有的修改单)适用于本文件。
GB/T223(所有部分)钢铁及合金化学分析方法 GB/T228.1金属材料拉伸试验第1部分:室温试验方法 GB/T229金属材料夏比摆锤冲击试验方法 GB/T231.1金属材料布氏硬度试验第1部分:试验方法 GB/T1979 结构钢低倍组织缺陷评级图 GB/T4336 碳素钢和中低合金钢多元素含量的测定火花放电原子发射光谱法(常规法) GB/T6394 金属平均晶粒度测定方法 GB/T10561一2005钢中非金属夹杂物含量的测定标准评级图显微检验法 GB/T20066钢和铁化学成分测定用试样的取样和制样方法
3订货要求
3.1需方应在订货合同或技术协议中注明执行的船级社标准及本标准、产品名称、材料牌号、锻件强度级别、交货数量和交货状态,以及由供需双方明确的相应技术要求和检验项目。 3.2需方应提供相关船级社审核批准的订货图样。 3.3需方应在订货合同或技术协议中注明要求参加现场检验和试验的项目。
4制造工艺
4.1总则 4.1.1锻件及用于锻件的坏料,其供方应具有订货合同规定的船级社认可资质。供方在生产前应制定生产试验大纲,并提交相关船级社认可,若生产试验大纲有重大变动,应取得相关船级社和需方的同意。 4.1.2锻件供方应具有完整生产、检测、资源及质量可追溯性管理体系。
冶炼方法。所有锻件应采用镇静钢锻制。 4.3锻造 4.3.1钢锭冒口和水口均应有足够的切除量,以确保成品锻件无缩孔、疏松、严重的偏析和其他有害缺陷。 4.3.2采用的锻造方法应尽可能使整个锻件得到均匀的组织结构。锻件应在有足够压力的锻压设备上锻造成形,以使整个截面锻透。 4.3.3应尽可能保持锻件轴线与钢锭的中心线重合,对于使用中要求具有一定纤维方向的锻件,制造工艺应提交相关船级社认可。 4.3.4锻造用开坏坏料的开坏锻造比应≥2.5。 4.3.5轴类锻件采用钢锭锻造成形时,主体截面的拔长锻造比应≥4.0;采用坏料锻造时,锻造比应≥ 1.5. 4.3.6饼形锻件(如齿轮)应采用镦粗法锻制,采用钢锭锻造时,若粗前开坏的拔长锻造比<1.5,镦粗锻造比应≥4.0;若镦粗前开坏的拔长锻造比≥1.5,总锻造比应≥4.0 4.3.7环形类锻件的锻造比,当其不满足4.3.6饼形锻件锻造比的要求时,其扩孔锻造比应≥2.0,其中扩孔锻造比按扩孔前后壁厚之比计算。 4.3.8芯棒拔长的筒形锻件,当其不满足4.3.6饼形锻件锻造比的要求时,其芯棒拔长锻造比应≥2.0。 4.3.9表面缺陷,若在产品尺寸充许范围内,可用修磨方法去除,其宽度不应小于深度的3倍,边缘有足够大的过渡圆角,必要时采用磁粉或渗透检测方法确认缺陷已消除。 4.3.10供方应对每个锻造、修复过的锻件进行记录,若有检测报告,需要时一同提交相关船级社。 4.4热处理 4.4.1锻件可进行正火加回火方式或退火方式的锻后热处理。 4.4.2性能热处理要求如下:
a)锻件应采用淬火加回火、正火加回火热处理工艺,其中回火温度应不低于550℃: b)若拟采用渗碳、氮化或高频火等方法进行表面硬化,应将其工艺、规程、技术条件等资料提
交相关船级社认可。
4.4.3锻件应保留热处理炉、炉批次、热处理日期、保温温度和时间等热处理信息记录,在验船师和需方有要求时应出示记录。 4.5去应力处理 4.5.1锻件在最终热处理结束后,局部需加热、进行矫正或冷矫正时,应做去应力处理。 4.5.2锻件应在低于最终性能热处理回火温度30℃下进行去应力处理。 4.6机械加工 4.6.1在性能热处理之前,锻件的全部表面进行第一次粗加工。未经相关船级社和需方同意,不得加工影响性能热处理和超声检测的部位(如槽和台阶)。 4.6.2在各项化学成分、非金属夹杂物、力学性能、无损检测等检测合格后按需方订货图样规定的尺寸公差进行加工。 4.7焊接 4.7.1当使用焊接方法将两个以上锻件,或锻件与其他钢构件连接成一个组合部件时,应将焊接工艺