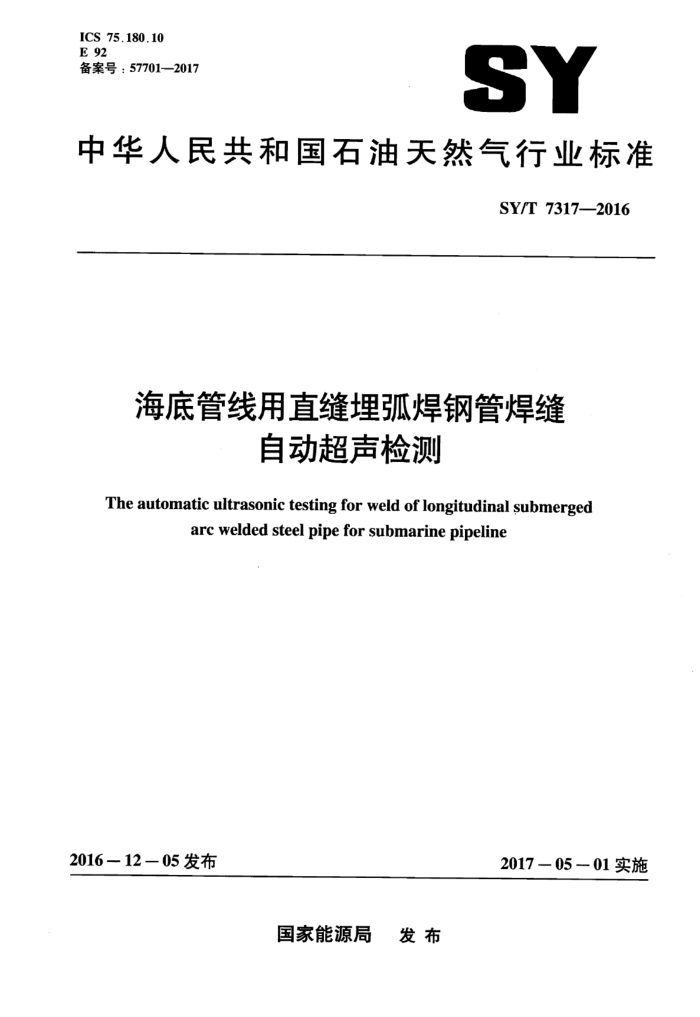
ICS 75.180.10 E 92 备案号:57701—2017
SY
中华人民共和国石油天然气行业标准
SY/T 7317—2016
海底管线用直缝埋弧焊钢管焊缝
自动超声检测
The automatic ultrasonic testing for weld of longitudinal submerged
arc welded steel pipe for submarine pipeline
2016-12-05发布
2017—05-01实施
国家能源局 发布
SY/T7317—2016
目 次
前言
II
范围 2 规范性引用文件 3 一般要求
1
自动超声检测系统、探头及试块 4.1 自动超声检测系统 4.2探头 4.3试块 5检测系统的调试 5.1调试内容 5.2检测系统分区调试 5.3 检测系统的总体调试 5.4检测系统设备测试项目及方法 6检测条件和方法
4
2
S
6
6.1 扫查灵敏度 6.2 检测灵敏度的校验 6.3 耦合监视的校验 6.4 检测速度 6.5 焊缝自动跟踪 6.6 标记 6.7 管端未检测区域 6.8 检测灵敏度复核
F
F
7 检测结果显示的评定
验收 9 检测报告和存档附录A(资料性附录) 典型探头的排列布置附录B(资料性附录) 典型对比试块的设计附录C(规范性附录) 自动超声检测系统测试与方法
11
14
SY/T73172016
前 言
本标准按照GB/T1.1-2009《标准化工作导则第1部分:标准的结构和编写》给出的规则起草。 请注意本文件的某些内容可能涉及专利。本文件的发布机构不承担识别这些专利的责任。 本标准由石油管材专业标准化技术委员会提出并归口。 本标准起草单位:中国石油集团石油管工程技术研究院、武汉中科创新技术股份有限公司、渤海
装备巨龙钢管公司、中油宝世顺(秦皇岛)钢管有限公司、湖南胜利湘钢钢管有限公司、河北沧海核装备科技股份有限公司、北京隆盛泰科石油管科技有限公司。
本标准主要起草人:黄磊、赵新伟、王子成、杨专钊、武占芳、唐彦林、聂向晖、蒋太秋、孟庆云。
II
SY/T7317—2016
海底管线用直缝理弧焊钢管焊缝自动超声检测
1范围
本标准规定了焊缝自动超声检测的超声设备、探头及试块,检测系统的调试,检测条件和方法,显示的评定,验收等级,检测报告等。
本标准适用于海底管线用直缝埋弧焊钢管焊缝自动超声检测与质量评定。 陆地管线及其他管线用直缝埋弧焊钢管焊缝自动超声检测,可参照本标准执行。
2规范性引用文件
下列文件对于本文件的应用是必不可少的。凡是注日期的引用文件,仅注日期的版本适用于本文
件。凡是不注日期的引用文件,其最新版本(包括所有的修改单)适用于本文件。
GB/T9445无损检测人员资格鉴定与认证 ISO11484钢铁产品无损检测人员的雇主资格制度[Steelproducts—Employer'squalification
systemfor non-destructive testing (NDT)personnel)
ASNTSNT-TC-1A无损检测人员资格签订和认证(Personnelqualificationandcertificationinnondestructive testing)
ASTME317超声脉冲回波检测仪器和系统工作特性的非电子测量评价标准操作规程(Standard practice for evaluating performance characteristics of ultrasonic pulse-echo testing instruments and systems without the use of electronic measurement instruments)
3一般要求
3.1被检测钢管应经外观检查合格。所有影响超声检测的锈蚀、飞溅和污物等都应予以清除,其表面粗糙度应符合检测要求。 3.2焊缝两侧声束经过区域应被证实无影响检测有效性的分层。 3.3检验场地应避开强光、强磁场、强振动、腐蚀性气体、严重粉尘等影响自动超声波检测系统稳定性或检验人员观察的因素。 3.4除非有其他产品标准规定或购方和制造商之间有协议,自动超声检测应在水压试验完成后实施。 3.5应选用适当的液体作为耦合剂,耦合剂应具有良好的透声性和适宜的流动性,对材料、人体及环境无损害,同时应便于检测后清理。典型的耦合剂为水。在试块上调节仪器和在管材检测时应采用同一种耦合剂。 3.6从事自动超声检测的人员除应按照ISO11484,ASNTSNT-TC-1A和GB/T9445的推荐作法或类似标准要求培训考核资格鉴定合格,取得相应等级资格证书后外,还应经过专门培训,熟悉设备性能,熟练操作计算机及自动超声检测系统和设备,并取得相关部门发的超声检测专业1级及以上级别资格证书。签发报告者应取得相关部门颁发的超声检测专业2级及以上级别资格证书。
SY/T7317—2016
4自动超声检测系统、探头及试块 4.1自动超声检测系统 4.1.1组成
自动超声检测系统至少应包括多通道超声检测仪、控制系统、耦合系统、焊缝自动跟踪系统、传送系统(或探头门架移动系统)、探头门架系统、信号处理系统、打印输出系统、附属装置等。 4.1.2基本要求
超声检测系统应提供足够数量的检测通道,保证扫查整条焊缝,且对整个焊缝厚度方向进行分区全面检测,焊缝区域划分应符合图1的规定。
仪器的线性应按照ASTME317确定,每6个月校准一次,垂直线性误差小于或等于满幅度的
5%,水平线性误差小于或等于满刻度的1%。闸门的位置和宽度及信号电平连续可调。
区域外焊区纯迈区二内焊区
区域外焊区内焊区
a)“I”型坡口的情况
b)“x”型坡口的情况
图1焊缝区域划分示意图
4.1.3记录系统
应采用编码器记录整条焊缝扫查的位置。编码器配置一个校正系统,保证显示记录的焊缝距离与实际外表面标记的位置一致。记录或标记系统应清楚地指示出缺欠相对于扫查起始点的位置,误差为 ±10mm。
焊缝缺欠扫查记录可用A扫描(带状图)或其他图像显示方式。焊缝的检测结果应显示在扫查记录上,并应在记录上有耦合监视显示。 4.2探头 4.2.1 探头应标出探头类型、入射角或折射角、频率及晶片尺寸,并应符合检测要求。 4.2.2探头楔件表面形状应与被检钢管表面曲率相吻合。 4.2.3探头的设计应按焊缝坡口型式及有效声束宽度设定,典型探头的排列布置参见附录A。 4.3试块 4.3.1用途
试块主要用于确定基准灵敏度、鉴定检测系统并监视系统的运行状况。 4.3.2试块制作原则 4.3.2.1试块的材料应采用规格相同、声学性能相似的管段(或钢管)制成。为保证动态校验,试块应有足够长度。试块的材料在Φ2mm平底孔灵敏度检测时,不得出现大于Φ2mm平底孔回波幅度的当量缺陷。
2
SY/T7317—2016
4.3.2.2试块制作根据检测项目的焊接工艺等要求进行,并应符合试块技术条件。 4.3.2.3根据焊缝坡口形式及壁厚来区分,每个区高度一般为6mm左右,设置一对两个人工反射体用来调节灵敏度和缺欠定位,这两个反射体对该区探头来讲,称为主反射体(邻近区反射体对该区反射体来讲,不能称为主反射体)。焊缝两侧各一个或一对探头来完成一个区的检测。 4.3.2.4人工反射体在水平方向的布置应使显示信号达到独立的程度,但邻近区反射体不得互相于扰。 4.3.2.5人工反射体的制作应符合下列要求:
a)外表面沿焊缝长度方向,位于外焊趾处表面纵向N或V型刻槽。主要用于模拟外咬边、向表
面延伸的未熔合、外焊趾裂纹,如图2a)所示。 b)在外焊区设置人工反射体,主要用于模拟坡口未熔合。其直径应为3mm的平底孔。平底孔的
中心线应垂直于坡口面,平底孔的位置应保证与相邻人工反射体声束覆盖与重叠,如图2b)所示。
c)在钝边区设置平底孔,主要用于模拟中间未焊透。其直径应为3mm的平底孔。平底孔的中心
线应垂直于钝边,平底孔的位置应保证与相邻人工反射体声束覆盖与重叠,如图2c)所示。 d)在内焊区设置人工反射体,主要用于模拟坡口未熔合。其直径应为3mm的平底孔。平底孔的
中心线应垂直于坡口面,平底孔的位置应保证与相邻人工反射体声束覆盖与重叠,如图2b)所示。
e)内表面沿焊缝长度方向,位于内焊趾处表面纵向N5或V5型刻槽。主要用于模拟内咬边、向
表面延伸的未熔合、内焊趾裂纹,如图2a)所示。 f)在焊缝中心钻一个直径为1.6mm(3.2mm)的竖通孔,如图2d)所示。直径为1.6mm的竖通
孔主要用于调节扫查灵敏度及确定闸门的终点和焊缝中心线的位置,该孔中心线应与焊缝截面中心线相重合且垂直于管壁。直径为3.2mm的竖通孔用于确定管端未检测区域长度。
g)距离焊趾为壁厚30%(最大为10mm,最小为5mm)的母材位置钻直径为3.2mm的竖通孔。
主要用于设置闸门宽度起点的位置,如图2e)所示。 h)外表面垂直于焊缝,位于外焊缝表面横向NS或V5型刻槽。主要用于调节横向缺欠检测灵敏
度,长度和焊缝宽度相同,如图2f)所示。 i)内表面垂直于焊缝,位于内焊缝表面横向N5或V5型刻槽。主要用于调节横向缺欠检测灵敏
度,长度和焊缝宽度相同,如图2f)所示。 j)内表面焊缝两侧距离焊趾12.5mm平底孔。主要用于调节焊缝两侧距离焊趾25mm范围内分层
的检测灵敏度,平底孔直径通常为6.0mm,埋藏深度为壁厚的1/2~3/4,如图2g)所示。如板边已经过超声分层检测,可不设置此类型人工反射体。
4.3.2.6除4.3.2对人工反射体的最低要求外,也可增加其他的反射体。 4.3.2.7人工反射体允许误差不应超过下列数值:
孔直径:±0.2mm;一槽宽度:±0.2mm;一槽深度:刻槽深度的±15%;角度:±1°;
-
一反射体中心位置:±0.5mm。
4.3.2.8试块上人工反射体的布置如图3所示,试块上的人工反射体数量、位置、类型应按焊缝的坡口型式设定,典型对比试块的设计示意图参见附录B。 4.3.2.9试块应经具有计量资质的机构标定,方可使用。
3
SY/T7317—2016
a)内外表面纵向刻槽
b)内外焊接区Φ3mm平底孔
c)钝边区Φ3mm平底孔
d)焊缝中心Φ1.6mm(Φ3.2mm)竖通孔
e)距焊趾一定距离处Φ3.2mm竖通孔
f)内外表面横向刻槽
g)内表面距焊趾一定距离处Φ6mm平底孔
图2试块单侧人工反射体图
17
1,13一外侧焊趾纵向刻槽;2,4,10,12—一坡口面平底孔;3,11钝边平底孔;5,9—内侧焊趾纵向刻槽, 6,8—距焊趾一定距离处竖通孔,7一中心竖通孔;14—外侧横向刻槽;15一内侧横向刻槽,16,17一内侧母材处平底孔
图3试块上人工反射体布置示意图
4
SY/T73172016
5检测系统的调试 5.1调试内容
检测系统的调试分为分区调试和总体调试。
5.2检测系统分区调试 5.2.1总则
检测系统分区调试时,应将焊缝沿厚度方向进行分区划分,每个区域用一对或一组探头检测。 5.2.2探头位置和基准灵敏度确定 5.2.2.1 在试块的模拟焊缝中心线两侧,根据反射体的位置,将探头排布在探头门架系统的扫查器中。 5.2.2.2移动扫查器,分别调整探头的位置,使每个探头对应的主反射体信号均达到峰值,即为该探头的位置。 5.2.2.3将每个探头的峰值信号调整到满幅度的80%,即为该探头的基准灵敏度。 5.2.3闸门设置 5.2.3.1 目的和方法
闻门主要用于确定该区域缺欠的位置和灵敏度,闸门设置用试块上的反射体来确定。
5.2.3.2 纵向缺欠闸门的设置
移动探头使图2e)与图2d)的波幅比约为3:1,此时闸门的起点【如图2e)所示】在其前至少2mm,闸门终点【如图2d)所示】在其后至少2mm超过焊缝中心线。设定闸门宽度后,将探头的声束对准一个主反射体,调节至反射体回波幅度最高处,移动闸门使闸门中心与反射体回波幅度最高处重合。 5.2.3.3横向缺欠闸门的设置
5.2.3.3.1对于OB探头闸门设置,先用一个探头的声束对准一个主反射体,闸门的起点【如图 2f)所示】在钢管厚度界面波后至少2mm,闸门的终点【如图2f)所示】在横向刻槽反射波后至少 2mm;该区域另一侧闸门的设置与上述相同。 5.2.3.3.2对于“K”型或“X”型探头闸门设置,先用一侧探头的声束对准一个主反射体,在该反射体声束的路径上设置一个闸门,闸门的起点如图2e)所示,闸门终点如图2e)所示的另一侧,否则,闸门终点【如图2a)所示】另一侧在其后至少2mm;该区域另一侧闸门的设置与上述相同。 5.2.3.4分层缺欠闸门的设置
对于分层缺欠探头设置,先用一侧探头的声束对准一个主反射体,在该反射体声束的路径上设置一个闸门,闸门的起点【如图2g)所示】在界面波后1mm~2mm,闸门终点【如图2g)所示】同一侧在一次底波后1mm~2mm;该区域另一侧闸门的设置与上述相同。
5.2.4闸门电平的设置
闸门电平不低于满幅度的60%,超过此幅度的信号应按第7章评定。
5