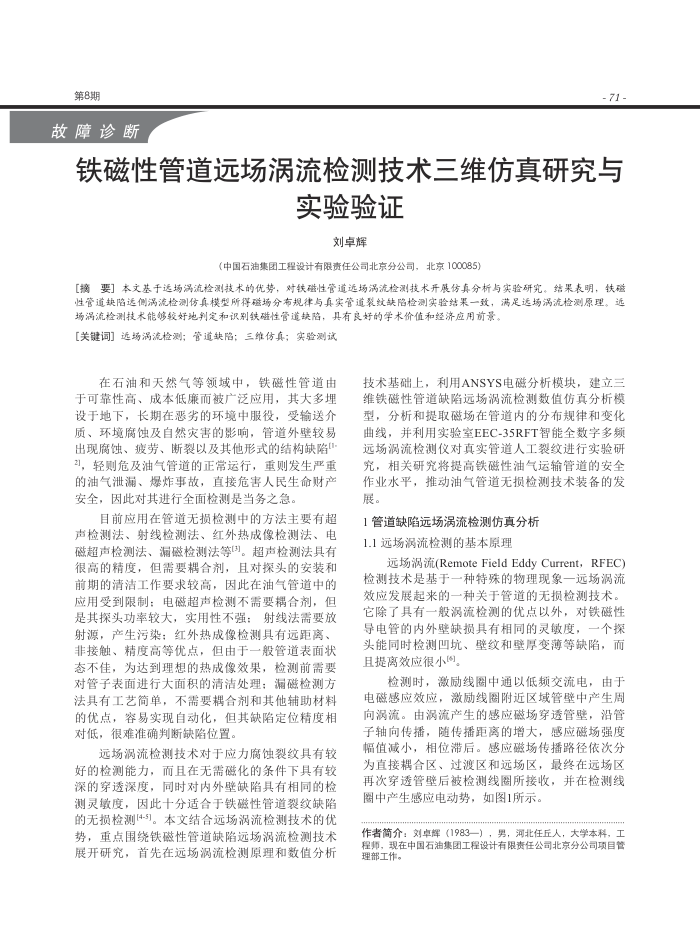
第8期
故障诊断
-71-
铁磁性管道远场涡流检测技术三维仿真研究与
实验验证
刘卓辉
(中国石油集团工程设计有限责任公司北京分公司,北京100085)
[摘要]本文基于选场涡流检测技术的优势,对铁磁性管道选场涡流检测技术开展仿真分析与实验研究。结果表明,铁础性管道缺陷送侧涡流检测仿真模型所得磁场分布规律与真实管道裂纹缺陷检测实验结果一致,满足送场涡流检测原理。远
场涡流检测技术能够较好地别定和识别继磁性管道缺陷,具有良好的学术价值和经济应用前量[关键词]选场涡流检测;管通缺陷;三维仿具;实验测试
在石油和天然气等领域中,铁磁性管道由
于可靠性高、成本低廉而被广泛应用,其大多理设于地下,长期在恶劣的环境中服役,受输送介质、环境腐蚀及自然灾害的影响,管道外壁较易出现腐蚀、疲劳、断裂以及其他形式的结构缺陷[ 2),轻则危及油气管道的正常运行,重则发生严重的油气泄漏、爆炸事故,直接危害人民生命财产安全,因此对其进行全面检测是当务之急。
目前应用在管道无损检测中的方法主要有超声检测法、射线检测法、红外热成像检测法、电磁超声检测法、漏磁检测法等3]。超声检测法具有很高的精度,但需要耦合剂,且对探头的安装和前期的清清工作要求较高,因此在油气管道中的应用受到限制:电磁超声检测不需要耦合剂,但是其探头功率较大,实用性不强:射线法需要放射源,产生污染:红外热成像检测具有远距离、非接触、精度高等优点,但由于一般管道表面状态不佳,为达到理想的热成像效果,检测前需要对管子表面进行大面积的清洁处理:漏磁检测方法具有工艺简单,不需要耦合剂和其他辅助材料的优点,容易实现自动化,但其缺陷定位精度相对低,很难准确判断缺陷位置。
远场涡流检测技术对于应力腐蚀裂纹具有较好的检测能力,而且在无需磁化的条件下具有较深的穿透深度,同时对内外壁缺陷具有相同的检测灵致度,因此十分适合于铁磁性管道裂纹缺陷的无损检测[4-5]。本文结合远场涡流检测技术的优势,重点围绕铁磁性管道缺陷远场涡流检测技术展开研究,首先在远场涡流检测原理和数值分析
技术基础上,利用ANSYS电磁分析模块,建立三维铁磁性管道缺陷远场涡流检测数值仿真分析模型,分析和提取磁场在管道内的分布规律和变化曲线,并利用实验室EEC-35RFT智能全数字多频远场涡流检测仪对真实管道人工裂纹进行实验研究,相关研究将提高铁磁性油气运输管道的安全作业水平,推动油气管道无损检测技术装备的发展。
1管道缺陷远场涡流检测仿真分析 1.1远场涡流检测的基本原理
远场涡流(Remote Field Eddy Current,RFEC) 检测技术是基于一种特殊的物理现象一远场涡流效应发展起来的一种关于管道的无损检测技术。它除了具有一般涡流检测的优点以外,对铁磁性导电管的内外壁缺损具有相同的灵敏度,一个探头能同时检测凹坑、壁纹和厚变薄等缺陷,面且提离效应很小9]。
检测时,激励线圈中通以低频交流电,由于
电磁感应效应,激励线圈附近区域管壁中产生周向涡流。由涡流产生的感应磁场穿透管壁,沿管子轴向传插播,随传插播距离的增大,感应磁场强度幅值减小,相位带后。感应磁场传播路径依次分为直接耦合区、过渡区和远场区,最终在远场区再次穿透管壁后被检测线圈所接收,并在检测线图中产生感应电动势,如图1所示。
作者简介:刘卓辉(1983一),男,河北任丘人,大学本科,工程师,现在中国石油集团工程设计有限责任公司北京分公司项目管理部工作。