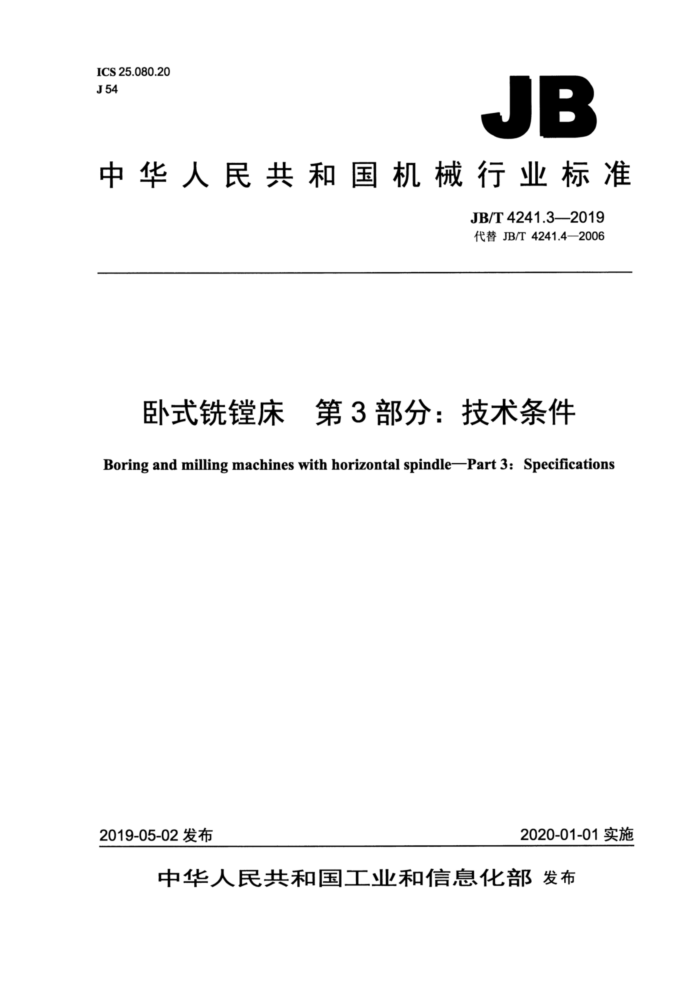
ICS 25.080.20 J 54
JB
中华人民共和国机械行业标准
JB/T4241.3—2019 代替 JB/T 4241.4—2006
卧式铣镗床 第3部分:技术条件 Boring and milling machines with horizontal spindlePart 3: Specifications
2020-01-01实施
2019-05-02发布
中华人民共和国工业和信息化部发布
JB/T 4241.3—2019
目 次
.II
前言... 1 范围. 2规范性引用文件 3一般要求..…. 4附件和工具. 5安全卫生. 6加工和装配质量 7空运转试验 7.1温升试验及主运动和进给运动检验.. 7.2普通机床功能试验, 7.3数控机床功能试验 7.4数控机床的连续空运转试验, 8负荷试验. 8.1 试验项目 8.2承载工件最大重量的运转试验. 8.3主传动系统最大扭矩试验. 8.4最大切削进给抗力试验 8.5主传动系统最大功率试验 9数控机床的最小设定单位试验.…. 9.1线性轴线最小设定单位试验. 9.2回转轴线最小设定单位试验. 10数控机床的原点返回试验. 10.1线性轴线原点返回试验 10.2回转轴线原点返回试验.. 11精度检验.. 12包装和随机文件参考文献,
C
6
6
6
8
8 8
8
8
8
9
10
欢电光光电临
12 .13 13 14
图1 主轴位移量检验图. 图 2 线性轴线最小设定单位试验方法示意图图3回转轴线最小设定单位试验方法示意图图4线性轴线原点返回试验方法示意图图 5 回转轴线原点返回试验方法示意图.
9
10 11 12
表1 附件和工具表 2 噪声... 表3手轮、手柄操作力.. 表 4塞尺插入深度.
t00000e000000000e00e00000.
2
2
4
1
JB/T 4241.3—2019
表 5 接触点数 .......... 表6接触指标.. 表7导轨导向面错位量.. 表8手轮、手柄的反向空程量. 表反向间隙..表10主轴位移量... 表11杂质、污物含量. 表 12 轴承温度和温升.
..
·
.
88..0..0............. c....
.
.....
5
l.0.00.0060c5.000c.0cc. ........
I
JB/T 4241.3—2019
前 言
JB/T4241《卧式铣镗床》分为三个部分:
第1部分:型式与参数;第2部分:主轴端部;第3部分:技术条件。
本部分为JB/T4241的第3部分。 本部分按照GB/T1.1一2009给出的规则起草。 本部分代替JB/T4241.4一2006《卧式铣镗床第4部分:技术条件》,与JB/T4241.4一2006相比
主要技术变化如下:
修改了“范围”(见第1章,JB/T4241.4一2006的第1章);修改了“规范性引用文件”(见第2章,JB/T4241.4一2006的第2章);增加了“特别重要固定结合面”的内容[见6.5f)];增加了重要固定结合面和特别重要固定结合面的具体要求(见6.6);增加了滑动导轨和移置导轨的具体要求(见6.9);增加了刮研面检验的具体要求(见6.11~6.14);修改了线性轴线最小设定单位试验方法示意图(见图2,JB/T4241.4一2006的图4);修改了回转轴线最小设定单位试验方法示意图(见图3,JB/T4241.4一2006的图5);修改了线性轴线原点返回试验方法示意图(见图4,JB/T4241.4一2006的图6);修改了回转轴线原点返回试验方法示意图(见图5,JB/T4241.4一2006的图7); -取消了“机床噪声测量布点图(见JB/T4241.4一2006的图1);取消了“制造厂的保证”(见JB/T4241.4一2006的第6章)。
本部分由中国机械工业联合会提出。 本部分由全国金属切削机床标准化技术委员会(SAC/TC22)归口。 本部分起草单位:沈阳机床(集团)有限责任公司、国家机床质量监督检验中心、沈机集团昆明机
床股份有限公司、机械工业机床产品质量检测中心(昆明)。
本部分主要起草人:李军、郭静、张维、陈妍言、施庆华、何春树、韩玉稳。 本部分所代替标准的历次版本发布情况为:
-JBn 4241-1986、JB/T 4241-1993; -JB/T 4241.42006。
II
JB/T 4241.3—2019
卧式铣镗床第3部分:技术条件
1范围
JB/T4241的本部分规定了卧式铣镗床设计、制造和验收的要求。 本部分适用于普通和数控卧式铣镗床(以下简称机床)。
2规范性引用文件
下列文件对于本文件的应用是必不可少的。凡是注日期的引用文件,仅注日期的版本适用于本文件。 凡是不注日期的引用文件,其最新版本(包括所有的修改单)适用于本文件。
GB/T 5226.1—2019 机械电气安全机械电气设备第1部分:通用技术条件 GB/T 5289.1-—2008 卧式铣镗床精度检验条件第1部分:固定立柱和移动式工作台机床 GB/T 9061—2006 金属切削机床通用技术条件 GB 15760—2004 金属切削机床安全防护通用技术条件 GB/T17421.5一2015机床检验通则第5部分:噪声发射的确定 GB/T 23570—2009 金属切削机床焊接件通用技术条件 GB/T 23572—2009 金属切削机床 液压系统通用技术条件 GB/T25373-2010 金属切削机床 装配通用技术条件 GB/T 25374—2010 金属切削机床 清洁度的测量方法 GB/T 25375—2010 金属切削机床 结合面涂色法检验及评定 GB/T 25376—2010 金属切削机床 机械加工件通用技术条件
3一般要求
按本部分验收机床时,应同时对GB/T9061—2006、GB/T25373-2010、GB/T25376—2010中未经本部分具体化的其余有关的验收项目进行检验。
4附件和工具
4.1为保证机床的基本性能,应随机供应表1所列附件和工具。
表1 附件和工具
数量 1件 1套 1套 1套 1套
备注普通机床普通机床普通机床
名称短变径套退刀楔专用扳手机床调整垫铁地脚螺栓
1
JB/T 4241.3—2019
4.2扩大机床使用性能的特殊附件,根据用户的要求按技术协议供应。
5安全卫生
5.1本部分中未规定的安全防护要求,还应符合GB15760一2004的规定。 5.2主轴箱、镗轴、平旋盘滑块、工作台及工作台滑座或上、下滑座等部件,凡不允许同时动作的,其控制机构应互锁。 5.3各直线坐标运动部件的极限位置应设限位装置。 5.4普通机床的手柄和带手柄的手轮在机动进给时不应旋转。 5.5具有自动卸刀装置的机床,应在主运动停止后刀具才能松开。 5.6普通机床镗轴的制动应灵敏、可靠,在最高转速下按停止按钮至镗轴停止转动的延迟时间不应超过 5 s。 5.7机床各移动部件进给与快速移动不应同时进行。 5.8 普通机床进给机构的保险装置应灵敏、可靠。 5.9机床导轨应采取措施,防止锈蚀与研伤。 5.10 数控机床的滚珠丝杠应设防护装置。 5.11机床工作区应采取安全措施,防止切屑、冷却液飞溅或采用信息方式提示用户。 5.12 机床液压系统的安全防护应符合GB/T23572一2009的规定。 5.13 机床电气系统的安全应符合GB/T5226.1一2019的规定。 5.14按GB/T17421.5一2015的规定测量整机的噪声,机床在空运转条件下噪声声压级:数控机床不应超83dB(A);普通机床不应超过本部分表2的规定。
表2 噪声
机床质量
>10
≤10
t 噪声声压级 dB (A)
83
85
5.15普通机床手轮、手柄操作力宜按表3考核。
表3手轮、手柄操作力
操作力 N
镗轴直径
镗轴移动 主轴箱升降 工作台横向移动 工作台纵向移动 平旋盘滑块移动 后立柱纵向移动
mm
手柄 120
手柄 120
手柄 100 120 160
手柄 80
手柄 100 120 140 160
手柄 120
70 90 110 130
120
160
160
160
6加工和装配质量
6.1下列铸件(焊接件)为重要铸件(焊接件),应在粗加工后进行时效处理或采取其他消除内应力的措施,必要时在半精加工后再进行一次时效处理: 2
JB/T 4241.3—2019
a)床身; b)立柱; c)主轴箱; d)工作台; e)工作台滑座或上、下滑座; f)滑枕。
6.2床身导轨、立柱导轨、工作台滑座导轨或下滑座上导轨为重要导轨,应采取与寿命相适应的耐磨措施。 6.3下列导轨副不宜焊补(贴塑导轨和镶钢导轨基面除外):
a)主轴箱与立柱导轨副; b)工作台滑座与床身导轨副或下滑座与床身导轨副; c)工作台滑座与工作台导轨副或上滑座与下滑座导轨副; d)工作台与上滑座环形导轨副; e)平旋盘与滑块导轨副。
6.4下列结合面应按“重要固定结合面”的要求考核:
a)立柱与床身的结合面; b)后立柱与后立柱滑座的结合面; c)纵横床身的结合面; d)各压板与主体的结合面; e)尾筒与主轴箱的结合面。
6.5下列结合面应按“特别重要固定结合面”的要求考核:
a)平旋盘支承套与主轴箱的结合处; b)滚珠丝杠托架与主体的结合面; c)滚珠丝杠螺母座与主体的结合面; d)端齿盘与主体的结合面; e)镶钢导轨与主体的结合面; f)直线导轨与安装基面的结合面。
6.6重要固定结合面和特别重要固定结合面应紧密贴合,要求如下:
a)重要固定结合面在紧固后用0.04mm塞尺检验时塞尺不应插入。 b)特别重要固定结合面除按GB/T25375一2010做涂色法检验外,紧固前、后用0.03mm塞尺检
验时塞尺均不应插入。 c)与水平面垂直的特别重要固定结合面可只在紧固后检验。 d)用塞尺检验时,允许局部(1处或2处)插入深度小于结合面宽度的1/5,但不大于5mm;若
插入部位的长度小于或等于结合面长度的1/5,但不大于100mm,则按1处计。
6.7下列导轨副应按“滑动导轨”的要求考核:
a)主轴箱与立柱导轨副; b)工作台滑座或下滑座与床身导轨副; c)工作台滑座与工作台导轨副; d)上滑座与下滑座导轨副; e)滑枕与主轴箱导轨副; f)平旋盘与滑块导轨副; g)数控机床工作台与上滑座环形导轨副。
6.8下列导轨副应按“移置导轨”的要求考核:
a)后立柱滑座与床身导轨副;
3
JB/T4241.3-2019
b)后立柱支架与后立柱导轨副; c)普通机床工作台与工作台滑座环形导轨副。
6.9滑动、移置导轨表面除按GB/T25375一2010做涂色法检验外,还应用0.04mm塞尺检验,塞尺在导轨、镶条、压板端部的滑动面间插入深度不应超过表4的规定。
表4塞尺插入深度
机床质量
≤10
>10
t
塞尺插入深度
20
25
mm
6.10直线导轨安装的基面应符合设计文件的规定。组装后运动应轻便、灵活,无阻滞现象。 6.11两配合件的结合面均为刮研面,用配合件的结合面做涂色法检验时,刮研点应均应。在每 25mm×25mm的面积内,接触点数不应少于表5的规定。
表5接触点数
滑动导轨每条导轨宽度
镶条、压板滑动面
重要固定结合面
mm
≤250
>250 接触点数 8
10
6
6
6.12两配合件的结合面一个是刮研面,另一个是机械加工面,用配合件的机械加工面检验刮研面的接触点数时,接触点数不应少于表5规定点数的75%。 6.13采用机械加工方法加工的两配合件的结合面做涂色法检验时,接触应均匀,接触指标不应低于表 6 的规定。
表6接触指标
滑(滚)动导轨
特别重要固定结合面
接触指标%
全长上 75
全宽上 60
全长上 65
全宽上 40
6.14多段拼接的镶钢导轨、床身导轨接合处宜留有0.020mm~0.040mm的缝隙,接合处导轨导向面的错位量不应大于表7的规定。
表7导轨导向面错位量
机床质量
≤10
>10
t
导轨导向面错位量
0.003
0.005
mm
6.15焊接件应符合GB/T23570—2009的规定。
X