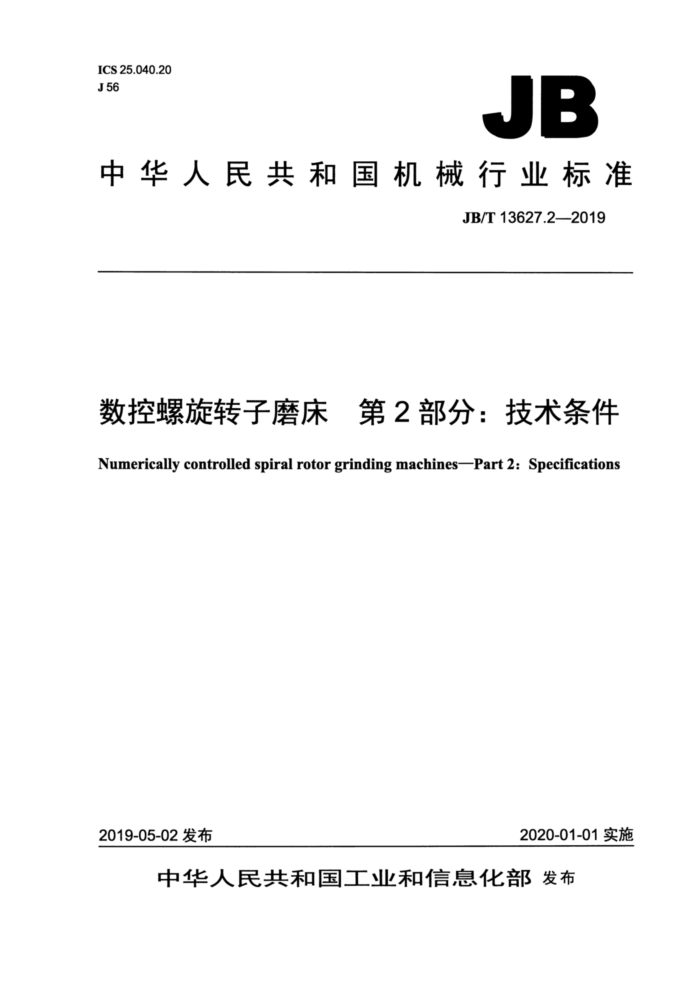
ICS 25.040.20 J 56
JB
中华人民共和国机械行业标准
JB/T 13627.2—2019
数控螺旋转子磨床第2部分:技术条件
Numerically controlled spiral rotor grinding machinesPart 2: Specifications
2020-01-01实施
2019-05-02发布
中华人民共和国工业和信息化部发布
JB/T 13627.2—2019
目 次
前言 1范围. 2规范性引用文件 3一般要求... 4附件和工具. 5安全卫生.. 6加工和装配质量 7空运转试验.
0
7.1运转试验 7.2温升试验, 7.3主运动和进给运动的检验(抽查) 7.4动作试验 7.5空运转功率试验(抽查) ·负荷试验 9数控轴线最小设定单位检验, 9.1试验方法 9.2误差计算方法 9.3 允差, 10精度检验.. 11包装.
0+.+0
....
te00o.0
4
JB/T 13627.2—2019
前言
JB/T13627《数控螺旋转子磨床》分为两个部分:
-第1部分:精度检验;一第2部分:技术条件。 本部分为JB/T13627的第2部分。 本部分按照GB/T1.1一2009给出的规则起草。 本部分由中国机械工业联合会提出。 本部分由全国金属切削机床标准化技术委员会(SAC/TC22)归口。 本部分起草单位:青海第二机床制造有限责任公司、天津第一机床总厂、重庆机床(集团)有限责
任公司、宜昌长机科技有限责任公司。
本部分主要起草人:颜芳、廉建铭、随英仕、高军、党晓练、柴宝连、喻可斌、李毅、钟瑞龄。 本部分为首次发布。
I
JB/T 13627.2—2019
数控螺旋转子磨床第2部分:技术条件
1范围
JB/T13627的本部分规定了数控螺旋转子磨床设计、制造和验收的要求。 本部分适用于最大磨削直径为30mm~350mm、最大工件安装长度为150mm~1700mm的数控
螺旋转子磨床(以下简称机床)。
2规范性引用文件
下列文件对于本文件的应用是必不可少的。凡是注日期的引用文件,仅注日期的版本适用于本文件。凡是不注日期的引用文件,其最新版本(包括所有的修改单)适用于本文件。
GB5226.1一2008机械电气安全机械电气设备第1部分:通用技术条件 GB/T 9061—2006 金属切削机床通用技术条件 GB 15760-2004 金属切削机床 安全防护通用技术条件 GB/T 17421.5—2015 机床检验通则第5部分:噪声发射的确定 GB/T23570—2009 金属切削机床焊接件通用技术条件 GB/T 25372—2010 金属切削机床精度分级 GB/T 25373—2010 金属切削机床装配通用技术条件 GB/T 25374—2010 金属切削机床清洁度的测量方法 GB/T 25376—2010 金属切削机床机械加工件通用技术条件 JB/T3997—2011 金属切削机床灰铸铁件技术条件 JB/T 8356—2016 机床包装技术条件 JB/T13627.1-2019 数控螺旋转子磨床 第1部分:精度检验
3一般要求
3.1按本部分验收机床时,还应对GB5226.1—2008、GB/T9061—2006、GB/T23570—2009、GB/T 25373一2010、GB/T25376-2010中未经本部分具体化的有关项目进行检验。 3.2验收机床时,按GB/T25372一2010规定的IV级精度机床的要求检验。
4附件和工具
4.1机床应随行供应表1所列的附件和工具。
表 1
用途安装工件用安装砂轮用
数量 1套 6 件
备注
名称顶尖垫板
I
JB/T 13627.2—2019
表1 (续)
用途
数量 1套 1套 1套 1套 1 把
备注
名称单头扳手双头扳手内六角扳手减振垫铁油枪注:制造厂根据机床结构确定提供具体所用的附件和工具。
调整机床用
安装机床用机床润滑用
包括地脚螺栓、螺母等
4.2扩大机床使用性能的特殊附件,可根据用户的要求按协议供应。
5安全卫生
5.1机床的安全防护应符合GB15760—2004、GB5226.1—2008的规定。 5.2在机床加工区应设置防护罩或挡板,并应具有足够的强度和刚性,同时便于操作者的观察。 5.3机床上外露而易被尘屑磨损的导轨副应安装防护装置。 5.4手轮、手柄的操纵力不应超过160N,手轮、手柄的操纵力在行程范围内应均匀。 5.5液压系统应能提供稳定的正常工作的压力,当压力低于设定限值时,应发出警告信号,并使机床运动停止。 5.6机床的噪声声压级在空运转条件下检验,测量方法应符合GB/T17421.5一2015的规定,其噪声声压级不应超过 83 dB(A)。机床运转时,不应有异常尖叫声、冲击声。
6加工和装配质量
6.1机械加工件、焊接件应符合图样、工艺文件及GB/T23570—2009、GB/T25376一2010等规定。机床装配应符合GB/T25373—2010的规定。 6.2机床灰铸铁件应符合JB/T3997—2011的规定。 6.3床身、床头箱体、工作台、电动机座、砂轮架壳体、砂轮架底座、轴承座、螺母座、滑座、尾座体、托架体等零件为重要铸件,在粗加工后应进行时效(如人工时效、振动时效等)处理。 6.4床身导轨副、工作台导轨副、砂轮架底座导轨副、砂轮架壳体导轨副、砂轮修整器导轨副、尾座体导轨副等重要导轨副,应采取耐磨措施,并符合材质及热处理的规定。 6.5主轴、蜗杆副、前(后)轴承、液压缸、活塞杆、顶尖、顶尖套、锥套等主要零件应采取与寿命相适应的耐磨措施。 6.6下列结合面按GB/T25373—2010和GB/T25376—2010规定的“重要固定结合面”的要求检验:
a)床身与后支座之间的结合面; b)床身与前电动机座之间的结合面; c)床身与前轴承座之间的结合面; d)后电动机座与砂轮架底座之间的结合面; e)后轴承座与砂轮架底座之间的结合面。
6.7下列结合面按GB/T25373—2010和GB/T25376—2010规定“特别重要固定结合面”的要求检验:
a)床身与滚动直线导轨之间的结合面; b)床身与砂轮架底座之间的结合面; c)砂轮架底座与滚动直线导轨之间的结合面;
2
JB/T 13627.2—2019
d)床头箱体与工作台之间的结合面; e)工作台与直线导轨滑块之间的结合面; f)砂轮架壳体与直线导轨滑块之间的结合面; g)磨头滑座与砂轮修整器底座之间的结合面。
6.8下列导轨按GB/T25373—2010和GB/T25376—2010中“滑(滚)动导轨”的要求检验:
a)床身与床头箱体的导轨面; b)床身与工作台的导轨面; c)工作台与床头箱体的导轨面。
6.9下列导轨按GB/T25373-2010和GB/T25376—2010中“移置导轨”的要求检验:
a)工作台与尾座体的导轨面; b)尾座体与顶尖座的导轨面。
6.10各运动坐标轴安装的滚珠丝杠副组装后应进行运转,其反向间隙值、丝杠轴向窜动量应符合设计规定。 6.11机床的清洁度按GB/T25374一2010规定的方法检验,其中床头箱、磨头、液压系统、润滑系统的清洁度按质量法检验(抽查);在机床运行30min后,立即在液压(或润滑)系统回油口处取样,般不少于200mL,污物不应超过150mg/L。其他部位用目测法、手感法检验,不应有脏物。
7空运转试验
7.1运转试验 7.1.1在无负荷状态下,机床主运动机构应从最低速度起按各级速度依次运转,每级速度的运转时间不应少于2min,最高速运转时间不应少于1h,使主轴轴承达到稳定温度。 7.1.2进给机构做低、中、高进给速度空行程试验,其运动应平稳、灵活,无明显的爬行和振动现象,试验时间一般不应少于30min。快速移动机构做快速移动试验,检验进给速度的正确性和变换的灵活可靠性,试验次数一般不少于10次。 7.2温升试验 7.2.1主轴轴承达到稳定温度时,在靠近磨头主轴轴承的外壳处测量轴承的温度和温升,温度和温升值不应超过表2的规定。
表 2
单位为摄氏度
温度 60 60 60
温升 30 30 30
检验项目滚动轴承滑动轴承液压系统
注1:机床经过一定时间运转后,当测量温度值上升幅度不超过5℃/h时,可认为达到了稳定温度。 注2:油液达到热平衡系指温升幅度≤2℃/h。
7.2.2液压系统应在额定工作压力下连续运行至油液达到热平衡后,测量油液的温度和温升,温度和温升值不应超过表2的规定。 7.3主运动和进给运动的检验(抽查) 7.3.1有级变速传动的各级主轴转速和进给量的实际偏差不应超过标示值的土5%。 7.3.2无级变速传动的各级主轴转速和进给量的实际偏差不应超过标示值的土10%。
3
JB/T 13627.2—2019
7.4动作试验
机床动作试验一般包括下述内容: a)起动机床,使机床实现自动循环,然后停止。如此循环10次,检验各动作是否灵活、可靠。 b)以中等进给量使工作台自动进给、停止及在行程范围内的任意给定位置起动、停止,各动作不
少于5次,在极限行程处不少于15次,动作应准确、可靠。 c)机床工作台左、右快速移动、停止10次以上,检验动作及限位开关是否稳定、可靠。 d)进给机构做低、中、高进给速度及快速进给变换试验10次,检验运转是否平稳,动作是否可靠。 e)工件主轴旋转点动,开、停不少于10次,检验动作是否可靠,润滑是否可靠。 f)磨头旋转点动,开、停不少于10次,检验动作是否可靠,润滑是否可靠。 g)左、右调整磨头角度5次以上,检查运动是否平稳、可靠,并检查磨头主轴转向是否正确。 h)压紧、松开砂轮架主轴刹紧按钮10次以上,检查高压泵及液压缸工作是否正常。 i)砂轮箱前后运动不少于10次,检查砂轮架横向慢速进给是否可靠。 j)液压泵站电动机起动、停止各10次,检验动作是否灵活、可靠。 k)润滑系统开、停10次,检验动作是否灵活、可靠,润滑是否正常。 1)冷却泵开、关各10次,检验动作是否灵活、可靠。 m)检验系统刀具补偿、螺距补偿及手轮功能是否可靠,动作是否灵活。 n)检验各手轮的回转是否平稳,操纵力是否均匀,反向空程量是否符合规定。 o)往复移动尾座顶尖套,检验移动是否平稳,刹紧是否可靠,操作力是否均匀。
7.5空运转功率试验(抽查) 7.5.1机床主运动机构在各级速度下空运转至功率稳定后,测量机床主传动系统的空运转功率,其值不应超过设计规定。 7.5.2机床应在全部功能下模拟工作状态做不切削连续空运转试验,循环过程中应包括各种程序功能和全部工作范围。其连续运转时间应符合表3的规定。在空运转过程中,各部分工作应正常,运行应平稳。各项功能、性能应可靠,不出现故障,各次循环程序之间的休止时间不应超过1min。当机床出现异常或故障时应查明原因并加以排除,然后重新进行试验。
单位为小时
表3
机床控制型式
连续运转时间
联动轴数<3 联动轴数≥3
36 48
数字控制
7.5.3在整机连续空运转过程中,机床的液压、润滑、冷却系统和其他部位均不应渗漏;转动部位的油不应甩出;润滑油路应畅通,冷却液应充分;切削液不应混入液压和润滑系统,机床各部分工作应正常。
8负荷试验
8.1.1最大承载重量的运转试验(抽查)
在机床上装上设计规定的机床承载最大重量的工件,机床以低速及设计规定的高速运转,检验机床运转是否平稳、可靠。
4
JB/T 13627.2—2019
8.1.2最大功率试验(抽查)
按设计规定的试件(材料和尺寸)、刀具(材料和几何参数)、进给量、切削速度,逐步改变切削深度使机床达到最大功率,检验机床在最大功率切削下各部分工作状态的稳定性、金属切除率及电气系统等是否可靠。
注:最大功率是指机床上主电动机的额定功率,不是设计的最大功率。某些机床如果只能在设计规定的计算功率下
进行最大功率试验,宜在机床使用说明书中注明,此情况下可按最大设计计算功率进行试验。
9数控轴线最小设定单位检验
9.1试验方法
先以快速使坐标上的运动部件向正(或负)向移动一段距离,停止后,向同方向给出若干个最小设定单位指令,再停止,以此位置作基准。每次给出1个最小设定单位指令,使运动部件向同方向移动,连续移动20个最小设定单位的距离,测量各个指令的停止位置。从上述的最终测量位置,再继续向同方向给出若干个最小设定单位指令,停止后,向负(或正)向给出若干个最小设定单位指令,使其约回到最终测量的位置(这些若干个最小设定单位指令下运动部件的停止位置不做测量)。然后从最终测量位置开始,每次给出1个最小设定单位指令,共给出20个最小设定单位指令,使运动部件继续向负(或正)向移动,约返回到基准位置,测量各指令的停止位置(见图1)。
至少在行程的中间及靠近两端的三个位置分别进行测量。
实际移动距离4
1
数个最小设定单位的、 移动距离不做测量
测量范围L20
最小设定单位
2
图1
9.2误差计算方法
误差计算方法如下: a)最小设定单位进给误差为|L;-mlmax。其中:
Li—相邻位置间的距离,单位为毫米(mm); m一最小设定单位量,单位为毫米(mm)。
b)最小设定单位相对进给误差为 12%g=20㎡ ×100%。 其中: L20— 20个最小设定单位移动的总距离,单位为毫米(mm)。 9.3允差
20m
最小设定单位进给误差应不大于一个最小设定单位;
5