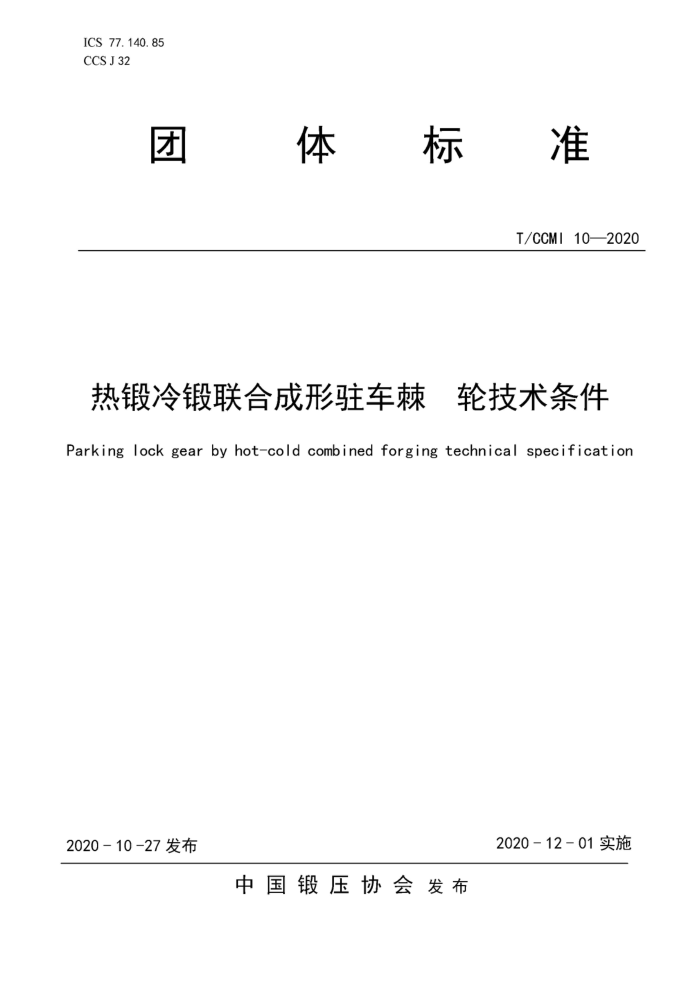
T/CCMI10-2020
目次
前言范围
II
1
规范性引用文件 3 术语和定义
2
2
要求取样
N
S I
5
试验方法. 检验规则,标志、包装、运输、
6
7
8
T/CCM110-2020
前言
本文件按照GB/T1.1-2020《标准化工作导则 」第1部分:标准化文件的结构和起草规则》给出的规定起草。
请注意本文件的某些内容可能涉及专利。本文件的发布机构不承担识别这些专利。 本文件由江苏太平洋精锻科技股份有限公司提出。 本文件由中国锻压协会归口。 本文件起草单位:江苏太平洋精锻科技股份有限公司、天津太平洋齿轮传动科技有限公司、江苏太
平洋洋齿轮传动有限公司、江苏大洋精锻有限公司、扬州恒通精密机械有限公司、扬力集团股份有限公司、恒锋工具股份有限公司、抚顺特殊钢股份有限公司。
本标准主要起草人:王晓飞、陶立平、黄泽培、宋银生、李斌、仲太生、杨益波、冯桂萍、张立平、 徐骥、刘志群、杨代起、王耀祖。
本标准为首次发布。
II
T/CCMI10-2020
热锻冷锻联合成形驻车棘轮 技术条件
1范围
本文件规定了热锻冷锻联合成形汽车驻车棘轮(以下简称“驻车棘轮”)的术语和定义、分类、要
求、试验方法、检验规则、标志、包装、运输及贮存。
本文件适用于轮齿采用热锻冷锻联合成形工艺成批生产的汽车用钢制驻车棘轮成品,其大外圆直径不大于Φ180mm。其他行业同类驻车棘轮锻件可参照采用。
2规范性引用文件
下列文件中的内容通过文中的规范性引用而构成本文件必不可少的条款。其中,注日期的引用文件,仅该日期对应的版本适用于本文件;不注日期的引用文件,其最新版本(包括所有的修改单)适用于本文件。
GB/T 191 包装储运图示标志 GB/T226 钢的低倍组织及缺陷酸蚀检验法 GB/T 228.1
金属材料 拉伸试验 第1部分
验方法
GB/T 230.1 金属材料 洛氏硬度试验 第 邓分:试验方法
度试验 第1部分 子:试验方法
GB/T 231.1 金属材料 GB/T 699 GB/T 1979 结构钢低倍维 GB/T 2828.1 计数抽样栏 GB/T 3374.1 齿轮术语 和定 头 第1部分 几何学 义 GB/T 3478.1 GB/T 4340.1 金属材料 维氏硬度试验 第1部分:试验方法 GB/T 5106 圆柱直齿渐开线 GB/T 5216 保证淬透性结构钢 GB/T 5617 钢的感应淬火或火 自萍火后有效硬化层深度的测 GB/T 6394 金属平均晶粒度测定方法 GB/T 8541 锻压术语 GB/T9239.1 机械振动转子平衡恒态(刚性)平衡品质要求 第1部分:规范与平衡允差的检
优质碳素结构钢
快陷评级图鉴程序 第1部分 按接收质量限(AQL) )检索的逐批检验抽样计划
a
圆柱直齿渐线花键
完美量规
27
验
GB/T9239.14 机械振动转子平衡第14部分:平衡误差的评估规程 GB/T9450 钢件渗碳淬火有效硬化层深度的测定和校准 GB/T10561 钢中非金属夹杂物含量的测定一标准评级图显微检验法 GB/T12362-2016钢质模锻件公差及机械加工余量 GB/T 15758 花键基本术语 GB/T30512汽车禁用物质要求 JB/T9173齿轮碳氮共渗工艺及质量控制 QC/T262汽车渗碳齿轮金相检验
1
T/CCM1 102020
QC/T267汽车切削加工零件未注公差尺寸的极限偏差 QC/T270汽车钢模锻造零件未注公差尺寸的极限偏差 QC/T502汽车感应淬火零件金相检验 QC/T29018汽车碳氮共渗齿轮金相检验
3术语和定义
GB/T3374、GB/T8541及GB/T15758界定的以及下列术语和定义适用本文件。
3.1
热锻冷锻联合成形驻车棘轮 parking Iock gearbyhot-cold combined forging 汽车驻车棘轮轮齿采用热锻冷锻联合成形工艺方法获得的,轮齿齿面不再进行切削加工的驻车棘轮。
3. 2
齿槽中线medlineofalveolar 驻车棘轮轮齿中心和跨棒距量棒中心之间的连线。
3. 3
齿槽半角a及βalveolarhalfangleaαandβ 驻车棘轮直线圆弧组合齿形齿槽两侧齿面分别与齿槽中线之间的夹角。见图1。
A.
A 3: 1
MRE
图1 不对称直线圆弧形
4要求
4.1技术要求
2
T/CCMI10-2020
4.1.1 驻车棘轮原材料宜采用符合GB/T699标准规定的优质碳素结构钢、符合GB/T5216标准规定的保证率透性结构钢,也可使用由供需双方商定的其他材料。驻车棘轮的原材料应附有出厂产品质量证明书。 4. 1.2 驻车棘轮热处理表面硬度、心部硬度及有效硬化层深度应符合图纸要求。 4.1.3 驻车棘轮热处理金相组织要求见表1。
表1驻车棘轮热处理金相组织要求
原材料最终工艺方案碳化物级别
优质碳素结构钢
保证透性结构钢渗碳泽火或碳氮共渗
感应淬火 NA NA NA 3级-7级
1级~5级 1级~5级 0. 02mm
残余奥氏体和马氏体级别
表面非马氏体组织
NA
金相组织
4. 1.4 驻车棘轮棘齿要求见表2。
表2 驻车棘轮棘齿尺寸要求
渐开线齿形 7GB/T 3478. 1
棘轮齿形外花键跨棒距轮齿大径公差
直线圆弧形
按图纸要求 h11
≤1°
齿槽半角公差(α、 β) 4.1.5 驻车棘轮内花键精度不低于GB/T3478.1标准的6级。 4. 1.6 驻车棘轮轮齿形状和位置公差要求见表3。
NA
表3 驻车棘轮轮齿形状和位置公差尺寸要求
渐开线齿形
直线圆弧形
驻车棘轮齿形
轮齿大径相对内花键同轴度端面相对内花键圆跳动
$ 0. 2 ≤0.08
≤0.2
NA
轮齿面轮廓度
4.1.7 驻车棘轮线性尺寸、形状和位置公差应符合图纸的要求;驻车棘轮锻造未注尺寸公差按QC/T270 的规定执行,驻车棘轮切削加工未注尺寸公差按QC/T267的规定执行。 4.1.8驻车棘轮齿面粗糙度应不大于Rz16μm,其余表面粗糙度应符合图纸的要求。 4.1.9驻车棘轮有效齿面仅允许微小凹坑等缺陷,不能有凸起,有效齿面缺陷极限值见表4。机械加工表面的缺陷及非机械加工表面的缺陷按GB/T12362-2016中3.2.14的规定。 4.1.10驻车棘轮有许用剩余不平衡量要求时,许用剩余不平衡量平衡品质级别宜采用GB/T9239.1 标准G6.3,在此基础上计算许用剩余不平衡量要求,用户另有要求时,则按用户要求执行。 4.1.11 驻车棘轮有清洁度要求时,应符合图纸或用户清洁度指标要求,
3
T/CCM1 10-2020 4.1.12驻车棘轮禁用物质要求应符合GB/T30512标准规定的有毒有害物质限值要求,用户另有要求时,则按用户要求执行。
表4 4驻车棘轮有效齿面缺陷极限值
棘齿大径
极限值单一齿面缺陷处数全部齿面缺陷处数每一缺陷最大长度每一缺陷深度
≤100mm 1处 3处 1. 0mm 0. 15mm
>100 mm~180mm
2处 4处 1. 2 mm 0. 15mm
4. 2 结构要求
驻车棘轮结构按外形分为圆形(见图2A)、盘形(见图2B)及碗形(见图2C);按轮齿形状分为渐开线齿形(见图3A)及直线圆弧形(见图3B);直线圆弧形按轮齿是否对称分为对称齿形(α= β,见图4B)及不对称齿形(α≠β,见图1)
图2 2A圆形
图2 B盘形
4
T/CCMI 102020
图2C碗形
图3A渐开线齿形
图3B对称直线圆弧形
4.3工艺要求
T/CCMI10-2020
目次
前言范围
II
1
规范性引用文件 3 术语和定义
2
2
要求取样
N
S I
5
试验方法. 检验规则,标志、包装、运输、
6
7
8
T/CCM110-2020
前言
本文件按照GB/T1.1-2020《标准化工作导则 」第1部分:标准化文件的结构和起草规则》给出的规定起草。
请注意本文件的某些内容可能涉及专利。本文件的发布机构不承担识别这些专利。 本文件由江苏太平洋精锻科技股份有限公司提出。 本文件由中国锻压协会归口。 本文件起草单位:江苏太平洋精锻科技股份有限公司、天津太平洋齿轮传动科技有限公司、江苏太
平洋洋齿轮传动有限公司、江苏大洋精锻有限公司、扬州恒通精密机械有限公司、扬力集团股份有限公司、恒锋工具股份有限公司、抚顺特殊钢股份有限公司。
本标准主要起草人:王晓飞、陶立平、黄泽培、宋银生、李斌、仲太生、杨益波、冯桂萍、张立平、 徐骥、刘志群、杨代起、王耀祖。
本标准为首次发布。
II
T/CCMI10-2020
热锻冷锻联合成形驻车棘轮 技术条件
1范围
本文件规定了热锻冷锻联合成形汽车驻车棘轮(以下简称“驻车棘轮”)的术语和定义、分类、要
求、试验方法、检验规则、标志、包装、运输及贮存。
本文件适用于轮齿采用热锻冷锻联合成形工艺成批生产的汽车用钢制驻车棘轮成品,其大外圆直径不大于Φ180mm。其他行业同类驻车棘轮锻件可参照采用。
2规范性引用文件
下列文件中的内容通过文中的规范性引用而构成本文件必不可少的条款。其中,注日期的引用文件,仅该日期对应的版本适用于本文件;不注日期的引用文件,其最新版本(包括所有的修改单)适用于本文件。
GB/T 191 包装储运图示标志 GB/T226 钢的低倍组织及缺陷酸蚀检验法 GB/T 228.1
金属材料 拉伸试验 第1部分
验方法
GB/T 230.1 金属材料 洛氏硬度试验 第 邓分:试验方法
度试验 第1部分 子:试验方法
GB/T 231.1 金属材料 GB/T 699 GB/T 1979 结构钢低倍维 GB/T 2828.1 计数抽样栏 GB/T 3374.1 齿轮术语 和定 头 第1部分 几何学 义 GB/T 3478.1 GB/T 4340.1 金属材料 维氏硬度试验 第1部分:试验方法 GB/T 5106 圆柱直齿渐开线 GB/T 5216 保证淬透性结构钢 GB/T 5617 钢的感应淬火或火 自萍火后有效硬化层深度的测 GB/T 6394 金属平均晶粒度测定方法 GB/T 8541 锻压术语 GB/T9239.1 机械振动转子平衡恒态(刚性)平衡品质要求 第1部分:规范与平衡允差的检
优质碳素结构钢
快陷评级图鉴程序 第1部分 按接收质量限(AQL) )检索的逐批检验抽样计划
a
圆柱直齿渐线花键
完美量规
27
验
GB/T9239.14 机械振动转子平衡第14部分:平衡误差的评估规程 GB/T9450 钢件渗碳淬火有效硬化层深度的测定和校准 GB/T10561 钢中非金属夹杂物含量的测定一标准评级图显微检验法 GB/T12362-2016钢质模锻件公差及机械加工余量 GB/T 15758 花键基本术语 GB/T30512汽车禁用物质要求 JB/T9173齿轮碳氮共渗工艺及质量控制 QC/T262汽车渗碳齿轮金相检验
1
T/CCM1 102020
QC/T267汽车切削加工零件未注公差尺寸的极限偏差 QC/T270汽车钢模锻造零件未注公差尺寸的极限偏差 QC/T502汽车感应淬火零件金相检验 QC/T29018汽车碳氮共渗齿轮金相检验
3术语和定义
GB/T3374、GB/T8541及GB/T15758界定的以及下列术语和定义适用本文件。
3.1
热锻冷锻联合成形驻车棘轮 parking Iock gearbyhot-cold combined forging 汽车驻车棘轮轮齿采用热锻冷锻联合成形工艺方法获得的,轮齿齿面不再进行切削加工的驻车棘轮。
3. 2
齿槽中线medlineofalveolar 驻车棘轮轮齿中心和跨棒距量棒中心之间的连线。
3. 3
齿槽半角a及βalveolarhalfangleaαandβ 驻车棘轮直线圆弧组合齿形齿槽两侧齿面分别与齿槽中线之间的夹角。见图1。
A.
A 3: 1
MRE
图1 不对称直线圆弧形
4要求
4.1技术要求
2
T/CCMI10-2020
4.1.1 驻车棘轮原材料宜采用符合GB/T699标准规定的优质碳素结构钢、符合GB/T5216标准规定的保证率透性结构钢,也可使用由供需双方商定的其他材料。驻车棘轮的原材料应附有出厂产品质量证明书。 4. 1.2 驻车棘轮热处理表面硬度、心部硬度及有效硬化层深度应符合图纸要求。 4.1.3 驻车棘轮热处理金相组织要求见表1。
表1驻车棘轮热处理金相组织要求
原材料最终工艺方案碳化物级别
优质碳素结构钢
保证透性结构钢渗碳泽火或碳氮共渗
感应淬火 NA NA NA 3级-7级
1级~5级 1级~5级 0. 02mm
残余奥氏体和马氏体级别
表面非马氏体组织
NA
金相组织
4. 1.4 驻车棘轮棘齿要求见表2。
表2 驻车棘轮棘齿尺寸要求
渐开线齿形 7GB/T 3478. 1
棘轮齿形外花键跨棒距轮齿大径公差
直线圆弧形
按图纸要求 h11
≤1°
齿槽半角公差(α、 β) 4.1.5 驻车棘轮内花键精度不低于GB/T3478.1标准的6级。 4. 1.6 驻车棘轮轮齿形状和位置公差要求见表3。
NA
表3 驻车棘轮轮齿形状和位置公差尺寸要求
渐开线齿形
直线圆弧形
驻车棘轮齿形
轮齿大径相对内花键同轴度端面相对内花键圆跳动
$ 0. 2 ≤0.08
≤0.2
NA
轮齿面轮廓度
4.1.7 驻车棘轮线性尺寸、形状和位置公差应符合图纸的要求;驻车棘轮锻造未注尺寸公差按QC/T270 的规定执行,驻车棘轮切削加工未注尺寸公差按QC/T267的规定执行。 4.1.8驻车棘轮齿面粗糙度应不大于Rz16μm,其余表面粗糙度应符合图纸的要求。 4.1.9驻车棘轮有效齿面仅允许微小凹坑等缺陷,不能有凸起,有效齿面缺陷极限值见表4。机械加工表面的缺陷及非机械加工表面的缺陷按GB/T12362-2016中3.2.14的规定。 4.1.10驻车棘轮有许用剩余不平衡量要求时,许用剩余不平衡量平衡品质级别宜采用GB/T9239.1 标准G6.3,在此基础上计算许用剩余不平衡量要求,用户另有要求时,则按用户要求执行。 4.1.11 驻车棘轮有清洁度要求时,应符合图纸或用户清洁度指标要求,
3
T/CCM1 10-2020 4.1.12驻车棘轮禁用物质要求应符合GB/T30512标准规定的有毒有害物质限值要求,用户另有要求时,则按用户要求执行。
表4 4驻车棘轮有效齿面缺陷极限值
棘齿大径
极限值单一齿面缺陷处数全部齿面缺陷处数每一缺陷最大长度每一缺陷深度
≤100mm 1处 3处 1. 0mm 0. 15mm
>100 mm~180mm
2处 4处 1. 2 mm 0. 15mm
4. 2 结构要求
驻车棘轮结构按外形分为圆形(见图2A)、盘形(见图2B)及碗形(见图2C);按轮齿形状分为渐开线齿形(见图3A)及直线圆弧形(见图3B);直线圆弧形按轮齿是否对称分为对称齿形(α= β,见图4B)及不对称齿形(α≠β,见图1)
图2 2A圆形
图2 B盘形
4
T/CCMI 102020
图2C碗形
图3A渐开线齿形
图3B对称直线圆弧形
4.3工艺要求