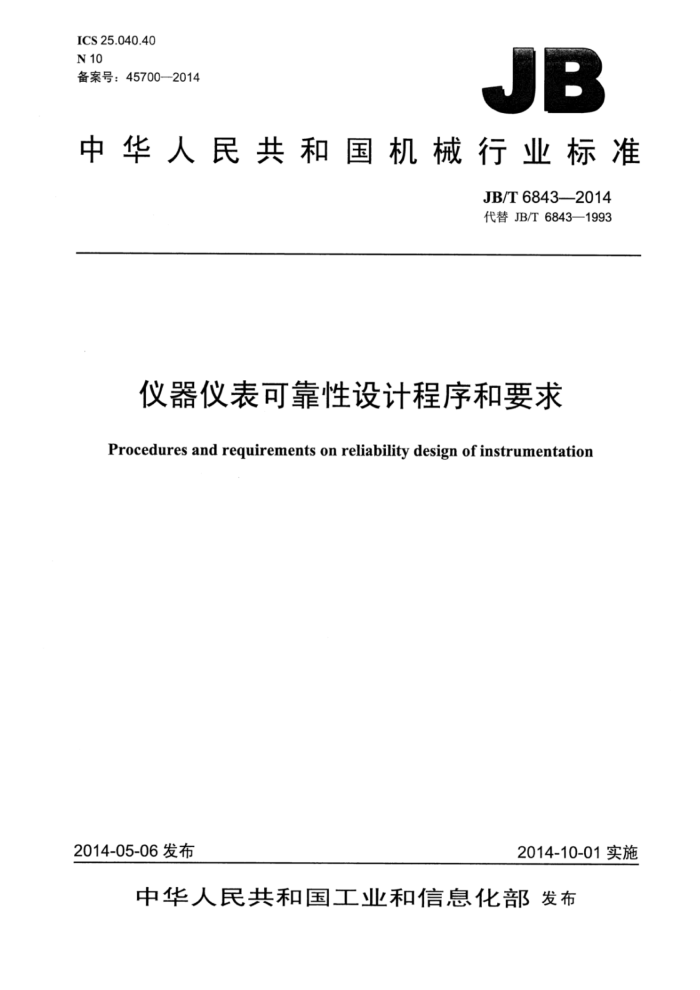
ICS 25.040.40 N10 备案号:45700—2014
JB
中华人民共和国机械行业标准
JB/T68432014 代替JB/T6843—1993
仪器仪表可靠性设计程序和要求
Procedures and requirements on reliability design of instrumentation
2014-10-01实施
2014-05-06发布
中华人民共和国工业和信息化部发布
JB/T6843—2014
目 次
前言. 范围 2规范性引用文件 3术语和定义. 4一般要求.. 5可靠性设计程序 5.1概述... 5.2任务确定阶段 5.3方案论证与审定阶段 5.4详细设计阶段 5.5 设计定型阶段. 5.6试生产阶段.. 6可靠性设计要求... 6.1 任务确定阶段, 6.2 方案论证与审定阶段 6.3 详细设计阶段, 6.4 设计定型阶段 6.5试生产阶段(定型生产阶段)参考文献
-
1
6
图1 可靠性设计程序流程
JB/T6843—2014
前言
本标准按照GB/T1.1一2009给出的规则起草。 本标准代替JB/T68431993《仪器仪表可靠性设计程序和要求》,与JB/T6843—1993相比主要技术
变化如下:
将原标准6.3的标题由“详细设计阶段”改为“技术设计阶段”,并修改了图1; -增加了“按JB/T50123要求做好现场数据的收集、分析和管理”的要求[见6.4.3b)];
一将原标准6.4.4的标题由“可靠性设计评审”修改为“设计评审”;一增加了参考文献。 本标准由中国机械工业联合会提出。 本标准由全国工业过程测量和控制标准化技术委员会(SAC/TC124)归口。 本标准起草单位:上海工业自动化仪表研究院、上海仪器仪表自控系统检验测试所。 本标准主要起草人:刘建侯、李佳嘉、谢亚莲。 本标准所代替标准的历次版本发布情况为:
JB/T6843—1993。
II
JB/T6843—2014
仪器仪表可靠性设计程序和要求
1范围
本标准规定了仪器仪表(以下简称产品)研制过程各阶段中可靠性设计的任务、工作程序和详细要
求。
本标准适用于仪器仪表新产品研制过程,定型产品的改进设计过程也可参照使用。本标准不适用软件可靠性设计程序和要求。
2规范性引用文件
下列文件对于本文件的应用是必不可少的。凡是注日期的引用文件,仅注日期的版本适用于本文件。 凡是不注日期的引用文件,其最新版本(包括所有的修改单)适用于本文件。
JB/T50123 3仪器仪表现场工作可靠性、有效性、维修性数据收集指南
3术语和定义
下列术语和定义适用于本文件。
3.1
可靠性设计程序reliabilitydesignprocedure 产品研制过程中可靠性设计工作内容及其先后联系的顺序。它包括研制过程中可靠性设计工作的阶
段划分及各阶段的主要任务与工作步骤。 3.2
可靠性设计要求reliabilitydesignrequirement 产品研制过程中,根据产品的复杂程度、价格水平、继承情况、结构型式,提出对各阶段可靠性设
计的详细要求(包括可靠性指标的确定、可靠性预计与分配、可靠性设计技术的应用、可靠性试验等)。
4一般要求
在产品研制过程中,设计项目除满足通常的技术性能指标外,还应有可靠性预计、分配、失效分析以及在可靠性设计方面的一系列活动,以满足预先规定的可靠性要求。
本标准着重强调方案论证和技术设计阶段的可靠性活动,要求加强全过程各个阶段的信息反馈,采取各种应力及手段来暴露和纠正潜在的缺陷,正确处理产品功能性、维修性、经济性和可靠性的关系,使产品在保证实现可靠性目标的前提下,加快进度,降低费用。
5可靠性设计程序
5.1概述
新产品可分下述五个阶段:任务确定阶段、方案论证与审定阶段、技术设计阶段、样机研制(设计定型)阶段、试生产(生产定型)阶段。可靠性设计工作主要在前四个阶段。
1
JB/T6843—2014
根据产品可靠性设计程序流程(见图1),给出各阶段的主要任务和工作步骤。
任务确定阶段资料收集
方案论证与审定阶段
国内外发展桃况 样机分析 市场动态 有关标准 无器件零部件可行性分 走访用户听取意见 反债和动志信息分 继承性产品分析 论证指标合理性 百能维织料 关健技术璜研工艺文件 主双 老练街递 开零部件认定 设计评审 现场使用 环境试验 重要元器件可靠性做 可靠性改进与验证 元薪饼鲜罐蜡线 可靠性设计 燃椒醇镜蜡灯样
可靠 技术性要中
品功
可#
设计评中
任
能框围 模 性摆围
信息反馈纠正措施
详细设计阶段价值分析
试生产阶段
设计定型阶疫
各种试验
医件
设计评审
技术应用
计
胖 L
y
图1可靠性设计程序流程
5.2任务确定阶段
对国内外有关资料和宣传使用情况、市场信息及用户要求等进行广泛的调查研究,初步确定任务要
求和可靠性要求。 5.3方案论证与审定阶段 5.3.1主要任务
对提出的几种总体设计方案从功能、性能、可靠性、维修性、安全性等方面进行全面分析和论证,通过多方面比较,做出最终评价。同时对方案中提出的关键技术进行预先研究和突破,为择优选定总体设计方案,进行技术设计提供依据。 5.3.2工作步骤
在论证产品总体性能指标的同时,进行可靠性指标论证,并初步对产品进行可靠性设计可行性分析,对方案中提出的关键技术进行预先研究,在此基础上进行方案设计评审。 5.4详细设计阶段 5.4.1主要任务
进行单元的电路、产品结构和关键工艺可靠性设计,对产品进行价值分析,具体贯彻落实可靠性设计和可靠性技术措施。 5.4.2工作步骤
通过对产品进行详细定量(或定性)的产品可靠性设计可行性分析(包括可靠性预计与分配、故障
2
JB/T6843—2014
分析),同时对电路、结构和关键工艺应用可靠性设计技术,对元器件和零部件的可靠性保证采取措施,在此基础上组织有关人员进行详细设计与开发阶段的初步设计评审,达到产品在可靠性、维修性、安全性等方面价值工程的分析。 5.5设计定型阶段 5.5.1主要任务工程
按详细设计阶段拟定的技术文件进行样机的研制、试验、评价和改进,验证可靠性技术措施和关键工艺的适用性,使样机可靠性增长达到计划要求。 5.5.2工作步骤
对重要的元器件、零部件进行必要的可靠性筛选试验,当样机性能试验通过后,对重要和关键的元器件、零部件及整机提出可靠性保证措施,进行环境试验和可靠性增长试验,对发现的问题提出改进措施并实施验证,在样机环境试验合格并具有可靠性增长的基础上组织现场使用,在上述工作基础上进行详细的设计评审。 5.6试生产阶段 5.6.1主要任务
按设计定型的技术文件进行小批量试生产,验证设计、工艺的合理性,形成和完善成套的工艺文件,采取质量保证措施,使产品可靠性增长达到预定的设计要求。 5.6.2 2工作步骤
编制关键件明细表,规定重点控制元器件、零部件、关键工艺的质量特性及其检验制度,进行可靠性筛选试验、环境试验和可靠性增长试验,在上述工作基础上进行设计评审。
6可靠性设计要求
6.1任务确定阶段 6.1.1资料收集
开展产品国内外发展情况的搜集和分析、市场动态的搜集和分析、样机分析(或继承性产品分析)及用户对产品质量要求的搜集和分析,确定总体设计思想,包括可靠性、维修性、安全性指标,电路、 结构、工艺的初步安排,可靠性结构模型,准备贯彻的标准、规范及试验评价方法等。 6.1.2确定可靠性要求
应定量规定产品的可靠性要求,全面描述产品的贮存、运输、工作和维修环境,确定时间度量及任务部面,明确产品失效的定义。 6.2方案论证与审定阶段 6.2.1确定产品可靠性设计指标
设计人员应根据产品完成任务的需要进行分析并提出可靠性指标,以及根据产品设计方案用经验数据或通过综合或计算预测能够达到的可靠性水平,再通过合理性、可行性分析后,确定产品可靠性设计指标。
3
JB/T6843—2014
6.2.2可靠性设计可行性分析
对产品进行初步可靠性设计可行性分析。根据提供的产品功能框图,分析提出可靠性框图,并用计
数法进行可靠性预计和故障模式影响分析(FMEA)方法分析产品薄弱环节,当预计值小于设计值时,应分析产品中关键元器件及零部件的可靠性,进行可靠性分配,重新提出关键元器件及零部件的可靠性要求,反复论证设计方案的合理性和可行性。 6.2.3关键技术预研
对产品的功能性、可靠性、工艺性、经济性、维修性和安全性等方面潜在的问题,进行全面分析和论证,做出多方面的比较和评价。同时,对论证中提出的关键电路、结构及工艺技术问题进行预先研究、 试验和评价,对新的元器件提前进行质量认定。 6.2.4设计评审
根据产品可靠性要求,制定相应的设计要求、设计评审要求、技术措施和试验方案等可靠性技术文件。并对上述可靠性指标合理性、可靠性设计可行性分析情况及关键技术预研情况等进行设计评审。 6.3详细设计阶段 6.3.1可靠性预计与分配 6.3.1.1可靠性预计
可靠性预计是一种反复过程,本阶段对电路常采用应力分析法,对机械构件可使用经过论证的经验数据,用计数法进行预计:
a)预计应考虑工作循环、失效率及已知的故障模式、故障机理等因素; b)预计应确定固有可靠度,并辅助以设计为基础的权衡决策,提供确定可靠性增长试验起始点的
依据,促进消除设计缺陷; c)预计数据可参照有关设备可靠性预计手册[如电子设备可靠性预计手册MIL-HDBK-217F或
GJB/Z299、非电子零部件可靠性数据(NPRD-3)J,其他数据来源应经过论证; d)在设计过程中,可反复进行预计,以证实产品满足由方案设计权衡分析得出的固有可靠度的可
信程度; e)应力分析法预计工作包括根据数学模型、元器件或零部件的应力和基本失效率、环境因子及由
故障的统计分布进行的分析,估计产品的可靠度R(t)或平均故障间隔时间MTBF; f)计划安排应将预计作为详细设计过程中一项连续性工作,对预计要定期修正,在初步设计评审
及详细设计评审时,应提交预计结果。
6.3.1.2可靠性分配
可靠性分配应符合以下要求: a)总的分配方法应以功能的重要性与复杂性、使用环境、相似设备的经验及现有技术水平为基础; b)具体的分配应以方案阶段的设计目标值为基础,并应包括进一步提高的因素; c)分配应进行到元器件、零部件级; d)应在详细设计阶段之后立即完成分配,并在设计评审之前提供分配结果
6.3.2故障分析 6.3.2.1故障模式影响及危害度分析(FMECA)
故障模式影响及危害度分析按以下要求进行:
4
JB/T6843—2014
a)可逐个进行元器件、零部件分析,也可仅对关键元器件、零部件进行分析,以确定故障对产品
可靠性、维修性及安全性的影响。 b)分析应根据设计技术状态,相似的结构部件、元器件使用数据及从预计分析获得的元器件故障
数据为基础。 c)分析应定量确定每一模式的故障及每种故障模式所占概率,并按概率值大小排序。 d)分析结果应用于下列任务:
一为可靠性预计提供输入,帮助决定改正措施的优先顺序;一确定关键的元器件、零部件、组件与关键参数及作为生产控制要求的特性;一在产品制造之前,制定改正措施准则,并且辅助编制试验计划及程序;
提供按故障模式统计的失效率的分配;提供安全性分析的基本数据及关键元器件、零部件、组件和它们故障模式的排序。
e)分析应定期修改,修改以故障分析数据及其他数据机构提供的数据为基础。 f)在设计过程中反复分析,在初步设计及详细设计评审时提交相应的分析结果。
6.3.2.2故障树分析(FTA)
故障树分析程序如下: a)收集和分析有关产品的设计、运行资料、流程图、技术规范和技术数据; b)正确分析产品或系统发生故障的情况,确定故障判据; c)把可能发生的故障分类排队,画成一个功能关系图和明细表,并注明其因果逻辑关系和事故链; d)根据6.3.2.2c)要求正确判断产品或系统最不希望发生的状态(即顶事件); e)把故障事件用方框图加以说明,并注明每个方框之间的逻辑关系; f)处理好产品和部件的边界条件; g)故障事件定义要准确、严格和解释的唯一性: h)各事件的逻辑关系和条件必须分析清楚,不应使逻辑混乱或条件矛盾; i)建树过程中及建成后,要注意合理的简化; j)选择演绎法或信号流程图法或计算机辅助法进行定性的故障分析。
6.3.3可靠性设计技术 6.3.3.1元器件和零部件的选用、控制和保证
可靠性设计技术应用于元器件和零部件的选用、控制和保证: a)应确定、控制所有关键的电路、机械及机电元器件、零部件、组件(列出全部明细表),使元器
件的数量及种类减到最少; b)应采用设计评审、结构分析、故障模式影响及危害度分析和费用分析等方法进行零部件的选择; c)应将确定关键件的工作编制成文件,把与安全性有关的关键件编码; d)应规定关键件的识别、控制、专门处理及定期检查的办法; e)应规定关键件早期采购、贮存及必要时可靠性增长试验规则; f)关键件文件应在初步设计评审之前提交; g)应说明控制过程、试验结果、可靠性增长及为减少关键件所采取的措施; h)控制工作应包括制定采购、进货检查或测量特性的规范,该规范应反映设计的可靠性要求并包
括成批验收试验、质量保证、管理措施及必要时的鉴定试验; i)应提出每种部件最大允许应力; j)应制定供应方控制大纲,审查供应方的工艺过程及有关文件; k)通过故障分析等手段不断改进部件质量;
5