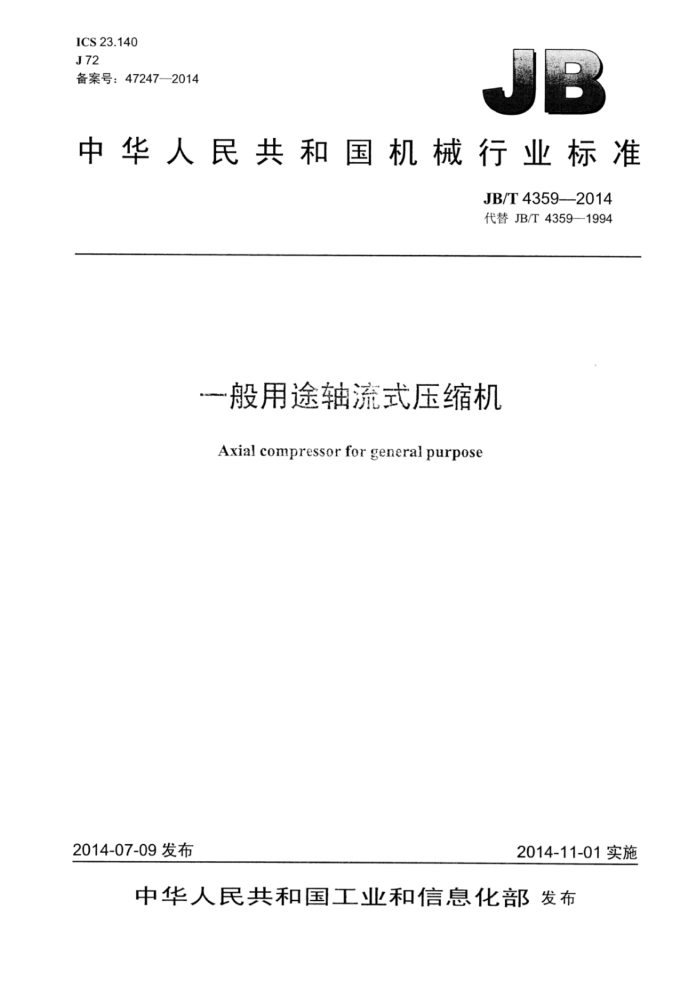
ICS 23.140 J72 备案号:47247—2014
中华人民共和国机械行业标准
JB/T4359—2014 代替JB/T4359—1994
一般用途轴流式压缩机
Axialcompressorforgeneralpurpose
2014-07-09发布
2014-11-01实施
中华人民共和国工业和信息化部发布
JB/T4359—2014
目 次
前言范围 2规范性引用文件
II
1
一般要求 4压缩机... 4.1 机壳. 4.2 外力和外力矩 4.3 扩压器及静叶承缸 4.4 转子... 4.5 轴承和轴承箱 4.6 轴端密封. 4.7 平衡与振动, 4.8 底座.. 4.9 旋转方向箭头和标牌 5辅助设备 5.1 原动机, 5.2变速器... 5.3联轴器. 5.4润滑油和控制油系统 5.5控制系统. 6检验与试验, 6.1材料及零部件检验 6.2压缩机试验. 7标志、包装、运输与保管 7.1标志... 7.2包装.. 7.3运输与保管附录A(规范性附录)外力和外力矩附录B(规范性附录)隔离裕度
3
1
10 10 .10 .10 11 12 14
图1 控制原理图图A.1 修正的力和力矩合成结果图B.1 转子响应图解曲线
13 14
表1 铸造系数表2齿轮的使用系数表3冷却器部件材料,表4常用仪表控制监测项目表5 材料及零部件检验.
f
1
JB/T4359—2014
前言
本标准按照GB/T1.1—2009规则起草。 本标准代替JB/T4359—1994《一般用途轴流式压缩机》,与JB/T4359—1994相比主要技术变化如下:
本标准“3一般要求”中删除了原标准中的合同性条款,整合了原标准4.1中的部分内容,增加了对压缩机噪声限制的规定;本标准“4.1机壳”将原标准4.2和4.4的内容做了修订和部分删除且进行了整合,并增加了有关机壳结构、设计、选材、性能等规定; -增加了附录A;本标准“4.3扩压器及静叶承缸”中增加了4.3.2及4.3.3内容; -本标准“4.4转子”将原标准4.6、4.7和4.8的内容做了修订和部分删除且进行了整合,并增加了对转子识别标记的要求;本标准“4.5.1轴承”中增加了4.5.1.1~4.5.1.3内容;本标准“4.5.2轴承箱”中增加了4.5.2.3~4.5.2.4内容;删除了原标准“4.11临界转速”;增加了附录B;本标准“4.7平衡与振动”将原标准“4.12振动”及“4.13平衡”的内容做了修订和部分删除且进行了整合,并增加了对平衡及振动的计算和测量值要求;本标准5.1.3中,将“所需最大功率”由原来的“115%”改为“110%”;修改了表2中齿轮的使用系数;删除了原标准“6辅助设备”;删除了原标准“7.7密封液排放槽”及“7.8 蓄能器” 本标准对图1中“2”及“3”的说明做了修订;删除了原标准“8.4 仪表板”;修改并补充了“表4常用仪表控制监测项目”;修改并补充了“表5 5材料及零部件检验”; -本标准6.2.1.1将原标准“9.2.3..试验压力为机壳设计压力的1.3倍”改为“....其试验压力为最高许用工作压力(表压)的1.5倍”;增加了“6.2.2超速试验”;修改并补充了“7标志、包装、运输与保管”中的条款及要求;删除了原标准“11资料”。 本标准由中国机械工业联合会提出。 本标准由全国风机标准化技术委员会(SAC/TC187)归口。 本标准起草单位:西安陕鼓动力股份有限公司、沈阳鼓风机集团股份有限公司本标准主要起草人:张稳娥、强宏、李翠芳、梅元平、刘侃、郑华、张三元。 本标准所代替标准的历次版本发布情况为:
JB/T4359—1994、JB/T4359—1989。
II
JB/T4359—2014
一般用途轴流式压缩机
1范围
本标准规定了一般用途轴流式压缩机(以下简称压缩机)的压缩机设计、辅助设备、检验与试验、 标志、包装、运输与保管等。
本标准适用于输送介质为空气的轴流式压缩机,其升压大于200kPa或压比大于3。对于输送介质为其他气体的轴流式压缩机可参考采用。
2规范性引用文件
下列文件对于本文件的应用是必不可少的。凡是注日期的引用文件,仅注日期的版本适用于本文件。凡是不注日期的引用文件,其最新版本(包括所有的修改单)适用于本文件。
GB/T191 包装储运图示标志 GB/T 2888 风机和罗茨鼓风机噪声测量方法 GB/T 6557 挠性转子机械平衡的方法和准则 GB/T8542 透平齿轮传动装置技术条件 GB/T 9239.1 机械振动恒态(刚性)转子平衡品质要求第1部分:规范与平衡允差的检验 GB/T 9239.2 机械振动恒态(刚性)转子平衡品质要求第2部分:平衡误差 GB/T 13306 5标牌 JB/T1267 50MW~200MW汽轮发电机转子锻件技术条件 JB/T3165 离心和轴流式鼓风机和压缩机热力性能试验 JB/T5442 压缩机重要零件的磁粉探伤 JB/T 6444 风机包装通用技术条件
3一般要求
3.1压缩机应在规定的压比条件下,其进口容积流量不出现负偏差,规定工况点上的功率不超过设计值的104%。 3.2压缩机及辅助设备的设计应能满足在规定工况运行点连续运行3年以上,其设计寿命不少于20年。 3.3压缩机及辅助设备的结构设计及布置应便于操作及维护,并留有足够的空间。 3.4主要零部件(如机壳和轴承箱)的设计、制造,应能保证在重新装配时的准确定位。 3.5静叶调节机构、轴承结构、轴端密封及油系统的设计应考虑在压缩机及其辅助设备运行或停机期间能防止湿气、粉尘及杂质的侵入。 3.6压缩机采用隔音措施后,其噪声≤85dB(A),噪声测量应符合GB/T2888之规定。
4压缩机
4.1机壳 4.1.1 机壳一般采用水平剖分结构,铸造成型或钢板焊接。 4.1.2机壳设计中,其允许拉应力(不包括连接螺栓)不超过其所选材料在最高规定的操作温度下最
1
JB/T4359—2014
小极限抗拉强度的0.25。对于铸造材料,允许拉应力应乘以表1中所示的铸造系数。 4.1.3对于机壳接合面使用的连接螺栓,其设计允许拉应力按4.1.2中确定,根据水压试验载荷和衬垫预载荷,确定总的螺栓连接面积。预载荷应力应不超过螺栓材料最小屈服强度的0.75。
表1铸造系数
铸造系数 0.8 0.9 0.9
无损检测形式目视、磁粉或渗透检测
局部X射线超声波全X射线
1.0
4.1.4对于空气或不可燃气体,机壳可以采用钢、球墨铸铁或铸铁材料。
a)当压力最高达6.4MPa(A)时,宜采用球墨铸铁; b)当压力最高达3.2MPa(A)时,宜采用灰口铸铁; c)当机壳设计压力在6.4MPa(A)以上,或机壳计算的最高运行温度在260℃以上时,宜采用铸
钢件或钢制焊接机壳。
4.1.5为便于拆卸和重新装配,应设置顶丝、导杆及机壳定位销。导杆应有足够的强度,以防止在装卸期间损伤壳体内件或壳体螺柱。为了起吊,在上机壳上应设计有吊耳或吊环。当使用顶丝分开接合面时,在被顶丝顶的面上应加工出凹坑或凹槽,以防造成接合面处泄漏或配合面不良配合。 4.1.6机壳应有足够的刚性,以便拆下和重装上机壳时不破坏机壳的运行间隙和轴承的对中找正。 4.1.7在机壳的主要连接面和螺栓连接的端盖上,应采用双头螺柱。 4.1.8承压部件中螺孔的使用应减少到最低限度。为防止机壳的承压部件泄漏,除了腐蚀裕度外,在要钻孔和车螺纹孔的周围和下面应留有至少12mm的厚度余量。 4.1.9对于用于连接的螺栓材料最低要求,铸铁机壳应采用碳钢,钢制机壳应采用高温合金钢,螺母材料应采用碳钢。 4.1.10机壳的最大允许工作压力至少是规定的最大出口压力(表压)的1.25倍。 4.2外力和外力矩
压缩机所能承受的外力和外力矩应符合附录A的要求。 4.3扩压器及静叶承缸 4.3.1扩压器通道应无任何突出物(例如铸造不规则)。 4.3.2当采用可调静叶时,可调静叶及静叶调节机构应适应所有规定的工作条件。 4.3.3当采用可调静叶时,应在机壳与传动装置配合连接处设置密封,以防气体泄漏。 4.4转子 4.4.1 转子应清晰地标有识别标记,该标记应打印在轴的非驱动端,或者打印在维护时不易损伤且易看得到的地方。 4.4.2如果转子上装有迷宫密封片,密封片应易于更换。当密封片在固定件上时,轴上应设保护套。 4.4.3为减少止推轴承上承受的轴向载荷,应设置平衡盘、平衡管和接口。 4.5轴承和轴承箱 4.5.1轴承 4.5.1.1轴承一般采用液体动压径向轴承和止推轴承。 2
JB/T4359—2014
4.5.1.2轴承一般装有轴承温度传感器,温度测定应设置有报警、联锁停机值。 4.5.1.3止推轴承应按其在最不利的规定工作条件下连续运行来设计,推力的计算至少应考虑下列因素:
a)密封的最大设计间隙和2倍的最大设计间隙; b)受压转子直径的台阶变化; c)级间最大压差; d)规定的进、排气压差和级间压差; e)由机组其他设备(即联轴器、齿轮或没有止推轴承的电动机等)传送给压缩机止推轴承的最大
轴向推力; f)如果与电动机或发电机直接相连,来自驱动机的最大轴向推力。
4.5.1.4压缩机应装有轴位移探头,用于探测转子轴向位移的变化。 4.5.2 轴承箱 4.5.2.1 轴承箱应能保证在更换轴承时不拆卸上机壳。 4.5.2.2 :轴承箱的设计应保证至少在每个径向轴承附近能够安装2支互成80°~100°非接触式测振探头。 4.5.2.3轴承箱应设计得使油产生的泡沫最少,排油系统应使油位和泡沫维持低于轴端密封。 4.5.2.4在轴穿过轴承箱的地方应设有可更换的油封和挡油环。油封和挡油环的设计应能有效地防止轴承箱内的润滑油向外泄漏以及外部杂质进入轴承箱内。 4.6轴端密封 4.6.1车 轴封应能阻止或防止工艺气体向大气泄漏或密封液体向工艺气体泄漏。 4.6.2轴封安装后应易于拆卸和更换。 4.6.3选择轴封材料时应考虑气体成分及运行条件的影响。 4.7平衡与振动 4.7.1 转子应进行横向振动分析及扭转分析。
隔离裕度与放大系数应符合附录B的要求,
4.7.2转子组装后应进行动平衡校正。刚性转子的平衡品质要求可按GB/T9239.1、GB/T9239.2进行,挠性转子的平衡方法可按GB/T6557进行。 4.7.3转子进行动平衡校正时,其剩余不平衡量应不超过公式(1)的计算值或质量偏心距250μm,两值中取较大值。
U=6350W/nm
.(1)
式中: U—剩余不平衡量,单位为克毫米(g·mm); W—轴颈处静载荷,单位为千克(kg); nmax最高工作转速,单位为转每分(r/min)。 当质量偏心距单位用微米(μm)表示,其计算公式为剩余不平衡量/轴颈处的静态质量载荷(U/1000W)。 4.7.4动平衡校正过程中,当剩余不平衡量超过要求时,可在轮毂端面用配置调整块、调整条或调整螺钉的方法进行平衡,并用螺钉紧固。 4.7.5压缩机在规定工作转速范围内的任一转速下进行机械运转试验时,在靠近径向轴承的任意环面上所测得的未滤波的峰-峰振幅值不应超过公式(2)的计算值或50μm两值中取较小值。
m
JB/T4359—2014
12000 nmax
A = 25.4,
(2)
L
式中: A一未滤波的轴振动振幅值,单位为微米(μm),是真实的峰-峰振幅值。 在最高连续工作转速至跳闸转速之间,其最大振幅值的增加量应不超过最高连续转速下所记录的最
大值之上12.7μm。 4.8底座 4.8.1底座上安放机组零件的表面应是已加工面,允许在机器和底座之间采用两面加工过的调整垫板或多层组合垫片。 4.8.2底座上应设计有水平和垂直导向键,以保证压缩机在热运转过程中的对中性。 4.8.3为了调整底座在基础上的垂直位置,应随机提供调整螺钉和垫板。 4.9旋转方向箭头和标牌 4.9.1转向箭头应铸在或固定在压缩机壳体上。 4.9.2 在压缩机的明显位置上应固定有压缩机标牌。 4.9.3 3标牌的有关要求应符合GB/T13306的规定,其内容包括:
a)产品名称; b)产品型号: c)产品编号; d)制造厂名; e)制造日期; f)进口流量; g)进口压力; h)出口压力: i)进口温度; j)轴功率; k)工作转速。
5辅助设备
5.1原动机 5.1.1一般要求
原动机功率的确定应考虑变速器和联轴器的功率损失。原动机的输出转矩和起动转矩应满足压缩机各工况的运行要求。 5.1.2汽轮机
一般情况下,作为主驱动装置的汽轮机应按下列条件设计: a)在正常进汽和排汽条件下,汽轮机的输出功率按压缩机最大功率的110%确定; b)在最低进汽和最高排汽条件下,汽轮机应连续供给压缩机100%的所需功率; c)在压缩机最低和最高连续运行转速之间,汽轮机应能连续运行。
4
JB/T43592014
5.1.3电动机
电动机的额定功率至少应是被拖动负荷(包括变速器和联轴器等)所需最大功率的110%。同时应考虑被驱动设备的起动方式,电动机在起动时应符合电网压降要求, 5.1.4透平膨胀机
其功率和转速要求同汽轮机。 5.2变速器 5.2.1平行轴齿轮对应为单斜齿或双斜齿,行星齿轮传动中可采用正齿轮,齿形由供方确定。 5.2.2在压缩机最高连续转速下,变速器应能传递额定转矩乘以相应的使用系数后得出的转矩值,其中额定转矩为各规定运行点中最大转矩,按公式(3)进行计算:
额定转矩(N·m)≥ 30000 输入功率单位为千瓦(kW))
.. (3)
元 输入端转数[单位为转每分(r/min)]
输入功率等于设计驱动功率。对于不传递全部驱动功率的变速器(例如2台单机之间的变速器)其输入功率需另行计算。
变速器的使用系数推荐见表2。
表2齿轮的使用系数
原动机种类汽轮机、透平影胀机
使用系数 1.6 1.4 与变速器厂商定
电动机其他
5.2.3 3止推轴承应承受联轴器轴向力以及齿轮轴向啮合力。 5.2.42 在规定运行点上低速轴的弯曲临界转速不应在高速轴转速的土15%以内。 5.2.5 变速器其他技术要求按GB/T8542执行。 5.3联轴器 5.3.1 在压缩机、变速器和原动机之间可采用刚性或挠性联轴器。 5.3.2 联轴器的设计应使驱动轴可脱开单独运转。 5.3.31 联轴器的中间传递单元或中间轴应在不拆卸压缩机、变速器和原动机的情况下可拆卸。 5.3.4 联轴器护罩的设计应便于检查和拆卸。 5.4 润滑油和控制油系统 5.4.1 一般要求 5.4.1.1润滑油和控制油系统向下列部位提供合适压力和温度的润滑油或控制油:
a)驱动机和被驱动设备的滑动轴承; b)汽轮机调速系统; c)其他液压控制系统。
5.4.1.2 润滑油系统与控制油系统可以组合在一起。 5.4.1.3过滤器和冷却器应有带阀门的排液口和排气口,阀门通径不得小于12mm。
5