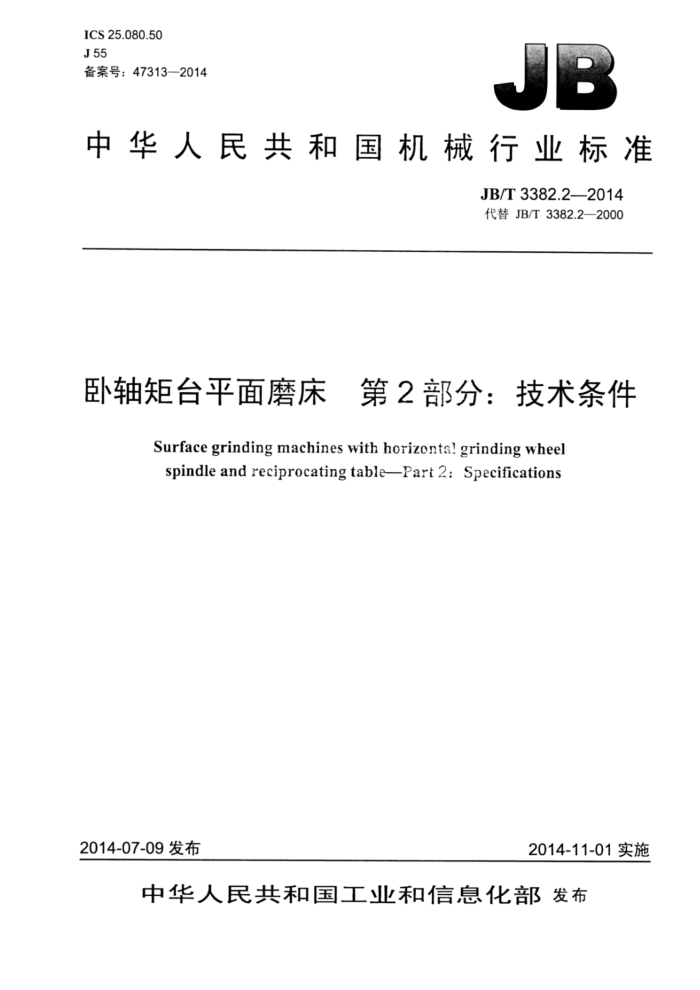
ICS25.080.50 J55 备案号:47313—2014
中华人民共和国机械行业标准
JB/T3382.2—2014 代替JB/T3382.2—2000
卧轴矩台平面磨床 第2部分:技术条件
Surface grinding machines with horizon tal grinding whee spindle and reciprocating table-Part 2: Specifications
2014-07-09发布
2014-11-01实施
中华人民共和国工业和信息化部发布
JB/T3382.2-2014
目 次
前言 1 范围. 2
II
规范性引用文件一般要求附件和工具. 安全卫生加工和装配质量机床空运转试验 7.1 温度和温升试验. 7.2 进给运动的检验 7.3 空运转功率试验(抽查) 7.4 功能试验 7.5 整机连续空运转试验, 8机床负荷试验(抽查) 8.1机床承载最大工件重量的运转试验 8.2砂轮主轴电动机达到最大功率试验。 9机床精度检验. 10磨除率试验(抽查) 10.1试验条件 10.2 试验结果
3 4 5 6 7
表1 附件和工具,表2 带刻度装置的进给手轮反向空程量表3滑动、滚动轴承的温度和温升表4液压油的温度和温升,表5垂直进给相对误差. 表6往复速度相对误差. 表7工作台往复移动最大冲出量表.8.连续空运转时间表9 工作台面表面和试件表面粗糙度值Ra
JB/T3382.2—2014
前言
JB/T3382《卧轴矩台平面磨床》分为四个部分:
第1部分:型式与参数;一第2部分:技术条件;一第3部分:精密级机床精度检验;
第4部分:高精度级机床精度检验。 本部分为JB/T3382的第2部分。 本部分按照GB/T1.1一2009给出的规则起草。 本部分代替JB/T3382.2—2000《卧轴矩台平面磨床技术条件》,与JB/T3382.2—2000相比主要技
术变化如下:
增加了安全卫生(见第5章);删除了手轮、手柄操纵力的要求,因为在相关强制性标准中已有规定(见2000年版的5.7);增加了砂轮主轴动平衡的要求(见6.8);一增加了功能试验的内容(见7.4.1、7.4.2、7.4.7~7.4.9);增加了表面粗糙度值Ra的规定(见9.5)。
本部分由中国机械工业联合会提出。 本部分由全国金属切削机床标准化技术委员会(SAC/TC22)归口。 本部分起草单位:杭州杭机股份有限公司。 本部分主要起草人:陈小飞、陈向东、阮志斌、黄强。 本部分所代替标准的历次版本发布情况为:
JBn3382-1983; JB/T3382.2—2000。
II
JB/T3382.2-—2014
卧轴矩台平面磨床 第2部分:技术条件
1范围
JB/T3382的本部分规定了卧轴矩台平面磨床的制造和验收的技术要求。 本部分适用于工作台面宽度为125mm~800mm的一般用途的普通级、精密级、高精度级卧轴矩
台平面磨床(以下简称机床)。
2规范性引用文件
下列文件对于本文件的应用是必不可少的。凡是注日期的引用文件,仅注日期的版本适用于本文件。凡是不注日期的引用文件,其最新版本(包括所有的修改单)适用于本文件。
GB/T9061—2006金属切削机床通用技术条件 GB/T23572一2009金属切削机床液压系统通用技术条件 GB24385-2009卧轴矩台平面磨床安全防护技术条件 GB/T25372-2010金属切削机床精度分级 GB/T25373—2010 金属切削机床装配通用技术条件 GB/T25374—2010 金属切削机床清洁度的测量方法 GB/T25376-2010 金属切削机床机械加工件通用技术条件 JB/T3382.3—2014 卧轴矩台平面磨床第3部分:精密级机床 精度检验 JB/T3997-2011金属切削机床灰铸铁件技术条件 JB/T3382.1臣轴矩台平面磨床第1部分:型式与参数
3一般要求
3.1本部分是对GB/T9061—2006GB/T25373—2010、GB/T25376—2010的具体化和补充。按本部分验收机床时,应同时对上述标准中未经本部分具体化的其余有关验收项目进行检验。 3.2机床按GB/T25372一2010的规定,普通级为IV级精度机床,精密级为II级精度机床,高精度级为 I级精度机床。
4附件和工具 4.1.1机床应按表1提供附件和工具。
表1附件和工具
数量 2 件 2副 1副 1副 1套 1套
备注
名称砂轮砂轮卡盘砂轮平衡心轴拆卸砂轮工具砂轮修整器
不附金刚钻
调整机床所必需的专用工具
1
JB/T3382.22014
4.1.2根据用户要求,按协议(或合同)的规定提供特殊附件。
5安全卫生
机床的安全防护应符合GB24385—2009的规定。
61 加工和装配质量
6.1铸件质量应符合JB/T3997—2011的规定。
床身、立柱、拖板、工作台、磨头体为重要铸件,应在粗加工后进行时效处理。精密级和高精度级机床的重要铸件还应在半精加工后进行第二次时效处理。 6.2砂轮主轴,进给丝杠等易磨损的主要零件,应采取与寿命相适应的耐磨措施。 6.3工作台纵向移动导轨副为重要导轨副,应采用耐磨铸铁、镶钢、贴塑或采取高(中)频感应淬火等耐磨措施。 6.4工作台纵向移动导轨副、拖板(或磨头立柱)横向移动导轨副、磨头(或拖板)垂直移动导轨副应按GB/T25373一2010中“静压、滑(滚)动导轨”的要求进行考核。 6.5下列结合面应按GB/T25373一2010中“特别重要固定结合面”的要求进行考核:
a)立柱与床身(或拖板)的结合面: b)按“静压、滑(滚)动导轨”要求进行考核的可拆卸的镶嵌导轨与其配合件的结合面; c)滚珠丝杠螺母座与基体的结合面。
6.6带刻度装置的进给手轮反向空程量应不大于表2的规定值,并符合下列规定:
a)普通级机床垂直进给手轮的最小刻度值为0.005mm时,其反向空程量应不大于
5
b)重量大于10t的普通级机床,其垂直进给手轮的反向空程量应不大于于
D
表2带刻度装置的进给手轮反向空程量
单位为转
机床精度等级
横向进给
垂直进给 1/10 1/20 1/20
普通级精密级高精度级
一
1/10 1/10
6.7按GB/T25374一2010的规定检验磨头部件内部的清洁度(抽查)。滑动轴承、静压轴承的清洁度按重量法检验,其杂质、污物普通级机床不应超过200mg,精密级、高精度级机床不应超过180mg(抽查);滚动轴承的清洁度按目测法或手感法检验,不应有杂质和污物。液压系统的清洁度检验按GB/T 23572—2009的规定。 6.8砂轮主轴连同轴上的电动机转子和旋转零件应进行动平衡校正,平衡值应符合设计的规定。 7机床空运转试验 7.1温度和温升试验 7.1.1砂轮主轴(带砂轮)在无负荷状态下进行空运转试验,高速运转不少于1h,当主轴轴承达到稳定温度时,在靠近主轴轴承的外壳处或轴承系统油箱中测量,其温度和温升应不大于表3的规定值。 7.1.2液压系统的温升试验宜符合GB/T23572一2009的规定。在额定工作压力下使系统运行至油液达到热平衡后,检验油液的温度和温升,其温度和温升均应不大于表4的规定值。 2
JB/T3382.2—2014
表3滑动、滚动轴承的温度和温升
单位为摄氏度
轴承型式滑动轴承滚动轴承
温度 55 65
温升 25 35
表4液压油的温度和温升
单位为摄氏度
机床精度等级
温度 55
温升 25
普通级精密级、高精度级
7.2 进给运动的检验 7.2.1 磨头垂直进给相对误差应不大于表5的规定值。
表5垂直进给相对误差
每次进给相对误差
连续10次进给相对误差
100%
20%
7.2.2试验条件如下:
a)指示器固定在磨头上,其测头垂直触及工作台面: b)以最小标称进给量进给,连续进给10次。
7.2.3计算公式见公式(1)和公式(2):
an-b] b
S每次
x100%
(1)
式中:每次 每次进给相对误差;
每次实际进给量,单位为微米(um); b最小标称进给量,单位为微米(um)。
an
10
-106
行
S1o次
H
x100%
(2)
00000E
10b
式中: S10次 一连续10次进给相对误差;
an 每次实际进给量,单位为微米(μm); b一最小标称进给量,单位为微米(um)。
7.3空运转功率试验(抽查)
砂轮主轴电动机(带砂轮)空运转功率应符合下列规定: a)采用他驱式电动机的空运转功率应不大于砂轮主轴电动机空运转功率指标的115%: b)采用自驱式电动机的空运转功率应不大于砂轮主轴电动机空运转功率指标的125%: c)在砂轮主轴电动机空运转功率指标尚未确定时,砂轮主轴电动机的空运转功率可按不超过电动
3
JB/T3382.2--2014
机额定功率的25%进行考核。 注1:选择装配质量较好的磨头10套,测量砂轮主轴电动机空运转功率,取其平均值作为砂轮主轴电动机空运转
功率指标。
注2:测量他驱式砂轮主轴电动机空运转功率时,扣除电动机空载功率。 7.4功能试验 7.4.1砂轮主轴进行10次起动、停止的操作试验,动作应灵活、可靠。 7.4.2对进给系统进行10次起动、停止的操作试验,动作应灵活、可靠。 7.4.3工作台纵向移动、拖板(或磨头、立柱》横向移动的往复速度相对误差应不大于表6的规定值(采用机械传动的往复速度相对误差按设计规定)。
表6往复速度相对误差
往复速度相对误差
传动型式
10% 理论计算值+10%
双活塞杆单活塞杆
计算公式见公式(3)。
s=2±-l 100%. t. +t2
(3)
式中:
一往复速度相对误差: tit2- 一分别为工作台往复单程时间,单位为秒(s)。
7.4.4拖板(或磨头、立柱)横向断续进给的不均匀量按设计规定。 7.4.5工作台纵向往复运动,两端最大冲出量应不大于表7的规定值,并符合下列规定:
a)工作台速度≥35m/min的机床最大冲出量按表中对应值增加20%: b)采用贴塑导轨、滚动导轨、静压导轨的机床,最大冲出量按设计规定。
表7工作台往复移动最大冲出量
机床重量
>5~10
>10
≤5
t 最大冲出量
150
80
120
mm
7.4.6在机床规定速度范围内,工作台纵向移动、拖板(或磨头、立柱)横向移动应平稳,高速无冲击现象:低速无爬行现象。 7.4.7对机床的各种指示灯、控制按钮等进行试验,动作应灵活、可靠。 7.4.8对机床的安全防护装置和保险装置进行试验,功能应可靠,动作应灵活、准确。 7.4.9对机床的冷却、润滑系统进行试验,应密封可靠,冷却充分,润滑良好,各系统不得渗漏。 7.5整机连续空运转试验
机床在全部功能下模拟工作状态作不磨削连续空运转试验,包括机床的所有功能和全部工作范围,连续空运转时间不应少于表8的规定值。连续空运转过程中不应发生故障,若出现异常或故障,在查明原因进行调整或排除后,应重新开始试验。试验时,自动循环应包括所有功能和全部工作范围,各次自动循环之间的休止时间应不大于1min。 4
JB/T3382.2—2014
表8连续空运转时间
单位为小时
机床控制型式机械控制
连续运转时间
4 8
电、液控制
8机床负荷试验(抽查)
8.1机床承载最大工件重量的运转试验
机床(未安装电磁吸盘)承载的最大工件重量应符合JB/T3382.1的规定。机床承载最大工件重量运转试验时,工作台应运行平稳,低速无爬行现象。 8.2砂轮主轴电动机达到最大功率试验。
用磨削方法进行,试验条件如下: a)试件:JB/T3382.32014中工作精度检验M2项规定的试件; b)工作台纵向移动速度:高速或中速; c)横向断续进给量:不小于1/4砂轮宽度; d)垂直进给:均匀地进给至砂轮主轴电动机达到额定功率或设计规定的最大功率。 试验时,机床应正常运转。
9机床精度检验
9.1普通级、精密级和高精度级机床的精度检验应符合JB/T3382.32014的规定。 9.2JB/T3382.3一2014中的几何精度G2、G4、G6的b)、G10四项和工作精度M1、M2两项,均应在机床达到稳定温度后进行检验。 9.3机床承载最大工件重量运转试验后应复检几何精度(允许在设计规定的精度恢复时间后进行)。 9.4工作精度检验的磨削规范按制造厂的规定。 9.5工作台面表面和工作精度检验试件的表面粗糙度值Ra应不大于表9的规定值。
表9工作台面表面和试件表面粗糙度值Ra
单位为微米
工作精度检验项目
工作台面 1.25 0.63 0.32
机床精度等级
M2 0.63 0.16 0.08
M1 0.63 0.16 0.08
普通级精密级高精度级
10 磨除率试验(抽查)
10.1 试验条件
a)试件:JB/T3382.3一2014中工作精度检验M2项规定的试件: b)砂轮:随机供应的砂轮: c)工作台纵向移动速度:高速:
5