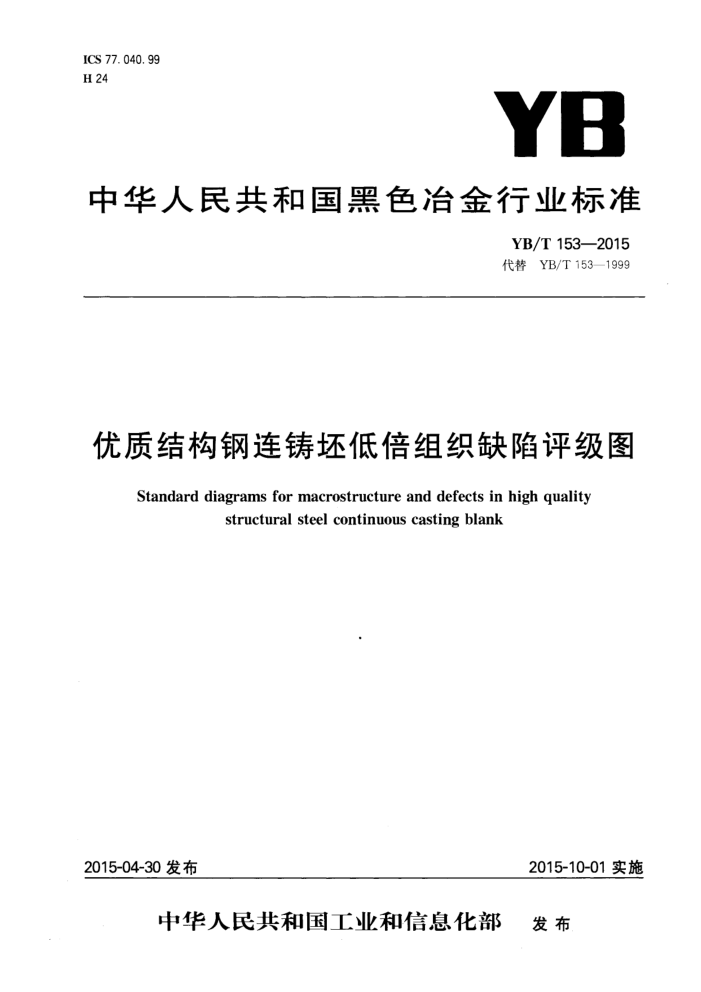
ICS 77. 040. 99 H 24
YB
中华人民共和国黑色治金行业标准
YB/T 153—2015 代替YB/T153—1999
优质结构钢连铸坏低倍组织缺陷评级图
Standard diagrams for macrostructure and defects in high quality
structural steel continuous casting blank
2015-10-01实施
2015-04-30发布
中华人民共和国工业和信息化部 发布
YB/T 153—2015
前言
本标准按照GB/T1.1--2009给出的规则起草。 本标准代替YB/T153—1999《优质碳素结构钢和合金结构钢连铸方坏低倍组织缺陷评级图》标准。 本标准与YB/T153一1999相比,主要变化如下:
标准名称更改为:“优质结构钢连铸坏低倍组织缺陷评级图”:扩大了连铸坏尺寸上限:连铸方坏或矩形坏边长由300mm扩大到550mm、连铸圆坏直径由
350mm扩大至1000mm;
增加了大规格方坏的低倍组织缺陷评级图谱(见附录B);增加了连铸圆坏低倍组织缺陷评级图谱(见附录C和附录D)。
本标准由中国钢铁工业协会提出。 本标准由全国钢标准化技术委员会(SAC/TC183)归口。 本标准起草单位:江阴兴澄特种钢铁有限公司、冶金工业信息标准研究院、天津钢管集团股份公司、
湖北新冶钢股份公司、首钢总公司。
本标准主要起草人:范海东、王晓宁、栾燕、李建设、郭艳、徐旭、顾林峰。 本标准1999年8月首次发布。
YB/T153—2015
优质结构钢连铸坏低倍组织缺陷评级图
1范围
本标准规定了优质结构钢连铸坏低倍组织缺陷形貌特征、产生原因、评级原则、评定方法和试验报告。 本标准适用于评定优质碳素结构钢、合金结构钢、弹簧钢等连铸坏的横截面酸蚀低倍组织缺陷。经
供需双方协商,也可用于评定其他钢类的连铸坏。
本标准适用于连铸坏尺寸范围为:边长为100mm~550mm的连铸方坏或矩形坏、直径为90mm~
1000mm的连铸圆坏(以下简称连铸坏)。其他尺寸的连铸坏可参照使用 2规范性引用文件
下列文件对于本文件的应用是必不可少的。凡是注日期的引用文件,仅所注日期的版本适用于本文件。凡是不注日期的引用文件,其最新版本(包括所有的修改单)适用于本文件。
GB/T226钢的低倍组织及缺陷酸蚀检验法 YB/T4149—2006连铸圆管坏
3分类和评定 3.1试样显示方法
试样的截取和显示按GB/T226的规定执行。 3.2各类缺陷(或组织)的形貌特征、产生原因及评定原则 3.2.1中心疏松
形貌特征:在酸蚀试样上集中在中心部位的空隙和暗点。 产生原因:钢液凝固时体积收缩而没有足够的钢液补充及最后凝固时气体析集和杂质集聚。 评定原则:根据试样中心部位的暗点和空隙数量、大小及密集程度评定。
3.2.2中心偏析
形貌特征:在酸蚀试样的中心部位呈现腐蚀较深的暗斑,有时在暗斑周围有灰白色带及疏松。 产生原因:钢液在凝固过程中,由于选分结晶的影响及连铸坏中心部位冷却较慢,造成心部的成分偏
析。
注:连铸坏鼓肚加重偏析程度。 评定原则:根据暗斑的大小和颜色的深浅程度评定
3.2.3缩孔
形貌特征:在酸蚀试样的中心部位呈现不规则的空洞。 产生原因:钢液凝固时柱状晶发达及局部柱状晶“搭桥”,中心最后凝固部分集中收缩而得不到钢液
补充。
评定原则:根据空洞的大小评定。
3.2.4内部裂纹 3.2.4.1角部裂纹
形貌特征:在酸蚀试样的角部,距表面有一定深度并与表面垂直或与对角线平行,严重时裂纹向内部扩展。
产生原因:钢液在结晶器内、外冷却强度不当及冷却不均,造成连铸坏角部受的应力超过钢的强度。
1
YB/T153—2015
评定原则:根据裂纹距表面的距离、宽度、长度和数量而评定 3.2.4.2皮下裂纹
形貌特征:在酸蚀试样的边部细等轴晶与柱状晶的交界处产生并沿柱状晶向内部扩展的裂纹产生原因:结晶器变形,局部摩擦力过大,对弧不准,结晶器及二冷区冷却不均,连铸坏鼓肚及矫直应
力过大。
评定原则:根据裂纹距表面的距离、宽度、长度和数量而评定 3.2.4.3中间裂纹
形貌特征:在酸蚀试样上裂纹在柱状晶区内出现,并沿柱状晶扩展,孤形连铸的连铸坏中间裂纹垂直于铸坏表面。
产生原因:连铸坏由于冷却不均,出二冷区后表面温度回升产生热应力,在拉坏和矫直时连铸坏受的机械应力过大。柱状晶发达也助长裂纹的发生。
评定原则:根据裂纹的宽度、长度和数量评定。 3.2.4.4中心裂纹
形貌特征:在酸蚀试样的中心部位出现的裂纹。 产生原因:连铸坏凝固末期因心部钢液凝固收缩产生应力,或连铸坏鼓肚,二冷不当,钢液过热度高。
气体含量高也能引起连铸坏中心裂纹。
评定原则:根据裂纹的宽度、长度和数量评定。 3.2.4.5非金属夹杂物
形貌特征:非金属夹杂腐蚀剥落后在酸蚀试样上呈不同形状或不同颜色的空隙或空洞,并成群分布。 产生原因:冶炼时脱氧产物、二次氧化产物等在结晶器内聚集未能上浮所致。 评定原则:根据夹杂物的数量、大小及密集程度评定。
3.2.4.6皮下气泡
形貌特征:在酸蚀试样的皮下沿柱状晶生长方向,呈分散或呈簇分布的细长裂缝或椭圆形气孔。 产生原因:钢液脱氧不良及二次氧化,气体含量高,加人钢液的原材料或浇注系统不于燥。 评定原则:根据气泡距表面的距离、大小和数量评定。
3.2.4.7白亮带
形貌特征:在酸蚀试样上,呈现抗蚀能力较强,组织致密的白色亮带。 产生原因:电磁搅拌不当,钢液运动速度快,凝固前沿温度梯度减小、凝固前沿富集溶质的钢液流出
形成白亮带。
评定时记录距边缘的距离和带的宽度。 3.2.4.8夹渣
形貌特征:在酸蚀试样上呈现不同的形状和不同的颜色的块状或颗粒。 产生原因:中间包低液位浇注产生旋涡将渣吸入至结晶器内未能上浮分离或结晶器内液面波动过
大,将渣卷人钢液在凝固前未能浮出形成中心夹渣。靠近连铸坏表面的夹渣为皮下夹渣。
评定时记录夹渣的大小、数量和位置。 3.2.4.9异金属夹杂
形貌特征:在酸蚀试样上呈现颜色与基体组织不同,无一定形状的金属块,有的与基体组织有明显界线,有的界线不清楚。
产生原因:由于加人的合金料或掉人的异金属在浇注前未完全熔化。 评定时记录异金属夹杂的大小和位置,并采用微观组织检验进行鉴别。
3.2.4.10翻皮
形貌特征:在酸蚀试样上有的呈现亮白色弯曲带,并在其上或周围有气孔和夹杂物;有的呈不规则
2
YB/T153——2015
附录A (规范性附录)
边长≥100mm~300mm连铸方坏或矩形坏低倍组织缺陷评级图
A.1 中心疏松(见图A.1) A.2 中心偏析(见图A.2) A.3缩孔(见图A.3) A.4角部裂纹(见图A.4) A.5 皮下裂纹(见图A.5) A.6 中间裂纹(见图A.6) A. 7 中心裂纹(见图A.7) A.8 皮下气泡(见图A.8) A.9非金属夹杂物(见图A.9) A. 10 白亮带(见图A.10) A.11 中心夹渣(见图A.11) A. 12 皮下夹渣(见图A.12)
2级
1级
图A.1中心疏松
YB/T153—2015
YB/T153—2015
4级
3级
图A.1 中心疏松(续)